Regional Sales Representative
- FMA
- The Fabricator
- FABTECH
- Canadian Metalworking
Preparing for hard metal milling
Tool selection, coolant strategy are critical for hard milling success
- By Adam Dimitroff
- December 11, 2020
- Article
- Cutting Tools
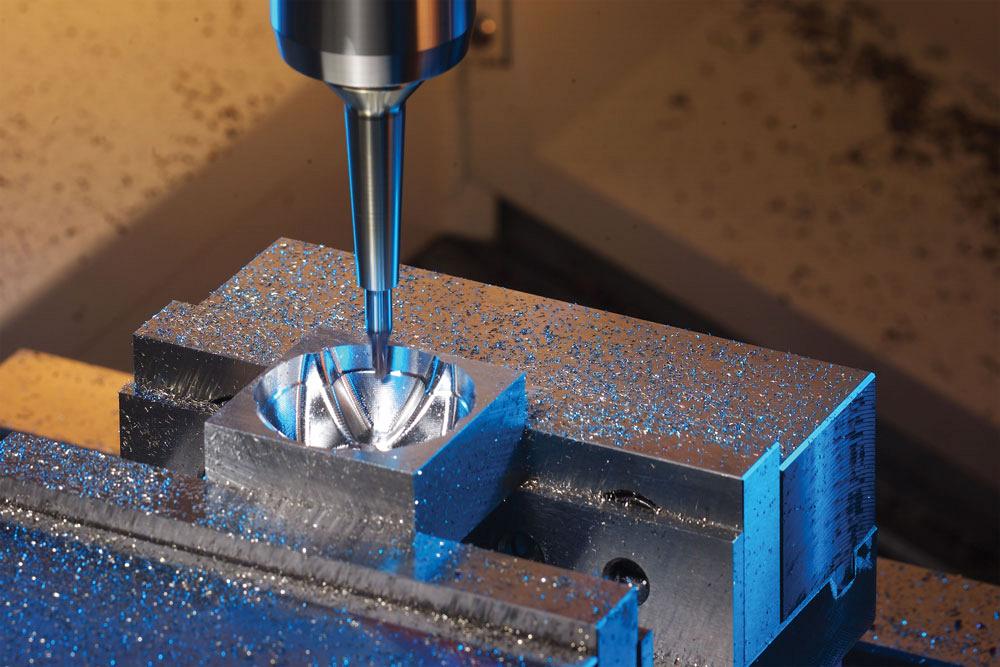
Unlike softer-state steels, milling hard materials favours toolpaths that have lighter depths of cuts, slower surface speeds, and decreased feed rates to combat the high cutting forces and large amount of heat produced.
In today’s shops machinists encounter endless materials with properties that vary greatly. These materials are grouped into categories that are based on how they typically react to a cutting tool during machining.
Ferrous metals that are hardened to 45 HRC or greater usually are classified as hard materials. A common example of their use is in the die and mould industry where die steels, high-speed tool steels, and alloy steels often are found.
In the past components produced from hardened steels were roughed in the soft state, heat-treated, and then finished by an EDM or grinding process. However, advancements in tool geometries and coatings, increasingly accurate toolholders, and continually evolving machines and CAM toolpaths have enabled these materials to be cut in their hardened state with high accuracy and productivity.
The Challenges
Hard materials are challenging to machine for several reasons.
First, hardened steels typically have much higher springback than their annealed counterparts. This results in much higher cutting forces during machining. High cutting forces can increase a tool’s susceptibility to deflection and vibration, which results in poor part accuracy and surface finish.
Because these materials produce high cutting forces, milling tools for hard materials typically have negative rake angles, which makes the cutting edge dull to prevent chipping. This dull cutting edge results in increased friction during the cut, which in turn generates more heat at the cutting edge.
To offset the cutting forces, slower feed rates may be required, resulting in the tool dwelling in one area and subsequently creating even more heat over a longer period of time. This increased heat can cause the cutting tool coating to break down rapidly followed by the tool substrate.
This rapid wear of the tooling is another reason that hard milling is often thought of as challenging.
Larger-scale components in the mould and die industry often require a single tool to finish a large surface area. Because the tool breaks down rapidly when machining hardened materials, it may become too worn to produce a satisfactory surface roughness as it progresses through the part. This often results in the need for a second finishing process, increasing part cycle times and, in turn, manufacturing costs.
Choosing the correct tool, holder, and toolpath is crucial to the success of milling hard materials accurately and efficiently.
Selecting the Right Tool
Hard milling typically is performed using coated carbide end mills, indexable milling cutters, or in some applications less conventional tool substrates. Tools and their geometries must be chosen based on a variety of factors.
Indexable milling cutters often are used for roughing processes when part accuracy and surface finish are not critical. These tools typically are larger in diameter and require powerful, rigid machinery and strong toolholding. Indexable milling cutters for hard milling should have negative cutting angles as well as inserts with an appropriate chipbreaker and coating for hard milling.
Tools should be selected with the largest diameter as the part features allow and with the shortest overhang possible to decrease deflection and vibration.
When compared to milling softer-state steels, hard milling toolpaths favour lighter depths of cuts, slower surface speeds, and decreased feed rates to combat the high cutting forces and large amount of heat produced. Because of this, it is important to choose the correct style of cutter to improve productivity. For milling with large overhangs and in deep pockets, high-feed-style tooling is favoured because of its ability to transfer cutting forces axially upward into the spindle rather than radially.
Finishing processes often are performed using coated carbide end mills. End mills for milling hard materials typically have geometries that are rigid and have high cutting edge toughness. These tools generally have very shallow flutes with largely negative rake angles.
Coatings for hard milling tools have high oxidation resistance, high surface hardness, and a low coefficient of friction. Three-dimensional finishing processes require high-precision tools that are manufactured to tight tolerances to produce an optimal surface finish.
It is important to understand that a lack of consistent precision in the manufacture of the cutting tool often leads to poor dimensional accuracy of a workpiece.
Like indexable cutters, carbide end mills with the largest possible diameter and shortest overhang should be selected. Compared to softer materials, solid-carbide tools should also run at reduced cutting parameters when machining hardened steels.
Milling Paths
Modern machinery and CAM software enable high-speed machining, which involves milling parts at high spindle speeds and feeds with a very shallow depth of cut.
When the depth of cut is shallow, the cutting edge is engaged in the work material for short periods of time, allowing additional time for the cutting edge to cool as it disengages from the workpiece. This method of machining is not only efficient but puts much less stress on machines and holders because cutting forces are reduced.
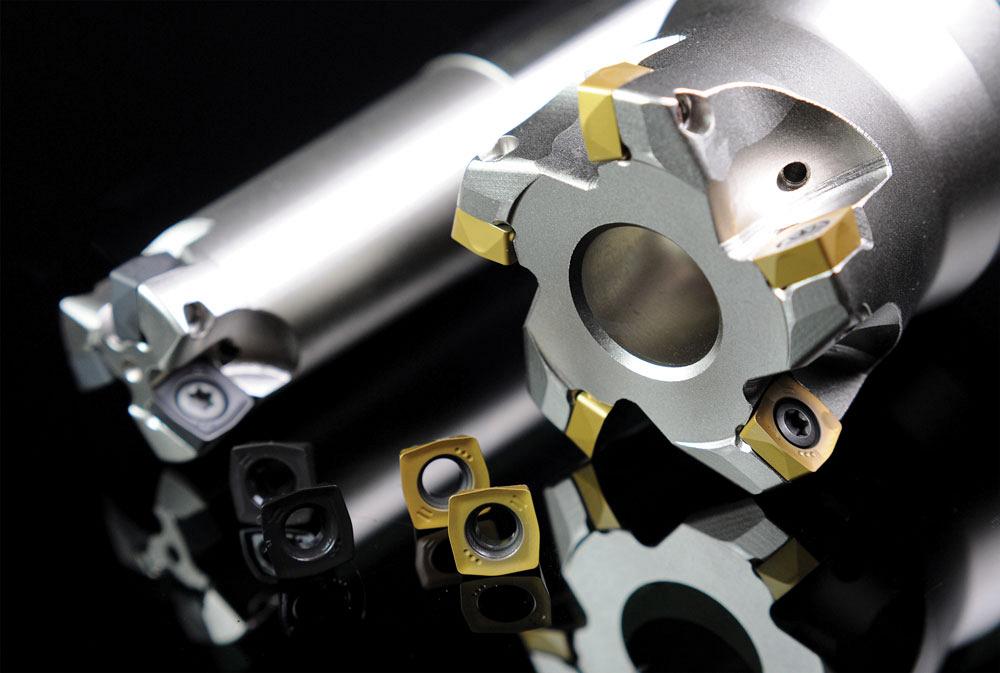
For milling large overhangs or deep pockets, a high-feed mill, such as the Phoenix indexable, four-corner tool, is suggested.
Trochoidal milling at light stepovers is another method of milling hard materials. This style of milling typically involves cutting at light radial depths of cut, combined with the maximum axial cut that the tool or part supports. Once again, the cutting edge enters and exits the workpiece in a short period of time, with plenty of time to cool in air.
Although carbide inserts and solid-carbide tooling are most commonly used in hard milling, certain applications can benefit from alternative tool substrates, such as cubic boron nitride (CBN). CBN has a similar crystal structure to diamond and is one of the hardest substances in the world. It is synthesized under high pressure and temperature similar to the process of producing diamond from graphite; however, CBN tools are not reactive with iron like diamond is.
CBN tools come with a much higher upfront cost but are significantly more wear-resistant than carbide. This not only allows the tools to be run at higher speeds, but when correctly applied, their good wear resistance allows them to machine hardened materials with exceptional surface finishes.
Best Practices
While choosing the correct tool is important when milling hard materials, it is just as critical to ensure the appropriate toolholder and coolant strategy are applied.
The most common toolholder types include collet chuck, hydraulic, and shrink-fit tooling.
Collet chucks are easy to use and have low setup costs and very good vibration-dampening properties. This makes the collet chuck a good candidate for heavy roughing and semi-finishing operations.
Hydraulic toolholders also provide ease of use but come at a higher initial cost. They have higher accuracy and good vibration-dampening qualities, as well as clamping strength. Like collet chucks, hydraulic holders also should be used for roughing and semi-finishing operations.
Heat-shrink holders provide both high clamping strength and high accuracy, but with low vibration-dampening qualities. They are available in many different lengths and size configurations, helping machinists reach deep sections of a part with maximum rigidity. Heat-shrink holders are suitable for finishing operations, because their high accuracy allows them to remove a consistent amount of stock from the part. They also can be used for roughing operations, but their poor vibration-dampening qualities may be detrimental to tool life in the roughing phase.
Coolant selection also influences tool life and, as a result, both part accuracy and surface finish.
In traditional machining, flood coolant is used to help remove heat from the cut while also flushing away chips. However, the amount of heat generated in hard milling is significantly greater than in traditional milling, and for this reason, flood coolant is generally detrimental for indexable, solid-carbide, and CBN tools.
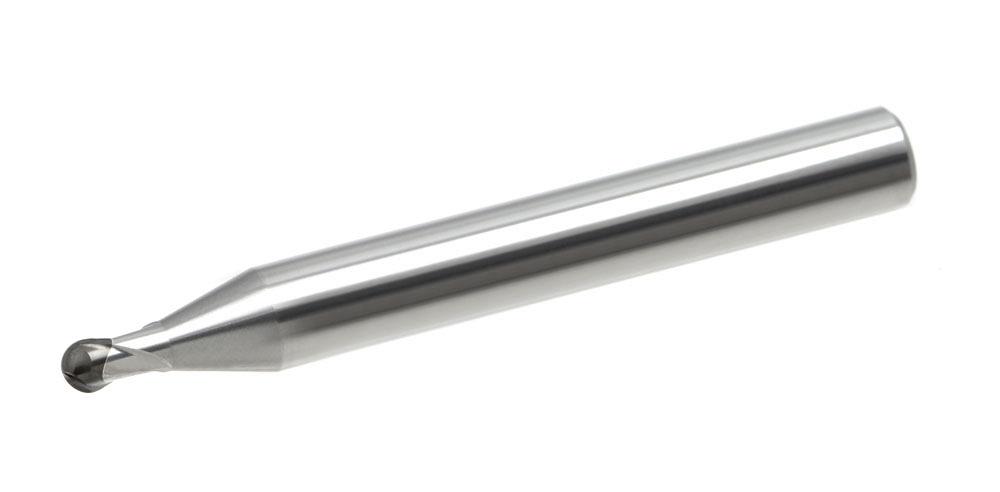
The Exocarb Max CBN ball end mill can be run at high speeds and still produce a good surface finish.
The use of flood coolant creates thermal instability in the tool as the cutting edge rapidly cools and reheats. This phenomenon, referred to as thermal shock, causes microfractures in the tool’s coating and substrate, which eventually lead to wear and chipping of the cutting edge.
During hard milling, air coolant or mist coolant should be used. The air will gently cool the tool without causing thermal shock while also aiding in chip evacuation. Using mist coolant or minimum quantity lubrication also provides the added value of lubricating the cutting edge, which reduces friction and produces better-quality surface finishes. Mist coolant typically is oil-based, which does not absorb heat like water-based coolants, thereby not causing rapid cooling of the cutting edge.
Although hard milling may seem challenging, using the proper equipment and strategies greatly improves productivity, accuracy, and finish.
Correct selection and application of tools, along with some know-how, will result in successful hard milling. And, understanding the benefit of investing in these material- and application-specific tools reduces overall manufacturing costs.
Adam Dimitroff is applications engineer for OSG Canada, 538 King Forest Court, Burlington, Ont. L7P 5C1, 905-632-8032, www.osgtool.com.
About the Author
subscribe now
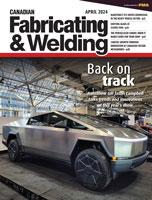
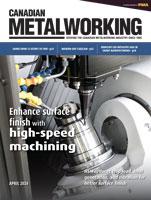
Keep up to date with the latest news, events, and technology for all things metal from our pair of monthly magazines written specifically for Canadian manufacturers!
Start Your Free Subscription- Trending Articles
Automating additive manufacturing
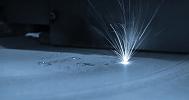
Sustainability Analyzer Tool helps users measure and reduce carbon footprint
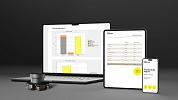
CTMA launches another round of Career-Ready program
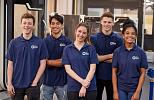
Sandvik Coromant hosts workforce development event empowering young women in manufacturing
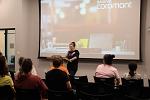
GF Machining Solutions names managing director and head of market region North and Central Americas
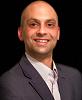
- Industry Events
MME Winnipeg
- April 30, 2024
- Winnipeg, ON Canada
CTMA Economic Uncertainty: Helping You Navigate Windsor Seminar
- April 30, 2024
- Windsor, ON Canada
CTMA Economic Uncertainty: Helping You Navigate Kitchener Seminar
- May 2, 2024
- Kitchener, ON Canada
Automate 2024
- May 6 - 9, 2024
- Chicago, IL
ANCA Open House
- May 7 - 8, 2024
- Wixom, MI