Editor
- FMA
- The Fabricator
- FABTECH
- Canadian Metalworking
Machining frogs
All-Canadian machine/tooling collaboration leads to a smoother train ride in Russia
- By Joe Thompson
- April 15, 2021
- Article
- Management
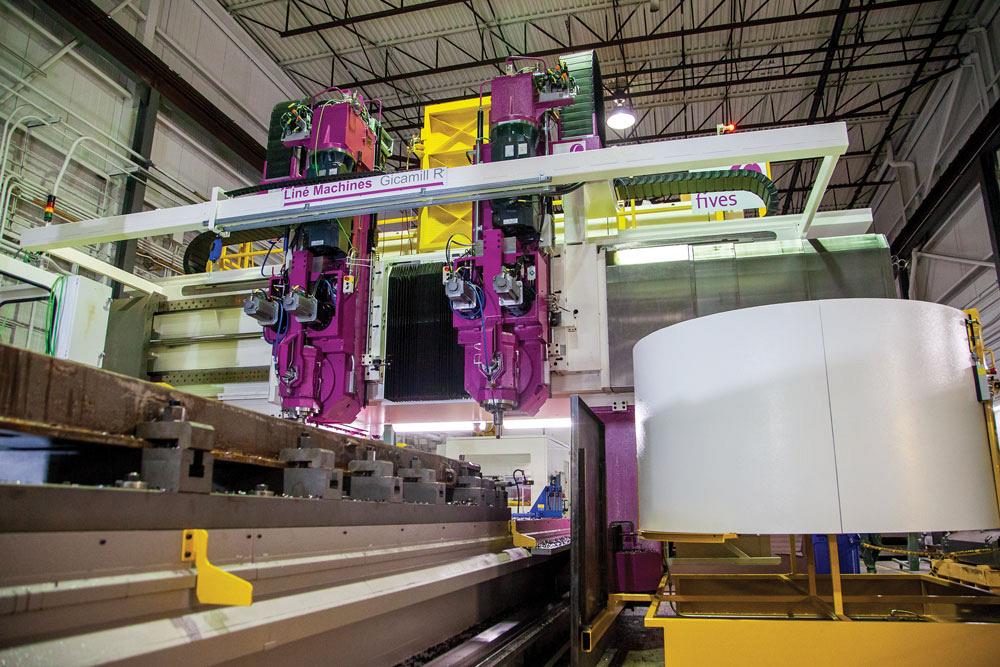
Fives Liné Machines (FLM), Granby, Que., built a Gicamill R vertical gantry mill for the machining of common railway crossings, commonly known as frogs. FLM
The world’s rail system is a vital part of the global supply chain and integral to moving nearly 2 billion travellers to their destinations each year. With nearly 90,000 km of rail track, Russia ranks No. 3 in the world, behind only the U.S. and China.
Keeping the trains rolling is a massive responsibility. Keeping the tracks in order is just as important, however. And a key part of the track system is the frog.
A railway frog, or common crossing, is a component of the rail switch mechanical structure that enables train wheels to cross from one track to another. A new, smooth frog helps ensure that the train transfers smoothly to another line.
When Russia's Murom Switch Works (MSW) needed to produce frogs for the new Moscow-to-Kazan railway line, the first stage of a new high-speed railway in the Russian Federation, it called upon Fives Liné Machines, Granby, Que., and its chosen tooling partner, Iscar Tools, Oakville, Ont., to create the manufacturing process necessary to make these much-needed parts.
Why high-speed rail? It’s simple math: The new Moscow-Kazan link will reduce the travel time between the two cities to about 4 hours from the current 14 hours on the existing railway infrastructure. With trains travelling at roughly 400 km/h, a smooth ride is important.
“MSW selected us because of our engineering services and because of the machine that we recommended to them,” explained Claude Perreault, marketing and communication specialist, Fives Liné Machines.
The machine in question is the company’s Gicamill R vertical gantry mill, which is designed and constructed specifically for the railway industry.
The machine’s power-operated slide movements are achieved by using anti-friction way bearings, including hardened and ground steel slideways (to 60 HRC) with preloaded, high-capacity recirculating roller bearing pads.
No Head Changes
What MSW also liked was the fact that the machine doesn’t perform head changes.
“By definition, a head change reduces rigidity to the system,” said Adrien Roubenne, sales director, Fives Liné Machines. “In addition, head changes increase the cycle time of the machine while increasing maintenance needs.”
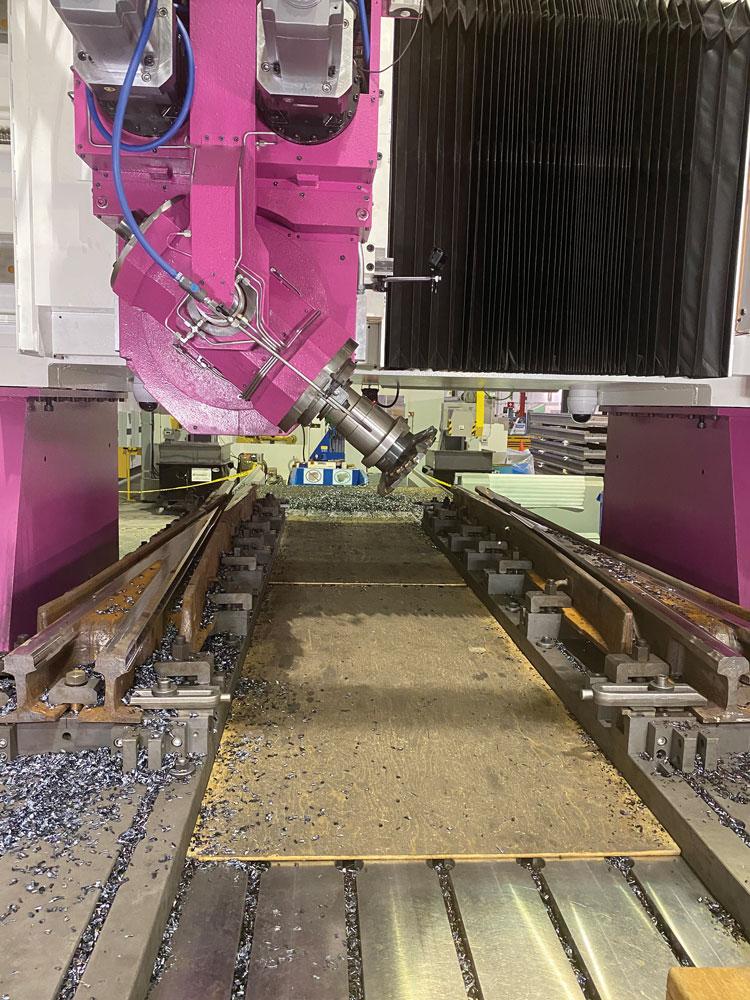
The gantry mill requires no head changes, which can increase cycle time and increase maintenance time and costs. Iscar Tools
The Gicamill R’s head design has a large A axis at the front of the ram, instead of at the bottom, and is specifically designed to absorb tremendous cutting forces. The 4-axis milling head has a travelling capability of ±105 degrees. For MSW, use of the fourth axis also helps reduce the need for specially shaped cutters.
“The head is permanently mounted to the bottom-front face of the main casting, which provides the spindle tilt position with extreme rigidity. The A-axis drive has 20,000 Nm of available torque and a spindle with power up to 60 kW, 4,000 Nm, and 2,000 RPM,” said Roubenne.
The motor drives the spindle from the driveshaft through a bevel geartrain system located inside the spindle housing. The spindle transmission system is controlled by the CNC, which automatically shifts to the range needed according to the programmed speeds. For maximum rigidity, the spindle uses ISO/CAT 60 toolholders.
“The machine also has a compact design that consists of rigid, one-piece bed and worktable sections that support the gantry. The simplified foundation is less costly to build yet assures better load distribution,” said Roubenne. “Sturdy and rigid construction offers the high performance needed for difficult-to-mill materials.”
In this case, the material is a challenging Russian-recipe manganese-based steel alloy.
The 3 Keys
While the first three key criteria for good cutting (understanding the material, geometry, and spindle) determine the cutting tools’ geometries, teeth, and insert arrangements, the generated frequencies also help to define the cutting parameters, such as cutting speeds.
“It’s a very resistant, tough material that gets hardened during machining. It goes from 26-28 HRC to 40-45 HRC,” said Iscar salesman Christian Meunier. “There also is a variation in thicknesses to be removed.”
To select the proper tooling for the machining operations, Iscar’s technical centre started with the part’s 2D drawing. Understanding the datum and radius of the rail was very important because it determined most of the sequences of the cutting operation and how it would be performed.
The company then produced a set of special tools to machine the part’s unique surfaces, including matching the profile of the rail. Several of its standard tools were capable of machining the other surfaces that did not require a special shape.
“In addition to the profile of the rail and the hardness of the manganese-based material, we have dimensions, surface finish, and tool life to respect,” said Meunier.
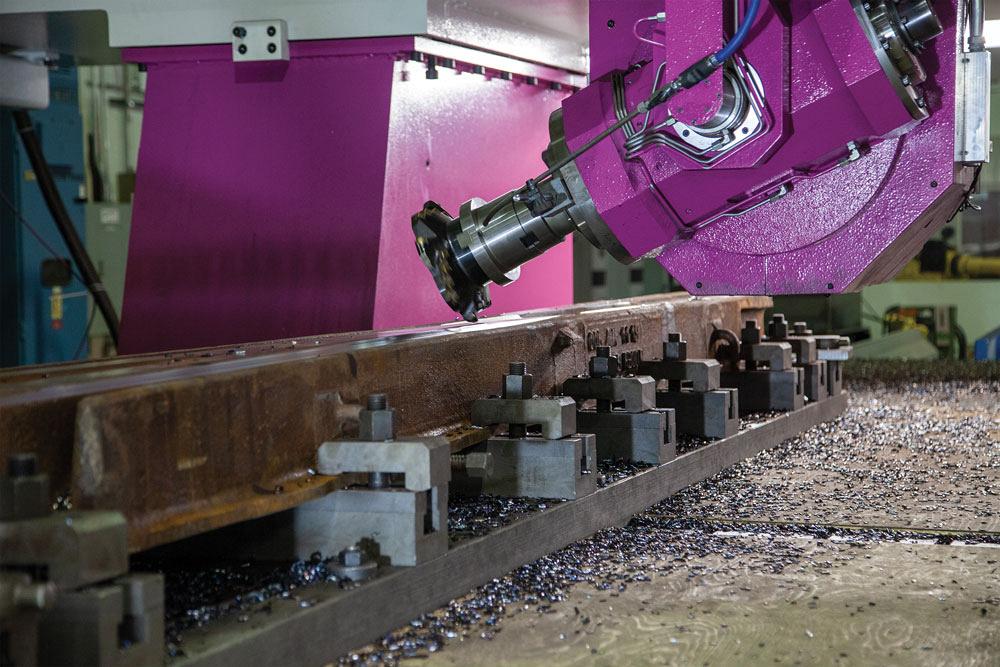
The machine’s 4-axis milling head has a travelling capability of ±105 degrees, which reduces the need for specially shaped cutters. FLM
Choosing a Tooling Partner
Early in the project, Fives launched a bid to select a cutting tool partner. This bid was sent to the few companies able to provide tools for the machine setup and part, and that also were capable of supporting the end user in Russia.
Iscar was chosen in part because it understood the importance of the support that would be required for the project in Russia, but also because of its experience in the rail industry.
The railway industry is a large consumer of cutting tools that requires a variety of both standard and custom-made options.
Machining railway parts represents a challenge for manufacturers and cutting tool producers alike, which must contend with a host of constraints, such as the relatively large workpiece sizes, complex structures, and complicated final profile. This, along with the need to remove a large volume of material, have predictable tool life, and avoid high maintenance costs, makes the process a challenge.
When Iscar’s engineering team selected the correct tools and inserts for each operation, many parameters were taken into consideration, such as material type and the machine tool’s power characteristics, including its clamping fixtures.
“The design of the cutting tools and inserts is very important to avoid chattering. Programming methods (definition of speed, feed, and cut depth) also are important factors that could make the cutters vibrate,” said Roubenne.
Many operations for railway part machining involve rotating tools, especially for milling functions.
In milling, because of the high volume of removed material, extended-flute indexable cutters (both conical and profile) are used. However, a modular shell-mill-design configuration can be used as an alternative to large extended-flute cutters.
According to Daniel Durand, Iscar’s regional sales manager for Quebec, the cutters used on MSW’s frogs have tangentially clamped inserts that improve the tools’ overall strength and help ensure higher tooth density, which improves productivity.
“These particular parts require tools that create good chip evacuation, and in this machine, chips are cleared with an air blast,” said Durand.
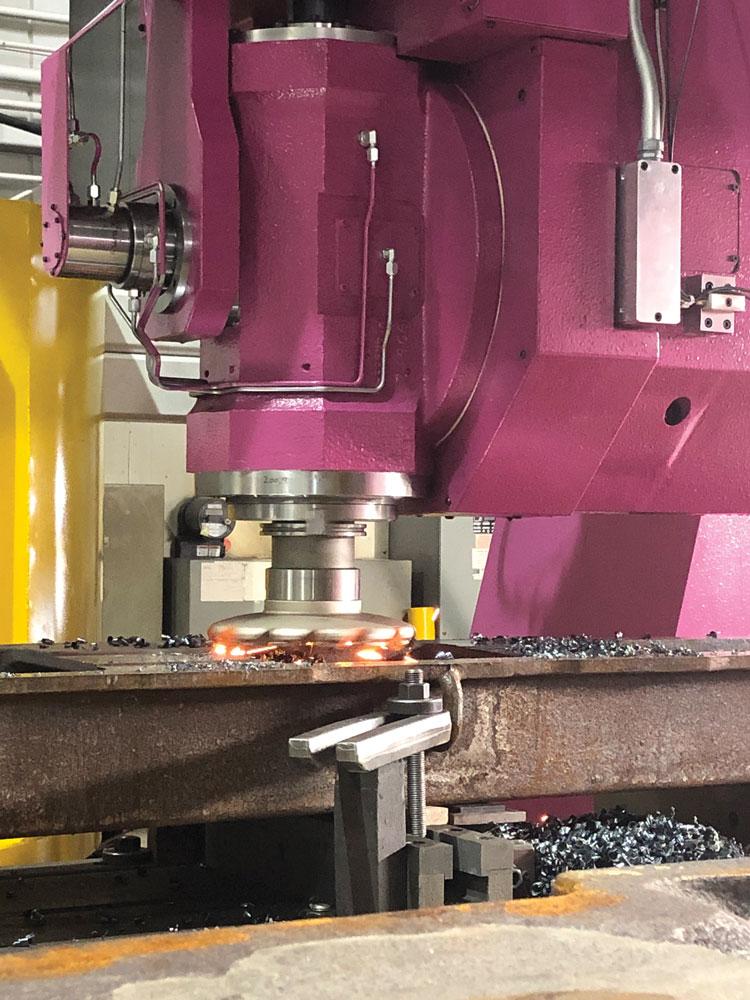
No coolant is used in the process, only an air blast, but Iscar Tools' cutters have tangentially clamped inserts that improve the tools’ overall strength and help ensure higher tooth density, which improves productivity. FLM
Iscar chose the insert size and cutter to have the largest possible mass. This requires a large adapter and cutter diameter as well as large inserts.
“The chosen inserts’ shapes, positive rake angles, insert helix, and chipbreakers help us control chips in these machining operations,” said Meunier.
The fixturing of the part also needs to be rigid enough to eliminate it as a source of vibration during the cutting process. Fives designed and located the fixturing’s clamps to use the full capacity of the machine and its tooling.
“Workholding is very important,” said Roubenne. “Success will depend on the combination of workholding, cutting tools, programming method, and machine. If the workholding creates vibration, surface quality will be affected and the lifetime of the cutters will be reduced, which is not acceptable when we understand the cost of these large tools and number of inserts needed.”
The machine, built at Fives' Granby location, performed test cuts on some of the customer’s actual parts. While Iscar achieved the necessary machining cycle time on the first test, further tool design and testing will be done to increase productivity and tool life at MSW when the machine is ready.
Ideally, the end result of this collaborative work will be a smooth ride for Russian travellers.
Editor Joe Thompson can be reached at jthompson@canadianmetalworking.com.
Fives Liné Machines, www.fivesgroup.com
Iscar Tools, www.iscar.ca
Murom Switch Works, https://aomsz.ru
About the Author
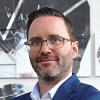
Joe Thompson
416-1154 Warden Avenue
Toronto, M1R 0A1 Canada
905-315-8226
Joe Thompson has been covering the Canadian manufacturing sector for more than two decades. He is responsible for the day-to-day editorial direction of the magazine, providing a uniquely Canadian look at the world of metal manufacturing.
An award-winning writer and graduate of the Sheridan College journalism program, he has published articles worldwide in a variety of industries, including manufacturing, pharmaceutical, medical, infrastructure, and entertainment.
Related Companies
subscribe now
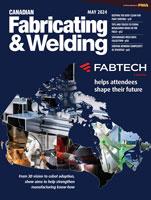
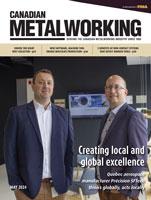
Keep up to date with the latest news, events, and technology for all things metal from our pair of monthly magazines written specifically for Canadian manufacturers!
Start Your Free Subscription- Trending Articles
Sustainability Analyzer Tool helps users measure and reduce carbon footprint
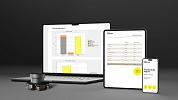
Enhance surface finish with high-speed machining
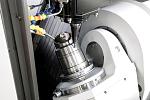
Equispheres secures $20 million investment round
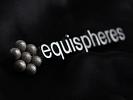
Solid carbide drills produce precision holes in short chipping materials
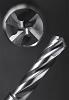
Okuma announces new personnel appointments
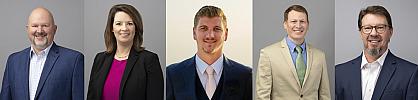
- Industry Events
Automate 2024
- May 6 - 9, 2024
- Chicago, IL
ANCA Open House
- May 7 - 8, 2024
- Wixom, MI
17th annual Joint Open House
- May 8 - 9, 2024
- Oakville and Mississauga, ON Canada
MME Saskatoon
- May 28, 2024
- Saskatoon, SK Canada
CME's Health & Safety Symposium for Manufacturers
- May 29, 2024
- Mississauga, ON Canada