Associate Editor
- FMA
- The Fabricator
- FABTECH
- Canadian Metalworking
Make lights-out wire EDM a reality
Wire control, slug management, and advanced CAM all play important roles in successful unmanned operations
- By Lindsay Luminoso
- February 1, 2021
- Article
- Metalworking
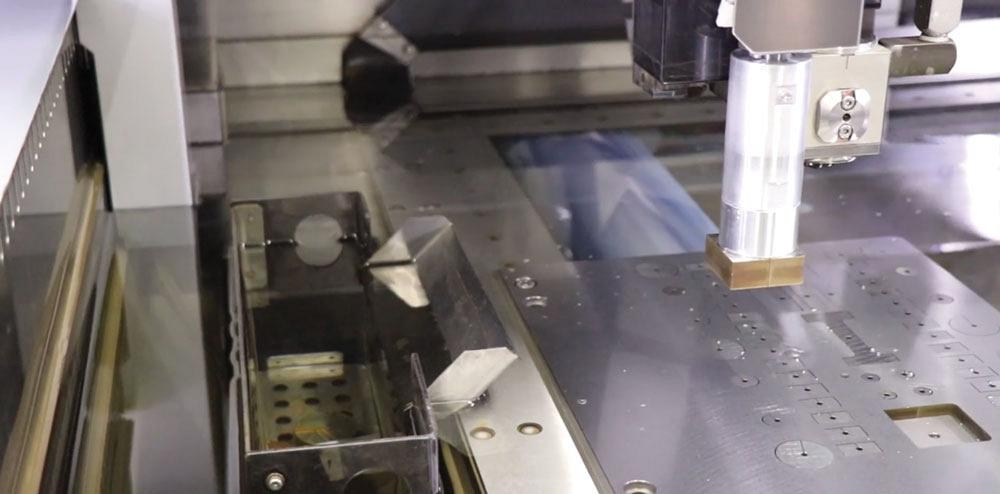
The ability to control slug removal is important for unmanned operations. The slug cannot just drop at any point during the machine cycle, as it could potentially stop or even damage the machine. Photo courtesy of Sodick.
Today’s machine shops have a lot of worries. Getting the most out of their machines is one of them. Having a process that requires an operator to stand in front of a machine day in and day out is ineffective and a waste of valuable resources. Not only that, with the skills gap, finding qualified operators is not always easy. So being able to run a machine unmanned is a huge advantage and can lead to more uptime and lights-out manufacturing.
"Wire electrical discharge machining (EDM) is basically an unmanned process," said Dave Thomas, vice-president, Sodick Inc., Schaumburg, Ill. "Typically, parts can run on a wire EDM for more than one hour without any manual interruption and could even run as long as 80 hours without any interruption or intervention from the operator with the right conditions and features."
Wire EDM is a slow machining process. And because of this, shops really tend to use it only when a part requires it. One of the advantages of this process is that once the machine is set up, it can run for quite some time before intervention is needed.
"Unlike milling, with wire EDM the cutting tool is always the same size and the operator doesn’t have to worry about cutter wear in the same way," said Brian Coward, EDM product manager, Makino, Mason, Ohio. "The wire is always moving consistently and regenerated, which makes wire EDM a very predictable process. There are two reasons why wire EDM lends itself to lights-out manufacturing: cycle time and built-in features that allow for automation."
Wire Control
Although the machine has the ability to keep the wire moving consistently, there is always the chance of wire breakage. And almost all wire EDM machines available today have an automatic wire threading or feed system to ensure that if there is a breakage, the machine can correct it.
"Not all automatic wire feeders are created the same, and some are more reliable than others," said Thomas. "The machine must be able to consistently cut the wire, move to a new position, and rethread the wire. That’s a fundamental part of a wire EDM and obviously key to unmanned machining. It’s also important to look for an automatic wire feeder that requires little maintenance so it can run for 100 to 200 hours without intervention."
Additionally, it’s important to understand the wire break repair function. Advanced wire feed systems can repair the tip of the wire, which is often badly damaged due to the break, causing wire rethreading to fail. Some systems are able to recognize this issue and remove the damaged wire tip until fresh good wire is present.
"As the machine is cutting a shape, if the wire breaks, the machine can be set up to thread at the break point," said Coward. "What that does is help speed up the process, as opposed to a more traditional approach where the machine will go back to the start hole position and rethread there."
If the machine is eight hours into a 10-hour burn and the wire breaks, going back to the starting point can add extra cycle time. It certainly won’t take another eight hours to get back to where it left off, but for shops concerned about machining uptime, threading at the breaking point is important.
Almost all systems have the capability to recover after breakage, but not all systems can repair right at the tip. A machine with advanced features like this may cost more, but in the long run, shortening cycle time and being able to run the machine unattended and lightsout can save both time and money.
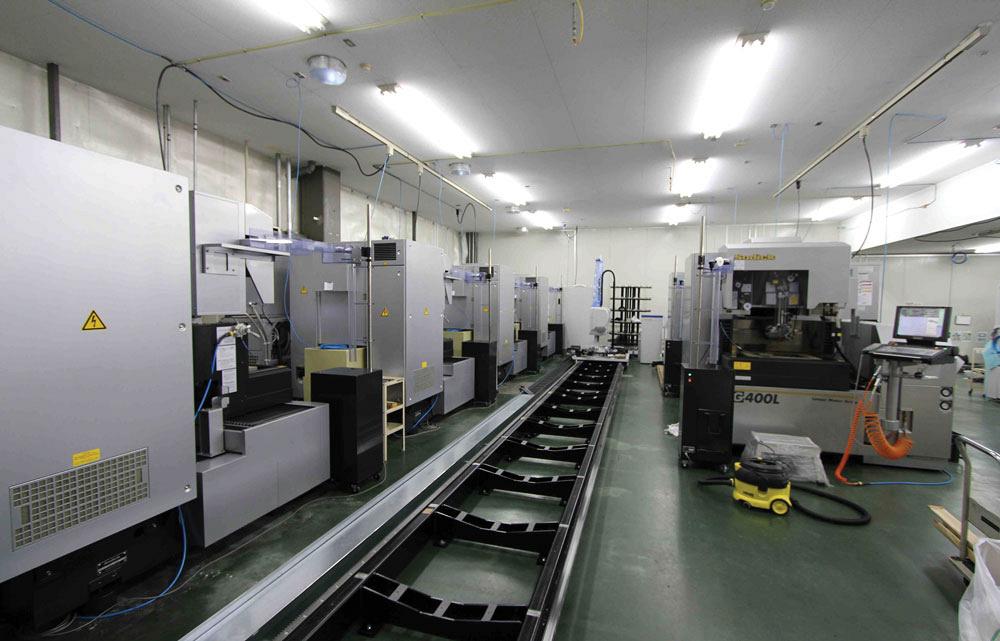
Shops set up for more production manufacturing may require advanced robotics that can be added to a track or railway system and feed multiple machines. Photo courtesy of Sodick.
Another wire consideration is wire processing.
"The ability to run large spools of wire is essential," said Thomas. "Typically, a small spool of wire may only last up to 16 hours. Having a machine that can handle and process a large spool, something in the 44-lb. range, can add 100-plus hours to the unmanned machine time."
Thomas added that it’s not just pre-processing that matters. When it comes to wire processing, once the wire has cycled through the machine, it needs to be stored in a storage bin or container, which often has a limited capacity. Some machines today have a feature that cuts the wire into small pieces.
"If the machine can’t cut the wire, it just spools into the bin," said Thomas. "And the machine may only be able to hold 40 hours’ worth of wire. A cutting mechanism allows more wire to be fit into the bin, and in some cases can extend the bin capacity to upwards of 500 hours’ worth of wire."
Slug Management
The next level of processing is the ability to remove the slug. The slug cannot just drop at any point during the machine cycle; in fact, if the slug does drop, it could potentially stop or even damage the machine.
A couple of options are available for slug management. For example, a slug retention system allows for the machine to automatically change conditions and deposit a layer of brass to prevent the slug from dropping from the workpiece. At any point the operator can intervene, interrupt the machine, and tap out each slug, which will drop from the part. This gives the operator control over the process, but it requires some preplanning and scheduled drop points to ensure the machine is running at maximum efficiency. It also requires the operator to return to the machine and manually perform the action.
For shops looking to remove operator intervention altogether, there are advanced slug removal systems. An automated system uses a robotic arm-like mechanism that is attached to the machine to remove the slug during the process. Once the slug is removed, the arm places it in a slug retention bin so that it is not impeding the machine in any way.
"The slug retention system is a standard function," said Thomas. "A more automated slug removal system is optional for shops that plan on running lights-out for any prolonged period of time. It just depends on what the shop’s needs are."
Advanced Computer-aided Manufacturing
Beyond wire and slug management, programming and setup are equally important. To get the most unmanned machine time from a wire EDM, preplanning is necessary, especially if an operator is managing more than one machine at a time.
"CAM software is very important because all the work is done upfront rather than at the actual machine," said Coward. "And this is where proper planning allows for lights-out machining. You need to think through how you are going to set parts up in the machine and process them efficiently to maximize machine uptime. Having a sophisticated CAM package will allow the programmer to plan better and schedule based on estimated machining time. If you skimp on the CAM software, you can still run the machine, but you are not going to get that optimal lights-out machining."
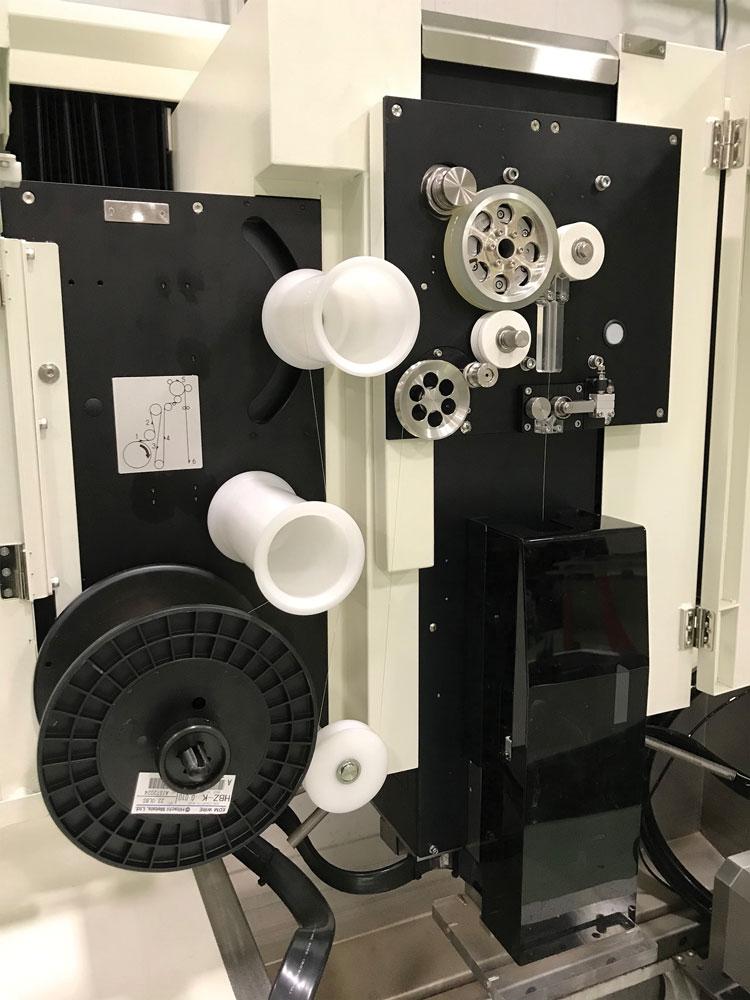
Almost all wire EDM machines available today have an automatic wire threading or feed system to ensure that if there is a breakage, the machine can correct it. Photo courtesy of Okuma.
An advanced CAM system is critical to have good lights-out performance on a wire EDM machine. Without it, a shop will spend a lot of time editing and adjusting the process parameters to fit the day-to-day needs.
Coward gives the example of an early and late strategy. In an early strategy, with multiple features, holes, and pockets, a shop can choose to rough everything out first. The machine processes by putting a tag on every opening during the roughing-out stage. Once the machine has roughed everything out, the operator must get involved to drop the slugs. The machine can then resume cutting the features. With this model, the only time the operator needs to be at the machine is during the initial setup and to drop the slugs.
There are times, however, when an operator is not available to remove the slugs at a specified time, for example, overnight. In these cases, the shop can use the CAM software to adjust the machining strategy to maximize cutting time. So instead of roughing all the features first, the machine would rough and finish all features before removing the slug.
"So now I’m getting the maximum unmanned machining time during the process," said Coward. "Then all the operator has to do is drop the slug and skim-cut the tag at the end of the machining process. Then he’s done. So those are ways that you can get the most unmanned machine time and lights-out machining. It really is about thinking the process through and programming to achieve your goal. A proper CAM system will have the capability to optimize different strategies at the click of a button."
Robot-Ready
Although wire EDM machines are already designed for unmanned operations, some more features can be added to increase lights-out capabilities, particularly robotics.
"The next level of automation is to load and unload workpieces using a robot," said Thomas. "There are a number of robots that are compatible with the EDM machines, which allows the operator to control the robot normally from the machine. In other words, the robot is a slave and that robot then can load and unload the workspace to the machine’s table. The robot can attend a singular or even several EDM machines."
Thomas added that some shops are set up for more production manufacturing and require advanced robotics beyond the load/unload automation available. In production shops, a robot can be added to a track or rail system and feed multiple machines. A more advanced system requires cell management software to control the cell to ensure maximum machine uptime.
Advanced Tech
Not all shops require robots, and the wire EDM unit can still perform unmanned operations without one. But there are some new technologies that are slowly being integrated into these machines, particularly those related to machine monitoring and remote functionalities.
"We will be rolling out an IIoT system on Makino machines," said Coward. "The machines will have sensors to better predict when the operator needs to address certain issues. And that will certainly help with downtime and unmanned machine time."
Thomas added that this type of system allows the shop to remotely monitor a machine or a number of machines. It also will provide real-time data and productivity features to help a shop make better decisions.
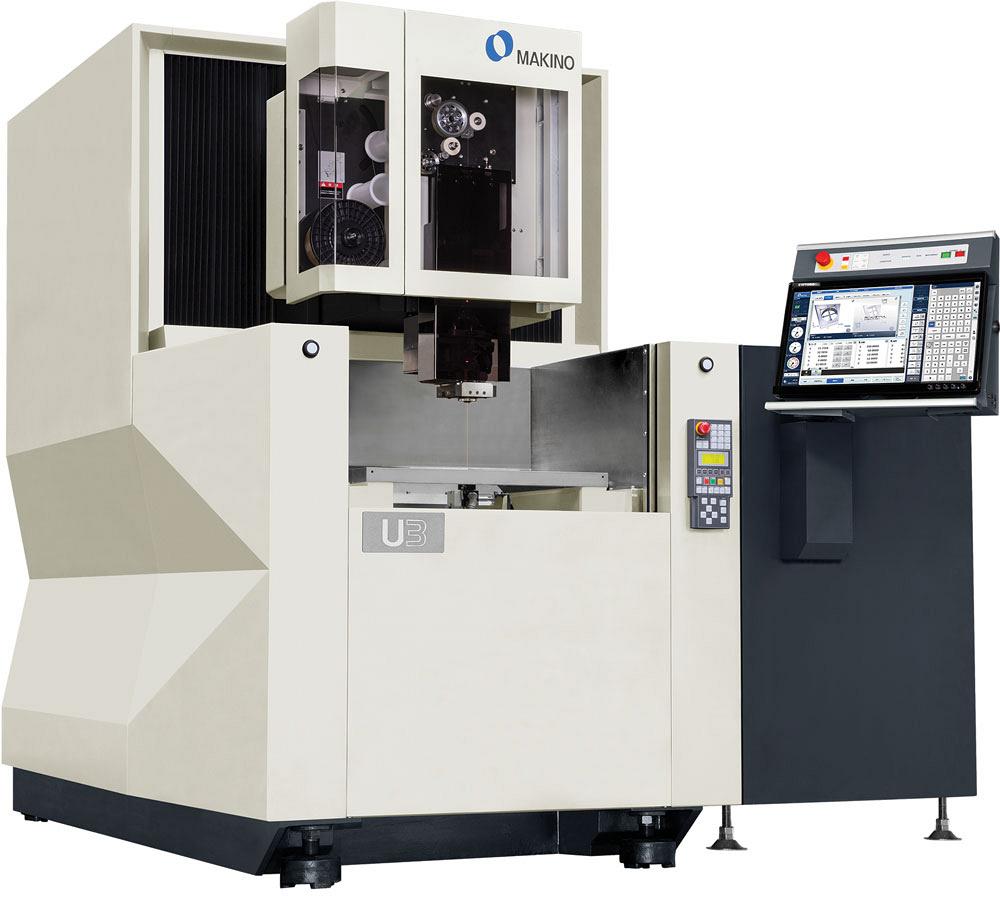
There are two reasons why wire EDM lends itself to lights-out manufacturing: cycle time and built-in features that allow for automation. Photo courtesy of Okuma.
Another new feature on the horizon is a voice control option. Coward explained that Makino is working toward adding its Athena voice control option to its wire EDM machines. It is currently in beta testing, but eventually it can be used to allow operators to ask the machine to perform certain functions without requiring them to be right in front of the machine. It may also remove any barriers to the technology, alleviating any issues an operator may have with using the controls or functionality for the first time. The voice control feature just performs the actions for the operator.
"It’s definitely something new we are doing, and it really assists the operator," said Coward. "If it’s quicker for an operator to use voice control, they are going to get that machine up and running faster and more efficiently."
Associate Editor Lindsay Luminoso can be reached at lluminoso@canadianmetalworking.com.
Makino, www.makino.com
Sodick, www.sodick.com
About the Author
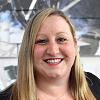
Lindsay Luminoso
1154 Warden Avenue
Toronto, M1R 0A1 Canada
Lindsay Luminoso, associate editor, contributes to both Canadian Metalworking and Canadian Fabricating & Welding. She worked as an associate editor/web editor, at Canadian Metalworking from 2014-2016 and was most recently an associate editor at Design Engineering.
Luminoso has a bachelor of arts from Carleton University, a bachelor of education from Ottawa University, and a graduate certificate in book, magazine, and digital publishing from Centennial College.
subscribe now
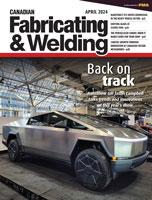
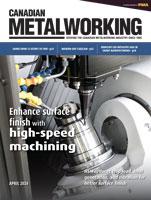
Keep up to date with the latest news, events, and technology for all things metal from our pair of monthly magazines written specifically for Canadian manufacturers!
Start Your Free Subscription- Trending Articles
Automating additive manufacturing
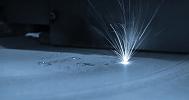
Sustainability Analyzer Tool helps users measure and reduce carbon footprint
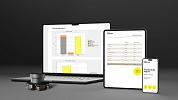
CTMA launches another round of Career-Ready program
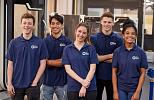
Sandvik Coromant hosts workforce development event empowering young women in manufacturing
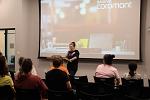
GF Machining Solutions names managing director and head of market region North and Central Americas
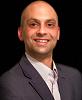
- Industry Events
MME Winnipeg
- April 30, 2024
- Winnipeg, ON Canada
CTMA Economic Uncertainty: Helping You Navigate Windsor Seminar
- April 30, 2024
- Windsor, ON Canada
CTMA Economic Uncertainty: Helping You Navigate Kitchener Seminar
- May 2, 2024
- Kitchener, ON Canada
Automate 2024
- May 6 - 9, 2024
- Chicago, IL
ANCA Open House
- May 7 - 8, 2024
- Wixom, MI