Associate Editor
- FMA
- The Fabricator
- FABTECH
- Canadian Metalworking
Success at Boeing Canada Winnipeg
Kathleen Garney talks aerospace fabrication and tech upgrades at BCW
- By Lindsay Luminoso
- October 17, 2022
- Article
- Fabricating
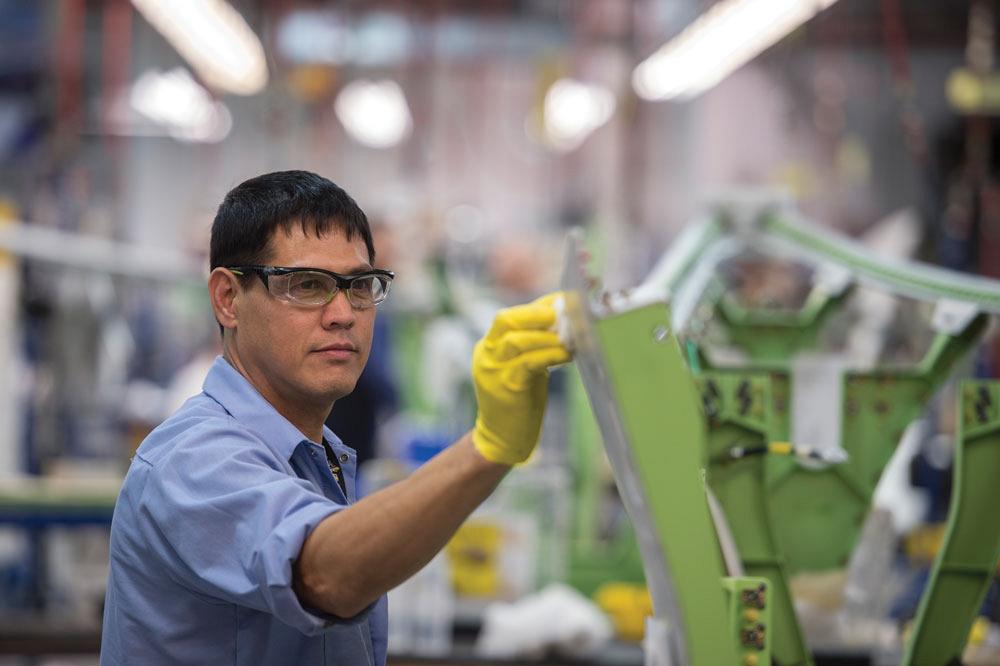
BCW’s fabrication department works with MBUs and local suppliers to purchase certain materials, like a super plastic forming titanium, and frames. It fabricates the composite panels and assembles aerospace components in-house. Boeing
In the August 2022 issue of Canadian Metalworking, Kathleen Garney, general manager, Boeing Canada Winnipeg, opened up about what she believes makes an effective leader. Now she discusses why Boeing has been successful in Winnipeg.
Check out "The path to success" from the August issue of Canadian Metalworking.
If you are seated on a Boeing 737 MAX aircraft with a window seat that allows you to look back at the wing and engine, you can catch a glimpse of a Canadian-made component. In front on the inlet is an acoustic inner barrel that has 186,000 perforations to deaden the sound of the engine. This part is extremely important for the aircraft’s use in regions like the European Union that have significant noise constraints. And it is produced at the Boeing Canada Winnipeg (BCW) facility.
Made in Canada
Boeing has had a facility in Manitoba for over 50 years. In 1969, Boeing Co. was looking to expand its fabrication and manufacturing footprint outside of its existing locations and have a more international approach. At that time, several sites were explored and the two finalists both were located in Canada.
"Do you know what differentiated Winnipeg over the other site?" asked Garney. "It was the people and the fact that there was a manufacturing workforce already present in Winnipeg."
In 1971 with an initial investment of $3.6 million, the site opened with 57 employees that were tasked with producing structural fibre glass components for the "Queen of the Skies," Boeing 747 aircraft. And while the company has grown significantly, the Murray Park facility still continues to manufacture and produce critical components that help keep Boeing aircraft in the skies.
"Our team is incredibly proud of our history and the products that we make," said Garney. "We are proud of the building that we get to make those products in, and proud of the team members that we make those products with."
Over the years there have been several expansions with significant investment. Today, BCW is the largest composite manufacturer in Canada, employing over 1,000 people across multiple disciplines including engineering, supply chain, human resources, and operations.
Aerospace Manufacturing
BCW makes many different components for Boeing commercial aircraft. In terms of the propulsion system, the facility produces the acoustic inner barrel, the engine strut aft fairing, and the engine strut forward fairing. It also produces complex doors like the nose gear door, the main landing gear door, and the shock strut door. Its parts can be found on 737, 747, 767, 777, and 787 aircraft.
"It is this product diversification that really helped stabilize BCW over the years, especially these last couple of years," said Garney.
BCW also specializes in composite manufacturing. In order to produce quality composite, the team creates a cloth in a specific configuration. These two components are then married together in layup. Once they achieve the right configuration, it is placed in one of the shop’s giant autoclaves, under both temperature and pressure specifications for a period of time, and there the composite is created. There is some rework that happens, especially machining and trimming to meet product specifications.
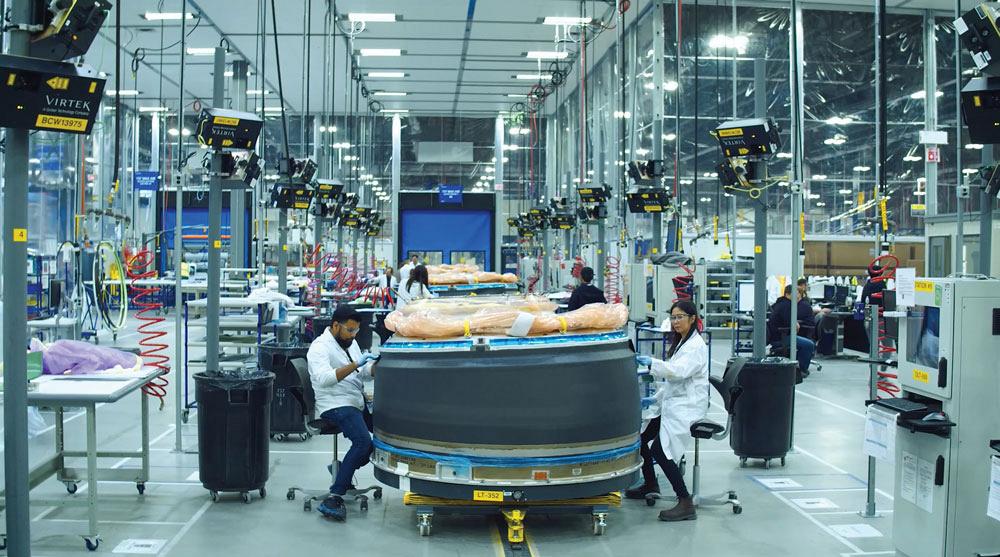
BCW produces the acoustic inner barrel, the engine strut aft fairing, and the engine strut forward fairing. It also produces the nose gear door, main landing gear door, and shock strut door. Its parts can be found on 737, 747, 767, 777, and 787 aircraft. Boeing
"Composite manufacturing relies significantly on non-destructive testing in order to determine that the product we make is conforming to the engineering requirements," said Garney. "All of our products go through non-destructive testing. Once we validate that the product is conforming, we then go into assembly, where we either marry up other composite structures or supplier purchased components that we then install. And then we can move on to paint. We do both protective and decorative paint. Once we get through all that, we’re able to ship our products to the airplane programs, whether in Puget Sound, Wash., or in Charleston, S.C."
BCW works in tandem with its sister manufacturing business units (MBUs) and helps produce products that travel across the Boeing Company network of facilities. For example, the engine strut aft fairing for the propulsion system is fabricated by BCW. However, the heat shield, a superplastic formed titanium component, is produced by another MBU, that is then shipped to BCW. From there the team purchases the metal frame from a local supplier, fabricates the composite panels, and assembles the part. That component will connect below the wing near the engine mount where exhaust from the engine requires a heat shield to limit exposure.
Collaboration and diversification of products helps keep BCW moving forward and its aircraft up in the air.
Technology Advancements
Garney explained that she approached technology in one of two ways: as an opportunity for a step-function change where new technology is adopted, or as an opportunity to adapt the facility’s existing technology to meet new needs.
"When the Boeing Co. was designing the 737 MAX, BCW was asked to develop a repeatable process with conforming results that was cost competitive and allowed the company to bring the manufacturing of its acoustic inner barrel in-house," said Garney. "The challenge was that the acoustic inner barrel has 186,000 perforations with tightly controlled locations. And up until that point BCW had not done that type of work. It was previously done by a supplier."
BCW’s solution was to create a robotic cell to perform these perforations.
"We also felt it was time to invest in simulation," said Garney. "Using cell simulation and model-based engineering practices, we developed the robotic cell and validated the process. When I reflect back on this project, it is a great example of the importance, from a leadership standpoint, of creating time and space for the teams to validate. Planning should be a significant part of the overall process. There’s absolutely nothing worse than spending money too quickly and realizing it was spent incorrectly. With proper validation we were able to create 186,000 perforations in less than four and a half hours. It was this competitive advantage that landed this work in-house."
The second technology advancement BCW undertook was in relation to its abrasion cell. Originally, an operator spent the day in the cell using a rotary grinder to prepare surfaces for paint. His or her body was used to apply force and pressure to the part, with arms raised above the head to reach certain areas. It was important to keep the rotary grinder parallel to the surface for quality control.
"Imaging doing this for eight hours, five days a week, 52 week per year," said Garney. "The wear and tear on the body can be significant. At BCW we used heat maps to identify areas of repetition and potential issues that can arise. This was a way for us to track safety and ergonomic situations. This abrasion cell had way too many instances resulting in injury, and we knew something needed to change."
A cross-functional team, including operators in the area, came together to perform problem-solving activities in an effort to find a better way to accomplish the work. The team decided to adapt a robot that had been used previously for a different task to now perform this grinding work.
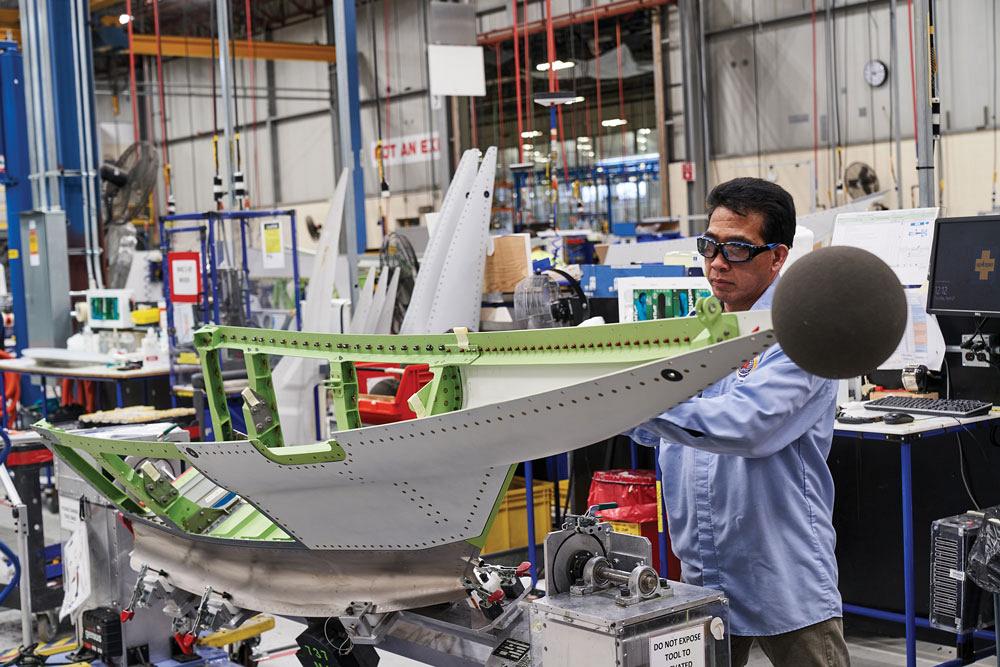
This component will eventually connect below the wing near the engine mount where exhaust from the engine requires a heat shield to limit exposure. Ian McCausland Photography
"The operators were part of that decision-making process, and they had a say in it and spoke to the fact that they didn’t want to do this repetitive work anymore," said Garney. "They much preferred being the person loading the robot, starting the robot, and turning the robot off. So we did have the necessary buy-in from the team and the consistency of the product increased, output increased, and downtime decreased. It was a win-win. I’ll say that the courage of conviction to do what’s right for both the employee and the business has to be there. We believe that people are our greatest asset and we need to treat them as such."
The company also used heat maps to identify quality issues across the shop floor. BCW identified its drilling and countersink cell as another area of opportunity for robotic use.
"We were able to redeploy those operators to more value-added tasks," said Garney. "When introducing robots to the factory floor, it’s so important to balance the needs of the workers with that of the company. Technology isn’t the only way to stay competitive, ensuring safety in the workplace is integral for staying competitive."
Safety First
Beyond technological advancements, safety has become a significant priority and the company’s understanding of safety has changed over time.
"Our understanding should always move us forward as a company and myself as a leader," said Garney. "We always need to make sure that we are creating an environment where people feel comfortable with the idea of safety and really find a way to include it within our culture. Today, safety has become our north star."
BCW has oriented everything it does towards safety. The company has created safety champions, volunteer teams, and cohorts that help push safety programs and training throughout all levels of the company.
"Even with many safety initiatives in place, people were still getting hurt," said Garney. "People were still making choices that resulted in injury. So we doubled down on training courses. In the end we still had people that were getting injured. We realized that the missing piece of the puzzle was culture."
The company began to explain how safety affects the company as a whole, particularly as it relates to being awarded new aircraft work and contracts. This was a big motivator for workers and really helped establish positive results within the safety record.
In recent years, BCW has worked with a consultant to gain a better understanding of how the company could achieve a safety-oriented work culture. Leadership focused on team buy-in by demonstrating its commitment through safety stands—a written declaration of what safety means to each individual. This allows for workers to read what leadership has in mind, but also allows them to be called out if they themselves are not following their own lead. Garney believes that it is so important to ask for help when needed and this safety initiative is something she has continued to foster in her leadership role.
For BCW, there wasn’t a magic bullet to help ensure everyone was acting and working safely. Instead, it was a series of top-down and bottom-up initiatives that helped embed safety into all aspects of the workplace culture.
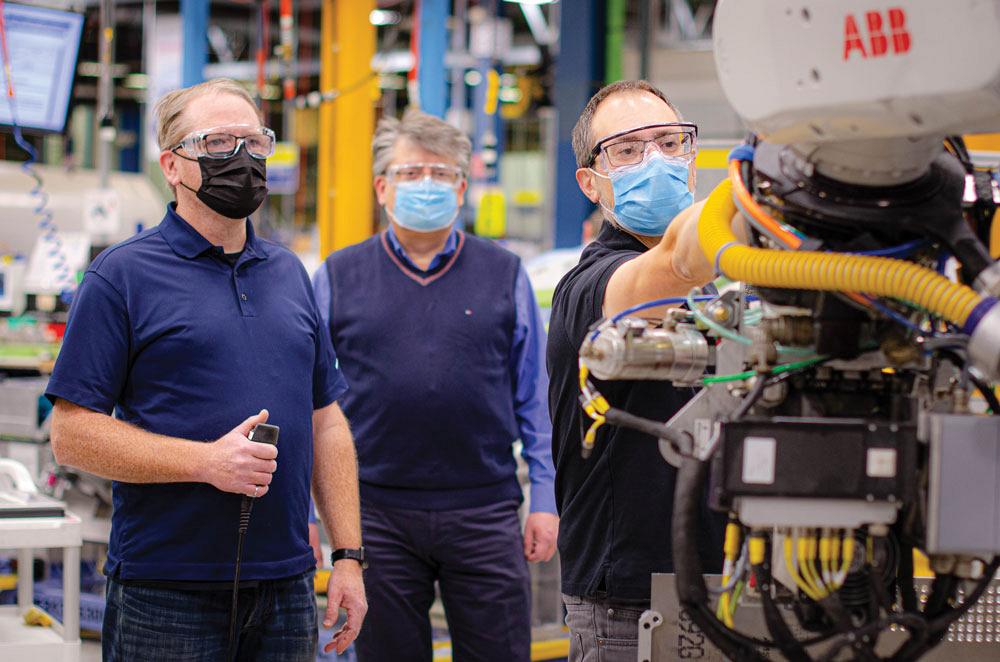
BCW has more recently invested in robotics to help boost productivity in various operations. It also created and invested in a robotic cell to perform 186,000 perforations with tightly controlled locations on an acoustic inner barrel. Boeing
At the end of 2021, the facility had reached over 2.1 million hours without a lost workday or serious injury.
"This was cause for celebration because we all did this as a team," said Garney. "We did a group recognition and gave gifts to each employee. It’s important to recognize these efforts, and we are continually finding new ways to create energy behind a culture of safety. Taking leadership and examining the various ways that we can get employee buy-in, whether from a safety perspective or adapting to new technology, has been one of the keys to our success."
Associate Editor Lindsay Luminoso can be reached at lluminoso@canadianfabweld.com.
Boeing Canada Winnipeg, www.boeing.ca
About the Author
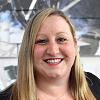
Lindsay Luminoso
1154 Warden Avenue
Toronto, M1R 0A1 Canada
Lindsay Luminoso, associate editor, contributes to both Canadian Metalworking and Canadian Fabricating & Welding. She worked as an associate editor/web editor, at Canadian Metalworking from 2014-2016 and was most recently an associate editor at Design Engineering.
Luminoso has a bachelor of arts from Carleton University, a bachelor of education from Ottawa University, and a graduate certificate in book, magazine, and digital publishing from Centennial College.
subscribe now
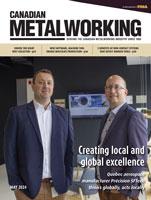
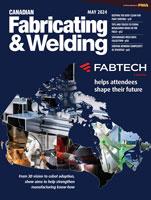
Keep up to date with the latest news, events, and technology for all things metal from our pair of monthly magazines written specifically for Canadian manufacturers!
Start Your Free Subscription- Industry Events
Automate 2024
- May 6 - 9, 2024
- Chicago, IL
ANCA Open House
- May 7 - 8, 2024
- Wixom, MI
17th annual Joint Open House
- May 8 - 9, 2024
- Oakville and Mississauga, ON Canada
MME Saskatoon
- May 28, 2024
- Saskatoon, SK Canada
CME's Health & Safety Symposium for Manufacturers
- May 29, 2024
- Mississauga, ON Canada