Associate Editor
- FMA
- The Fabricator
- FABTECH
- Canadian Metalworking
Don’t underestimate zero-point workholding
5 benefits of using these systems
- By Lindsay Luminoso
- May 8, 2023
- Article
- Metalworking

Most systems available today come in both a small and large size. Shops can use all the workholding it has invested in over the years and integrate the pull stud into them.5th Axis
With so many workholding options available, it can be hard to know which one makes the most sense for a given application, production size, or the equipment available. In recent years, zero-point workholding systems have become increasingly popular, and the experts agree that there are increasingly fewer reasons not to use them. Here are a few reasons why a shop should invest in zero-point workholding.
1. Adaptability
Not all machine shops have one single brand or machine type, so choosing a workholding system that can be used across the board can help standardize production.
“Zero-point workholding can be used in a variety of machines, whether that’s 3-, 4-, or 5-axis machines,” said Samuel Lane, sales engineer at Union, Ohio-based Te-co, Toolex, and Raptor. “Generally, it makes the most sense when you have short to medium production runs. For companies with a variation of products where a lot of different features are being made, these systems are very adaptable and allow for adjustments on the fly.”
This is because most zero-point workholding systems have been standardized based on industry needs. Fixtures have locating studs—with four being an industry standard—on the bottom, which allow zero-point fixturing plates to be switched out quickly and easily.
“It is a huge benefit to be able to change out a fixture or part when needed,” said Kevin Schumann, sales, standard parts, Halder USA, Waukesha, Wis. “Operators don’t need to waste time standing in front of the machine loading new parts into it. Instead, while the machine is running, they can perform off-line set up of the next part, which can be totally different from the one the machine is running.”
For example, if a machine is running a gearhouse program but the next part is an oil pan, zero-point workholding allows the operator to have everything set up and ready to switch over rather than spending lots of time at the machine, adjusting and testing that everything is in the right position.
“Today, there is a zero-point system available for almost any part, work envelope, and material type,” said Eric Nekich, sales manager, 5th Axis Inc., San Diego. “There may be a part with unique contours that may not be suited for this type of fixturing, but today, many shops are taking dedicated tooling for these unique applications and designing them in a way that they can be used with zero-point systems.”
These systems have been designed to be as adaptable as needed. For example, Nekich noted that adding fully integrated risers can make these systems better suited for 4- or 5-axis applications that require the additional height to clear the spindle when rotating the A- or B-axis. The ability to take a standard system and customize it to make it work on any machine on the floor means that shops can be more flexible with workflow.
2. Repeatability
Being able to move from machine to machine quickly and easily is great, but for this to be effective, the system needs to have high precision and accuracy to be repeatable.
“With zero point, it can simply move from one machine to the next across all the steps necessary to change the workpieces, making the need for repeated and laborious aligning and centring a thing of the past,” said Schumann. “It only takes a few seconds to centre and clamp the workpiece at the zero point. Better still, you only have to set the zero point once and can achieve that repeatability.”
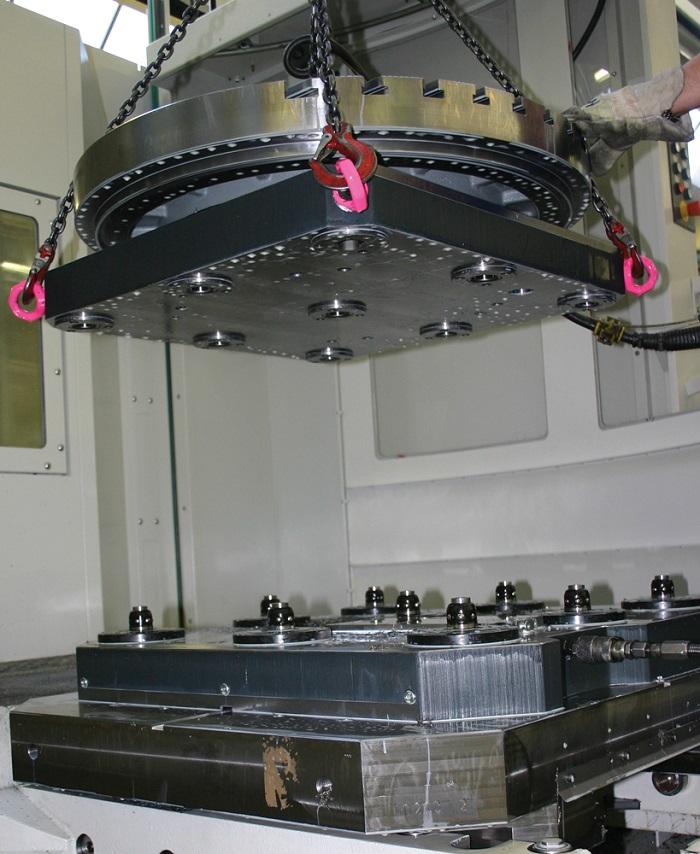
While quick setups are a big feature of these systems, it is really the precision and accuracy that make these a great option. Halder
While quick setups are a big feature of these systems, it is really the precision and accuracy that make these a great option. It can be necessary and time-consuming to have to touch on the device and parts to locate where everything is before starting a job.
“Having that very high repeatability of within 0.01 mm means that the fixture can be taken on and off and moved from machine to machine without having to worry about locating the device each and every time,” said Lane.
3. Scalability
Today’s zero-point systems come in a range of sizes and specifications, but it is important to ensure that it’s suited not only for today’s work but for future production changes as well.
“Zero-point plates generally have four pull studs, but you can also select ones that have eight studs,” said Lane. “The larger the vise, the more studs needed. Some shops may even want to use blank-type plates to add their own mounting to it, making it easier to scale up or down to meet application needs.”
The size of the fixture must also correspond to the size of the part. For example, machining big molds may require larger workholding, which means that more pull studs may be needed to ensure the rigidity and stability of the system.
“Being able to increase or decrease run quantity and scale up and down is easy with zero-point because you are always repeating off that same offset,” said Nekich. “The pull studs are industry standard, and even ones that support much larger work still use that same pull stud. The machine doesn’t care what the pull studs are attached to, so a shop can work with self-centring vice technology or even directly attach the workpiece. Scaling up and down is easy when everything is standardized.”
Most systems available today come in both a small and large size. The experts agree that it is much easier to adapt from a large size down to a small size, but it is much more difficult to go from small to large.
“Purchase for capacity not for a specific job or application,” said Nekich. “Even if an initial project is a small part, having that added size and capacity means that it can grow with your needs. An operator can easily pull a small fixture off the plate and put a big fixture down, and nothing else is needed because that initial investment had capacity in mind.”
4. Accessibility
Another advantage of this system is that it is an accessible technology. Not only is it easy to use, operators can be more creative with how it is applied. For example, having standardized pull studs means that different type of fixtures, clamping, and other mechanisms can be used to creatively hold parts.
“Don’t be afraid to redeploy those four pull studs,” said Nekich. “You can be creative because they basically cost $130. Take all the workholding that has been invested in over the years, whether that’s dedicated fixturing, stationary jaw-type vices, or the like, and integrate the pull stud into them. Now your existing workholding is compatible with the zero-point system, or even better, now you don’t have to indicate ever again as it will repeat precisely.”
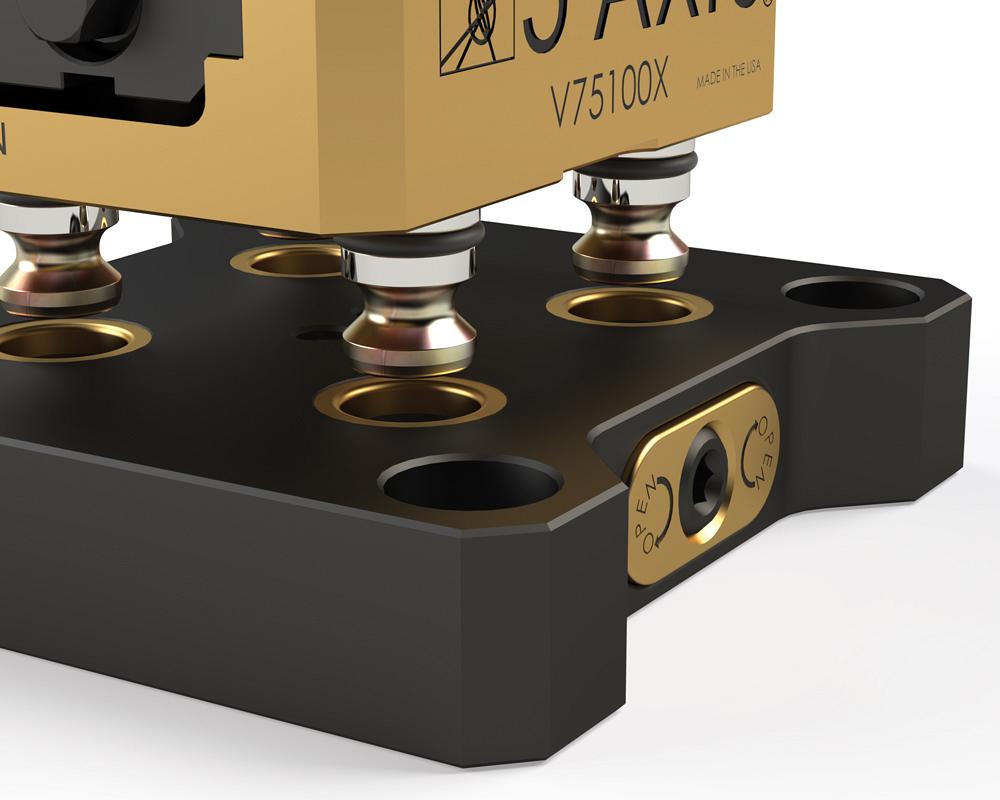
Pull studs are industry standard, and the machine doesn’t care what the pull studs are attached to. Therefore, a shop can work with self-centring vice technology or attach the workpiece directly. 5th Axis
Nekich also noted that another advantage of having a standardized system like zero-point means that it is more accessible to new users. It’s easier to teach and easier to use. It has mechanical controls that can be put in place to prevent new operators from loading things incorrectly or in the wrong orientation.
5. Versatility
A lot of shops look to invest in zero point because the ultimate goal is to standardize across the entire shop. Not only does this type of system work on multiaxis machines, but it also can be used on horizontally or vertically configured machines, grinding machines, measuring applications, and even automation.
“There is the endless possibility to use zero-point systems outside of the machining centre,” said Schumann. “For example, it can be used for a robotic system as a quick connector for different tools. There are tons of possibilities for diversifying how these systems are used. Robotics and material handling are just a few areas where we are seeing zero-point systems applied.”
For those looking to integrate automation, there are two choices: integrated workpiece exchange or integrated fixture exchange. Most people automatically think the former, but zero-point systems make the latter possible.
“Integrated fixture exchange, like a pallet pool, enables next-level automation to be added to the shop floor,” said Nekich. “The top tooling is loaded and unloaded into an automatic zero-point base. That provides huge flexibility when you get into higher-volume runs. But for job shops who are considering automating some of the processes, this can also be a great way to ease into it without making huge investments.”
Associate Editor Lindsay Luminoso can be reached at lluminoso@canadianmetalworking.com.
5th Axis, 5thaxis.com
Halder USA, www.halderusa.com
Raptor Workholding, www.raptorworkholding
About the Author
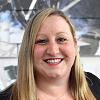
Lindsay Luminoso
1154 Warden Avenue
Toronto, M1R 0A1 Canada
Lindsay Luminoso, associate editor, contributes to both Canadian Metalworking and Canadian Fabricating & Welding. She worked as an associate editor/web editor, at Canadian Metalworking from 2014-2016 and was most recently an associate editor at Design Engineering.
Luminoso has a bachelor of arts from Carleton University, a bachelor of education from Ottawa University, and a graduate certificate in book, magazine, and digital publishing from Centennial College.
subscribe now
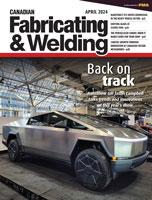
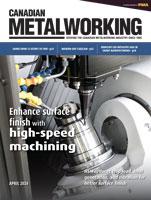
Keep up to date with the latest news, events, and technology for all things metal from our pair of monthly magazines written specifically for Canadian manufacturers!
Start Your Free Subscription- Trending Articles
Automating additive manufacturing
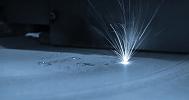
Sustainability Analyzer Tool helps users measure and reduce carbon footprint
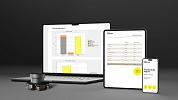
Sandvik Coromant hosts workforce development event empowering young women in manufacturing
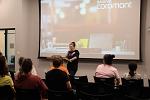
GF Machining Solutions names managing director and head of market region North and Central Americas
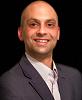
Mitutoyo updates its end-user portal
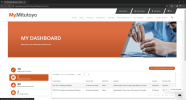
- Industry Events
CTMA Economic Uncertainty: Helping You Navigate Kitchener Seminar
- May 2, 2024
- Kitchener, ON Canada
Automate 2024
- May 6 - 9, 2024
- Chicago, IL
ANCA Open House
- May 7 - 8, 2024
- Wixom, MI
17th annual Joint Open House
- May 8 - 9, 2024
- Oakville and Mississauga, ON Canada
MME Saskatoon
- May 28, 2024
- Saskatoon, SK Canada