Editor
- FMA
- The Fabricator
- FABTECH
- Canadian Metalworking
Steel: The green choice
If you want something to last, metal should usually be the go-to material
- By Rob Colman
- September 6, 2022
The Intergovernmental Panel on Climate Change’s most recent report was sufficiently dire that the push to curb CO2 emissions seemed to go into hyperdrive. Plans to phase out fossil-fuel vehicles has been the most prominent example of this.
But ultimately, the conversation is much broader. The question for every major industry will be, “What processes or materials will net my project a lower CO2 footprint?” In some instances, those working in steel already are ahead of the competition.
A team of researchers at the University of Wyoming have released a report that presents the results of their study comparing two functionally equivalent, rural bridges to evaluate sustainability and life cycle cost. They found that the steel bridge outperformed its concrete counterpart across the board.
Over the bridges’ life cycles, the steel bridge will result in 26.3 per cent fewer embodied CO2e emissions, consume 8.7 per cent less energy, and lead to 17.8 per cent more recycled material (assuming the concrete is recycled) at the end of its service life—plus, the steel bridge’s life cycle cost is 23 per cent lower than that of the concrete bridge.
Michael Barker, PE, University of Wyoming’s Civil & Architectural Engineering & Construction Management program, led a team that evaluated two bridges in Whitman County, Wash. Both bridges met the two-lane rural crossing requirements and were built by the same crew. The study considered only the superstructures of these bridges to allow a direct comparison.
The Seltice-Warner bridge is a roughly 36-ft.-long, prefabricated, modular steel bridge with seven rolled beams and a corrugated gravel deck. The Thornton Depot bridge is a 34-ft.-long, prefabricated, precast, prestressed concrete girder bridge with eight beams and a concrete deck. The Whitman County, Wash. bridge crew built them within the last three years.
Researchers noted that the historical decision criteria for choosing which bridge should be built is based on first costs for installing the bridge. But the sustainability benefits may become a critical consideration in the coming years.
Metal producers and users are also looking for environmentally cleaner products and production methods. For instance, Shape Corp., Grand Haven, Mich., a Tier 1 automotive and industrial component supplier, has entered into an agreement with Hydro, a producer of aluminum and renewable energy, to bring to the U.S. market automotive components using Hydro CIRCAL recycled aluminum, which they say is expected to deliver an estimated 70 per cent CO2 reduction versus the North American average for aluminum. SSAB and Shape, meanwhile, are partnering on fossil-free steel for automotive applications. You can read more about these two projects in our August 2022 news section in the digital edition of Canadian Fabricating & Welding.
As you, our readers, know well, if you want something to last, metal should usually be the go-to material. Studies like the one mentioned, and efforts to make production processes cleaner should strengthen that message going forward.
subscribe now
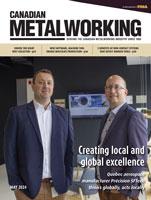
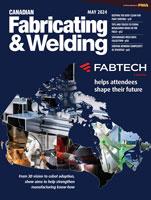
Keep up to date with the latest news, events, and technology for all things metal from our pair of monthly magazines written specifically for Canadian manufacturers!
Start Your Free SubscriptionAbout the Author
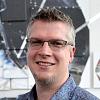
Rob Colman
1154 Warden Avenue
Toronto, M1R 0A1 Canada
905-235-0471
Robert Colman has worked as a writer and editor for more than 25 years, covering the needs of a variety of trades. He has been dedicated to the metalworking industry for the past 13 years, serving as editor for Metalworking Production & Purchasing (MP&P) and, since January 2016, the editor of Canadian Fabricating & Welding. He graduated with a B.A. degree from McGill University and a Master’s degree from UBC.
- Industry Events
Automate 2024
- May 6 - 9, 2024
- Chicago, IL
ANCA Open House
- May 7 - 8, 2024
- Wixom, MI
17th annual Joint Open House
- May 8 - 9, 2024
- Oakville and Mississauga, ON Canada
MME Saskatoon
- May 28, 2024
- Saskatoon, SK Canada
CME's Health & Safety Symposium for Manufacturers
- May 29, 2024
- Mississauga, ON Canada