- FMA
- The Fabricator
- FABTECH
- Canadian Metalworking
Turn on the milling machine
Maker of thin-wall moulds shortens lead times by performing turning operations on its milling machine
- By Canadian Metalworking
- August 27, 2020
- Article
- Metalworking
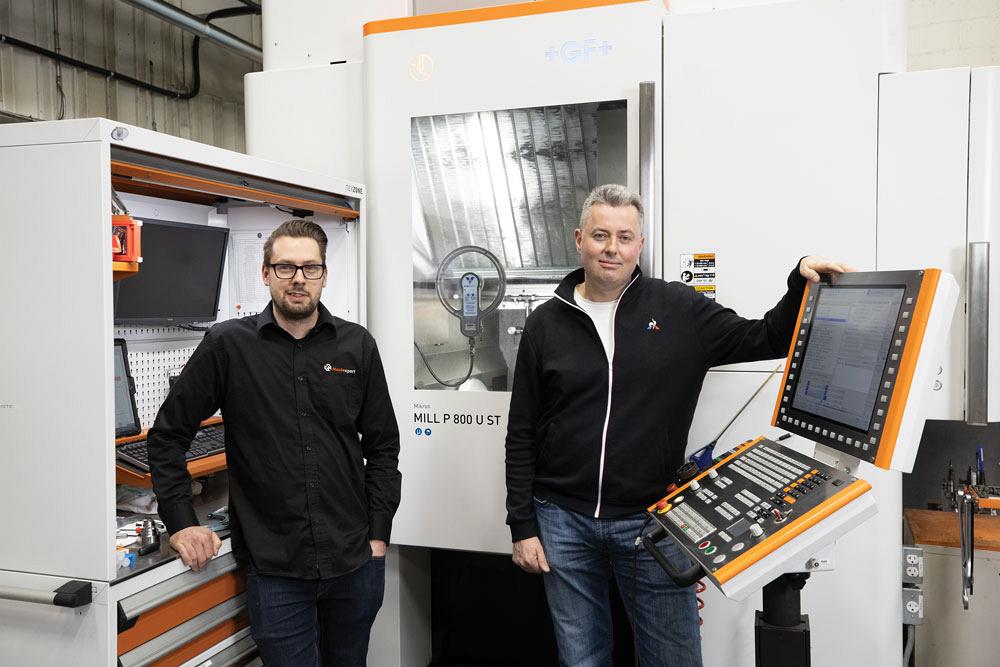
Company CEO Steve Nadeau (right) and Project Manager Marc De Grandmont stand with the company’s Mikron Mill P 800 U ST from GF Machining Solutions.
Situation
Moulexpert Inc., Levis, Quebec, a designer and manufacturer of multicavity injection moulds for the food packaging industry’s thin-wall packaging sector opened in 2001 and its customer base now spans Eastern Canada, Europe, and the U.S. The mouldmaker needed to meet its customers’ demand for faster turnaround times, and with the goal of expanding its footprint and growing its share of this niche market, it began its search for precise, repeatable, and versatile machine tool technology.
Initially the company focused on plastic injection moulds for the packaging industry, but around 2011 it decided to refocus on its strength and specialize primarily in designing and manufacturing thin-wall packaging moulds. This decision heavily influenced the type of machine tool technology the shop needed.
Not long after joining Moulexpert in 2011, company CEO Steve Nadeau asked his team what they thought the shop’s true strengths and expertise were, and their reply, he said, was the focus on thin-wall packaging.
“We had solid experience in that sector and had been doing it since the shop started. We also had been successful in repairing and modifying moulds for world-class thin-wall mouldmakers, and doing so taught us what works and what doesn’t when it comes to mould design and production,” said Nadeau.
Manufacturing thin-wall moulds presents numerous challenges. It’s more difficult to inject plastic into the mould cavities because the flow channels are more than merely “thin” at just 15-thousandths of an inch. During the plastic injection process, these thin flow channels create high pressure inside the tool.
Even with a good mould design, any uneven wall thickness will have physical effects on the mould and prevent it from producing good containers. According to Nadeau, it was for this reason that any purchased machine tool must be able to produce mould components with tolerances in the range of 5 microns.
Nadeau and his team now had a newly streamlined business model and were confident in their ability to be successful in what was becoming a fast-growing specialty market. They doubled down on weaving customer experience into their long-term business strategy. With a single product manager overseeing each project from beginning to end, the company moved toward a one-customer-at-a-time approach to the design and manufacture of their moulds.
As the shop positioned itself for further growth and put its new business plan into action, Nadeau and his colleagues decided the time was right to invest in more machine tool capacity – especially in terms of roughing, finishing, and turning of mould cavities. However, the shop had to be mindful of its limited floor space when it came to machine size.
Initially the company considered a lathe, but determined that wasn’t a sufficiently versatile option. According to Nadeau, they were looking for the “Swiss army knife” of machines – something small that could do a lot. The shop looked at alternatives like a vertical turning centre but estimated it would be idle up to 90 per cent of the time, and its capabilities were limited to only turning parts for the round container moulds. They needed something that did more than turn, including rough and finish milling.
Resolution
The company finally found what it needed in GF Machining Solutions’ Mikron Mill P 800 U ST. The shop purchased the machine in 2018, and according to Nadeau, it immediately made a difference in the shop’s operations.
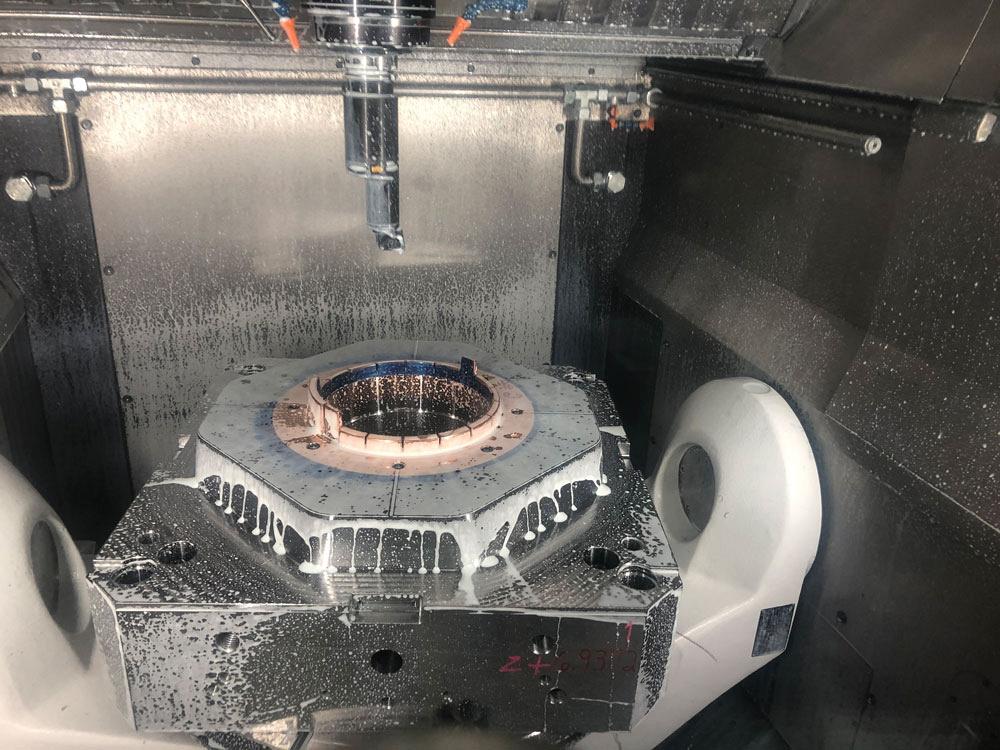
The company’s new machine can drill and tap holes in mould cavities, then rough and finish-turn them to within 5-micron tolerances.
Designed to achieve high removal rates and high precision on round and other challenging mould cavity components, the machine, with its 800-kg part table capacity, provided the capabilities Moulexpert needed to meet its production and rigid quality requirements. Plus, it was a machine that didn’t consume large amounts of floor space.
The new machine enabled the shop to reduce lead times and strengthen the customer experience. It also helped Moulexpert be more competitive by improving productivity, especially for thin-wall moulds for round containers.
“If we had purchased a turning machine, we wouldn’t have 5-axis capabilities, and we would have to buy two machines,” said Project Manager Marc De Grandmont. “We also didn’t have enough space and weren’t interested in modifying the building, so we had to look for a machine that met all of our requirements.”
The company’s machine mills and turns and has a 20,000-RPM spindle with a hydraulic system that locks it in place for turning operations. Additionally, the machine manufacturer’s patented machine and spindle protection system protects the spindle in the event of a crash. The machine also is automation-ready, with such features as automated pallet handling, without restricting access to the work area.
For fully optimal part production, the machine’s intelligent spindle monitoring (ISM) feature helps save on tooling costs by extending the machine’s working life, increasing part quality, and reducing machining cycle times. ISM displays the milling process-related vibrations in the X, Y, and Z directions, which provides the machine operator with the essential information for process optimization.
“The machine’s compact design, in addition to its turning functionality to run round containers, was important,” Nadeau said. “At the same time, we liked the machine’s powerful, versatile spindles that allow us to drill and tap holes in mould cavities, then rough and finish-turn them to within 5-micron tolerances.”
The shop’s investment in the machine enabled it to increase capacity by 25 per cent, and today operations continue to include design, programming, EDM, conventional machining, polishing, assembly, and laser welding. The shop now ships more new moulds per week and plans to expand its footprint in Canada and expand further into the U.S. market.
Moulexpert continues to differentiate itself in the marketplace by staying true to its one-customer-at-a-time approach to doing business, which, despite the company’s small size, allows it to compete with larger manufacturers. With business growing and difficulties finding skilled mouldmaking labour, the shop will eventually need to invest in more equipment and programming technology for automation integration.
This will allow the shop to make its current workforce better able to manage the increase in production volume created by further growth.
GF Machining Solutions, www.gfms.com
Moulexpert, www.moulexpert.com
About the Author
Related Companies
subscribe now
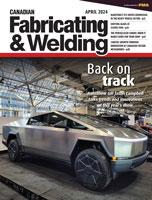
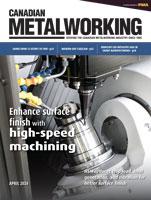
Keep up to date with the latest news, events, and technology for all things metal from our pair of monthly magazines written specifically for Canadian manufacturers!
Start Your Free Subscription- Trending Articles
Automating additive manufacturing
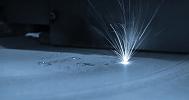
Sustainability Analyzer Tool helps users measure and reduce carbon footprint
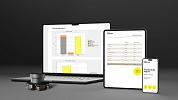
CTMA launches another round of Career-Ready program
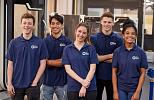
Sandvik Coromant hosts workforce development event empowering young women in manufacturing
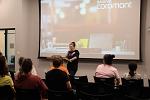
GF Machining Solutions names managing director and head of market region North and Central Americas
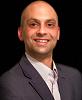
- Industry Events
MME Winnipeg
- April 30, 2024
- Winnipeg, ON Canada
CTMA Economic Uncertainty: Helping You Navigate Windsor Seminar
- April 30, 2024
- Windsor, ON Canada
CTMA Economic Uncertainty: Helping You Navigate Kitchener Seminar
- May 2, 2024
- Kitchener, ON Canada
Automate 2024
- May 6 - 9, 2024
- Chicago, IL
ANCA Open House
- May 7 - 8, 2024
- Wixom, MI