- FMA
- The Fabricator
- FABTECH
- Canadian Metalworking
Technology Spotlight: Horizontal machining centre
Power, precision, and palletization push HMC productivity
- By Canadian Metalworking
- September 7, 2022
- Article
- Metalworking
Not all horizontal machining centres are the same. While some provide powerful spindles and have robust construction for aggressive roughing operations, others are built more for high-precision surface finishing.
However, truly productive HMCs can perform both operations equally well, which eliminates the need for shops to rough parts on one machine and finish-cut them on another. Productivity is further enhanced when shops incorporate these performance-balanced HMCs into palletized cells that cost-effectively automate both high-volume and high-mix/low-to-medium volume jobs.
Performance-balanced HMCs are well-thought-out machines when it comes to every aspect of their designs. Machine base, axis movement, spindles, horsepower, and torque are all carefully considered. All are optimized for both roughing and finishing.
An example of this type of machine is Mazak’s HCN-6800 NEO.
Machine Construction
To create both precision and rigidity, the machining centre includes the company’s hybrid linear roller guides on its X, Y, and Z axes, and a rigid mounting surface for the X- and Y-axis linear guides that minimizes distortion on the bed during axis travel. These guide ways give shops the rigidity of box ways combined with the benefits of linear guides, the company states.
The machine’s base is an X-axis construction with the X-axis linear guides mounted on a slanted surface at the bottom of the machine’s column. The result is high-accuracy positioning and heavy-duty machining capability because the axis ballscrew is close to the column’s centre of gravity.
This construction also enables the machine to move pallet/table loads of up to 1,500 kg at rapid traverse rates of 60 m/min. in the X, Y, and Z axes. To handle these table loads, the machine sports a pallet clamping system that uses four conical cones. The design not only provides maximum clamping strength for high metal removal rates, but also ensures consistent part accuracy from the bottom of the workholding zone to the top. In turn, this allows for greater cutting real estate and greater flexibility to run more multiple parts or larger ones on a single pallet face.
Optional direct-drive motor rotary tables also contribute to efficient, high-speed, high-precision workpiece positioning, the company reports.
The HMC transfers driving power directly to the rotary table axis, eliminating common power transmission components, such as worm shafts and worm gears, that can generate backlash. Additionally, auto-tuning functions further optimize acceleration/deceleration of inertia on the table to reduce positioning times.
For example, the machine’s rotary table indexes (90 degrees) in as quickly as 1.2 seconds, while it maintains a bidirectional positioning accuracy of 7.0 seconds at minimum increments of 0.0001 degree. This table rotation speed and accuracy are possible because the direct-drive motor does not require the pallet to lift then clamp upon rotation.
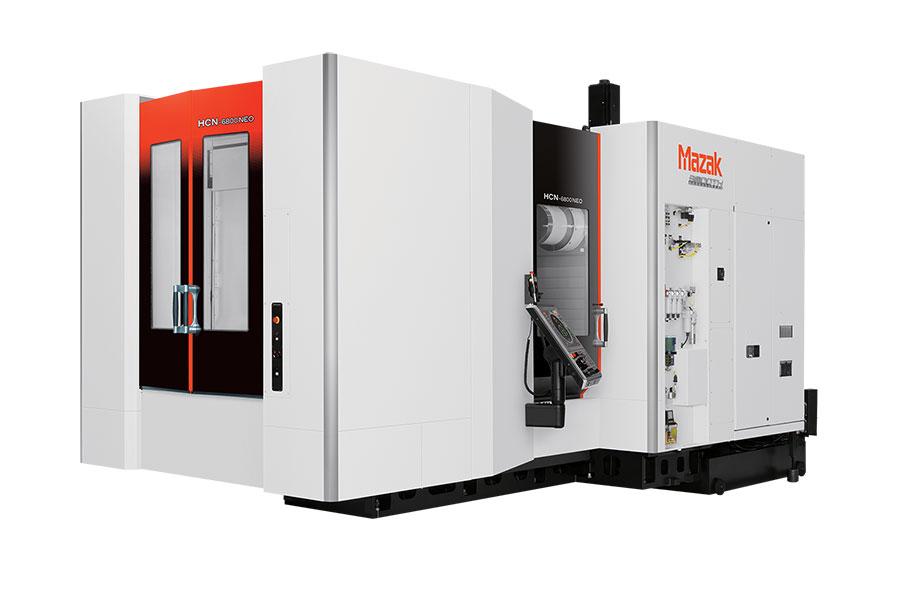
The Mazak HCN-6800 NEO horizontal machining centre has spindles that are optimized for both roughing and finishing.
Spindle Power
Rigid bases and high-precision axis motion form the foundation that supports numerous spindle options. These include not only standard spindle types that effectively rough and finish, but also optional types such as high speed or high torque.
This machine comes with a 10,000-RPM direct-drive spindle as standard that puts out 45 kW of power.
The elimination of drive gears minimizes power loss and spindle vibration, improving machine surface quality and extending tool life, the company states.
Temperature-controlled cooling oil circulates around the spindle bearings and headstock to minimize any thermal change to the spindle. These integral spindle motor designs also allow for faster, more precise tapping along with quick and accurate spindle directional changes and precision tool tip positioning.
The company’s high-torque, 8,000-RPM spindle provides powerful machining of steel and cast iron and the high-speed, 16,000-RPM spindle with changeable bearing preload ensures rigidity during low-speed machining, as well as high-speed machining of aluminum.
Automated for Productivity
The nature of the machine tool’s design enables long-reach milling, drilling, and boring operations. In addition, spindle utilization is increased thanks to an integrated two-pallet changer that allows parts to be loaded/unloaded while the machine’s spindle continues to work uninterrupted.
For even higher HMC productivity, pallet changing systems, such as the company’s PALLETECH system, quickly change pallets, even when dealing with heavy workpieces. Shops also gain the convenient option of adding more machines and increasing pallet storage capacity after initial installation because the system is modular.
The automation system also can include numerous loading stations with capabilities such as wash, tilt, and precision centring. Shops can pace their capital investment to match the growth of their business via the ability to have as many as 16 machines in one system, six to 240 pallets, and as many as eight loading stations.
Shops that use this technology can be agile—running one part, then two hours later, for instance, running a completely different one, then an hour after that yet another different one. For shops in which cost per part is just as critical as quality and output, the increase in efficiency from HMCs and pallet systems results in faster turnarounds with lower costs.
Regardless of part types or production environments, today’s HMCs that offer the power and precision to perform both roughing and finishing operations with equal effectiveness are the key to productivity. Shops can take that productivity even further when they pair these HMCs with palletized cells that provide cost-effective automation and the flexibility to handle both high-volume and high-mix/low- volume jobs within the same cell.
Mazak Canada, www.mazakcanada.com
About the Author
Related Companies
subscribe now
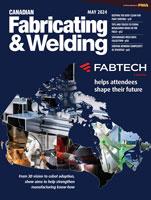
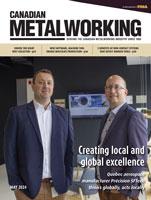
Keep up to date with the latest news, events, and technology for all things metal from our pair of monthly magazines written specifically for Canadian manufacturers!
Start Your Free Subscription- Trending Articles
Sustainability Analyzer Tool helps users measure and reduce carbon footprint
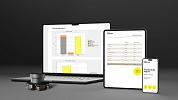
Enhance surface finish with high-speed machining
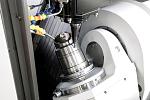
Equispheres secures $20 million investment round
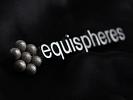
Solid carbide drills produce precision holes in short chipping materials
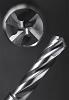
Okuma announces new personnel appointments
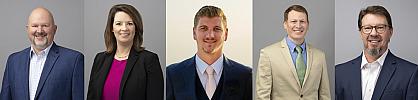
- Industry Events
Automate 2024
- May 6 - 9, 2024
- Chicago, IL
ANCA Open House
- May 7 - 8, 2024
- Wixom, MI
17th annual Joint Open House
- May 8 - 9, 2024
- Oakville and Mississauga, ON Canada
MME Saskatoon
- May 28, 2024
- Saskatoon, SK Canada
CME's Health & Safety Symposium for Manufacturers
- May 29, 2024
- Mississauga, ON Canada