Associate Editor
- FMA
- The Fabricator
- FABTECH
- Canadian Metalworking
Keys to successful machine automation
There is more than meets the eye when integrating automation on the shop floor
- By Lindsay Luminoso
- January 6, 2021
- Article
- Metalworking
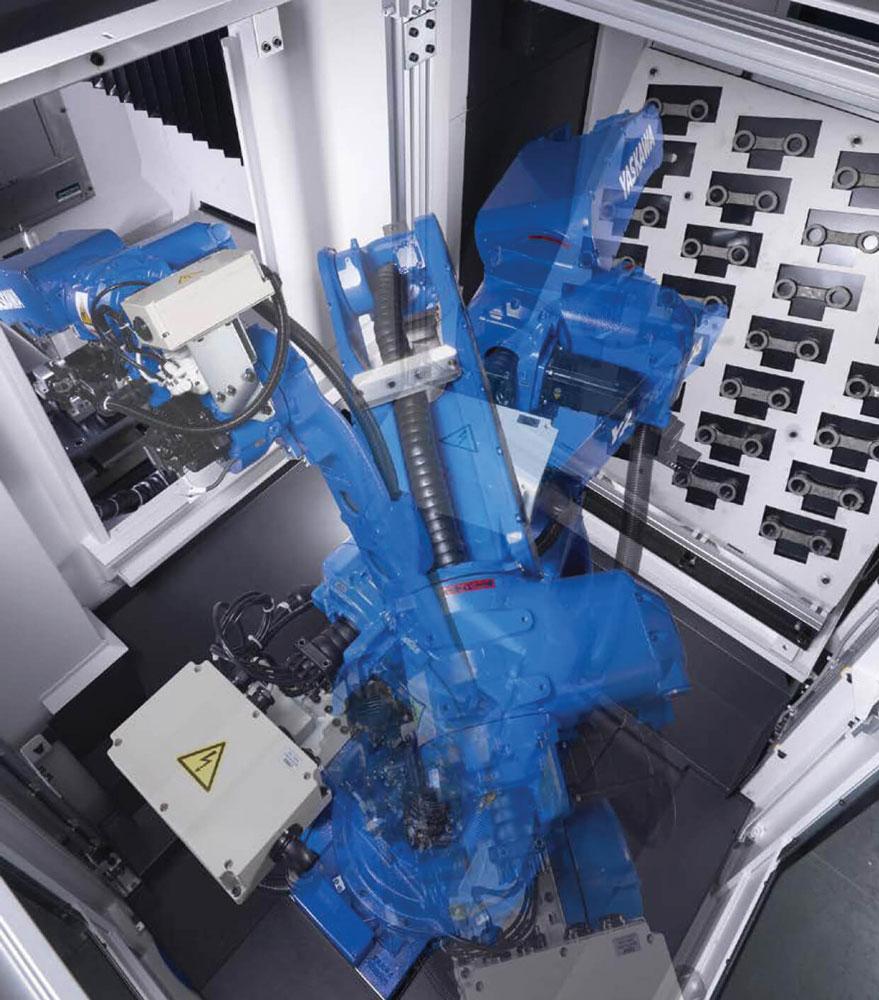
Automation is a means to increase efficiency, so having the ability to compare pre- and post-automation processing will help expose any areas of concern. Photo courtesy of Okuma.
In today’s competitive landscape, manufacturers are looking for ways to reduce cycle time and increase quality, all while dealing with a skilled labour shortage. When most people think of automation, they envision large, fancy robot arms moving across a shop floor, but simpler automated part handling and loading systems, like pallet pools and automated part changers, can boost productivity, too, while freeing up operators to take on more value-added work.
One of the most important reasons that shops automate is to maximize machine uptime and keep the chips flying for as long as possible. But to do this effectively, they should consider their expectations and goals before they begin to run unattended or in a lights-out environment.
Get a Baseline
A good place to start is with the overall process. Manufacturers need to assess their expectations of new technology and anticipate how it can be used for future growth. Most shops look at automation as a means to solve a problem they are currently experiencing with existing production. There are many questions that a shop should explore before beginning the automation process.
“What are your short-term goals and what are your long-term goals? What are you doing the next three to six months? What are you doing in the next five to 10 years? Where are you trying to take the company?” said Wade Anderson, product specialist sales manager, Okuma America, Charlotte, N.C. “These are important questions to help make sure you’re putting a system in place to help you get to your long-term goals. You have to examine all variables of the machining process and make sure they are all under control. Without control over these elements, automation will not be successful.”
With this information a shop can better set up the machine to work with automation and get a better sense of what can be expected. Getting the process squared away upfront will help make the transition to automation easier. For the most part, process work and fine-tuning happens at the machine at the operator level. In an automated environment, that can’t happen.
“Understanding where a shop was before automation is important,” said Anderson. “Automation is a means to increase efficiency, so having the ability to compare pre- and post-automation processing will help expose any areas of concern. If you're going to automate and be successful at it, you have to have processes in place where you are taking care of all the downstream processes ahead of time.”
Plan
Proper planning can mean the difference between a successful run and an idle machine. Once a baseline is set, a shop can anticipate the amount of raw material and stock that will be needed to fulfill part orders. Going from a single eight-hour shift to lights-out manufacturing means that shops need to account for more material usage. If an operator doesn’t have the right material or enough material to run all parts through the night, the machine will sit idle and the shop will lose valuable machining time.
It may take some fine-tuning and test runs before a shop can really understand what unattended machining looks like, but monitoring stock levels and tracking material usage for the first couple of runs will give a good indication of what it will take to run smoothly going forward.
The real struggle with implementing automated part handling and loading is not with the automation itself, but rather ensuring that all the upfront processes are in place, so the machine can properly execute the production run without any errors.
This is where scheduling comes into play. Most automated part handling and loading systems don’t require extensive programming knowledge; instead, scheduling software can be used to easily plan how lights-out manufacturing will flow.
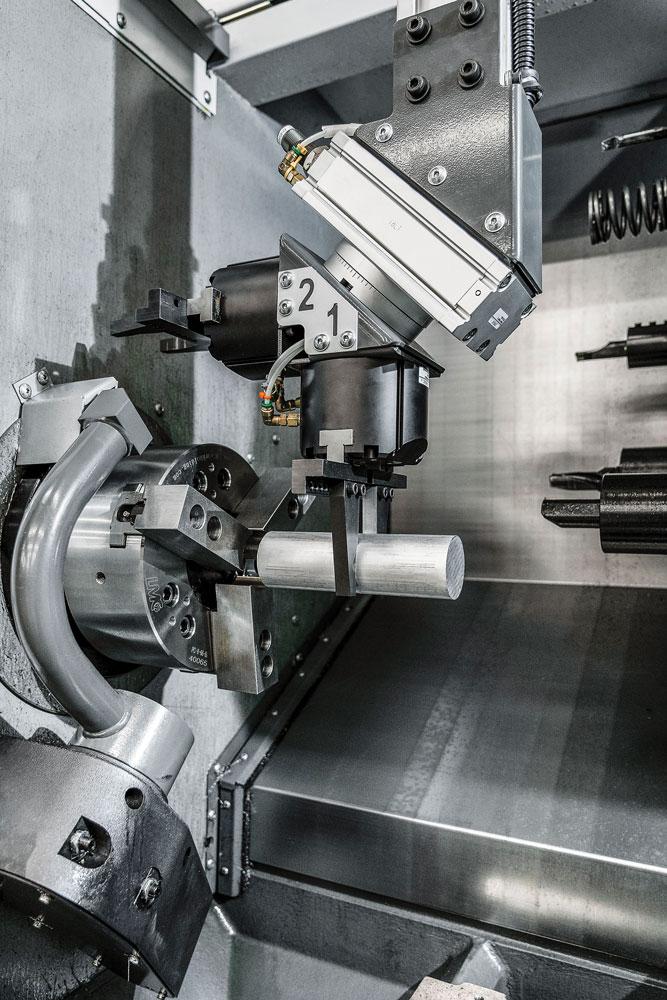
It’s important to have the necessary raw material ready and available to be loaded at the machine, so that when the operator does hit the start button, the machine can run through all the scheduled jobs. Photo courtesy of Haas Automation.
“Good scheduling software within the control itself will allow an operator to schedule pallets in a specific order and have each pallet tied to a specific part program,” said Scott Rathburn, product technical specialist, Haas Automation, Oxnard, Calif. “There’s a lot more to do than just push the cycle start button. It’s not like just having to set up for a single job; you need to make sure that the raw material is available to be loaded up and ready, so that when you do hit the start button, the machine can run through all the scheduled jobs.”
Have the Right Tools on Hand
Beyond material, having the correct tools and fixturing available will ensure that the machine can run smoothly without operator intervention. No shop wants to start loading up pallets and find out that it doesn’t have the correct fixtures or enough fixtures to get all the parts loaded.
“One of the things to keep in mind is that with these types of systems, a shop will probably need to automate workholding in some way with automatic vises or the like,” said Rathburn. “So investing in the necessary tools is essential. And shops will need to explore how to integrate all the different systems in order to get them to work well.”
The last thing any operator wants is to return to the machine only to find out that it has been sitting idle because the parts weren’t fixtured properly or, even worse, that an entire batch of parts needs to be scrapped because the workpiece wasn’t fixtured properly.
“With fixturing and workholding, the ability to detect if it’s seated correctly and confirm that the part is loaded correctly will prevent any parts from being misloaded, allowing the machine to catch the error ahead of time and keep the automation system running,” said Anderson.
Beyond workholding and setting up the pallets correctly, the machine needs to be equipped with the necessary tools. If a shop expects to run unattended or lights- out, it has to expect that there may be tool wear or breakage during the process; in those cases, the tools need to be replaced. Adding redundancy tools to the magazine will ensure that the machine can change out tools as needed.
If a shop is setting up its pallets with multiple part families, and the lights-out scheduling will be producing various components, the machine needs to include all tools. Forgetting to load one tool could stop cutting in its tracks. Keeping a tool list and double- checking that the machine is set up for lights-out operation is a good check list item.
“With long and unattended runs, shops are going to need more tools,” said Rathburn. “They will also need backup tooling and a probe system for detecting tool wear and broken tools.” So, investing in a larger tool changer for the machine might be necessary. Exploring the machine’s redundancy tooling options in the control is also a good practice. Looking at how broken tools are detected is also important. These are all things shops need to keep in mind.
Companies looking to expand the number of projects they run on a single machine using this type of automation might also need to invest in expanded tool capacity. Adding an automatic tool changer (ATC) that can hold additional tools may be something worth exploring or something to consider for future growth opportunities. It will give an operator peace of mind to know that there are enough backups if needed.
Culture Shift
One thing that is often overlooked regarding any automated technology implementation is organizational buy-in. A lot of hidden features help unattended machining and lights-out manufacturing be successful, which means that many people may need to be involved in the process. Management needs to effectively communicate why automation is needed and how it will affect existing work flow structures.

Most automated part handling and loading systems don’t require extensive programming knowledge. Okuma’s ARMROID includes one operation panel to control both the machine and robot, reducing the learning curve for operators. Photo courtesy of Okuma.
“Having buy-in from the organization is sometimes overlooked,” said Anderson. “This goes for any kind of new technology – it’s going to be as successful as the people who have bought into it. So whether it’s automation or whether you’re just talking about a new piece of software, if you haven’t got that culture where you’ve got a team that’s excited and embracing change and tackling new technologies, it can be a struggle at times. And it’s really a cultural shift that’s needed.”
A lot of new technology, especially automation, can bring a fear factor. Workers may worry that this new automation will encroach on their work, or even eliminate their job. People are creatures of habit, so anything new can create friction. This is why management needs to be clear with expectations and communicate changes.
“This is where training and education can come into play,” said Anderson. “Taking the time to learn the new technology and all the various aspects needed for it to run smoothly gives people a vested interest in its success. It will also help root out any problems early on, elevate people’s skillset, and make the entire operation more successful. It will really be incumbent on management to lead. The wrong approach could cause workers to resist, and with so many elements involved, everyone needs to get on board.”
Associate Editor Lindsay Luminoso can be reached at lluminoso@canadianmetalworking.com.
Haas Automation, www.haascnc.com
Okuma, www.okuma.com
About the Author
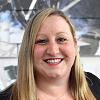
Lindsay Luminoso
1154 Warden Avenue
Toronto, M1R 0A1 Canada
Lindsay Luminoso, associate editor, contributes to both Canadian Metalworking and Canadian Fabricating & Welding. She worked as an associate editor/web editor, at Canadian Metalworking from 2014-2016 and was most recently an associate editor at Design Engineering.
Luminoso has a bachelor of arts from Carleton University, a bachelor of education from Ottawa University, and a graduate certificate in book, magazine, and digital publishing from Centennial College.
subscribe now
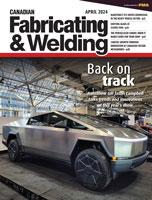
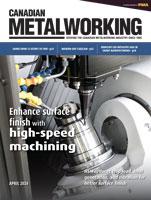
Keep up to date with the latest news, events, and technology for all things metal from our pair of monthly magazines written specifically for Canadian manufacturers!
Start Your Free Subscription- Trending Articles
Automating additive manufacturing
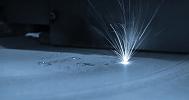
Sustainability Analyzer Tool helps users measure and reduce carbon footprint
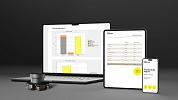
CTMA launches another round of Career-Ready program
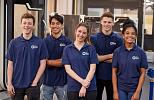
Sandvik Coromant hosts workforce development event empowering young women in manufacturing
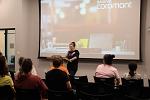
GF Machining Solutions names managing director and head of market region North and Central Americas
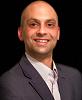
- Industry Events
MME Winnipeg
- April 30, 2024
- Winnipeg, ON Canada
CTMA Economic Uncertainty: Helping You Navigate Windsor Seminar
- April 30, 2024
- Windsor, ON Canada
CTMA Economic Uncertainty: Helping You Navigate Kitchener Seminar
- May 2, 2024
- Kitchener, ON Canada
Automate 2024
- May 6 - 9, 2024
- Chicago, IL
ANCA Open House
- May 7 - 8, 2024
- Wixom, MI