Thread Milling Product Manager
- FMA
- The Fabricator
- FABTECH
- Canadian Metalworking
Choosing a large thread milling tool
Production volume, thread size, and pitch variability matter in tool selection
- By Marlon Blandon
- June 29, 2022
- Article
- Cutting Tools
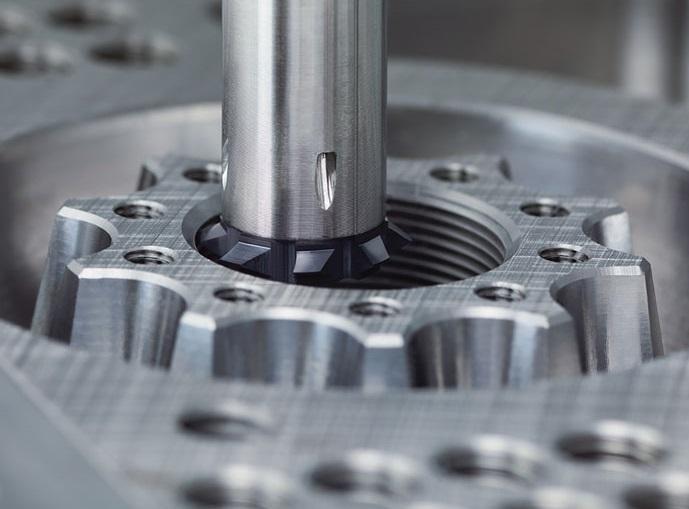
The EMUGE-FRANKEN Circ-GF circular thread milling bar/bodies with exchangeable face inserts provide an excellent modular solution for milling larger thread dimensions thanks to a high-flute-count insert that creates high metal removal rates.
Part complexity, material, and machine tool setup all have an effect on tool choice. When creating threads, in particular, machinists have many options, including thread mills with exchangeable heads, indexable tools, and solid tools.
Many variables exist, and each type of tool has its own benefits for specific applications and metal removal rates. And, while selection is highly dependent on the workpiece itself, among the most important variables are thread size and thread depth, part volume for the specific thread size, workpiece material and hardness, and the machine tool being used.
Solid Carbide Option
We often think that a full milling section, solid-carbide cutter is the fastest way to produce large thread sizes because of the nature of the tool. While this is true, this type of tool is limited to one specific pitch and to a maximum depth of cut of 2xD.
When threading tough materials such as high-temperature alloys and mold steels, several radial passes are required to bring the thread into gauging values, thus increasing cycle time per hole and overall cycle time per part.
Indexable Option
For job shops producing threads that are 7/8 in. and larger, and where part volume is low and cycle time is not an issue, consider the benefits that come from the versatility and simplicity of a single-plane indexable tool.
These tools can be used for several thread sizes, diameters, and pitch combinations (in some cases reaching up to 3xD in thread depths with up to four times more tool life) because of the ability to index the tool.
These cutters are designed with precision-ground pockets for each individual insert, making them very stable and the preferred system choice for shops making large threads in tough materials. They also are used in setups where the available machines cannot handle the torque needed to turn a tap.
They also are a great option for short runs of odd diameter/pitch combination thread requirements.
Exchangeable-head Option
Exchangeable heads, or modular systems, are designed to be easy to set up and to achieve very high metal removal rates. Using high-flute-count inserts, the feed rate can be increased in most materials, reducing cycle time considerably. Modular systems are a good option when producing large thread sizes in 2xD thread depth ratios, when needing to combine tools to increase machine tool magazine space, and to reduce cycle times.
One single-edged insert produces numerous pitch and diameter combinations, and the body/seat design enables the inserts to have more cutting edges on the same circumference than those found in indexable systems.
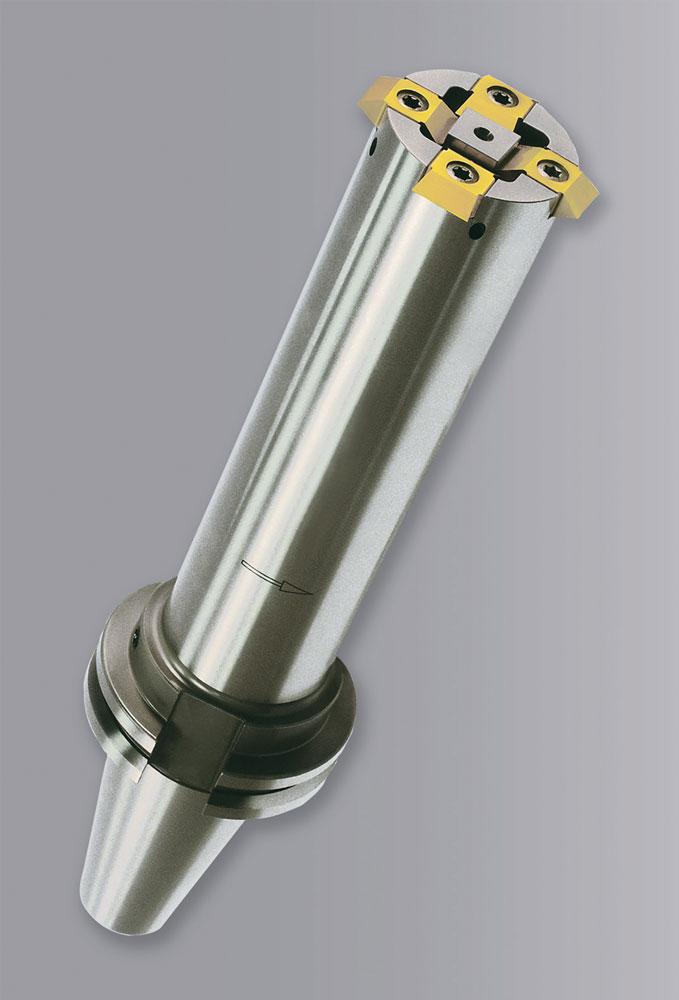
The EMUGE-FRANKEN Gigant-IC is a partial-profile insert technology requiring only two separate inserts for multiple diameters and pitches, including UN, UNC, UNF, UNEF, UNJF, UNS, M, MF, MJ, NPT, NPMS, and API.
Production variables, thread sizes, and thread depths are the decisive factors when determining if a multipurpose tool is advantageous. Set up time and cycle time are not key factors (depending on the application, the type of shop, and part volume). A single-plane indexable thread milling cutter is not the fastest method but is an economical way to minimize costs and achieve a good-gauged thread.
You can index the inserts for added tool life and exchange threading inserts easily to produce numerous thread diameters and pitch combinations using the same bar.
Job shops dealing with different short runs of specific materials (production variables) on an ongoing basis, and where equipment is limited in horsepower and torque needed for tapping large thread sizes, can greatly benefit from using single-plane, indexable multipurpose-type cutters.
Conversely, if you have large runs of parts (by volume), if possible, use a faster method to produce those threads than the multipurpose-type tool. These situations call for full milling section, solid-carbide cutters.
For shallow holes—2xD maximum—use a solid-carbide, full milling section cutter designed for multiple diameters of the same pitch. It is more cost effective because of reduced machining time (cycle time per hole).
Tool life also is better in some materials when using a full milling section cutter because they use more cutting teeth to remove material. Modular, multipurpose tools use just a single row of teeth with maybe three to five points on the same circumference. However, most shops producing large thread sizes typically are doing small to medium runs of these parts and will almost always be OK with a single-plane multipurpose/indexable option.
The ID and OD
ID and OD threads are not symmetrical. So, with indexable thread mills you must use a specific insert for the ID and another insert for OD, but without having to buy separate setups or bodies. It is just as easy as changing the insert.
The modular exchangeable heads, although easy to setup, also require two different inserts, one for internal and one for external threads.
As for solid-carbide full milling section cutters, some manufacturers offer separate cutters with specific grinds to meet the internal thread tolerance only, and those that are ground for external threads only.
Tool Wear
Tool wear typically is noticed first by gauging the threads.
The most common wear seen is a dulling of the cutting edges, which happens on the teeth-cutting flanks.
Start by programming the cutter with a specific cutter compensation value to achieve the desired pitch diameter. Once you have dialed that in and found the “sweet spot,” run the tool and keep checking the finished threads.
When the threads’ go-gauge starts to get tight, increase the cutter compensation and keep it running like this until you have to compensate it again. Eventually, the compensation value will no longer have an effect on increasing the pitch diameter for gauging the threads properly, and that’s when you’ll know the edge is done and it is time to change or index the inserts or exchange the modular head.
Coolant Use
When performing thread milling, it’s more important to cool the cutting edge than it is to have high lubricity. This means that high oil concentration is not necessary for the coolant.
Water-soluble emulsions will help a lot in getting chips up and out of the way. And a nice cold blast of air also works just fine. Avoid using neat oils or high-viscosity agents when thread milling so you do not recut chips or obstruct the chip evacuation.
Technology Spotlight: Thread mills
EMUGE-FRANKEN USA has options for all three tool categories mentioned previously, and it offers two options for insertable cutters.
Gigant-IC
A versatile system for threads 7/8 in. or M20 and above with through-coolant capability, the design of these tools is based on lean manufacturing principles. This tooling system facilitates quick setups and rapid changeovers for numerous threading applications.
Using micro-grain carbide inserts with a TiAlN-T4 coating enables easy machining of all difficult materials.
This is a partial profile insert technology requiring only two separate inserts for multiple diameters and pitches, including UN, UNC, UNF, UNEF, UNJF, UNS, M, MF, MJ, NPT, NPMS, and API. This system produces low radial cutting pressure, helping to ensure true-to-gage threads, providing good process consistency and safety for expensive workpieces and promising a long tool life.
Circ GF
Circular thread milling bar/bodies with exchangeable face inserts provide an excellent modular option for milling large thread dimensions, such as ½ in. or M12 and above.
A rigid, anti-vibration body design creates thread-to-diameter ratio depths of 2xD and 2.5xD and has a coolant supply exiting radially at the insert’s cutting edge for optimized cooling, chip evacuation, and thread quality.
These single-edged face inserts are fast and easy to setup; they affix rigidly in a solid-steel precision pocket with a Torx locking screw, providing low radial cutting pressure to help ensure true-to-gauge threads. Easy programming and maintenance are characteristics of this system, with the high-flute-count insert providing high metal removal rates.
Marlon Blandon is thread milling product manager, EMUGE-FRANKEN USA, 1800 Century Dr., West Boylston, Mass. 01583, 800-323-3013, www.emuge.com.
About the Author
Related Companies
subscribe now
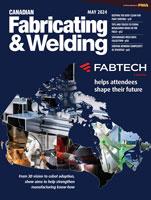
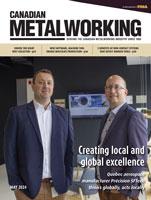
Keep up to date with the latest news, events, and technology for all things metal from our pair of monthly magazines written specifically for Canadian manufacturers!
Start Your Free Subscription- Trending Articles
Sustainability Analyzer Tool helps users measure and reduce carbon footprint
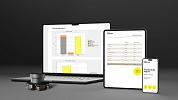
Mitutoyo updates its end-user portal
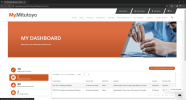
Enhance surface finish with high-speed machining
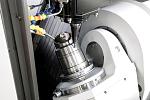
Equispheres secures $20 million investment round
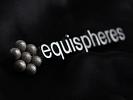
Solid carbide drills produce precision holes in short chipping materials
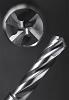
- Industry Events
Automate 2024
- May 6 - 9, 2024
- Chicago, IL
ANCA Open House
- May 7 - 8, 2024
- Wixom, MI
17th annual Joint Open House
- May 8 - 9, 2024
- Oakville and Mississauga, ON Canada
MME Saskatoon
- May 28, 2024
- Saskatoon, SK Canada
CME's Health & Safety Symposium for Manufacturers
- May 29, 2024
- Mississauga, ON Canada