Welding Applications Technologist
- FMA
- The Fabricator
- FABTECH
- Canadian Metalworking
Weld bead clarity
Understanding how autodarkening weld helmet developments can help you get the best view of your job
- By Andrew Newman
- March 31, 2022
- Article
- Welding
Managing operator safety is a critical consideration in welding operations. Welding helmets are, of course, a major safety tool. The development of autodarkening welding cartridges created a valuable aid for welders in that it made it possible to perform secondary operations around the weld without having to constantly flip up the helmet to make adjustments in their workspace. It also meant that the operator’s vision gained additional protection while doing these secondary tasks because of the base shading offered by autodarkening cartridges.
Choosing the right autodarkening helmet for your job requires understanding how optical clarity is rated and what level of sophistication you require from your helmet.
Optical Ratings
With the right autodarkening welding helmet, it’s possible to get a clearer, more precise view of the weld bead. Ensuring that you are going to get the precision you want from a helmet has been made easier with the creation of a rating system to help guide comparisons of helmet vision systems.
When looking for a new welding helmet, you will see optical class ratings listed for helmets in the following manner: 1/1/1/1. The European Standards Commission developed this EN 379 rating for autodarkening welding cartridges to measure the quality of optical clarity in the helmet lens. For this rating system, autodarkening lenses get tested and rated in four categories. Each category is rated on a scale of 1 to 3, with 1 being the best and 3 the worst.
The four numbers in the rating system measure the following:
- Optical rating (1/X/X/X): This first number determines how clear the image is. A number of lenses are sandwiched together to create cartridges, and this number determines whether the image is at all distorted or rippled – like looking through water.
- Light diffusion rating (X/1/X/X): This rating also measures clarity but relates more precisely to the sharpness of the image. In other words, are there any defects in the lenses creating blurriness in the view?
- Variations in luminous transmittance rating (X/X/1/X): This number rates the consistency of the autodarkening across the entire lens. If you have a screen of a certain size, you want to ensure that the whole lens darkens all the way; light or dark spots in your visible area can affect the ability to weld safely.
- Angular distortion rating (X/X/X/1): If you look up or down in your viewing area, are you seeing any distortion in the view? If you need to weld out of position, for instance welding around a tank, it is important to ensure your helmet has a 1 rating for angular distortion. Some welders, knowing they will always be working with welds right in front of them, choose helmets with a 2 rating for the financial savings such a helmet will bring.
Another time you might choose to go with a helmet with a 2 rating for angular distortion is if you want to adjust your shade level to DIN 3 or lower when not welding to do a lot of grinding while wearing the autodarkening helmet. The shade rating indicates the intensity of light radiation allowed to pass through a filter lens. Some more advanced helmets have ratings of between 2 and 2.5, which is valuable if you need to do finesse work around welds. It is not currently possible to get a 1/1/1/1-rated helmet with a minimum shade level less than 4.
Sensitivity and Visibility
These ratings are a key indication of how well you can view the workpiece, but there are other considerations related to the functionality of an autodarkening helmet.
The speed at which an autodarkening helmet changes is generally quite rapid – between 0.1 and 0.09 millisecond. However, the number of sensors around the helmet will affect when and how the autodarkening is triggered. Typically, less expensive helmets have one or two sensors, whereas more advanced helmets have as many as five sensors. The more sensors a helmet has, the more precise the autodarkening function is. For instance, when you are working out of position, it might be possible that one or two sensors are blocked from the light sources or are affected by a different light source. In this scenario, the other sensors help to ensure the autodarkening functions as it is designed to.
Even more advanced options are available now too. For example, some welding helmets now are equipped with Bluetooth that connects them to the power source. The helmet usesthe arc-on signal from the torch trigger to darken the helmet rather than depending on the visible light setting off the sensors. When the arc shuts off, the lens lightens again.
Another consideration is the eye strain caused by rapid switches from shade to bright light when a weld is finished. Something Fronius has introduced in its helmets is a “twilight mode”; when the arc is turned off, the lens gradually brightens so that eye strain is better managed.
A last consideration in comparing visibility among helmets is the size of the area covered by the lens. Although lens cartridges are being designed larger, it is important to test them out to ensure that visibility is as extensive as it needs to be.
Many weld helmets have optical ratings of 1/1/1/1, but it’s that rating combined with other factors like number of sensors, viewing area, and, on the most basic level, comfort that will determine the best fit for a welder.
Andrew Newman is welding applications technologist at Fronius Canada Ltd., 2875 Argentia Rd., Mississauga, Ont. L5N 8G6, 905-288-2100, newman.andrew@fronius.com, www.fronius.com.
About the Author
subscribe now
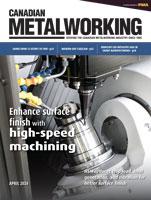
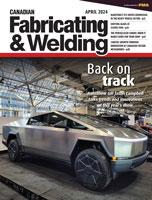
Keep up to date with the latest news, events, and technology for all things metal from our pair of monthly magazines written specifically for Canadian manufacturers!
Start Your Free Subscription- Trending Articles
Aluminum MIG welding wire upgraded with a proprietary and patented surface treatment technology
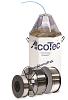
Achieving success with mechanized plasma cutting
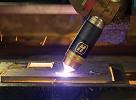
Hypertherm Associates partners with Rapyuta Robotics
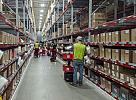
Brushless copper tubing cutter adjusts to ODs up to 2-1/8 in.
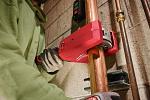
Gema welcomes controller

- Industry Events
MME Winnipeg
- April 30, 2024
- Winnipeg, ON Canada
CTMA Economic Uncertainty: Helping You Navigate Windsor Seminar
- April 30, 2024
- Windsor, ON Canada
CTMA Economic Uncertainty: Helping You Navigate Kitchener Seminar
- May 2, 2024
- Kitchener, ON Canada
Automate 2024
- May 6 - 9, 2024
- Chicago, IL
ANCA Open House
- May 7 - 8, 2024
- Wixom, MI