Marketing Content Leader
- FMA
- The Fabricator
- FABTECH
- Canadian Metalworking
Portable system becomes hot tech in heat treatment
Heat View delivers compact, rugged, customizable systems
- By James Figy
- April 17, 2024
- Article
- Welding
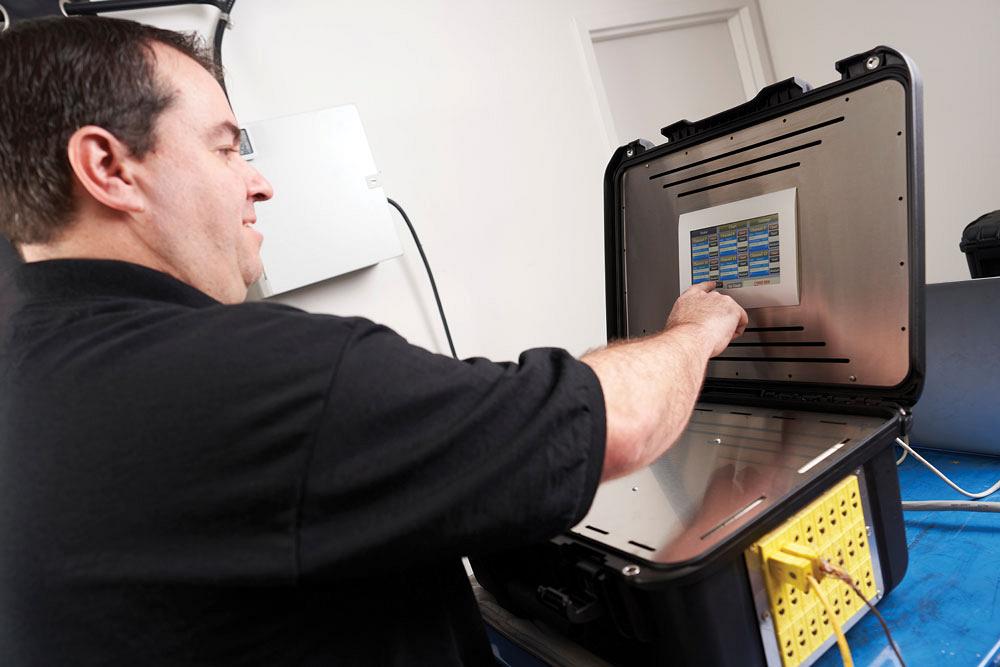
The engineering team at Heat View was determined to develop an intuitive operator interface after reviewing the convoluted options on the market. Beckhoff
When Jeremy Breetzke started prototyping the HeatView heat-treating system, he had no idea how many different applications and industries it would eventually be used in globally. Back in 2018, Breetzke, owner and controls specialist at Heat View Heat Treating Controls Inc., London, Ont., simply saw a gap to fill.
There was no compact, flexible option to monitor and provide reports during in situ heat treating for applications in factories, plants, or remote areas. So he started working on a design as part of his system integration business, Grand Controls Inc.
“The HeatView product grew so quickly that in 2021 we spun it off as its own company, Heat View Heat Treating Controls Inc.,” Breetzke explained.
Its original use was to ensure that welded parts reached and held the correct temperature to avoid defects. This is critical when building oil and gas pipelines or refining infrastructure, for example, where failures can be costly and environmentally catastrophic. The system has been used for that purpose in aerospace, mining, shipbuilding, petrochemical, and more. But it has also been applied to power generation and high-velocity combustion. Once the work is completed, the unit provides the necessary quality control reports.
During development of the HeatView system, Scott Fong, group director at KASI Technologies Inc., Sherwood Park, Alta., has provided technical input about the heat-treating process. KASI sells and rents field heat-treating equipment and consumables, so Fong knew there was a need for a more a compact, flexible platform, but didn’t know just how broadly it would apply.
“There are so many interesting applications that we never thought of,” Fong said. “And it’s used in very harsh environments, often out in the elements for days, so the technology has to hold up.”
Technology Demands Turn Up the Heat
The Heat View team had several additional goals for their system. First, the product had to be easy to transport and set up. Second, it needed to flexibly adapt to customers’ requirements, such as accommodating different types of current transformer (CT) coils or communicating via various fieldbus protocols to existing equipment. Third, it needed to be easy to use with an intuitive operator interface, whether the customer wanted a built-in control panel or simply to plug in a laptop.
Breetzke and Fong worked through the end of 2018 to find the ideal answer to these questions. But demand sped up the timeline to finalize the system. Breetzke knew a flexible automation platform would be key not only to meeting the timeline, but also to creating a scalable, adaptable solution for future orders. He had been working with Beckhoff Canada since 2017 for applications with his system integration business, and the company’s EtherCAT and PC-based control technologies seemed like an ideal fit for the HeatView system.
PC Control
There are several Heat View Heat Treating System models with customization options. The most portable is the ConPak stand-alone 24-channel temperature controller, which is built into a rugged plastic case for easy setup and portability. In addition, the company provides an embedded controller for installation into new or existing equipment and generator panels that mix the embedded controls system with all necessary electronics.
From an automation technology perspective, both controllers are very similar. Scalable, fully integrated control technologies from Beckhoff allow the company to use either a C6015 ultra-compact industrial PC (IPC) or a CP6606 panel PC when customers want a built-in 7-in. industrial touch screen.
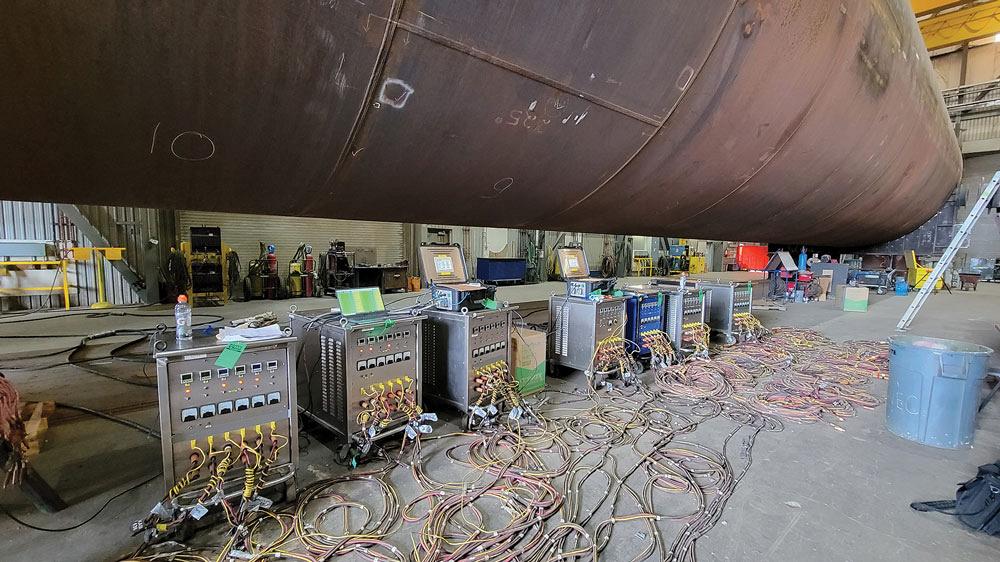
The system optimizes in situ heat treating for a range of applications, including shipbuilding, petrochemicals, mining, aerospace, and more. Heat View Heat Treating Controls Inc.
“Both controllers run the same Windows version, along with TwinCAT 3 automation software, of course,” Breetzke said. “So, the code that we wrote for the CP6606 was easy to port over to the C6015, and we could write custom code in C# and C++, which isn’t possible on a traditional PLC.”
By leveraging TwinCAT 3 from Beckhoff, the Heat View team benefitted from a universal end-to-end engineering and run-time platform for automation. TwinCAT integrates with Microsoft Visual Studio, which empowers engineers to program in a familiar, contemporary environment with the language that best fits their application. That includes IEC 61131-3 programming languages with their object-oriented extensions, predefined or custom function blocks, and computer science standards.
Breetzke appreciated having Structured Text as a programming option, as well as the ability to deploy functions built into the libraries.
“TwinCAT has a vast array of libraries that include many function blocks that aren’t very common with PLCs, such as file read and write,” Breetzke explained. “This makes code development much faster.”
EtherCAT I/O Measures Up to Heat View’s Requirements
The EtherCAT industrial Ethernet system simplifies industrial networking for Heat View. While their system doesn’t require EtherCAT’s real-time speeds, it does take advantage of its openness and flexibility. Beckhoff’s variety of bus couplers and gateways to more than 30 common protocols ensure Heat View can connect to all kinds of modern control and supervisory control and data acquisition (SCADA) systems.
“Customers have asked us to integrate the systems with EtherNet/IP, PROFINET, and even Modbus Serial,” added Breetzke. “The only question I’ve needed to ask was, ‘Why are you still using Modbus Serial?’”
Heat View uses various EL series EtherCAT terminals for basic input and output of signals. However, even more specialized measurement modules retain the same compact 12-mm housing. For the HeatView systems, these include the EL2624 four-channel relay output and EL3174 four-channel analogue input.
The EL2624 offers a relay contact up to 125-V alternating current (AC) or 30-V direct current (DC), reliably cycling in the field for years. “The EL2624s are phenomenal; they have a ridiculously long lifetime,” Breetzke said. “I would expect maybe 10 million cycles out of this type of terminal, but most the cards in the field are performing well beyond that. And I haven't had any terminals fail in the field from usage, which blows my mind.”
With four individually parameterizable inputs, the EL3174 supports signals ranging from -10/0 to +10 V or -20/0/+4 to +20 mA on each channel. This helps the HeatView systems adapt to changing customer requirements in terms of current transformers, according to Breetzke.
“Because the EL3174s do positive and negative voltage measurement, we can use them with various CT types. With most heat-treating control solutions, changing the CT type would require opening up the console, rewiring it, and replacing all the CTs – or using very expensive ones that rectify the signal and feed it back into their controllers,” Breetzke noted.
The EL3174 terminals allow the HeatView system to feed the AC signal from any CT into the system, then calculate the current going out. The system can use that for fault analysis and checking the power, Fong explained.
“We were able to design ours in such a way that it could adapt to any existing hardware rather than having to order a proprietary CT coil.”
A Hot Commodity
These systems empowered the Heat View team to meet all their goals and deliver a scalable, lightweight product for countless methods of heat treatment. Through purposeful, innovative design, they delivered a system that could handle challenging environments.
“Sometimes, crews weld pipelines in remote areas where they camp and use generators for power. Other times, they’re working on large facilities and move the setup around frequently,” Breetzke said. “It’s much easier to pull a 45-lb. system out of your pickup and plug in four cables than transport traditional consoles that often weigh 800 lbs. or more.”
The system’s next step will involve additional IoT connectivity for reporting and system updates. Currently, Heat View appreciates the ability to communicate quality control data to an operator’s laptop using an Ethernet cable and the automation device specification (ADS) protocol. Since TwinCAT engineering software is a free download from the Beckhoff website, customers can also easily install updates. In the future, the inherent connectivity of Beckhoff controls and support for vertical communication protocols—such as OPC UA, MQTT, and AMQP—will allow them to send reports and push updates from the cloud.
What continues to be important is delivering better technology for heat treatment, according to Fong. As both a customer and advisor on the system’s development, he hopes to continue to streamline operation with new tools.
“We're monitoring so many different variables and mitigating faults to create a foolproof system. Our systems integrate elements of AI, so they can learn on the fly and detect problems while factoring in external variables,” Fong said. “These capabilities are game-changers compared to what's on the market, and the next-generation products we have in development will be even better. Our further work will only continue to differentiate us as a leader in heat treatment.”
James Figy is marketing content leader at Beckhoff Automation LLC, www.beckhoff.com.
Heat View Heat Treating Controls Inc., heatviewcontrols.com
About the Author
subscribe now
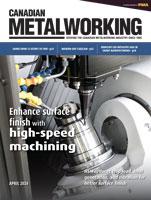
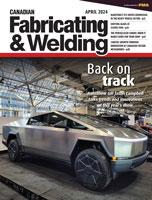
Keep up to date with the latest news, events, and technology for all things metal from our pair of monthly magazines written specifically for Canadian manufacturers!
Start Your Free Subscription- Trending Articles
Aluminum MIG welding wire upgraded with a proprietary and patented surface treatment technology
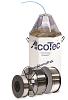
Hypertherm Associates partners with Rapyuta Robotics
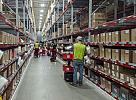
Gema welcomes controller

Brushless copper tubing cutter adjusts to ODs up to 2-1/8 in.
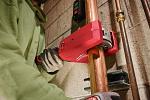
HGG Profiling Equipment BV names Western Canada area sales manager
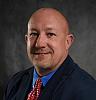
- Industry Events
MME Winnipeg
- April 30, 2024
- Winnipeg, ON Canada
CTMA Economic Uncertainty: Helping You Navigate Windsor Seminar
- April 30, 2024
- Windsor, ON Canada
CTMA Economic Uncertainty: Helping You Navigate Kitchener Seminar
- May 2, 2024
- Kitchener, ON Canada
Automate 2024
- May 6 - 9, 2024
- Chicago, IL
ANCA Open House
- May 7 - 8, 2024
- Wixom, MI