Associate Editor
- FMA
- The Fabricator
- FABTECH
- Canadian Metalworking
Take advantage of multitasking
Multitasking machines have a robust design and range from simple 2-axis to hybrid additive/subtractive
- By Lindsay Luminoso
- June 2, 2020
- Article
- Metalworking
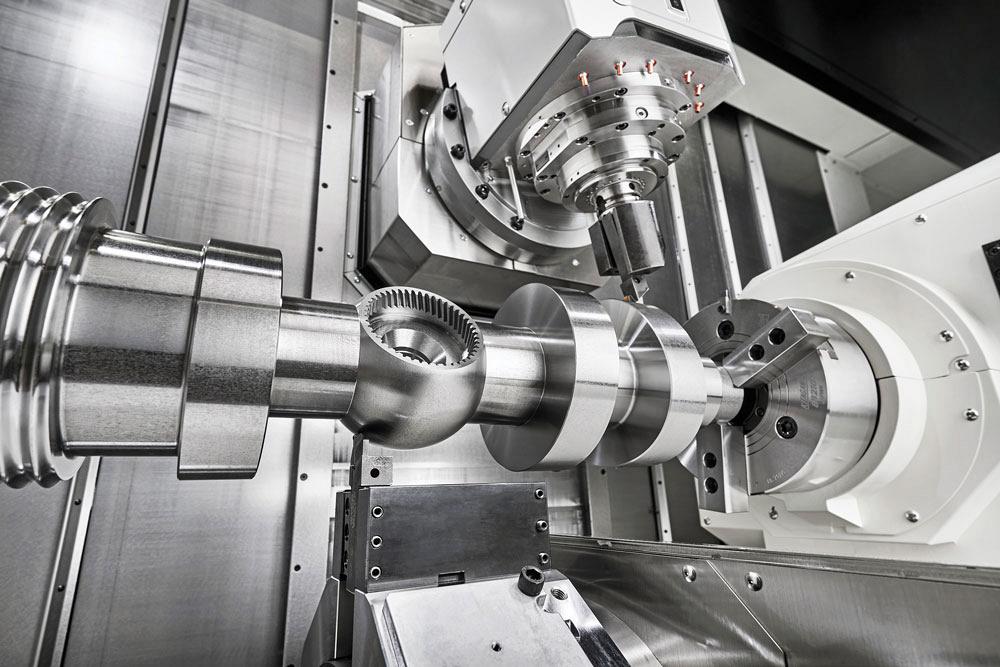
A multitasking machine is recommended for shops that are looking to consolidate the process, as it can replace a minimum of two machines, generally takes up a smaller footprint compared to traditional single machine, and requires only one operator. Photo courtesy of DMG MORI.
For shops that both turn and mill parts, it’s time to start looking into multitasking machines. These workhorses can perform these two operations in one footprint, eliminating the need to move the workpiece through the shop. Today’s multitasking machines have a robust design and vary in operational capability depending on a shop’s needs. Adding this machine on the shop floor goes beyond simply combining turning and milling operations though. It can help transform a shop’s ability to effectively implement an integrated approach to production.
Why Multitasking?
With many types of machines available on the market, shops may not see the value of a multitasking machine. Right off the bat, these machines tend to be much more expensive than their single-operation counterparts. And although that might be a strike against them, shops should not undervalue the advantages of having one on the shop floor.
"We usually recommend the multitasking machine when customers want to consolidate the process," said Siroos Askari, product sales manager, DMG MORI Canada Inc., Mississauga, Ont. "If a part has many operations like turning and milling, the multitasking machine can put all these in one setup. With the turn-mill technology of the multitasking machine, the operator is able to load the part for spindle one and then the part can be transferred and finished with spindle two. The part doesn’t have to move from machine to machine. Therefore, the setup time will be drastically reduced. Additionally, part precision will not be affected because there is less handling."
Beyond this, a multitasking machine can replace a minimum of two machines, generally takes up a smaller footprint compared to traditional single machines, and requires only one operator. This is important for shops that have multiple sequestered machining departments, where the milling machines are kept in one area and the turning machines in another.
"Traditionally, to produce a part requiring both turning and milling operations, it would run through a shop’s turning centre department, then move to its milling department either to a vertical or horizontal machining centre or to both," said Joe Wilker, advanced multitasking manager, Mazak Canada, Cambridge, Ont. "That whole process could take an entire week to get a batch of 50 parts through production and out the door."
Wilker added that beyond the movement of the part from machine to machine, shops also need to consider the queue time and WIP for each of those machines. He estimates that some machines can be backlogged and take two or three days to become available to run the batch of parts, creating huge bottlenecks and further backlogs in production. With multitasking, such a scenario is simply moot.
Multitasking machines are designed for high-mix, small- to medium-volume runs. They usually are not recommended for high-volume production because multiple stand-alone machines can apply more spindles to the task. Another consideration is the types of part being produced. Where this machine shines is in the production of highly complex components, particularly in the aerospace and energy industries. They are also suited for production of small parts like those found in medical parts manufacturing. However, it is generally not recommended for extremely heavy parts that require more rigid turning and minimal milling.
"A significant benefit of multitasking is the increased part accuracy," said Wilker. "The data points on your part features don’t change because both operations (milling and turning) are done in a single setup, which eliminates any problems with stacked tolerances. This is compared to workpieces having to move between four or five different machines where accuracy is at the hands of the operator when it comes to loading and gauging the part correctly multiple times to get all the part features just right."
What to Look for in a Multitasking Machine
Over the years the multitasking machine has grown to include hundreds of different models and multiple configurations to meet any shop’s production needs. From simple 2-axis machines to highly robust hybrid additive/subtractive multitasking machines, there is something for everyone. But how do you go about choosing among the various options available?
"When we’re looking at multitasking, it’s all about the tools, tools, tools," said Kevin Smith, turning products manager, Elliott Matsuura Canada, Oakville, Ont. "The more tools that can fit in the machine, the less setup time will be needed to go from part to part. In my opinion, the more tools the better. The first thing some customers will say to me is that they don’t have that kind of volume. But you really don’t necessarily need it because not all turrets will be running at the same time. However, what this does is give the shop more flexibility and minimizes cycle time, allowing them to take on more projects."
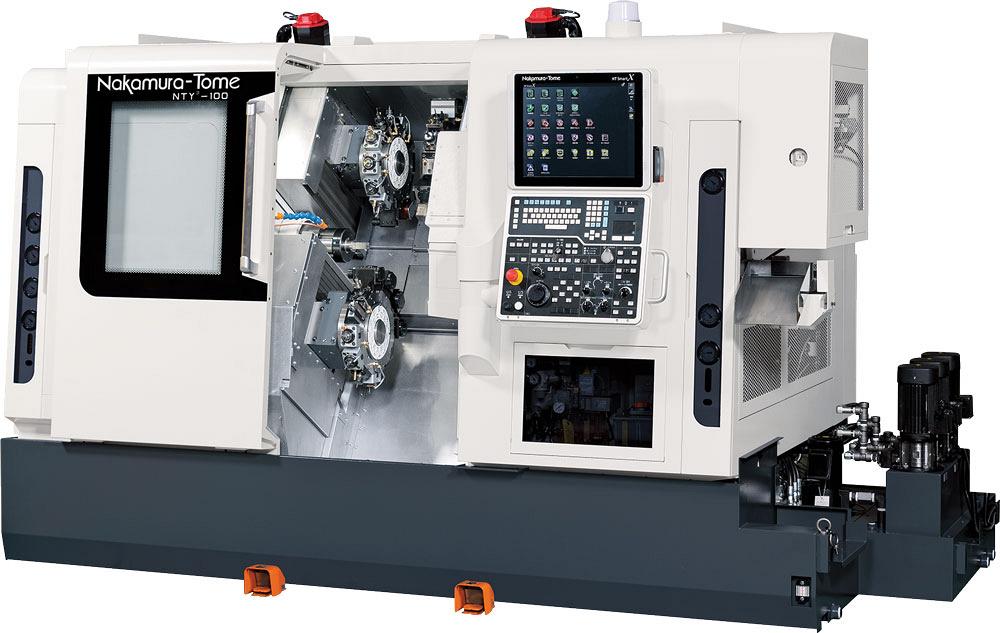
Nakamura-Tome NTY3-100 is a three-turret, 3-Y-axis multitasking machine centre, with an ergonomic 60-degree slant bed. Productivity is increased with simultaneous machining on the left- and right- hand spindles, as well as the Y axis on all three turrets. Photo courtesy of Elliott Matsuura.
One of the biggest factors is cost. These machines tend to be much more expensive than their stand-alone counterparts. However, Askari noted that the value of these machines is a shop gets all the features they need to expand in the future. It’s not just about what is needed right now, and if a shop isn’t willing to invest in the features and accessories that maximize the machine’s effectiveness, then it may not be worth looking into a machine like this. Assessing the budget, a shop can customize the multitasking machine to fit its specific needs.
"If we are looking at a turn-mill, it can have one or two spindles, and it can also have a lower turret," said Askari. "You can have a magazine with 38, 76, or more tools. Depending on the budget, you can customize the multitasking machine to fit your specific needs. I always recommend having a secondary spindle, a lower turret, and the largest tool magazine you can afford. However, this is also very application-oriented."
Askari gave the example of a long shaft. For a shop that is taking on this type of project, there is really no point in having a second spindle. A machine with a tailstock would be a better option, and instead of a lower turret, a steady rest might be better.
"Another thing to consider when purchasing a multitasking machine is the graphical user interface and how easy it is to use," said Smith. "If it’s asking you very direct and simple questions to allow you to get into production a lot faster, that’s a huge advantage. You also want to ensure, especially if this is a first-time buy, that the machine builder offers strong support to help you with any challenges that may arise and can help to maximize the machine on the shop floor."
Machine Advancements
Multitasking machines have been around for decades, and Wilker admitted that he’d be hard-pressed to find a machine shop that doesn’t have at least one on the shop floor. He said that he sells more multitasking machines today than stand-alone machines. This is because the machines have changed significantly over the years, making them faster and more rigid.
"You can now have machines perform in up to nine axes," said Askari. "The challenge with this is that if the machine sees an error with precision at the beginning of the cycle, that error will be compounded and create major issues. With heat being the enemy of precision, this type of machine requires additional cooling technology run in and around the components that could be a heat source. This creates a shield that allows the machine tool to perform operations without any heat interference. As the machines become more sophisticated, we need to ensure they are meeting accuracy requirements."
Another area of advancement is in ergonomics.
"These machines have become much more ergonomic over the years," said Smith. "Previous configurations made it somewhat challenging for the operator to interact with the machine. What we are seeing is many of the newer machines have moved the spindle closer to the front of the machine, making it easier for the operator to work. Almost every component that requires human interaction is brought forward to increase accessibility."
Smith added that moving the spindle forward also makes sense when it comes to adding automation, which is a hot topic in today’s manufacturing environment. He explained that even in the job shop, there is a push for more automation. Machine builders are aware of this trend and are building multitasking machines with this in mind so that a shop can simply add automation with few challenges.
The experts agreed that there have been a lot of changes to the machines over the years. And one of the biggest advantages is their ability to produce gears. A multitasking machine is no longer restricted to turning and milling.
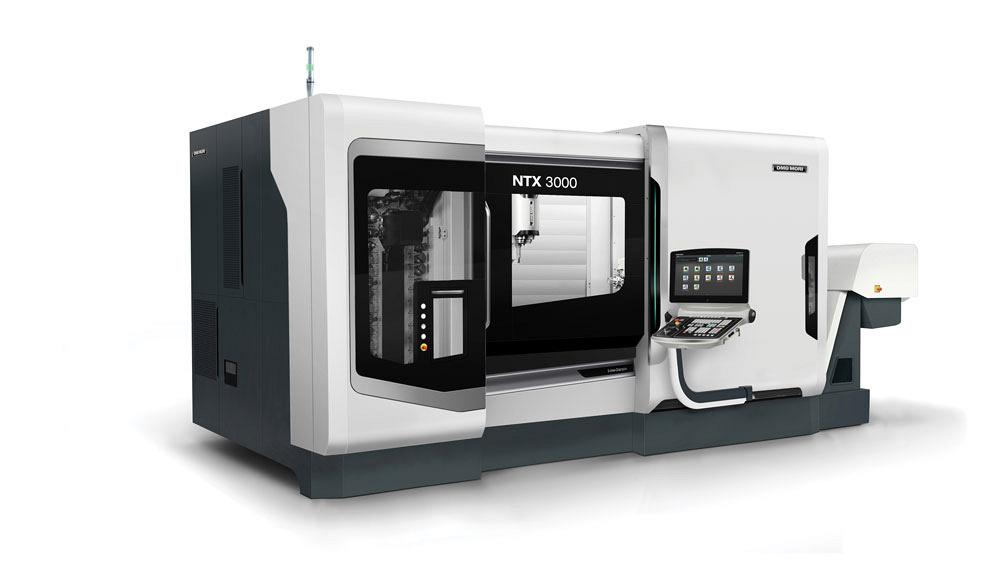
DMG MORI’s NTX 3000 turn-mill centre offers six-sided, heavy-duty machining for the aerospace industry, automotive and energy sectors, and medical engineering. It includes an upper B-axis spindle with a ±150-mm Y axis and a lower turret (BMT type) with driven tools and Y-axis (±40 mm). Photo courtesy of DMG MORI.
"Gear cutting is fairly specialized," said Wilker. "Often customers will get a part with a gear on it and have to send that component out to have the gear feature produced. This leads to significantly increased turnaround time, anywhere from one to five weeks. Today’s multitasking technology enables shops to perform gear cutting operations in-house. Gears are basically geometry, no different than contouring a bore or a bolt hole pattern. The addition of a gear program makes this multipurpose machine even more versatile."
These machines now can create gears using a number of different technologies. Single-point machining is flexible, but also slow because it’s milling one tooth at a time. Hobbing is probably the most economical and user-friendly. And if a shop wants to get into high-volume gear production, gear skiving is going to be the fastest and the only process that can do OD and ID gears in that format.
"With gear cutting, we are also seeing multitasking machines incorporate gear measuring and process adjustment for a closed-loop system within the same platform," said Wilker. "Such an ability to perform in-process gear checking helps shops not only shorten turnaround times, but also reduce cost per part."
Askari added that one of the advantages of these newer machines is their capability to perform what he calls various technology cycles. The software has been adapted to include macroprograms to enable things like gear cutting and complex machining, built right into the control. Operators can easily access these technology cycles and the machine is ready to perform a range of operations. Having a simple and easy-to-use control package is key to maximizing all that multitasking machines can do.
Future Configurations
"While I would personally like to see more grinding operations incorporated into multitasking," said Wilker, "I think additive manufacturing is going to be the future, as we are seeing with today’s hybrid multitasking machines that can produce a part that incorporates three different types of materials. This allows shops to, for instance, make some of a part’s features from a less expensive material and others that might require extra wear resistance from a second and even a third material through the additive process."
Wilker noted that AM as well as the friction stir welding process are already being integrated into next-generation multitasking machines, making them more valuable to individuals that require or may require such capabilities in the future.
"I’m expecting to see more onboard lasers," said Smith. "I also see more capability as far as measuring and inspecting tools in the machine and really pushing the boundaries of speed and accuracy of the machine."
Associate Editor Lindsay Luminoso can be reached at lluminoso@canadianmetalworking.com.
DMG MORI Canada, ca-en.dmgmori.com
Elliott Matsuura Canada, www.elliottmachinery.com
Mazak Canada, www.mazakcanada.com
About the Author
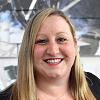
Lindsay Luminoso
1154 Warden Avenue
Toronto, M1R 0A1 Canada
Lindsay Luminoso, associate editor, contributes to both Canadian Metalworking and Canadian Fabricating & Welding. She worked as an associate editor/web editor, at Canadian Metalworking from 2014-2016 and was most recently an associate editor at Design Engineering.
Luminoso has a bachelor of arts from Carleton University, a bachelor of education from Ottawa University, and a graduate certificate in book, magazine, and digital publishing from Centennial College.
Related Companies
subscribe now
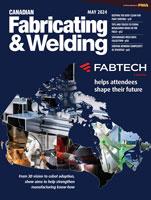
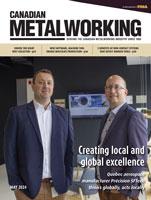
Keep up to date with the latest news, events, and technology for all things metal from our pair of monthly magazines written specifically for Canadian manufacturers!
Start Your Free Subscription- Trending Articles
Automating additive manufacturing
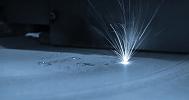
Sustainability Analyzer Tool helps users measure and reduce carbon footprint
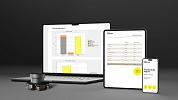
GF Machining Solutions names managing director and head of market region North and Central Americas
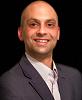
Mitutoyo updates its end-user portal
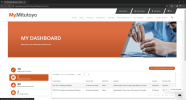
Enhance surface finish with high-speed machining
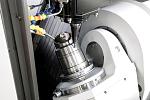
- Industry Events
CTMA Economic Uncertainty: Helping You Navigate Kitchener Seminar
- May 2, 2024
- Kitchener, ON Canada
Automate 2024
- May 6 - 9, 2024
- Chicago, IL
ANCA Open House
- May 7 - 8, 2024
- Wixom, MI
17th annual Joint Open House
- May 8 - 9, 2024
- Oakville and Mississauga, ON Canada
MME Saskatoon
- May 28, 2024
- Saskatoon, SK Canada