Associate Editor
- FMA
- The Fabricator
- FABTECH
- Canadian Metalworking
Creating machining efficiencies
Streamlining its machine shop has enabled Pazmac to take on technologically demanding projects
- By Lindsay Luminoso
- January 29, 2020
- Article
- Metalworking
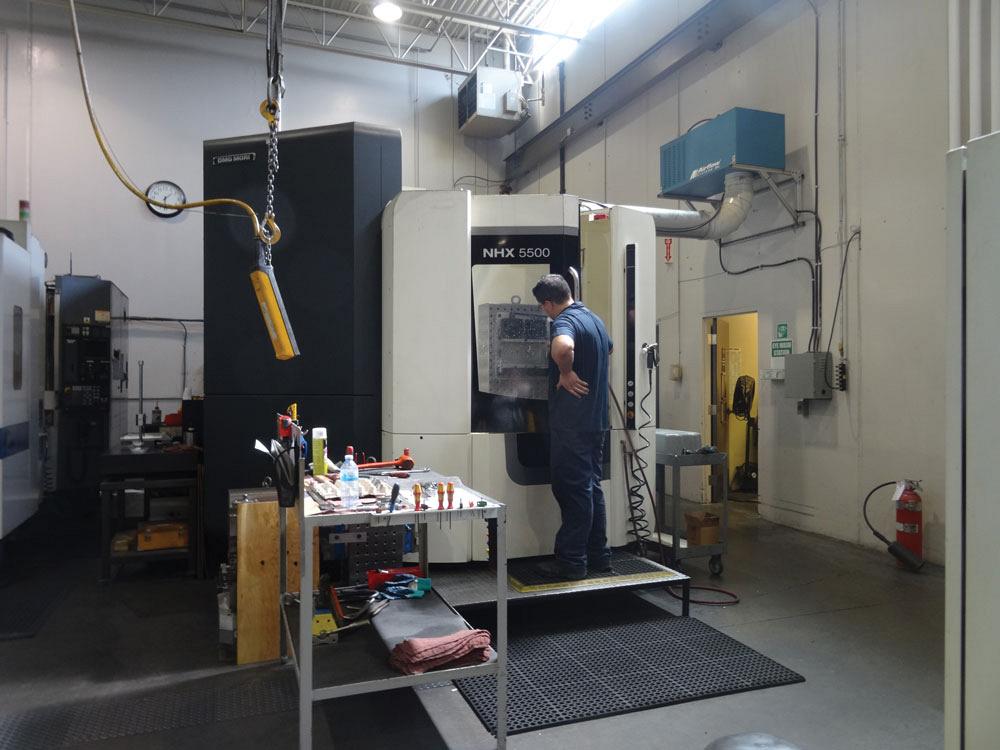
Pazmac recently invested in a second DMG Mori NHX 5500 horizontal milling machine to bookend the one that is currently on the shop floor.
Pazmac considers itself to be a manufacturing specialist for the Global OEM markets requiring turnkey machined components. Located in Langley, B.C., this machine shop has expanded its offerings, transforming itself into a full production shop, all while pushing the boundaries of its CNC machining capabilities.
"We aren’t just a machine shop," said Stacey Saumure, vice-president, operations and procurement, Pazmac. "We work in a range of industries and with a number of different materials including alloy steel, exotics, and difficult-to-machine materials. Yet, we take on work that includes the full scope of a project and provide turnkey solutions to our client base."
The shop can do this because of a significant investment in equipment. With a 30,000-sq.-ft. facility and no yard for materials, the shop has needed to be strategic with its investment and opt for machines that maximize efficiencies. Saumure gave the example of how investing in two Amada CNC saws eliminated the three non-CNC saws on the shop floor while providing faster processing of materials.
"We also offer robotic laser cladding, some heat treating, and gas nitriding," said Saumure. "Beyond that, we do a number of different surface finishing services including shot peen, glass bead, and grit blasting, as well as EDM machining with the ability to manufacture our own electrodes."
With the material handling and finishing services configured in one area of the shop, the remainder of the shop’s footprint is dedicated to Pazmac’s extensive lineup of DMG Mori milling, turning and mill-turn machines, along with EDM, NDT, laser hardfacing, heat treating, laser engraving, and quality control department.
FROM MILLING TO TURNING
Previously, the machining department was segmented between the company’s 16 milling, turning, and mill-turn machines. However, with recent investment, particularly in the shop’s milling capabilities, the entire department has become more integrated and streamlined.
"We just recently bought another DMG Mori NHX 5500 horizontal milling machine to bookend the one that we currently have on the shop floor," said Tim Walls, president/general manager, Pazmac. "And we are actually considering adding a third one along with a 5-axis machine. We are looking for a machine that can be an intermediate between the direct 4-axis that we get out of our horizontals with something that is more mill-oriented but with 5-axis capability. It just makes sense with our milling side becoming so busy. We want to have an alternative to our mill-turns, which are also incredibly busy."
The mill-turn segment of the shop has expanded over the last 15 years and includes six machines. There are three different configurations offering up to 9-axis capability.
"We still have two of the older Mori Seiki MT 2500 mill-turn machines," said Saumure. "They don’t build this machine anymore and we were looking to bring the hours down on them, but we haven’t been able to do it because they are so versatile. The whole idea behind the mill-turn machines is that they offer done-in-one. We can put a product on the machine and it comes out complete, or we do as many operations as we possibly can. However, not all projects are a good candidate for this type of equipment, which is why we have an extensive lineup of both milling and turning machines."
Saumure noted that investing in advanced technology, particularly with its machining equipment, has been a huge advantage for Pazmac. The shop has worked closely with DMG Mori to leverage and push the boundaries of the current technology, especially when it comes to hard milling and turning.
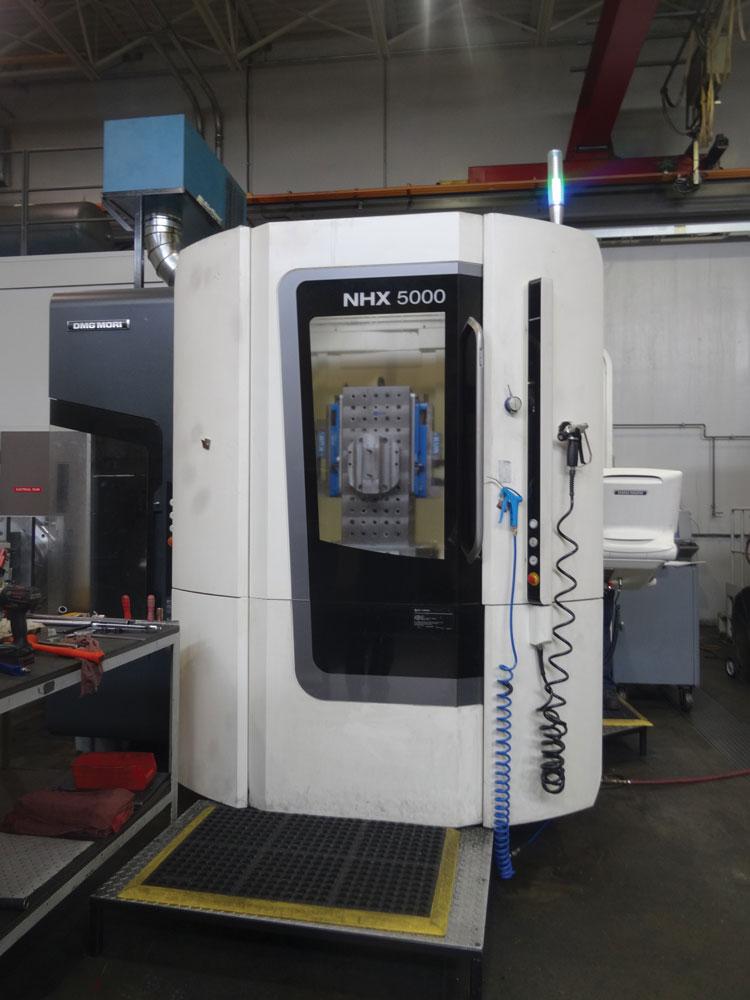
Pazmac’s milling department has become so busy that they are looking to invest in a machine that can be an intermediate between the direct 4-axis that we get out of our horizontals with something that is more mill-oriented but with 5-axis capability.
"We are doing some interesting work with our machines and that challenges the machine manufacturer with some of their own technologies," said Saumure. "In some cases, we are performing operations that may not have been done in a production environment before, so we’ve really been working alongside the manufacturer to take advantage of this advanced technology. It’s something we are really excited about."
AN INTEGRATED APPROACH
Walls added that the departments have really become more integrated with a high level of sharing across programming capabilities, modelling, and tool selection. If it has been optimized in one department, it will also be migrated across the shop floor for uniformity. Benchmarking and leveraging the learning curve of new processing options is critical to Pazmac’s success.
"I think a lot of what is happening in our industry these days is you see current or potential clients that have needs that are technically challenging and very advanced," said Walls. "There’s not nearly as much of the sort of baseline, commercial-type machining happening in North America anymore. So I think there needs to be a willingness to move forward and not get myopic about the technology that you have. You need to have a willingness to change work centres out when needed in order to be viable and competitive with market demands. It’s more about finding manufacturing solutions, not just machining solutions, and adapting to manage the ROI within a forecastable time frame."
To truly integrate all of its departments to more efficiently manufacture parts, Pazmac completed a project to hardwire connectivity to all of its shop equipment and is just introducing real-time machine monitoring. It is also moving towards enhancing tool presetting capabilities. The shop is close to its goal of having all processes fully integrated and ultimately offer a seamless system for job recall and setup management.
"All processing tools and metrology equipment are owned by Pazmac," said Saumure. "The reason for this is that we can control the quality and calibration of every single tool that is required. It also ties these items to the setup sheets and the programs in our ERP system. We put these systems in place to get efficiency up and reduce changeover times."
QUALITY CONTROL
Pazmac has taken on some extremely challenging projects and worked with difficult-to-machine materials. Because of this, the shop has invested in a quality assurance lab including four Zeiss CMMs, portable measuring arms, and thousands of calibrated and controlled measuring instruments and gauges.
Beyond the traditional metrology services, the shop contracts qualified independent third parties to come into the facility daily to perform non-destructive testing services. Some customers require specific certification for NDT, and in-house testing ensures Pazmac has more control over the process and flexibility to get jobs done on time, while maintaining third-party certification.
"We work with a few NDT companies and these partnerships have worked out especially well," said Saumure. "We also do a lot of ultrasonic testing as it relates to our specialty coatings. We have a certified contractor come in weekly for that. All certification is done on-site and electronically matched to our work orders."
For Pazmac, verification is key. The Quality Assurance department has a full gauge certification program, which is especially helpful with the number of threads the company produces. To ensure correct verification, the company has an electronic calibration recall system that ensures all metrology equipment, no matter the size or usage, is accounted for and calibrated when necessary.
"Every single part we manufacture has a CMM program for it and it comes in to the CMM at various stages of the manufacturing process," said Saumure. "This doesn’t mean that we are perfect, but we do track the metric and we have excellent report cards from our customers for producing accurate parts."
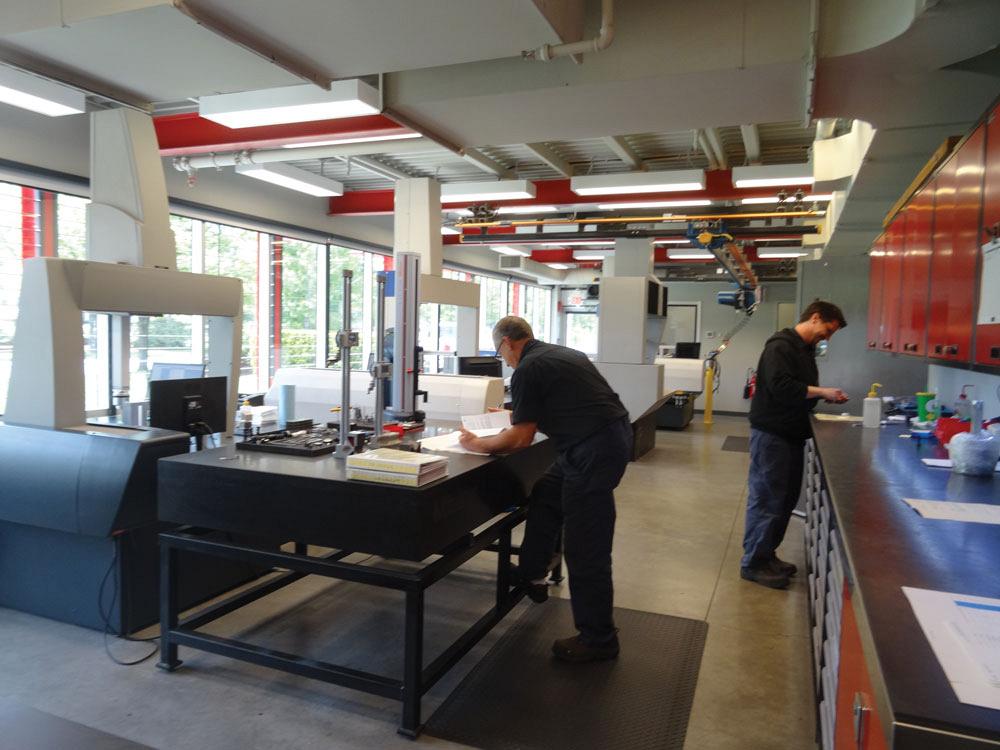
Beyond its extensive lineup of DMG Mori milling, turning, and mill-turn machines, the shop has also invested heavily in its Quality Assurance department.
MOVING FORWARD
Pazmac is focused on continued optimization of resources. As the company looks to push the boundaries of its processing platforms, it is also looking at integrating new technologies, particularly metal additive manufacturing equipment.
"We are diligently looking at additive manufacturing systems," said Walls. "We are looking to see where that fits in our future. We believe that it’s going to have an impact relative to our space requirements as well. We are also looking at work centres and platforms that are purpose-built for specific customer requirements. We are finding that we have some amazing options available to us that perhaps weren’t present two or three years ago."
Walls explained that the shop has been cutting internal splines with its new power skiving capabilities.
"This has been really exciting for us," he added. "We are really trying to make intelligent choices about the new technology that’s coming out."
Associate Editor Lindsay Luminoso can be reached at lluminoso@canadianmetalworking.com.
Pazmac, www.pazmac.com
About the Author
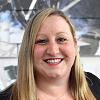
Lindsay Luminoso
1154 Warden Avenue
Toronto, M1R 0A1 Canada
Lindsay Luminoso, associate editor, contributes to both Canadian Metalworking and Canadian Fabricating & Welding. She worked as an associate editor/web editor, at Canadian Metalworking from 2014-2016 and was most recently an associate editor at Design Engineering.
Luminoso has a bachelor of arts from Carleton University, a bachelor of education from Ottawa University, and a graduate certificate in book, magazine, and digital publishing from Centennial College.
subscribe now
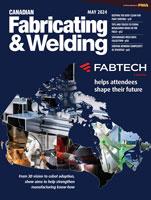
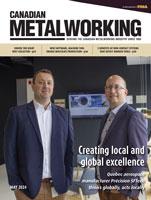
Keep up to date with the latest news, events, and technology for all things metal from our pair of monthly magazines written specifically for Canadian manufacturers!
Start Your Free Subscription- Industry Events
Automate 2024
- May 6 - 9, 2024
- Chicago, IL
ANCA Open House
- May 7 - 8, 2024
- Wixom, MI
17th annual Joint Open House
- May 8 - 9, 2024
- Oakville and Mississauga, ON Canada
MME Saskatoon
- May 28, 2024
- Saskatoon, SK Canada
CME's Health & Safety Symposium for Manufacturers
- May 29, 2024
- Mississauga, ON Canada