Freelance Writer
- FMA
- The Fabricator
- FABTECH
- Canadian Metalworking
Automation success story
Gilbert Products doubles production output with flexible manufacturing system
- By Mark Cardwell
- June 13, 2022
- Article
- Automation and Software
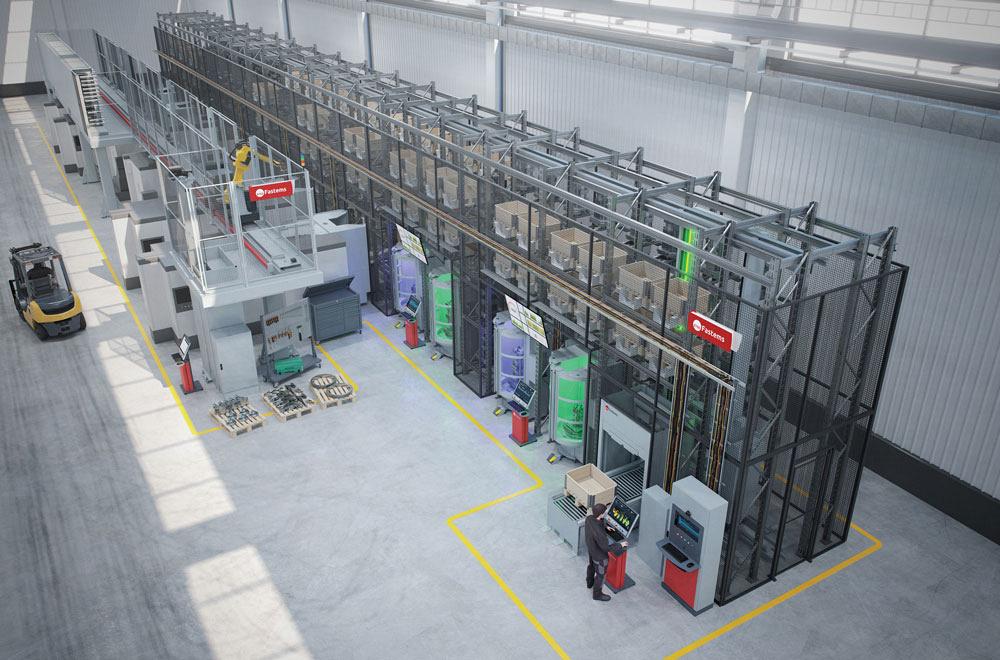
The Fastems FMS was installed in a new 40,000-sq.-ft. manufacturing facility the company built in the Roberval, Que.
Canadian industrialist Sylvain Gilbert was on a visit to Fastems headquarters in Finland in 2005 when it hit him. Sylvain, founder and president of Gilbert Products, a Quebec- based designer and manufacturer of equipment for the forestry, wood, construction, and snow grooming industries, had long been contemplating the purchase of a robotic flexible manufacturing system (FMS) to improve his company’s production process and help bring its activities at four sites together under one roof.
“I’d watched an FMS in action in Germany several years earlier for four or five hours,” recalled Sylvain. “At first it wasn’t obvious to me what the advantages were of such a large installation for a few CNCs. But as I watched it run unattended and the setup work being done on a station where the raw material was being delivered with the corresponding jib, I started dreaming of getting a similarsystem. By the time I visited Fastems in Finland, that’s when I fully understood and appreciated the potential their technology had for us. I decided to buy it right then and there.”
The Fastems FMS was installed a year later in a new 40,000-sq.-ft. manufacturing facility the company built in the Roberval, Quebec, industrial park, a two-hour drive north of Quebec City. The Fastems FMS became the robotic heart of an automated production systemthat quickly transformed the company’s way of thinking, doing, and being. Initially connected to and feeding two 5-axis DMG MORI milling machines with 240-tool magazines and 1-cubic-m work envelopes, the FMS controlled and quarterbacked the manufacture of myriad variable metal parts and modules that Gilbert uses to make its wide array of high-performance industrial brand products, most notably planers for the global sawmill industry.
Automated Machining
Working as an integrated entity with the machine tools, which were doubled in number to four in 2013, the FMS components–a rail-guided stacker crane, a setup station, five material stations (for inventory management and kitting of 300 material pallets and 90 machine pallets), a buffer storage, and manufacturing management software (MMS) control system—helped to increase the flow and speed of production items for Gilbert Products’ machine tools and allowed them to be used at nearly 100 per cent capacity overnights, on weekends, and holidays thanks to pre-configured setups. The system also helped to smooth out the complex, frustrating, and time-wasting problems that often are associated with the organization and management of production resources like tools, materials, and data inscheduled production in variable, small-batch manufacturing.
“The FMS completely changed our production philosophy,” said Sylvain. “Before Fastems we required human intervention for the most complex tasks. But the system did all that and better: better tool management, better CNC program tracking, and better jobplanning. It put pressure on everyone to improve.”
Two-year Journey
According to Sylvain, it was easy for employees to learn how to run the $7 million system.
“But it took us two years to get to the point where we could fully harness its capabilities and benefits,” he added. “Our speed of production increased as did the quality of the parts we manufactured.”
The system also helped the company in terms of labour, because it allowed operators to input their knowledge into the system and help to multiply output.
“We basically doubled our production output with the same number of employees,” said Sylvain. “That enabled us to expand our product line and to more than double our sales revenues in just a few years.”
Sylvain also credited the introduction of the FMS with making his company both a market leader and a force to be reckoned with in all four fields it competes in–and not only in Canada, but around the world.
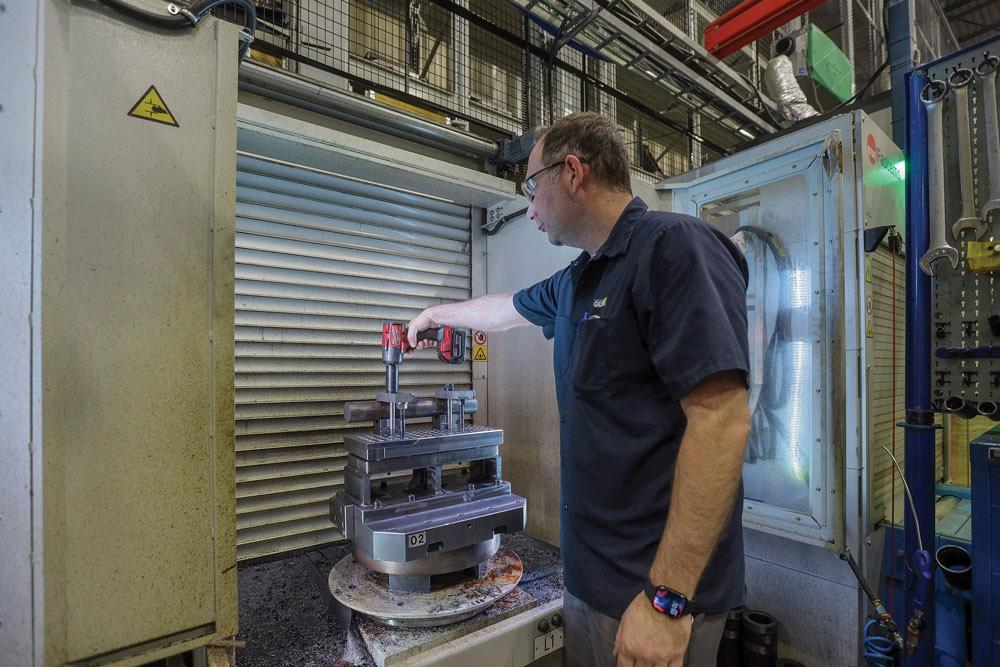
The company produces a series of specifically designed Gilbert products, including its excavator-mounted 3018 felling heads for logging and public works companies and its GM series of brush cutter-mowers.
“It made us much more competitive by helping to reduce our production costs,” he said. “Its impact on our business was even better than I had hoped for.”
To sustain his company’s growth—and because of his company’s positive experience with the system’s builder—Sylvain ordered a second, similar FMS from Fastems: a multi-level system (MLS) with a gantry tool system (GTS) that feeds pallets and tools to milling machines as well as material pallets to operators for raw material and fixture handling. Installed parallel to the first system in the Roberval plant in spring 2019 as part of a $5.5 million investment, the new MLS was connected to two new DMG MORI NHX 5500 4-axis milling machines.
“We needed to extend the capacity of the shop with new machining centres,” explained Frank Gilbert, the company’s production manager and Sylvain’s oldest son. “We looked at our production log and sized the machines for the parts we needed most. We chose 4-axis machines, which are more robust by design, so cycle times can be reduced. Also, the work envelope is smaller, so the travels are shorter.”
In addition to flexibility, if one of the machines stops for any reason, production is rerouted to the next available machine without human intervention, Frank said the new system offers a variety of savings, from time spent looking for tools and having to move them manually to actual tooling costs.
The company’s first FMS, he noted, requires the entire tool list to be loaded in the tool magazine before the stacker crane will bring a job to a CNC, meaning that multiple jobs needing the same tool must either be run on the same machine or require multiple iterations of the same tool to be on hand for use on other machines.
According to Frank, the FMS’s MMS control enables the system to look ahead in the job queues of all CNCs and predict when and where a tool will be needed. It then delivers tooling to machine tools just before use and, at the same time, keeps track of tool wear and notifies operators well in advance of the need for tool maintenance.
“With our new FMS, a job will be started even when the 15th tool it will need is being used elsewhere, because it knows the robot will bring it in time for the scheduled task,” said Frank.
While the original FMS remains dedicated to making more complex parts, Frank said it made sense to aim for efficiency with the new MLS.“We worked with Fastems and DMG MORI to come up with a setup that was tailored to what our customers were demanding,” he said.
Producing Parts for the Lumber Industry
Topping that list always is the urgent need for replacement parts by Gilbert Products’ customers, especially those in the wood and lumber industries, where time means money.
“Planers are our mainstay product, and we sell them worldwide, with about 60 per cent of sales in the U.S.,” said Frank. “Big losses can pile up fast when work gets stopped or slowed down due to a lack of parts.”
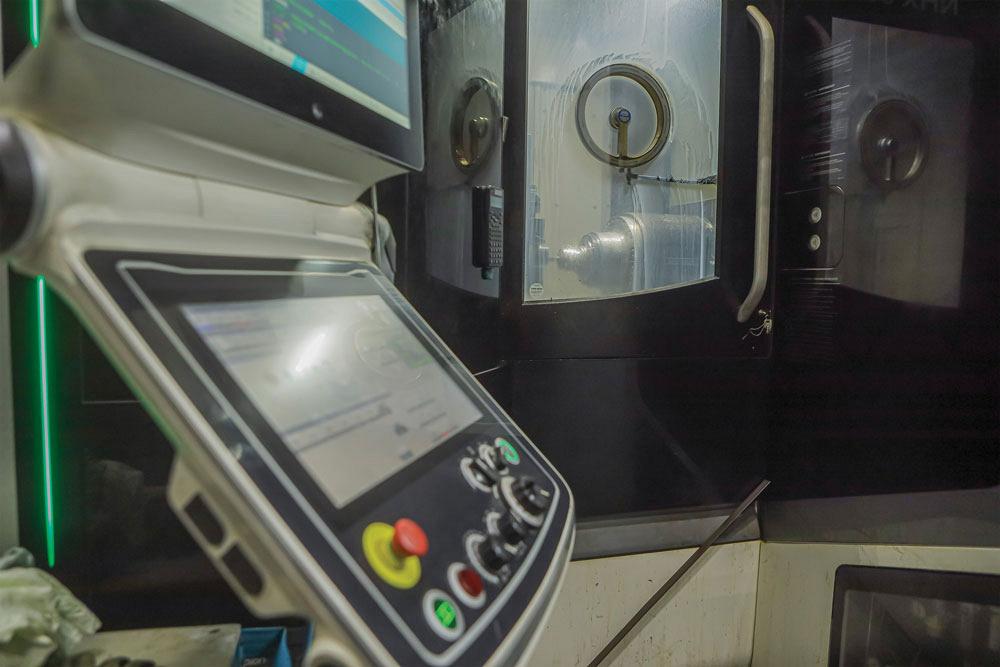
The FMS controls the manufacture of many metal parts on the company’s DMG MORI milling machines with 240-tool magazines and 1-cubic-m work envelopes.
From the get-go, Frank said the introduction of both the original and the newest FMSs have been a boon to his company’s sales performance, which is forecast to top $40 million in 2022, and its reputation for quality manufacturing and fast delivery of some two dozen products.
“[It’s] helped to make us an industry leader and keep our order book full well into the future,” he said.
To keep that momentum, he added, Gilbert Products is currently working with both DMG Mori and Fastems to add two more NHX 5500s to its newest FMS system, as well as an NHX 8000 horizontal milling machine for the machining of large workpieces and hard-to-cut materials.Frank credits his father with having the innovative foresight to see and comprehend the advantages of flexible manufacturing systems, along with the entrepreneurial spirit and wherewithal needed to invest in them.
“My dad is a hands-on guy who knows how to run every machine in the shop,” said Frank, 37. “He also knows when a job is done well, how it can be improved, and what products we should develop.”
His father, he added, is a quiet person who rarely raises his voice and says little in meetings, but when he does, it is often to voice a contrarian opinion.
“And he usually ends up being right,” said Frank, laughing. “It’s like he can tell the future and forecast the needs of the industries we serve. He’s a true visionary and innovator.”
How It Began
Born into a big family on a small mixed farm in the village of Saint-Prime, 10 km northwest of Roberval on the shores of Lac Saint-Jean, Sylvain grew up knowing he wanted to work for himself, but not on a farm.
“I hated farming,” said Sylvain. “I worked on our farm until I was 15 and that was enough for me.”
By then he was helping his father, who moonlighted as a carpenter, build houses in the area. Though he enjoyed working with wood, Sylvain’s interest soon turned to metal. “I liked working with metal and I thought it offered a lot more job and business opportunities,” he recalled.
After completing a machinist’s course at a regional trade school, Sylvain worked for a couple of local machine shops before landing a job at Industries Tanguay, a now-defunct manufacturer that made heavy equipment for Quebec’s then-thriving forestry and pulp andpaper industries. Among his duties was doing repairs and maintenance on equipment and machinery in commercial sawmills over the weekends when operations were shut down.
In 1986, at age 27, Sylvain decided to strike out on his own and landed similar repair and maintenance contracts with several regional sawmills. After a year of working from his pickup truck and his family’s garage, where he had a small lathe and milling machine in pre-CNC days, he rented a small shop and hired a half-dozen mechanics, machinists, and welders to help him make and repair broken parts from the motors and machines they dismantled and fixed in sawmills.
“I split my time between working in the shop and looking for new customers,” recalled Sylvain, now 64.
He also started building spare parts and novel pieces that modified sawmill machines to help make cuts better and faster.
“There were lots of broken parts and machines, especially planers, that were hard to adjust for the dimension of lumber,” said Sylvain. “It could take up to 30 minutes to get nice cuts. So, I’d come up with custom solutions to help improve performance.”
Soon, he added, companies were calling him to discuss their problems and to ask him to help them find resolutions. Other times he identified problems while doing repairs and suggested to companies possible options that would save them time and money.
“There was never a shortage of work because there were always lots of problems that needed fixing,” said Sylvain. “And that led us into making parts.”
First Expansion
After expanding into a new and bigger building in an industrial park, he invested nearly $1 million in CNC machines and hired several new employees.
In 1988 he introduced a felling head for wood harvesting. Since then the company has continued to produce a series of specifically designed Gilbert products, including its excavator-mounted 3018 felling heads for logging and public works companies and its GM seriesof brush cutter-mowers, which are renowned for their effectiveness, low operating costs, and versatility.
In the early 1990s, Gilbert Products expanded into another market when it introduced its own machines to help groom the snowmobile trails that criss-cross not only the Lac Saint-Jean region but much of Quebec during the long, cold winter months.
“Some snowmobiling groups came to see us and said they were having problems with the machines that were available on the market,” said Sylvain. “So, we bought some tractors and built groomers that we hooked up behind them and they were an instant hit.”

By automating its manufacturing process, the company essentially doubled its production output with the same number of employees.
Since then the company has continued to build and sell grooming drags and two series of snow groomer: the MCS and RTS. Soon after it began exporting its felling heads to the U.S. in 1996, Gilbert also became the first, and still the only, Canadian company to design and build planers for wood processing factories. Today the company offers three Gilbert brand-named models with a dozen different configurations, including a high-speed planer, a 6-roll planer, an S-series planer, a moulder planer, a mass timber planer, and feed tables.
Though the company has added a promising and fast-growing fourth category of brand-named products in recent years, the Gilbert Grizzly MultiGrip vibratory pile driver for the construction industry, which is designed to be mounted on any hydraulic excavator, and a control and assistance system, planers remain its bread-and-butter offering.
“Planers represent about 80 per cent of our sales,” said Sylvain. “They are quite complex pieces of equipment that are made with up to 1,000 metal parts and modules. The challenges involved with making them are what got me thinking about the need and possibilitiesof converting our production process to FMS.”
Now equipped with two Fastems robotic manufacturing systems; some two dozen CNC machines; and a brand-new, $1.3 million building with a large cafeteria, recreation rooms, and facilities for the company’s 130 employees, Sylvain is feeling bullish about the future ofthe family business he founded.
“We’re looking at another $4 million investment to expand our FMS and add those two MORI machines,” he said. “That would give us a total of eight [automated] machines. The ways things are looking, we’re going to need them, because demand for our products shows no signs of slowing down.”
All photos courtesy of Francis Vachon.
Contributing writer Mark Cardwell can be reached at m.cardwell@videotron.ca.
Fastems, www.fastems.com
Gilbert Products, www.gilbert-tech.com
About the Author
subscribe now
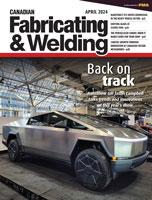
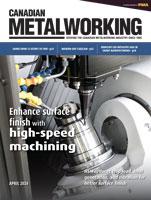
Keep up to date with the latest news, events, and technology for all things metal from our pair of monthly magazines written specifically for Canadian manufacturers!
Start Your Free Subscription- Trending Articles
Automating additive manufacturing
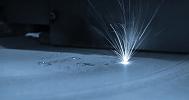
Sustainability Analyzer Tool helps users measure and reduce carbon footprint
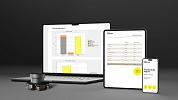
CTMA launches another round of Career-Ready program
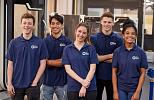
Sandvik Coromant hosts workforce development event empowering young women in manufacturing
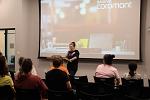
GF Machining Solutions names managing director and head of market region North and Central Americas
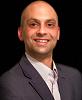
- Industry Events
MME Winnipeg
- April 30, 2024
- Winnipeg, ON Canada
CTMA Economic Uncertainty: Helping You Navigate Windsor Seminar
- April 30, 2024
- Windsor, ON Canada
CTMA Economic Uncertainty: Helping You Navigate Kitchener Seminar
- May 2, 2024
- Kitchener, ON Canada
Automate 2024
- May 6 - 9, 2024
- Chicago, IL
ANCA Open House
- May 7 - 8, 2024
- Wixom, MI