Associate Editor
- FMA
- The Fabricator
- FABTECH
- Canadian Metalworking
Optimize finish turning of titanium
A better surface finish comes down to proper insert selection, coolant, and speed
- By Lindsay Luminoso
- August 17, 2020
- Article
- Cutting Tools
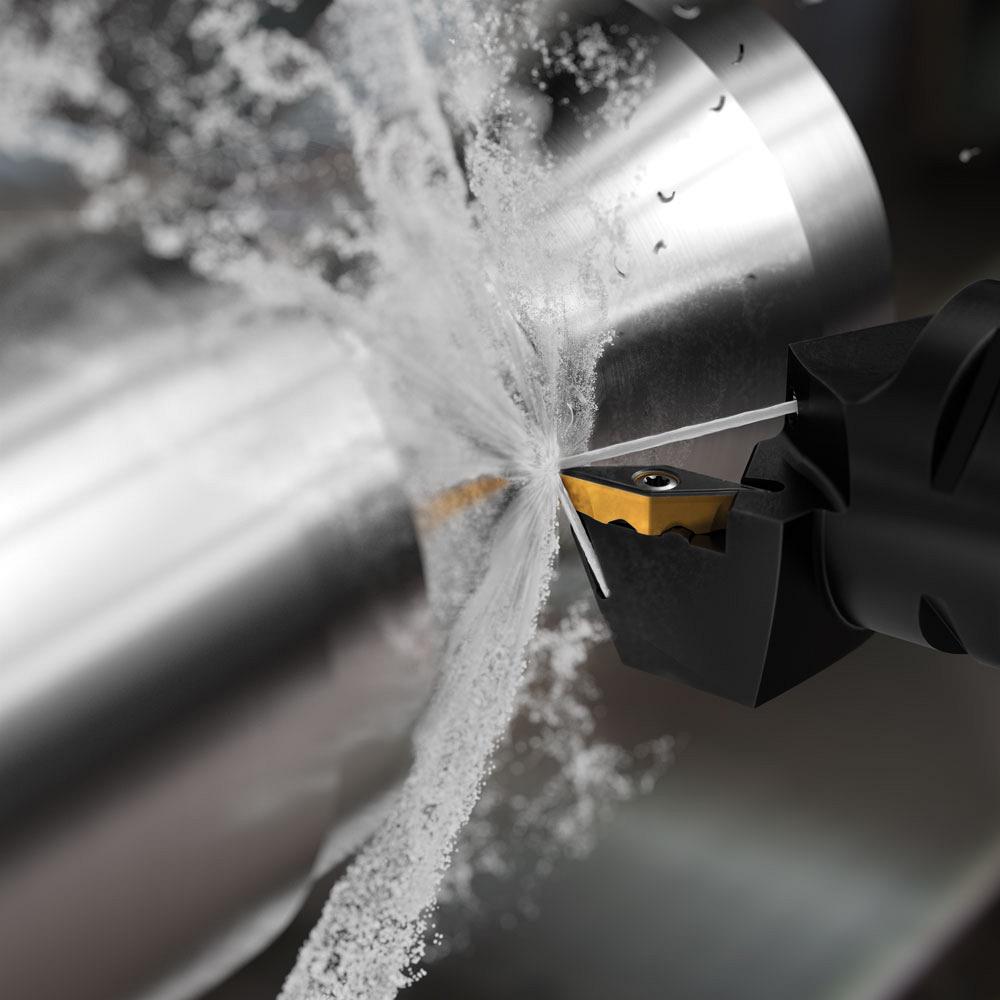
Finish turning of titanium must be a wet process. High-precision coolant offers significant advantages, particularly as it can be directed to the cutting zone. Photo courtesy of Sandvik Coromant.
Titanium generally is used to produce critical aerospace components and medical devices. It offers a high strength-to-weight ratio and excellent corrosion resistance, which enables it to be used for designs with thin walls.
It’s no secret that titanium alloys are difficult to machine, particularly compared to general and stainless steels. It has poor thermal conductivity and generates high cutting forces and heat at the cutting edge. The demand this material places on cutting tools is significant and can lead to both premature tool wear and poor surface quality if not done properly.
The low modulus of elasticity causes greater workpiece springback in these materials. This modularity is one of the material’s strengths, particularly when it comes to structural aerospace components that require that movability quality. However, this makes it a challenge to machine, often resulting in tool vibration, chatter, and poor surface finish.
"Titanium in general does not shear efficiently, so the material springs back and the size control of a component is more difficult," said Edwin Tonne, training and technical specialist, Horn USA Inc., Franklin, Tenn. "The finishing pass depth must be carefully maintained to account for this behaviour. Additionally, during finishing the forces and heat are concentrated over a small region of the cutting edge, which breaks down the edge more rapidly than in other materials."
Certain applications, particularly critical components in aerospace, have stringent surface integrity requirements. Many shops have had tried-and-true certified processes in place for years. These processes may be working, but with the latest cutting tool advancements, there are often better or more production options available, particularly as they relate to finish turning.
"We have seen that many shops are unwilling to change from their current processes, even if it means better finishes," said Kevin Burton, turning product and application specialist, Sandvik Coromant, Mississauga, Ont. "If the certified process uses an uncoated carbide insert, shops may not want to change to a coated or diamond insert because of the extra cost both from a time and financial standpoint. It’s the same with grades. With the new generation of grades out, some look different with different colours even though they typically have the same elements, just different percentages. Yet shops tend to be concerned about the coating being left behind on the surface of the part."
Burton noted that although current processes may be working, upgrading to newer cutting tools with different coatings or grades can provide significant productivity gains and better surface finishes.
Insert Options
For many years shops have been using uncoated inserts in titanium, and many still do. But now with so many different types of titanium, there are additional factors to consider for better surface finish when turning.
The experts recommend using a physical vapour deposition- (PVD-) coated insert because it is thinner. With titanium, it’s not advisable to use a thick coating because of the chemical reaction that can occur. Many of today’s coatings have titanium in them, like TiCN, which is used in chemical vapour deposition (CVD). This is why PVD is more commonly recommended.
"PVD coatings have high temperature resistance and lubricous surface, which reduces built-up edge and heat," said Tonne. "When it comes to inserts, the best shape is round, but it is often not practical due to part shape. C- or W-style inserts offer the best finish with clearance for part features. For negative-type inserts, make sure the top rake is positive. If tight tolerances are required, fully ground inserts can improve outcomes."
Tonne noted that there is a misconception that shops can use a roughing insert for finishing. Geometries and edge preparations are specifically designed for an application, so he recommends inquiring with the tooling vendor on the best insert, not a universal insert.
For finish turning, Burton suggests that polycrystalline diamond (PCD) inserts are the way to go because of the much higher surface speed, which of course reduces cycle time drastically. However, he noted that some shops have a difficult time accepting a visual difference of the surface.
"When we start finish-turning with PCD, it looks totally different than with other inserts," said Burton. "The titanium will look really nicely polished and almost have a hardened steel, superfinished look."
Why Wipers?
Similar to PCD inserts, wipers are the first choice in stable conditions and it’s recommended to use wipers whenever it is possible.
"We noticed this many years ago when we introduced wipers," said Burton. "Because of the refraction of light, wipers produce a different-looking surface, showing a grey scale surface appearance. But the surface quality, when measured, is still better. That’s a challenge that many shops have to understand and overcome."
Wipers are considered primarily as high-feed-rate machining inserts. Using them shops can increase the feed rate, which translates into less time in the cut, effectively increasing tool life. But if wipers are used at a normal feed rate, shops can gain measurable improvements in surface quality.
"The rule of thumb is the surface finish will be twice as good when a normal feed rate is maintained; doubling the feed rate will maintain normal surface finish," said Burton.
A wiper insert is built up through a number of extra radii. This makes the engagement surface longer, which also affects the surface in a positive way. A long engagement surface also affects the cutting force and the vibration sensitivity.
High-precision Coolant
Finish turning of titanium must be a wet process. A high-precision coolant offers significant advantages, particularly as it can be directed to the cutting zone.
"We recommend using tooling with internal coolant; this delivers coolant precisely to where it is needed," said Tonne.
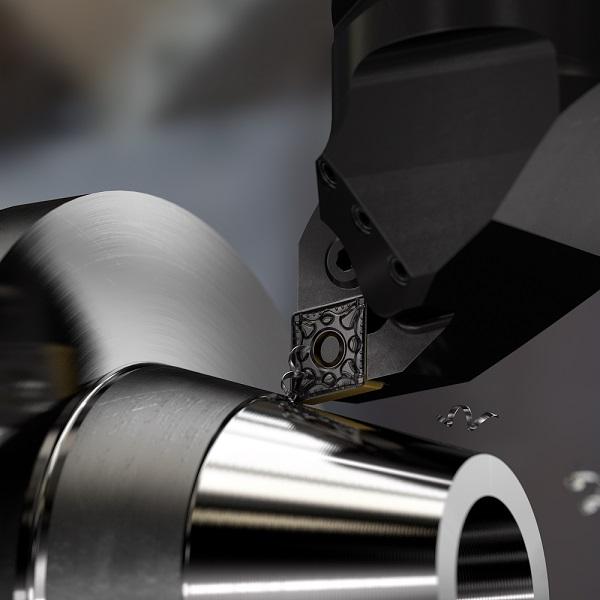
Upgrading to newer cutting tools with different coatings or grades can provide significant productivity gains and better surface finishes. Photo courtesy of Sandvik Coromant.
Having the ability to direct the coolant to the cutting zone is particularly important with titanium. It’s also recommended that shops use both over- and under-coolant for finishing operations and depth of cuts below the nose radius. This allows for the full effect of the high-precision coolant for better chip control, surface finish, and tool life.
As for the coolant, making the mix a bit stronger than standard can also be advantageous.
Maximizing Surface Finish
The experts agree that shops need to explore many options if they hope to improve surface finish when turning titanium.
"One misconception is that turning almost no material on the last pass will improve surface finish," said Tonne. "In most cases, the finishing pass depth should be equal to the radius of the tool used for turning. Using zero-depth passes will often fail."
Tonne added that it’s important for shops to inspect tooling centre height positions frequently. Incorrect cutting heights will result in reduced surface finish quality.
Speed Factor
Depending on the type of titanium alloy, speeds and feeds will differ.
"All titanium runs with the same general parameters is one misconception," said Tonne. "Usually the phase of the metallurgy is the best starting point. Alpha phase titanium alloys tend to run higher speeds and feeds. Alpha beta, which is the most prevalent, is well-documented, and finally beta alloys are the most difficult. The key is to research the material and understand the properties."
For example, Ti-5553 requires a very hard surface coating to basically get through it. This material can run at only around 50 per cent of the speed of Ti6Al4V.
Tonne added that titanium is much more sensitive to small changes in speed due to its heat-resistant nature. Speed should only be bumped up in 5-m/min. (15-SFM) steps. It’s also important not to run too slowly, because running below the recommended speed for a given tooling system will cause material to build up on the cutting edge, which effectively dulls the edge.
"Speed is the killer in all materials but very much so in titanium," said Burton. "If you go from uncoated to coated, then your speed can go up. Speed is productivity because your feed per revolution stays the same, but the speed goes up. This allows the feed per minute to increase, which is an advantage. Typically, this can be around a 20 per cent gain in productivity. If a shop goes to, say, a PCD insert for finish turning, there will be an even bigger productivity gain. With coated carbide you can expect 150 to180 SFM but up to 600 with PCD. The gain in productivity is huge."
Associate Editor Lindsay Luminoso can be reached at lluminoso@canadianmetalworking.com.
Horn USA, www.hornusa.com
Sandvik Coromant, www.sandvik.coromant.com
About the Author
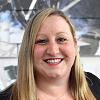
Lindsay Luminoso
1154 Warden Avenue
Toronto, M1R 0A1 Canada
Lindsay Luminoso, associate editor, contributes to both Canadian Metalworking and Canadian Fabricating & Welding. She worked as an associate editor/web editor, at Canadian Metalworking from 2014-2016 and was most recently an associate editor at Design Engineering.
Luminoso has a bachelor of arts from Carleton University, a bachelor of education from Ottawa University, and a graduate certificate in book, magazine, and digital publishing from Centennial College.
Related Companies
subscribe now
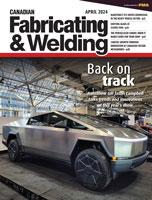
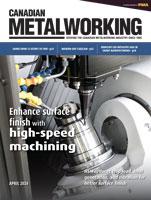
Keep up to date with the latest news, events, and technology for all things metal from our pair of monthly magazines written specifically for Canadian manufacturers!
Start Your Free Subscription- Trending Articles
Automating additive manufacturing
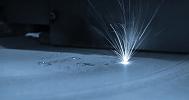
Sustainability Analyzer Tool helps users measure and reduce carbon footprint
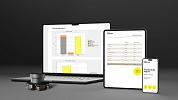
CTMA launches another round of Career-Ready program
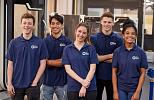
Sandvik Coromant hosts workforce development event empowering young women in manufacturing
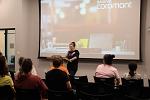
GF Machining Solutions names managing director and head of market region North and Central Americas
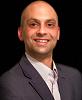
- Industry Events
MME Winnipeg
- April 30, 2024
- Winnipeg, ON Canada
CTMA Economic Uncertainty: Helping You Navigate Windsor Seminar
- April 30, 2024
- Windsor, ON Canada
CTMA Economic Uncertainty: Helping You Navigate Kitchener Seminar
- May 2, 2024
- Kitchener, ON Canada
Automate 2024
- May 6 - 9, 2024
- Chicago, IL
ANCA Open House
- May 7 - 8, 2024
- Wixom, MI