- FMA
- The Fabricator
- FABTECH
- Canadian Metalworking
Surface Preparation Garners Unexpected Benefits
Automated shotblasting leads to better weldability for Steelway Building Systems
- November 26, 2014
- Article
- Automation and Software
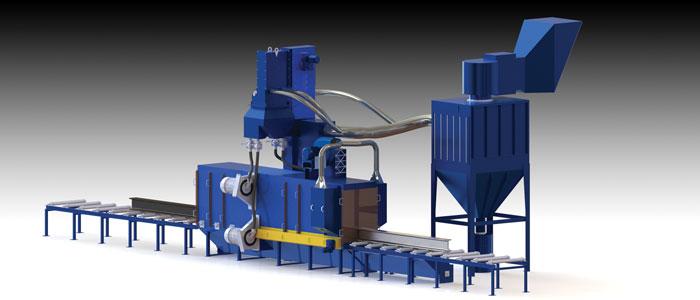
Roller tables move structural steel elements through Wheelabrator’s pass-through shotblast equipment.
Structural steel deserves a good paint finish too. That’s the approach to coating at Ontario-based steel building systems manufacturer Steelway, a family company now in its second generation.
To achieve the desired paint finish quality, Steelway upgraded its surface preparation operations at its 155,000-sq.-ft. main facility in Aylmer and discovered some unexpected side effects.
Steelway’s building systems comprise simple shapes of raw steel—wide flanges, structural tube, angle, and channel—ranging from 2 in. by 4 in. by 12 in. up to 20 in. by 44 in. by 60 ft. These hot-rolled structural steel components typically are primed or painted to prevent rust during storage or transit to the customer.
Surface preparation at Steelway used to be handled manually with power tools to wire-wheel each steel element. The process was slow, messy, and it created a dusty and dirty production environment.
Bryan White, a hands-on co-president at Steelway, explained: “We used to go through grinders like crazy. At times it created a bottleneck, preventing us from getting product out the door. And the working environment was not at all pleasant for the guys on the floor.”
The company also wanted to improve the quality of the surface preparation. Dealing with the paint issues on-site, problems with adhesion, and rusting were time consuming and resulted in occasional back charges from customers. A better, cleaner method was sought.
Surface Prep Menu
Surface preparation methods range from manual cleaning with wire brushes or power tools to chemical cleaning and abrasive blasting.
Abrasive blasting is a highly effective method that uses the kinetic energy of millions of small particles of shot, accelerated with either wheel or airblast technology, to “beat” contaminants out of the surface. At the same time, the blast process creates a defined surface profile of even peaks and troughs that is ideal for coating adherence.
The result is a clean, even finish and a precise anchor profile for coating, which provides a controlled root system that enables the paint to adhere to the product. The better the anchor profile, the better the coating; and the more even and precise the peaks and troughs, the less paint is needed to achieve the same dry-film thickness.
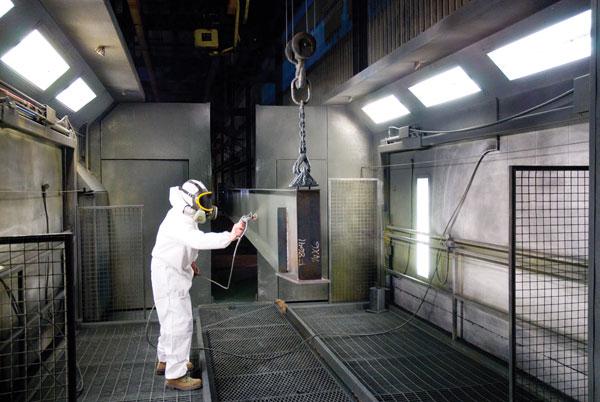
Shotblasting in a blastroom creates even peaks and troughs on the surface of structural components, which helps meet paint adhesion specifications and improves weldability.
Automated Blasting
Wheel technology is most common for blast cleaning parts with fairly simple shapes. Generally speaking, wheel blasting is more powerful, faster, and usually more cost-effective than the airblast option. However, for some applications or surface requirements, a separate touchup area for manual airblasting can be necessary.
At Steelway, a 10-ft.-wide, 18-ft.- high, and 59-ft. 4-in.-long (including conveyors) automated shotblast machine from Wheelabrator blastcleans structural steel elements before fabrication and coating. Four 20-HP blast wheels operate at a constant 3,600 RPM to remove rust and scale, foot by foot.
The machine’s work opening of 2 ft. 10 in. wide by 4 ft. 6 in. tall accommodates a range of geometries. All material handling, except for a Steelway-made crane, is part of the machine, including a roller conveyor to move the structural sections through the machine at the correct pace, usually between 3 and 6 FPM. The speed can be varied depending on the desired finish and the amount of the scale to be removed.
Unexpected Benefits
A beneficial and unexpected side effect of moving to automated shotblasting was better weldability. The blast process removed mill scale and other contaminants, leaving a cleaner, more even surface for better, easier, faster welds.
Beyond weldability and paint finish, the new process has also had an impact on quality control.
David Smith, production manager at Steelway, said, “One of the often overlooked benefits of blasting before fabricating is that on the rare occasion—maybe once or twice a year—we get a beam in that suffers from delamination, cracks, or other hidden imperfections. An imperfection will immediately show after blasting. It’s very important for us to catch those few faulty beams.
“The main benefits to the new process, however, are the increased quality of the paint job and better welds. The welds are also more visible when the paint job is good, which delights the quality inspectors.”
How Clean Is Clean?
The accuracy of the blast process provides the precise, quantifiable surface profile necessary to match exacting specifications and standards. Usually the paint supplier specifies the surface profile required for maximum paint adhesion. A common profile for structural steel is between 1.7 and 2.0 mil.
A key factor in determining the surface profile is the size of the abrasive. Small abrasive such as S170 leaves small surface dimples; S330 and higher abrasive leaves bigger dimples, resulting in a rougher surface.
A contact profilometer reads the surface profile like a record player stylus can measure roughness to determine the exact surface profile and match it against specifications. Achieving a different profile roughness is a matter of changing the blast media or the feed rate.
Once the machine is configured for a certain profile, that profile will be reliably reproduced across every part. Any surface patches or unevenness can be a sign that the blast pattern has shifted, for example through wear in the wheel, and needs correcting.
Abrasive Matters
The inside of a blast machine is a violent world, with abrasive hurled at parts with speeds of up to 280 feet per second. The high-velocity impacts cause the blast media to break down over time, at a rate related to process parameters including blast wheel horsepower and abrasive type and hardness.
This means that at any given time, the abrasive mix contains a desirable mix of new shot and partly brokendown elements. An even surface finish needs an even distribution of abrasive sizes. All-new abrasive would produce a surface profile with too many peaks.
On modern blast equipment, most of the abrasive handling is automated, including filtering and recycling. Automatic abrasive adders with level controls are common, as well as automated recycling systems with airwash separators, to help keep an optimum blast media mix.
Smooth Operations
Moving to shotblasting for its surface preparation changed things at Steelway in a number of ways, not all of which are easy to quantify.
The manual surface preparation used previously kept up to three people occupied for 30 to 60 minutes per beam. This is now done by the shotblast machine, manned by one operator, in five to 10 minutes: a time savings of over 80 percent.
Add to that savings on back charges, fewer rejects, and time savings on shop floor cleanup, welding, and painting, and the machine paid for itself in less than two years.
“The machine has now been in operation for a couple of years and we’ve never looked back,” said Smith.“Our previous method was costly, time-consuming, and dirty, but worst of all, not effective. Blast cleaning has turned our surface prep shop into a very smooth operation.”
Photos courtesy of Steelway and Wheelabrator.
subscribe now
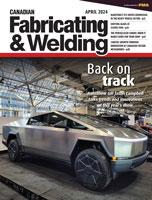
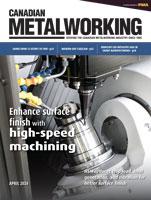
Keep up to date with the latest news, events, and technology for all things metal from our pair of monthly magazines written specifically for Canadian manufacturers!
Start Your Free Subscription- Trending Articles
- Industry Events
MME Winnipeg
- April 30, 2024
- Winnipeg, ON Canada
CTMA Economic Uncertainty: Helping You Navigate Windsor Seminar
- April 30, 2024
- Windsor, ON Canada
CTMA Economic Uncertainty: Helping You Navigate Kitchener Seminar
- May 2, 2024
- Kitchener, ON Canada
Automate 2024
- May 6 - 9, 2024
- Chicago, IL
ANCA Open House
- May 7 - 8, 2024
- Wixom, MI