Manager, Environmental Systems
- FMA
- The Fabricator
- FABTECH
- Canadian Metalworking
Fume management basics
A thorough approach to a healthier shop environment includes looking at everything from materials to methods
- By Keith Daly
- December 16, 2020
- Article
- Welding
Many welding processes produce a fume plume, which contains very small, solid particles such as metal oxides. This particulate can come from a variety of sources, including the consumables, base metal, and base metal coating. Exposure to the particulate found in welding fume may be regulated by the government, which might set exposure limits for certain types of particulate.
In 2013 the American Conference of Governmental Industrial Hygienists (ACGIH) instituted a new recommendation for manganese, reducing the allowable exposure limits to respirable manganese from 0.2 mg/m3 down to 0.02 mg/m3 – a tenfold reduction. A number of smaller jurisdictions like Manitoba and the Maritimes made this recommendation law.
If you’re looking to reduce the potential exposure to manganese in your shop, you should first identify and assess your actual needs and operating conditions - what you are doing in your shop and where you are doing it.
To assess your actual needs for additional welding fume control, start by having an industrial hygienist take and analyze samples of the air in the workers’ breathing zone to give you a baseline relative to any exposure level. This is particularly important if you are welding with stainless or hardfacing products, which contain greater amounts of substances that have low exposure limits, for example, manganese.
Assessing your operating conditions includes identifying which of your fabrication processes are contributing to a potential exposure. In your review, you should consider your welding operations as well as your cutting and grinding operations. In addition, your analysis should include reviewing how your shop is laid out. This information – what you are doing and where -- will help you evaluate ways to reduce the risk of exposure.
Keep in mind that your assessment should include not only the welders, but other individuals in the shop. Fume may migrate away from the initial work area and expose others as well.
Shops should regularly review their potential exposures and their use of fume control equipment for its adequacy. Having regular refresher sessions with your workers on health and safety topics, including keeping your head out of the fumes, keeping fumes and gases away from your breathing zone, and proper training and use of fume extraction equipment, can go a long way in promoting safe practices and improving how fume control equipment is used.
Working From the Arc: Consumables
When you are doing a review of your welding operation, you can start closest to the arc by reviewing your use of welding consumables. There may be a consumable available that will generate less of a particular welding fume constituent.
For instance, if you switch your welding wire to one with a reduced manganese content, it is possible to reduce your exposure by as much as 20 per cent.
Note that you should always consult your welding engineer before changing consumables. Manganese is used to give welds a certain toughness, and your particular application may require that toughness.
Pulse Welding
Another aspect of your welding operation to consider is the type of welding process in use. Changing your welding process can make a significant difference in fume generation. For example, switching to a pulse welding waveform from a constant-voltage process may reduce your fume generation by up to 50 per cent.
The pulse waveform changes the way the welding consumable crosses the arc. Welding fume can contain metal that has been vaporized in the heat of the welding process. When the welding fume cools down, it coalesces as a metal oxide in the air. Vaporization happens from the liquid at the surface of the weld. The more surface area on that weld pool, the more metal that’s going to be vaporized. The pulse waveform keeps that pool small, which may result in both less fume and less spatter. Downstream, this helps creates other benefits in your processes. Less spatter may result in less grinding and polishing, increasing efficiency and reducing the opportunities for the creation of airborne particles.
Fume Guns
Fume extraction guns work by capturing welding fume generated by the welding operation right at the source, at the weld pool. The fume is drawn through the handle of the welding gun and through a hose into a filtration system. Used in the right application, a fume gun may remove up to 90 per cent of the fume.
Fume guns work particularly well where the fume is contained. For instance, if you are welding rebar outside, a fume gun may not be the best option because the fume is too easily blown away from the weld and can’t be properly captured by the fume gun. In comparison, if you are welding flat and the fume is contained, a fume gun may be more effective.
Fume Arms
Fume arms are fume extraction systems that can be adjusted to ensure that the welding fumes can be drawn away from the weld without entering your breathing zone.
The strength of fume arms is their flexibility, but they may not be ideal for every situation. For example, if you are working in an overhead, upward position, it may be difficult to position the fume arms so that they move the welding fume away from the breathing zone.
Overhead Extraction
Welding fume’s effects must be considered in the remainder of a shop too. While concentrations outside of the main welding area may be lower, there is still a potential for overexposure to welding fume constituents such as manganese.
One solution to consider is a low-power overhead extraction system that can draw additional fume out of the shop before it reaches other areas. Engaging an industrial hygienist to determine particulate levels throughout your shop can help clarify how such systems should be distributed.
Weld Positioners
For some weld processes, automated weld positioners help bring the weld to the welder by pivoting the assembly to accommodate a better weld position, which then helps minimize exposure to fume in the breathing zone. Like any other approach to weld fume management, this is another tool to help improve welding fume control.
Automation
With the use of welding robots it is still necessary to have a welder who understands what the robot needs to do and how it’s supposed to run to ensure an effective weld. A robot holds the torch and separates the worker from the hazards of the job – the heat, shock, flash, and fumes. It not only distances the welder from these hazards, but also allows repeatable quality.
There are essentially two types of welding automation you can choose from: flexible automation using robotic arms or hard automation. Hard automation is effective for pipe work or anywhere you are running a long, straight seam.
For instance, a manufacturer of specialized truck bodies needed to make a large toolbox for a truck. The toolbox had 5-ft.-long welded corner seams that were being welded with flux-cored wire. A switch to submerged arc welding was proposed because it was a large weld going in a straight line. Investing in this one technology meant that the amount of fume generated in the process was greatly reduced while also reducing the operator’s potential exposure to that fume.
PPE
Proper ventilation through fume extraction and other engineering controls may not be an option in every welding environment. In such cases, personal protective equipment (PPE) such as a purified air-powered respirator (PAPR) welding helmet is available and can be used to help minimize an individual welder’s exposure to welding fume. For example, PAPRs may be an effective solution when welding must be performed in enclosed or other areas where it is difficult to provide effective ventilation or otherwise control exposure to welding fume.
As an example, a large transportation equipment manufacturer was able to extract fume effectively, but had some limitations when welding large frames in a cumbersome work area with half a dozen welders.
Other Processes
While welding may be the initial fabrication process you think of when considering the potential sources of exposure in your shop, you should also review your other processes, including plasma cutting, flame cutting, grinding, and gouging. A full review of your processes is necessary to understand potential exposures, and these non-welding processes can be overlooked.
Certain types of cutting tables have fume filtration or extraction capabilities. Water tables, for instance, can filter fume produced during the cutting process. Downdraft tables can also be designed to help remove fume generated during welding, cutting, or grinding. With grinding, if you have a backdraft table and an isolated area where you can grind, that will reduce fine particles, and larger particles will drop where they can be swept up.
The health and safety of your shop should always be top of mind, a concept that is even more at the forefront of the world during a pandemic. Introducing fume extraction tools not only helps reduce overexposure to welding fume constituents like manganese, it also demonstrates to workers your commitment to their health and safety.
Keith Daly is manager, environmental systems, Lincoln Electric Canada, 179 Wicksteed Ave., Toronto, Ont. M4G 2B9, 416-421-2600, keith_daly@lincolnelectric.com, www.lincolnelectric.ca.
About the Author
subscribe now
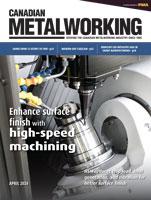
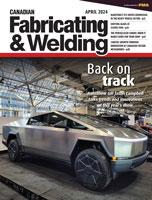
Keep up to date with the latest news, events, and technology for all things metal from our pair of monthly magazines written specifically for Canadian manufacturers!
Start Your Free Subscription- Trending Articles
Aluminum MIG welding wire upgraded with a proprietary and patented surface treatment technology
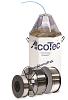
Achieving success with mechanized plasma cutting
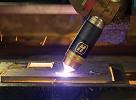
Hypertherm Associates partners with Rapyuta Robotics
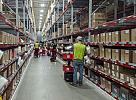
Gema welcomes controller

Brushless copper tubing cutter adjusts to ODs up to 2-1/8 in.
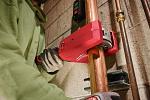
- Industry Events
MME Winnipeg
- April 30, 2024
- Winnipeg, ON Canada
CTMA Economic Uncertainty: Helping You Navigate Windsor Seminar
- April 30, 2024
- Windsor, ON Canada
CTMA Economic Uncertainty: Helping You Navigate Kitchener Seminar
- May 2, 2024
- Kitchener, ON Canada
Automate 2024
- May 6 - 9, 2024
- Chicago, IL
ANCA Open House
- May 7 - 8, 2024
- Wixom, MI