Vice-President of Operations and Service
- FMA
- The Fabricator
- FABTECH
- Canadian Metalworking
Simplify your supply chain management
Enterprise resource planning software enables better decision making
- By Mike Melzer
- July 4, 2022
- Article
- Automation and Software
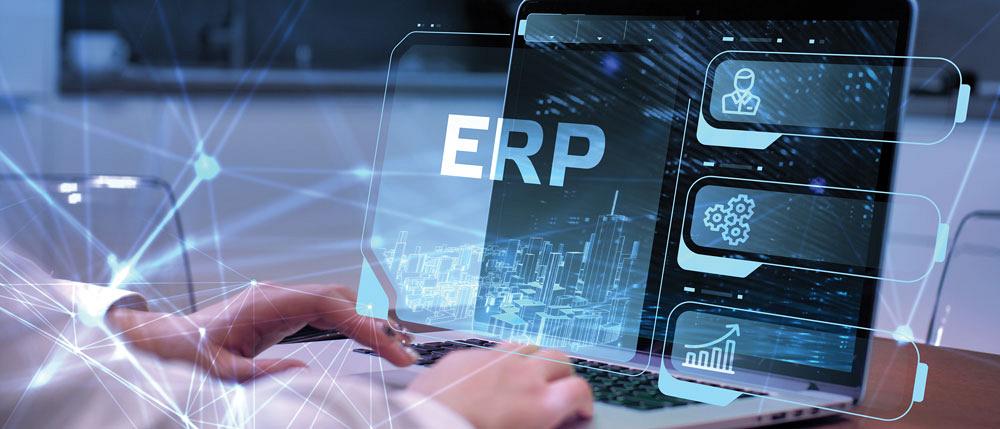
Enterprise resource planning software is a powerful tool that keeps supply chains operating smoothly by providing data about every aspect of the shop floor. putilich/iStock/Getty Images Plus
Effective supply chain management (SCM) is essential and more important than ever to help ensure the efficient movement of raw materials, goods, and services in today’s global markets. When SCM is managed well, it lowers cost for manufacturers, distributors, and consumers, and helps avoid bare shelves caused by a lack of product availability.
However, effective SCM also involves a lot more than putting raw materials and finished goods on tanker ships, trains, and trucks and getting them from point A to point B in a timely manner.
SCM begins the moment you receive an order from a customer, setting in motion a series of processes and activities that affect the entire supply chain. When you can’t produce the desired part or product in time to meet the customer’s deadline, it introduces inefficiency and delay into every subsequent point in the supply chain.
Enterprise resource planning (ERP) software is a powerful management tool to help keep the supply chain operating smoothly. By providing data visibility for every aspect of the shop floor, you can stay on top of scheduling, inventory, purchasing, production, shipping, and other vital supply chain functions.
Whether it’s a custom job shop or a product line manufacturer, ERP software simplifies the process of getting products out the door, on time, and within budget.
You can see everything that’s happening on the shop floor at any given time with a good ERP system. The software tracks and displays real-time data on parts in inventory, materials on order, available machine and labour capacity, and finished goods ready for shipment.
It also shows the current status of in-progress jobs so managers can identify “hot” jobs and make in-the-moment decisions about whether to push other jobs back or schedule overtime to meet a promised shipping date.
Most importantly, ERPs enable you to make decisions based on accurate, up-to-date information rather than guesswork.
Describing all of the ways that ERP supports smart SCM could easily fill an encyclopedia, so let’s look at three of the most impactful features for keeping your supply chains operating as efficiently as possible.
1. Automate to Eliminate
In today’s JIT manufacturing environment, shipping finished parts on time gets the ball rolling for efficient SCM. Sending jobs out the door late throws a wrench into the process by negatively affecting everyone further down the line.
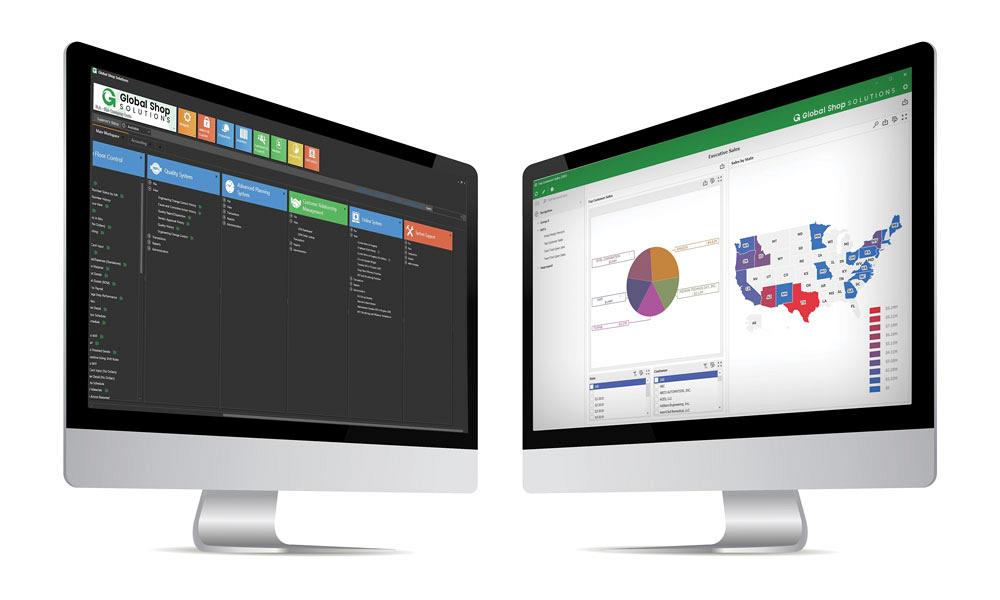
Enterprise resource planning systems have robust management dashboards that combine easy-to-read summaries of key production data with the ability to drill down into detailed information from one screen. Global Shop Solutions
Many factors lead to missing due dates. One factor that is common today is the ability to hire enough people. When labour shortage becomes a problem, smart manufacturers use their ERP to automate tasks and activities that typically are performed manually so they can continue shipping jobs on time.
Few activities are more inefficient than manually distributing paper documents throughout the shop. With an ERP system, you can go as paperless as you want.
For example, ERP software eliminates hand-written work orders by creating digital versions in the system. These work orders are accessible to anyone on the shop floor from their workstations, so they don’t have to spend time distributing them manually.
Tired of handwriting dispatch lists? ERPs automatically produce them with just a few keystrokes. Routing software in the ERP system helps ensure that all production processes are listed in the correct order and are easily modified and updated, if necessary.
The ability to integrate material requirements from the router to your bill of materials (BOM) saves huge amounts of time, especially with large BOMs requiring hundreds, or even thousands, of parts. Automating much of the purchasing process cuts down on labour time and makes it easier to manage today’s very short lead times. Purchasing materials JIT saves money, but sometimes it makes sense to bring in materials sooner to protect against stockouts. With an ERP system, you simply schedule the job requirements and the auto-purchasing system shows you what you need to buy and when you need it.
Quality ERP software also helps simplify the purchasing process by letting you import customer drawings directly into your system.
For example, let’s suppose that you receive a rush order from one of your best customers. Importing all of the drawing information into your ERP system allows you to create purchase orders and research vendors immediately to produce the fastest delivery and best price.
If you’re looking for ways to overcome a labour shortage and keep your production processes running smoothly, don’t wait . . . automate.
2. Trust Your Inventory
Another challenge currently affecting manufacturers is a difficulty in sourcing parts and materials because of logjams or other problems at the macro level, such as the staggering number of products and materials currently sitting in shipping containers waiting to be unloaded because of the pandemic.
Meeting this challenge starts with knowing exactly what you have in inventory at all times. No tool is better equipped for this vital task than ERP software.
Manual inventory counts and material movement tracking is a time-consuming and often inaccurate task. ERP software reduces labour time dramatically and maximizes inventory accuracy by using bar code scanning for part identification, mobile material movement tracking, and material counts.
Scanning incoming materials eliminates the errors that occur with manual receiving. Mobile material movement records transactions as they occur, anywhere on the shop floor, so you know exactly what went where. When cycle counting, ERPs let you know instantly if your manual count matches what you show in inventory. Any mismatches send a red flag indicating that some transactions aren’t being conducted through the system.
Most ERP systems also offer an automatic reorder feature that makes it easy to maintain stock without running out of materials or overbuying. When inventory levels for a certain material fall below your pre-set minimum, the inventory module automatically triggers an order to bring in more material.
The entire production process slows down when you can’t trust your inventory numbers. When properly conducting all inventory transactions in an ERP system, you get precise, up-to-date inventory levels and locations that allow you to accept short lead times and get jobs into production quickly.
3. On Time, Every Time
For manufacturers, the primary goal of efficient SCM is on-time delivery, and that starts with a streamlined scheduling process.
If a regular customer needs 500 parts with a very short lead time, you need to know how much labour and materials are required to complete the job, examine your inventory of both, and agree to a shipping date. Is your ability to squeeze the job into your schedule based on accurate data or rough estimates?
Manual scheduling on spreadsheets that may have outdated information often results in “hoping” you can meet the customer’s deadline. ERP provides access to all the data necessary to determine whether you can deliver as promised, including:
- Available labour and machine capacity
- Materials on hand
- Incoming material
- Status of all in-progress jobs
- Outside processing, if any
Every factor than can affect the job is all there at your fingertips.
But what if the data indicates you can’t make the due date? The best ERP systems handle that by rescheduling and rerouting jobs. With some ERP systems, it’s as simple as “dragging and dropping” jobs into different places to see how it affects the schedule. This flexibility also lets you see the effects of scheduling overtime, bringing in temps, and pushing back the schedule to accommodate rush jobs. Most importantly, when you give your customer an answer, you’ll know it was based on accurate data.
Most ERP systems have robust management dashboards that combine easy-to-read summaries of key production data with the ability to drill down into detailed information from one screen. The number, type, and sophistication of these dashboards varies from one system to another, but they provide critical data for making informed decisions about customer due dates and your ability to achieve them.
When we ask our ERP customers about their most important dashboards, three commonly come up. They are:
Master schedule dashboard. This helps keep jobs on schedule by providing complete visibility of all open orders. It allows you to print and release work orders, put them on hold, issue material, and close jobs.
Production dashboard. The data on this screen indicates where a job is on the floor, shows the estimate versus actual hours, and how much time is left before the deadline. It is especially helpful for job/machine shops that don’t stock finished goods inventory and have to make all parts as customers order them.
Shipping dashboard. This screen displays what’s available to ship right now. If you have some of the parts needed in stock, shipping them now may allow you to push back the due date to complete the order without disrupting other jobs.
The best dashboards offer a high degree of customization so you can adjust the data to track and display it in the manner you prefer. For example, product line manufacturers that make standard parts or products can customize the production dashboard to show sales, the status of current work orders, and what needs to get shipped that day.
These and other types of dashboards positively impact on-time delivery by helping you understand where bottlenecks occur so you can take appropriate action to resolve them.
SCM problems caused by COVID-19 continue to make life difficult for manufacturers everywhere. ERP provides the features and functionality that allow your business to adjust quickly to this and other circumstances that effect your internal SCM. Automation, inventory, and flexible scheduling are a good place to start, but ERP offers many more features to help you get parts and products out the door on time.
If you’re still handwriting work orders, doing manual inventory counts, and scheduling on spreadsheets, do yourself a favour and find an ERP system that’s right for your business. Your employees and your customers will appreciate it.
Mike Melzer is vice-president of operations and service for Global Shop Solutions, 975 Evergreen Circle, The Woodlands, Texas 77380, 800-364-5958, www.globalshopsolutions.com.
About the Author
Related Companies
subscribe now
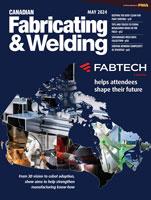
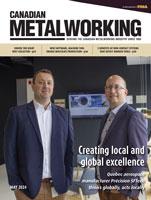
Keep up to date with the latest news, events, and technology for all things metal from our pair of monthly magazines written specifically for Canadian manufacturers!
Start Your Free Subscription- Industry Events
Automate 2024
- May 6 - 9, 2024
- Chicago, IL
ANCA Open House
- May 7 - 8, 2024
- Wixom, MI
17th annual Joint Open House
- May 8 - 9, 2024
- Oakville and Mississauga, ON Canada
MME Saskatoon
- May 28, 2024
- Saskatoon, SK Canada
CME's Health & Safety Symposium for Manufacturers
- May 29, 2024
- Mississauga, ON Canada