Associate Editor
- FMA
- The Fabricator
- FABTECH
- Canadian Metalworking
Breaking down the digital twin
A digital twin begins as a virtual model but enhancements make it a powerful tool
- By Lindsay Luminoso
- May 10, 2021
- Article
- Metalworking
The term digital twin is commonly thrown around, but there are some misunderstandings about what exactly a digital twin is and what it can do. A digital twin is most commonly defined as a virtual representation of the physical world. For a machine shop, a digital model of a single machine tool or the entire shop floor can be used to detect, prevent, predict, and optimize a process through real-time data and simulation without putting tool to metal.
"Digital twin is something that came up in the last couple of years," said Gisbert Ledvon, director business development machine tool, Heidenhain, Schaumburg, Ill. "Terms like Industry 4.0 and IIoT have been thrown around very generously, and many people believe that what they have is a digital twin, but in order for it to be a true digital twin, it needs to be a true duplication of the machine tool in a virtual space."
One of the big misconceptions is that a digital twin is a function of CAD/CAM software and simulation. And while CAD/CAM simulation can show the mechanics of the machine, a 3D model, and the subsequent motion that the machine will perform, what it cannot do is show exactly how the machine will behave dynamically during the cutting process, especially in terms of speeds and feeds. That’s where the digital twin comes in, articulating and estimating parameters such as chip loads, material removal rates, cutting forces, tool deflection, and cutting time.
"The goal of a digital twin is to collect data, information, and metrics about what’s going on in the real world," said Gene Granata, product manager, CGTech, Irvine, Calif. "The digital twin allows users to see in advance what’s going to happen, or go back and reference the data when something unexpected occurs. It also helps mimic exactly what’s going on with that component and process to help achieve better results."
The push toward digitization has occurred over the last several years and has taken root in a number of industries, becoming an important element of the digitization process. The twin can be a machine, production process, performance, or the like, but at its core, it is the visual representation of a physical entity.
"If you look at the market today, we see the big changes and a big shift in technologies," said Gligor Ukropina, product manager—machine tools, Siemens Canada, Oakville, Ont. "There also is a move toward customization, individualization, and complexity in components. There is also a cost pressure and need for manufacturers to be highly flexible. To meet these growing demands, the machine tool industry can leverage the power of a digital twin."
A digital twin begins as a virtual model but becomes a powerful tool when it starts receiving data from its real-world counterpart. Unlike simulation, which offers passive modelling, a digital twin can dynamically change based on the data amassed over its lifetime, growing and maturing through its real-world product life cycle.
Levels of Digital Twins
Once a shop has decided to invest in digital twin technology, it must determine what the end goal of the digital twin will be.
"You need to have the end goal in mind," said Ledvon. "Why do you want a digital twin? What do you want it to do? If you just want to do a verification, then go with the less expensive solution. If you really want to go deep into optimizing and getting every second out of the part to maximize your profits, then you should look into a comprehensive digital twin designed by the control manufacturer in conjunction with the machine tool builder. It’s more expensive but it’s going to give a quick return on investment. But it’s also going to take longer to develop, so there are lots of things to consider."
The experts agree that various levels of digital twinning are available, and it all depends on what a shop is looking for. A basic digital twin can be used for collision avoidance and ensuring that the part fits in the machine. In this level, the 3D model reflects the machine and its movements, similar to standard CAD/CAM verification software.

A digital twin begins as a virtual model but becomes a powerful tool when it starts receiving data from its real-world counterpart. Siemens
"When it comes down to estimating accurate speeds and feeds, the digital twin really needs to dig deeper into the motion control system of the machine," said Ledvon. "It needs to mimic the exact behaviour of the machine. For a more encompassing digital twin that looks at the entire manufacturing process, it needs to include setup features, tooling, material type, component features, and just anything that goes into the production process."
Granata outlined three layers of digital twinning. The first level is basic machine kinematics. A level one digital twin shows how the machine moves, its axes, and how far and fast it can move.
"These are the core foundation of the machine," he said. "The first thing that we generally do, especially if it’s a newer machine, is ask the vendor to provide models of the machine for simulation purposes. The models need to be accurate and detailed based on the customer’s machine specifications. We always recommend that when a shop purchases a new machine, it insists it comes with simulation models that they can use for the digital twin software. Our virtual machine building experts also request a copy of the parameters from the CNC because these hold important information about how a particular machine is configured to move, how it handles various offsets, etc."
Once a digital twin of the CNC machine, including the control and how the machine behaves, has been developed, there is the opportunity to move into a second level of digital twinning, which focuses on all the components related to the job.
"When a job is scheduled for a shop, a piece of stock material needs to get prepared for the machine," said Granata. "What sizes and shapes are going to be used? How many flutes are going to be used on cutting tools? How is the part fixtured? What’s going to hold the workpiece on the machine, and where will it be located? A list of cutting tools, specific pocket locations, tool lengths, build parameters, and other elements of the machining process is needed for the digital twin to accurately simulate the process. We encourage users to put in everything: accurate models for fixtures, clamps and bolts, design models, and stock models. To avoid unpleasant surprises during machining, it’s important to prep the digital twin to the maximum material conditions that are found in the shop."
This can be a more time-consuming process, but for the full benefits of a digital twin to be reaped, accuracy and developing a full picture are needed.
"It always comes down to how much time a shop has and how much effort it wants to spend. If it doesn’t put in the time and effort, what’s the risk of the potential problem that this might cause?" said Granata. "Shops doing more expensive parts, especially in aircraft titanium or INCONEL, are going to spend the time to digital-twin everything they can to make sure they’ve caught every potential problem that can be caught. On the other hand, some guys in production shops that are making one or two ‘low-risk’ parts may not believe they need that level of digital twinning."
The third level that has gotten a lot of attention lately involves the cutting methods and processes. Once all the hardware is twinned, the creativity in the NC toolpaths and the cutting methods can be input. This level is all about optimization rather than verification.
"This layer gets into all kinds of physiological things that relate to the performance of the tool against a specific workpiece of material," said Granata. "Aluminum behaves differently than titanium, which behaves differently than tool steel. The most robust optimization software and digital twin can show all of that data. At this level, the programmer can see what cutting conditions look like, for example, going into a specific corner, and if it’s too rough on the tool, they can choose a different tool to produce less deflection, or change the cutting approach to use less stepdown. Best of all, these decisions are made and strategies refined before any machining is done on the real machine. In the best-case scenario, a shop using NC program optimization software can press a button and the software goes through all of the NC code and adjusts all feed rates to keep forces in line and keep chip thicknesses optimal."
Many shops believe that once they have a simple digital twin, they are done. But so many levels of quality and sophistication can be built into a digital twin. Shops need to do their homework to see exactly what is needed, how it will be provided, and where to start.
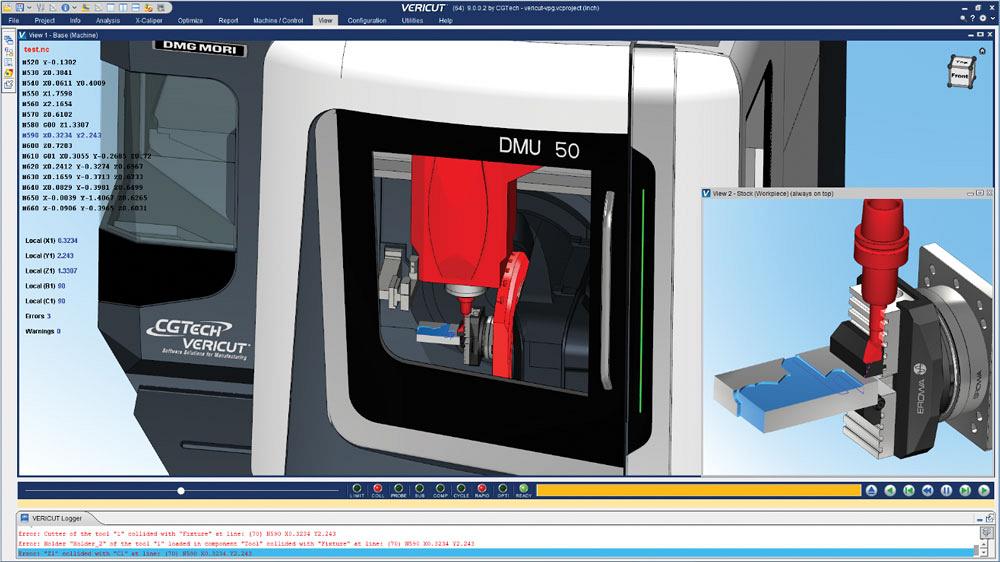
A twin of a part setup includes stock blank size and shape, fixtures and hardware holding stock workpieces, cutting tool assemblies, and where everything goes on the NC machine (tool-to-pockets, part setup on machine table, operator instructions). CGTech
"It will really depend on how a shop can use the technology and information," said Ledvon. "If it can save 30 per cent on setup, reduce operation time, improve cutting speeds, and finish parts much faster than it would have done before, then it’s easy to see why it is a worthwhile investment. It can help make shops more competitive, especially in accurately quoting jobs."
Creating a Digital Twin
Although it may seem like a daunting task, creating a digital twin does not need to be a scary undertaking. Shops have the option to work with companies offering digital twin consulting services. Their experts will work with a shop to collect the necessary data and build the digital twin. Shops also have the option to build it themselves.
"When we build a digital twin for a customer, we first need to know what the control type is and its processing power," said Ledvon. "Then we need to know about the machine and obtain a 3D model of all features and components, including clamping, setup, table, and spindle. When we get all that information, we can build the digital twin customized for a specific machine. It can then be downloaded into a PC or simulator software. From there the shop can import raw materials and other features into the digital twin. It’s as simple as loading it in and playing around with it."
Alternatively, shops can create the digital twin themselves. However, they must have a clear understanding of the machine and its control in order to extract the correct information needed. A number of classes and courses are available to help shops start the process and help them go above and beyond the basic "out-of-the-box" features.
To begin this undertaking, shops will first need to select a software program and subsequent technology to allow for real-time flow of data between the physical asset and the virtual model.
It’s also important to decide early on how exactly a shop wants the digital twin to function. Will it be used strictly for monitoring, or will more reciprocal data-sharing be used for predictive maintenance? Will it be used to perform simulations to improve performance and produce better products? The more advanced the digital twin application, the more comprehensive insights can be achieved.
"The best place to start is to work closely with the machine tool builder," said Ukropina. "Using CAD drawings of the machine can help develop a 3D virtual model. Axis movements, PLC safety and functionalities, external fans or switches, tool magazine, and more are all needed to create a full digital twin, so hardware now becomes software in the loop. The archive files or data of the exact machines has to be integrated into the software so we know exactly how the machine is configured."
It’s important to detail out the machine and twin it as closely as possible to what the real CNC machine does all the way down to the subroutines in the control. Every machine is different with a different group of settings. Literally thousands of settings go into a machine. It’s important to simulate where the machine is going to go in the digital twin, but also confidently know that it will perform the exact same way in real time.
For the most part, machine shops can start small and expand the digital twin’s capabilities as they become more familiar with the technology and how to use the insights and information.
"It’s a digital first approach," said Ukropina. "It’s about performing all the tasks digitally in the office before stepping foot on the shop floor. In order to do this effectively, shops need to find and understand the full potential of digital twinning and how it can be applied to their specific needs."

The third level of digital twinning involves cutting dynamics: chip thickness, cutting force, spindle power demand, and tool deflection resulting from the cutting tool and type of stock material. CGTech
Additive Application
Siemens’ Guy Dulude breaks down how digital twins help make AM easier
“Additive manufacturing (AM) is not an easy thing,” said Guy Dulude, portfolio development manager for simulation, Siemens PLM Software. “You can't just go on an AM machine and hash it out. There is a lot of trial and error involved, and the equipment and material are expensive. It’s a complex process, so having the ability to virtualize the overall process can really help. A digital twin will confirm your overall AM process so that when you go to print the part, it will be done right the first time.”
Manufacturers have moved toward AM to help reduce the number of parts or weight in a component. It’s all about reducing complexity of an assembly. Design for AM is about generative engineering, but actually building a component is far more complex.
“One of the complexities with printing powdered metal is that it moves into a liquid state when it heats,” said Dulude. “This can lead to significant distortion. And if you print it without accounting for this deformation, you can bet that the final product will not be to specification. A digital twin can be used to predict that deformation because it understands all the thermal-mechanical behaviours inside the printing process. If you understand the deformation from the cooling process, you compensate for it during the printing so that when it cools down it straightens up, counteracting the deformation.”
A digital twin allows manufacturers to confirm the performance of the different steps in a design and manufacturing process, ensuring that the product and process will behave properly in real time.
“A comprehensive digital twin is used to streamline the AM work flow from design to completion to utilization,” said Dulude. “It is used for generative design, optimization, and determining if the final printed part is structurally sound and its in-service durability. A digital twin can also help manufacturers understand the build preparation and process, where you need supports for the material deposit, material behaviour, machine and factory floor efficiency all in one environment. You can also monitor the printing process through an IIoT framework and feed the data back into your procedures, triggering a loop of continual improvement.”
There are many ways that a digital twin can help manufacturers to virtually test, validate, and analyze products and manufacturing processes, and it certainly can be used with AM to help make this technology more accessible and cost- effective.
Associate Editor Lindsay Luminoso can be reached at lluminoso@canadianmetalworking.com.
CGTech, www.cgtech.com
Heidenhain, www.heidenhain.us
Siemens, www.siemens.com
About the Author
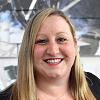
Lindsay Luminoso
1154 Warden Avenue
Toronto, M1R 0A1 Canada
Lindsay Luminoso, associate editor, contributes to both Canadian Metalworking and Canadian Fabricating & Welding. She worked as an associate editor/web editor, at Canadian Metalworking from 2014-2016 and was most recently an associate editor at Design Engineering.
Luminoso has a bachelor of arts from Carleton University, a bachelor of education from Ottawa University, and a graduate certificate in book, magazine, and digital publishing from Centennial College.
Related Companies
subscribe now
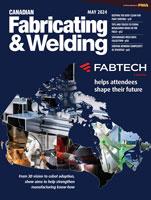
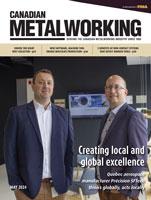
Keep up to date with the latest news, events, and technology for all things metal from our pair of monthly magazines written specifically for Canadian manufacturers!
Start Your Free Subscription- Trending Articles
Sustainability Analyzer Tool helps users measure and reduce carbon footprint
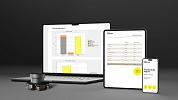
Enhance surface finish with high-speed machining
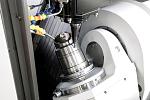
Equispheres secures $20 million investment round
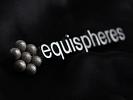
Solid carbide drills produce precision holes in short chipping materials
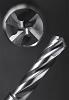
Okuma announces new personnel appointments
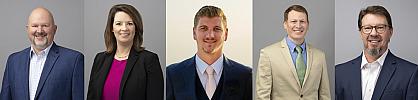
- Industry Events
Automate 2024
- May 6 - 9, 2024
- Chicago, IL
ANCA Open House
- May 7 - 8, 2024
- Wixom, MI
17th annual Joint Open House
- May 8 - 9, 2024
- Oakville and Mississauga, ON Canada
MME Saskatoon
- May 28, 2024
- Saskatoon, SK Canada
CME's Health & Safety Symposium for Manufacturers
- May 29, 2024
- Mississauga, ON Canada