Editor
- FMA
- The Fabricator
- FABTECH
- Canadian Metalworking
Building from the finished part
Your next machine investment may not be what you expect
- By Rob Colman
- June 28, 2022
Research and development continually help us view how work is done differently. Consider the change in thinking that occurred when additive manufacturing using metal powder replaced subtractive metal cutting technologies for certain products. In no way has additive replaced mills, lathes, or metal forming machinery, but it is the perfect technology for certain complex parts.
Likewise, in resin 3D printing, Harvard researchers have been working to make 3D printing a truly 3D process; instead of building a shape layer by layer, it uses blue light to polymerize resin in entire volumes at one time. While the 2D approach to this type of printing may be the best for some products, this research opens up a potentially new production method.
I was reminded of this in May while I was speaking to a shop owner who was planning a trip to FABTECH Canada. His shop had invested in a number of newer machines recently and he’d seen the positive impact those investments had on the shop. He was thinking about what was next. He said he knew what outcomes he wanted but not necessarily what the ideal machine would be for the job.
Sometimes I think that can be the hardest leap to make when looking for new machinery; if a shop has always used press brakes, considering a panel bender or folder may not come to mind automatically. If you’re used to working with a plasma table, a laser may seem foreign. Likewise, if you’ve only ever worked with lasers, a laser/punch combo machine may appear to be a stretch for the work you do. Automation in any form, of course, complicates this picture further.
It’s easy to get caught up in the minutia of a new machine setup as well. A certain job—say, part sorting—may appear to run slower than desired, but when analyzed from a broader perspective, production from raw material to final part may be faster. Brendon DiVincenzo, regional head of solutions for Bystronic Inc., probably said it best in last month’s article on part sorting: “The question is, if you put a tarp over your whole laser/sorting setup and just saw neat stacks of finished parts coming out according to your production schedule, are you still satisfied with that?”
If it’s time for the next big investment in your shop, it can help to start with a blank slate and your most common finished parts in mind. Even job shops have a certain subset of parts (or at the very least variations on them) they can confidently say they will make. Or perhaps it’s the ones that you currently can’t make that will drive the decision. Either way, those parts might lead you to surprising answers. They generally are what help companies start their automation journey. Perhaps the change will work its way even deeper into your organization.
subscribe now
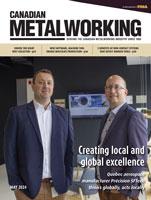
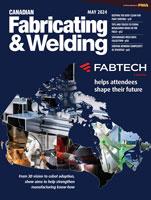
Keep up to date with the latest news, events, and technology for all things metal from our pair of monthly magazines written specifically for Canadian manufacturers!
Start Your Free SubscriptionAbout the Author
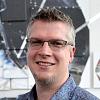
Rob Colman
1154 Warden Avenue
Toronto, M1R 0A1 Canada
905-235-0471
Robert Colman has worked as a writer and editor for more than 25 years, covering the needs of a variety of trades. He has been dedicated to the metalworking industry for the past 13 years, serving as editor for Metalworking Production & Purchasing (MP&P) and, since January 2016, the editor of Canadian Fabricating & Welding. He graduated with a B.A. degree from McGill University and a Master’s degree from UBC.
- Industry Events
Automate 2024
- May 6 - 9, 2024
- Chicago, IL
ANCA Open House
- May 7 - 8, 2024
- Wixom, MI
17th annual Joint Open House
- May 8 - 9, 2024
- Oakville and Mississauga, ON Canada
MME Saskatoon
- May 28, 2024
- Saskatoon, SK Canada
CME's Health & Safety Symposium for Manufacturers
- May 29, 2024
- Mississauga, ON Canada