Editor
- FMA
- The Fabricator
- FABTECH
- Canadian Metalworking
Is manufacturing at an evolutionary crossroads?
To remain successful, shops need to innovate. Those that don’t will find they are no longer competitive
- By Joe Thompson
- March 22, 2022
In 1965 artist Rudolph Zallinger created the famous illustration “The Road to Homo Sapiens.” Now called “The March of Progress,” this artwork illustrates 25 million years of human evolution in six easy-to-understand steps from the ape-like Dryopithecus, who is drawn crouched over and walking on all fours, to the cellphone-ready modern human five places to its right.
It’s a fine illustration, all right. But it’s all wrong.
In reality, the progress of the human species had many more starts and stops, sidetracks, and crossroads than are shown in Zallinger’s drawing. Recent discoveries of the prehistoric human-like Denisovans and the more hobbit-like Beornus honeyi show clear evidence of the divergent forks along our evolutionary road.
Manufacturing at the moment also seems to be at a crossroads in its evolution. Many shop practices still are seen as both old-school and necessary, whether it’s hand-bombing raw material and parts around the shop, scribbling notes on coffee-stained paper drawings, or having a run-it-until-it-wrecks mentality.
This thinking needs to end up in the industry’s trash bin along with the shop’s ashtrays, pin-up calendars, and any other outdated material.
Shops that are hesitant to enter their next phase need to understand that they can’t stay the same forever. The industry will change with or without them.
The Industrial Internet of Things, Industry 4.0, and digital/smart manufacturing essentially all mean the same thing. Whether your business is small or large, and whether or not you have an on-staff digital champion, it’s important to know how to take the first steps towards digitalization.
The path to digitalization starts with collecting data from your machines, cutting tools, quality systems, and even your operators. This data collection leads to analysis, which leads to better decision-making.
Shops that adopt digitalization practices will have much better information and, therefore, make more-informed decisions on everything from true cost per part to maintenance schedules. For example, “smart” machines and cutting tools identify chatter better, which directly leads to improved part quality and longer tool life. But this can be done only if the machine, tool, and control talk to each other in a common digital manner and easily convey this information to the operator in an easy-to-understand way.
On the eve of this massive shift, shops that want to remain successful will innovate. Those that don’t will find they are no longer competitive. They will be on the outside looking in. They’ll be dragging their knuckles.
subscribe now
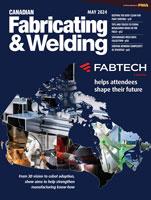
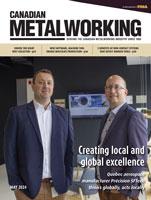
Keep up to date with the latest news, events, and technology for all things metal from our pair of monthly magazines written specifically for Canadian manufacturers!
Start Your Free SubscriptionAbout the Author
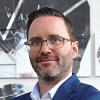
Joe Thompson
416-1154 Warden Avenue
Toronto, M1R 0A1 Canada
905-315-8226
Joe Thompson has been covering the Canadian manufacturing sector for more than two decades. He is responsible for the day-to-day editorial direction of the magazine, providing a uniquely Canadian look at the world of metal manufacturing.
An award-winning writer and graduate of the Sheridan College journalism program, he has published articles worldwide in a variety of industries, including manufacturing, pharmaceutical, medical, infrastructure, and entertainment.
- Trending Articles
Sustainability Analyzer Tool helps users measure and reduce carbon footprint
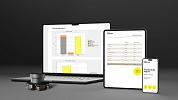
GF Machining Solutions names managing director and head of market region North and Central Americas
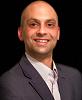
Mitutoyo updates its end-user portal
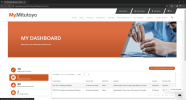
Enhance surface finish with high-speed machining
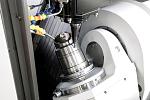
CME's Health & Safety Symposium for Manufacturers
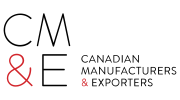
- Industry Events
Automate 2024
- May 6 - 9, 2024
- Chicago, IL
ANCA Open House
- May 7 - 8, 2024
- Wixom, MI
17th annual Joint Open House
- May 8 - 9, 2024
- Oakville and Mississauga, ON Canada
MME Saskatoon
- May 28, 2024
- Saskatoon, SK Canada
CME's Health & Safety Symposium for Manufacturers
- May 29, 2024
- Mississauga, ON Canada