Application Development Specialist, Abrasive Systems Division
- FMA
- The Fabricator
- FABTECH
- Canadian Metalworking
Finishing stainless tube
Both tools and abrasives affect the ideal approach to effective stainless tube finishing
- By Gabi Miholics
- August 4, 2022
- Article
- Metal Finishing
Stainless steel has many properties that make it attractive for various applications, but those same properties can make it a difficult material to work with. It is easily scratched and blemished in the process of working with it, leaving it susceptible to corrosion. And, just as important, it is more expensive than carbon steel, so material cost concerns are magnified when producing stainless parts.
Customers have high finish quality expectations as well, with demands for near-mirror finishes on material that, by its very nature, will be on display as a finished product. There is little chance to cover up an error with a coating or paint.
These challenges are amplified somewhat when working in stainless steel tube, as the optimal and efficient tool options for easily working the material to a fine finish are limited.
Tool Options
Because of stainless steel’s corrosion resistance, it is an ideal material for applications where the metal’s natural lustre is desired—such as handlebars and hand railings. It also means that the tube’s OD may require a finish from a matte to a smooth, blemish-free appearance.
Achieving this requires the right tool, hand in hand with the right abrasives. Oftentimes the first question we ask customers is what type of capital investment they are willing to make to ensure the tube receives that ideal finish quickly and consistently. For those hoping to maintain a steady stream of tube finishing orders, automating the process with a centreless grinder, a cylindrical grinder, or some other kind of belt machine definitely makes it simpler to sequence a part to achieve the desired finish. It also is possible to achieve a consistently finished product from part to part.
However, there are hand-held tool options as well. Depending on the tube’s size, a file belt sander tool can be an effective way to ensure that the part geometry isn’t altered during finishing. Using the slack of the belt allows for the tube contour work without flattening it. Some belts have three contact wheels, which creates a bit more flexibility getting around the tube. Belts are available in many sizes. File belts vary from 18 to 24 in., whereas King-Boa requires 60 to 90 in. belts. Centreless and cylindrical belts can be as long as 132 in. or more, up to about 6 in. wide.
The challenge with hand-held tools is that getting the finish exactly right time and again is more of an art than a science; experienced operators can achieve great finishes using this technique, but it really takes practice. Basically, faster speeds cause more shallow scratches while slower speeds yield deeper scratches. Finding the balance for a particular job is up to the operator. There are recommended starting belt speeds based on the finish one is trying to attain.
It is important to avoid using any kind of discs or hand sanders on tube work, however. It is very difficult to achieve the desired patterns with these tools, and there is a risk of affecting the geometry and creating flat sections on the tube if the disc is pushed too firmly into the material. In the right hands, and if the goal is a polished mirror finish rather than a scratch pattern, many abrasive steps will be used, with the last step using a buffing compound or stick.
Abrasive Approaches
Choosing an abrasive requires a clear idea of what the final finish is going to be. This is easier said than done, of course; oftentimes a part is matched to an existing product using visual inspection. However, a shop’s abrasive supplier can help determine how best to step down abrasives gradually to achieve that finish.
Having a stepped process in your abrasives when working stainless to a final finish is important. Initially, you want to ensure that all blemishes and dents are removed. We want to start with the finest product possible to remove these defects; the deeper the scratches, the more work it will take to remove the scratches. Care must be taken at each subsequent step; scratches from the previous abrasive are being removed. In this way, a consistent scratch pattern on the finished product is achieved.
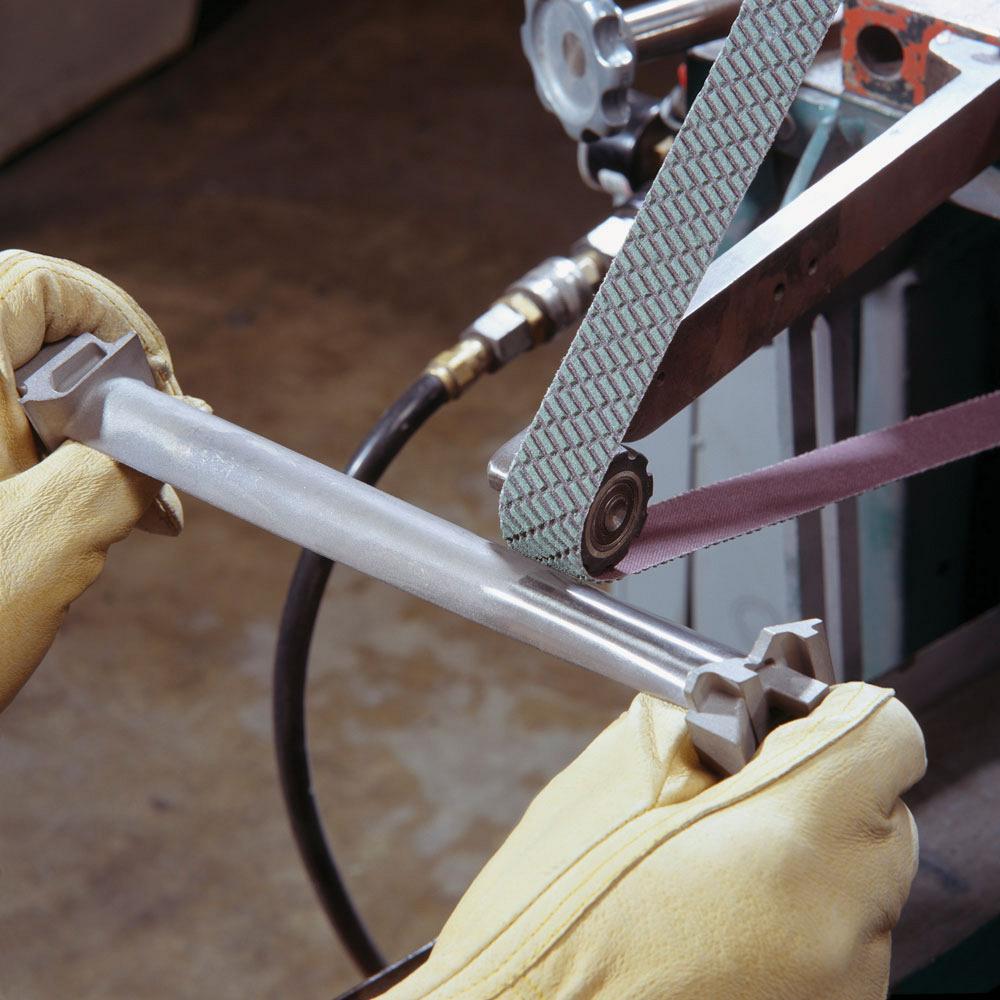
With traditional coated abrasives, it is difficult to skip an abrasive grade in achieving the right matte finish on stainless steel because of the way the abrasive breaks down. There are, however, some technologies that do allow for skipping steps, like 3M’s Trizact abrasives, which wear in such a way that the abrasive is “refreshed” with newly exposed grit as you use it. 3M
Determining how coarse of an abrasive to start with depends on the material, of course. If scale or defects like dents or deep scratches need to be removed, a heavy-grit abrasive is necessary. As an example, we’ll generally start with our 3M 984F or 947A belts. Once we’re down to an 80-grit belt, we switch to a more specialized abrasive belt.
With traditional coated abrasives, be sure to step down each abrasive grade without skipping to achieve the right matte finish on stainless steel because of the way the abrasive breaks down. Once the abrasive breaks down, more pressure is necessary to achieve the same finish as the mineral gets duller or it is removed from the abrasive. Dull minerals or higher forces will generate heat. Because heat is a concern when finishing stainless, this can affect the finish and “blue” the surface.
Another issue that can occur with some inexpensive abrasives is the consistency of its finishing minerals. Inexperienced operators will have difficulties ensuring the abrasive has achieved the required finish at each step. If there is any inconsistency, wild scratches can be made that may not get noticed until the polish stage.
There are, however, some technologies that do allow for skipping steps. For instance, 3M’s Trizact abrasives use a mix of resin and abrasive to create a pyramid structure that refreshes the abrasive surface with newly exposed grit, even as it wears down. This technology allows for a consistent finish, part to part, through the whole life of the belt. Because each grade of Trizact belt gives a predictable finish, we are able to skip grades of abrasives to our final finish. This saves time by reducing abrasive steps and reducing rework due to incomplete sanding.
The key to choosing an abrasive is determining how to get the right finish most efficiently in terms of time and cost.
Managing Heat
Because stainless is a hard material, the choice of abrasive and mineral is very important. With an unsuitable abrasive, the longer the material is worked, the more heat is generated. It’s important to use the correct mineral type and use an abrasive with a heat-dissipative coating to pull the heat away from the grinding contact area.
If using a machine, a coolant can be used on the part as well, which also helps remove debris, ensuring that scratches from that debris don’t mar the surface. Be sure that a proper filter is used so that debris doesn’t get reintroduced as the coolant is recirculated in the machine.
Defining the Final Finish
Most people think that all stainless looks the same, but when it comes down to a part’s final finish, two different mineral types can affect how that part will look. That look depends on the user.
Traditional silicon carbide, for instance, tends to leave deeper scratches, which reflect the light differently and make it look blue.
Traditional aluminum oxide, meanwhile, leaves a more rounded shape that reflects light differently and makes the material look yellow.
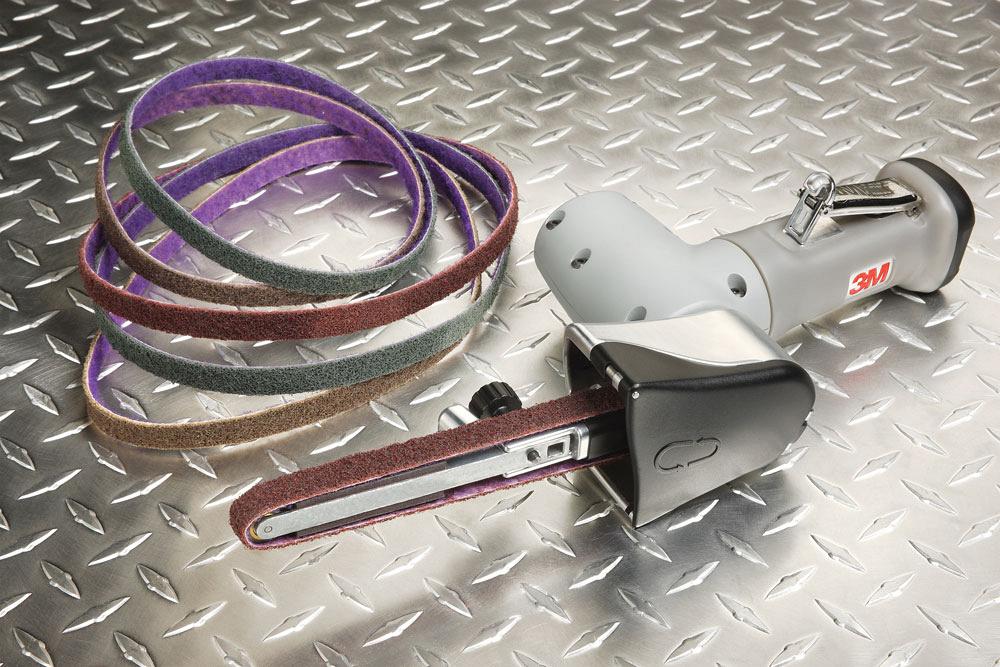
Depending on a tube’s size, a file belt sander tool can be an effective way to ensure that the part geometry isn’t altered in the finishing process. Using the slack of the belt allows for the tube contour work without flattening it. 3M
It is important to know the desired part finish because the application typically requires the new part to match an existing part.
Stainless steel is an expensive material, and it is important to choose finishing tools carefully. The right support from the supplier can help shops find an approach that is both time and cost effective.
Gabi Miholics is application development specialist, abrasive systems division, 3M Canada, 300 Tartan Dr., London, Ont. N5V 4M9, gabimiholics@mmm.com, www.3mcanada.ca.
About the Author
subscribe now
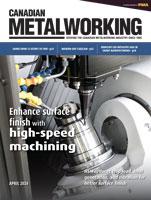
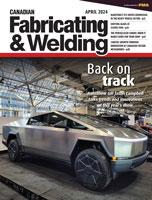
Keep up to date with the latest news, events, and technology for all things metal from our pair of monthly magazines written specifically for Canadian manufacturers!
Start Your Free Subscription- Trending Articles
Aluminum MIG welding wire upgraded with a proprietary and patented surface treatment technology
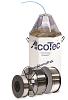
Achieving success with mechanized plasma cutting
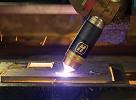
Hypertherm Associates partners with Rapyuta Robotics
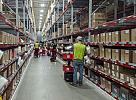
Brushless copper tubing cutter adjusts to ODs up to 2-1/8 in.
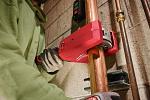
Gema welcomes controller

- Industry Events
MME Winnipeg
- April 30, 2024
- Winnipeg, ON Canada
CTMA Economic Uncertainty: Helping You Navigate Windsor Seminar
- April 30, 2024
- Windsor, ON Canada
CTMA Economic Uncertainty: Helping You Navigate Kitchener Seminar
- May 2, 2024
- Kitchener, ON Canada
Automate 2024
- May 6 - 9, 2024
- Chicago, IL
ANCA Open House
- May 7 - 8, 2024
- Wixom, MI