Founder
- FMA
- The Fabricator
- FABTECH
- Canadian Metalworking
Managing arc blow in pipe work
Demagnetization for weld management is key to avoiding this critical issue
- By Alex Palynchuk
- April 14, 2021
- Article
- Welding
Magnetic arc blow is defined as the deflection of welding filler material within the arc caused by remnant magnetic field in the pipes that results in forces around the weld pool. This sometimes is referred to as arc wander. For welders on the job, it’s important to understand how much residual magnetism can be tolerated and, if the magnetism is too high, how to manage the problem.
Magnetic Limits
Many opinions have been expressed about the maximum tolerable level of residual magnetism and how to measure it. A paper based on a study by Newport News Shipbuilding suggested that at about 40 gauss, the welding arc can become unstable and, in some cases, even arc blow out. It also suggested that 40 gauss could be tolerated if certain procedures were followed (for instance, balancing the residual magnetism level in the adjacent pipe ends). Without such procedures being used, I would suggest that the maximum allowable residual magnetism should be much lower, between 5 and 7 gauss. The less magnetism, of course, the easier it will be to weld, so the ideal is to get that level down to 0.
Studies of welding arc stability have been documented as far back as 1860, but almost all work on record has been about mitigating the effect of remnant magnetism and not on demagnetization, except for pipe.
Residual magnetism in excess of 40 gauss is not uncommon in line pipe. Figure 1 shows a 24-in. pipe being prepared for welding. The steel parts hanging from the pipe indicate the residual magnetic field that made it impractical to weld. The residual magnetism reported by the operator was 50 gauss, with the gauss meter 2 ft. from the end of the pipe; this is an unusually high level of magnetism.
There are many causes of residual magnetism in pipes, and the level can vary widely. There also doesn’t appear to be any practical way of preventing the magnetization of pipes in the normal course of pipe manufacturing, coating, and handling.
Measurements
Electronic devices based on the Hall effect principle are the most widely known technology for measuring residual magnetism. The output voltage of a Hall effect sensor is directly proportional to the magnetic field strength through it. It’s often assumed that digital devices are better than analog ones, but in pipeline magnetism measurement, they are more difficult to use.
Purpose-built magnetometers (see Figure 2) have been developed to make it easier to measure residual magnetism in the field. These gauss meters are very effective and take only minutes to train an operator to use appropriately. As a precaution, the meters should be brought toward the end of the pipe from a distance to avoid possible damage to the meter caused by a high field level of magnetism.
Managing the Magnetics
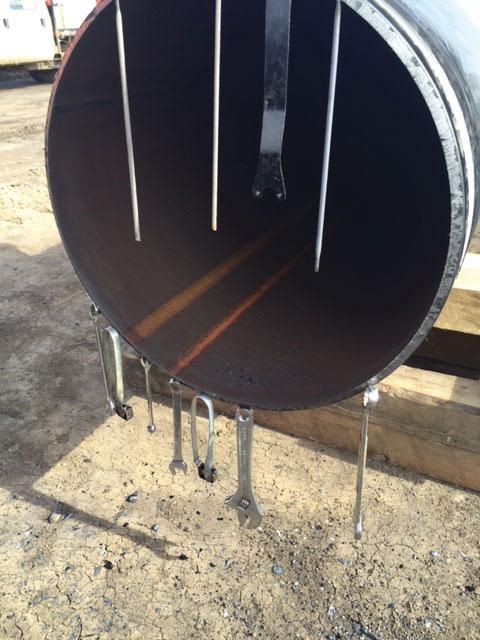
Figure 1: This is a 24-in. pipe being prepared for welding. The steel parts hanging from the pipe indicate the residual magnetic field that made it impractical to weld. The residual magnetism reported by the operator was 50 gauss, with the gauss meter 2 ft. from the end of the pipe - an unusually high level of magnetism.
If measurements suggest that it is possible to weld without further demagnetization, there are a few ways in which to manage the weld process.
One approach is to use a lower arc voltage and the lowest practical current for the joint in question. When the voltage is changed, the arc blow is counteracted by the force of the arc. Changing the welding current, of course, could require a reduction in arc speed.
Another option could be to use an alternating current (AC) for demagnetization, but this has limited application due to the “skin” effect of alternating currents (the tendency of AC to be distributed such that the current density is greatest near the surface of the conductor and decreases exponentially with greater depths). The use of appropriately pulsed direct current (DC), on the other hand, demagnetizes the entire thickness, and the pipe then stays demagnetized for an extended period of time.
Eliminating the Magnetics
With very high gauss readings, it is essential that the pipe be demagnetized rather than managed through mitigation measures. Various types of demagnetization devices are available that use either AC or DC. Studies have suggested that DC devices are better suited for large components because AC fields lack penetration to remove internal residual magnetization (as mentioned above).
It is now feasible to reduce the residual magnetism of a pipe to near zero using pulsed DC. These DC pulses not only demagnetize the ends of the pipe, but the ends stay demagnetized, typically for days. For instance, using its WDV series demagnetization equipment, Western Instruments tested a 10¾-in.-OD pipe for 10 days using a Hall effect magnetometer, and no measurable re-magnetization occurred through the full thickness of the pipe wall. This is a particularly practical outcome for pipeline work, as the pipe can be demagnetized well ahead of the welding crew. Figure 3 shows this device being used on a 16-in. pipe on a pipeline right-of-way. The WDV coils are made from 8½ to 62 in. ID, but they can demagnetize much smaller pipe than the internal diameter. For example, 25-in.-ID coil can demagnetize pipe down to about 2 in. diameter.
Operators typically can be trained in a short time to use this equipment. With the WDV equipment, it is possible to reduce the residual magnetic field in the ends of a pipe in less than a minute with as little as one pulse, with the right training.
The opportunities created by the right demagnetization process can be substantial, and with the right application can have an even greater impact. For instance, a computer-controlled unit with 16 custom coils was created to induce a specific and unique magnetization pattern. Such a system can be built to demagnetize a complete pipe in a short time, if the need arises.
In pipeline welding, where about 80 per cent of the welding cost is labour, tools that can greatly decrease labour costs and pipe weld defects can be a game-changer. Choosing the right demagnetization coils can reduce welding time, defect frequency, and repairs.
Alex Palynchuk is a member of the Canadian Petroleum Hall of Fame, CSSE, and the founder of Western Instruments, 26509 Township Road 543, Sturgeon County, Alta. T8T 1M1, 780-459-6720, alex@westerninstruments.com, www.westerninstruments.com. References available on request.
About the Author
Alex Palynchuk
26509 Township Road 543
Sturgeon County, Alberta, Canada
subscribe now
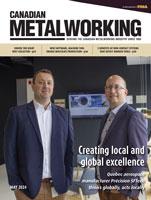
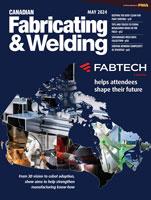
Keep up to date with the latest news, events, and technology for all things metal from our pair of monthly magazines written specifically for Canadian manufacturers!
Start Your Free Subscription- Industry Events
Automate 2024
- May 6 - 9, 2024
- Chicago, IL
ANCA Open House
- May 7 - 8, 2024
- Wixom, MI
17th annual Joint Open House
- May 8 - 9, 2024
- Oakville and Mississauga, ON Canada
MME Saskatoon
- May 28, 2024
- Saskatoon, SK Canada
CME's Health & Safety Symposium for Manufacturers
- May 29, 2024
- Mississauga, ON Canada