- FMA
- The Fabricator
- FABTECH
- Canadian Metalworking
Recycling Carbide Benefits Go Beyond Sustainable Manufacturing
- May 25, 2015
- News Release
- Management
More and more used carbide cutters, inserts, tips, and sludge are finding second lives outside of landfills. Carbide recycling is trending up, according to tooling suppliers and recyclers.
Increasing respect for the importance of sustainable manufacturing and the desire to break away from reliance on Chinese- based tungsten supplies may be contributing to the upward trend, but manufacturers are also finding that recycling can provide an additional income stream with little to no effort. A bin to collect carbide scrap and time to ship it to a recycler or tooling manufacturer with a recycling program are the only investments required.
Many tooling suppliers are closing the carbide loop by establishing their own recycling facilities and creating programs that make it easy for their customers to collect, return, and profit from participation. In turn, they gain a source for carbide.
Seco Tool LLC’s North American Used Carbide Recycling Program collected 15 percent more used carbide in 2014 than in the previous year, processing 144,877 lbs. of used carbide tools. The program was recognized with the 2014 national Best and Brightest Sustainable Companies™ Award from the National Association of Business Resources.
“We are deeply committed to sustainability and being a leader in environmental initiatives,” said Robert Keenan, president of Seco Tools. “Plus, our customers appreciate the opportunity this program provides to them to contribute to a cleaner, safer environment.”
Using reclaimed carbide can also lower manufacturing costs of new tooling.
Sandvik Coromant reuses 95 percent of the recycled carbide from worn inserts and round tools. The company reports that using the recycled materials to make tools requires 70 percent less energy than working with virgin raw materials.
subscribe now
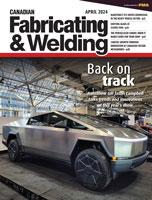
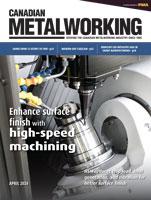
Keep up to date with the latest news, events, and technology for all things metal from our pair of monthly magazines written specifically for Canadian manufacturers!
Start Your Free Subscription- Trending Articles
Automating additive manufacturing
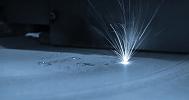
Identifying the hallmarks of a modern CNC
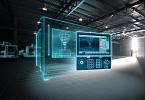
CTMA launches another round of Career-Ready program
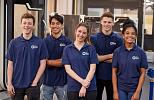
Collet chuck provides accuracy in small diameter cutting
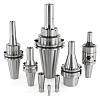
Sandvik Coromant hosts workforce development event empowering young women in manufacturing
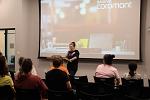
- Industry Events
MME Winnipeg
- April 30, 2024
- Winnipeg, ON Canada
CTMA Economic Uncertainty: Helping You Navigate Windsor Seminar
- April 30, 2024
- Windsor, ON Canada
CTMA Economic Uncertainty: Helping You Navigate Kitchener Seminar
- May 2, 2024
- Kitchener, ON Canada
Automate 2024
- May 6 - 9, 2024
- Chicago, IL
ANCA Open House
- May 7 - 8, 2024
- Wixom, MI