Applications manager
- FMA
- The Fabricator
- FABTECH
- Canadian Metalworking
Oxyfuel automation advancements
Though an old technology, oxyfuel tables with the right automation hold their own against competing methods, given the right application
- By David Binger
- April 14, 2021
- Article
- Fabricating

Oxyfuel torches can be configured for special cut profiles. This series of three torches is set up to create a K bevel in one pass.
Oxyfuel cutting is a long-established method dating back to the late 1800s. With the advent of plasma and laser cutting technologies for thinner plate and sheet metal, oxyfuel can seem like an outdated, fussy, and messy process. For the right jobs, however, it remains an ideal—and sometimes the only viable—option. And with newer automation tools, it has become an easier process to run and teach to younger operators more entranced by newer cutting technologies.
Oxyfuel Advantages
Given the appropriate application, the initial capital investment is lower for an oxyfuel system than other cutting processes. Compared to a plasma system, it requires fewer devices to support a power supply.
The operating costs for an oxyfuel table also tend to be lower. For example, if you are cutting 3-in. mild steel, an oxyfuel table will have a total cutting cost per hour (excluding labour) of around $7.04. That translates to a cost per foot of about 8 cents.
With new technology, it is possible to make your consumables last quite a long time using a moving pierce technique. If you have ever heard a popping noise when piercing plate using oxyfuel, that is an ominous sound; it means slag is entering the oxygen stream and could foul up your tip immediately. Newer tech helps avoid this issue.
Another advantage to oxyfuel is that you can add a number of torches to your table—up to 12 torches on some machines. So while oxyfuel torches run slower than plasma torches, by adding more torches you can even the playing field and, in some applications, surpass the output of a plasma torch.
Perhaps the main benefit of oxyfuel though, is its ability to cut up to 8-in. plate, while plasma torches typically pierce up to 2-in. plate. Special oxyfuel torches can be designed to cut plate as thick as 24 in.
Even when cutting such thicknesses, there is a precision to oxyfuel. The cut edge is very, very straight, virtually zero degrees. With plasma, there inevitably is some angle to the cut face.
Oxyfuel torches also can be configured for special cut profiles. For instance, if you need to put a K bevel on a part for weld prep—a bottom bevel, a flat, and a top bevel combined—an oxyfuel device can be designed with three separate torches to cut that K bevel all in one pass. A plasma torch would have to create that bevel in three passes.
Ignition and Height Sensing
Traditionally it’s necessary to ignite an oxyfuel torch manually and adjust the torch height by hand as well. This becomes a particular challenge if you have multiple torches, even if you are a skilled operator. And even if an operator is skilled enough to handle this, there’s a safety risk when the operator has to be up on top of a plate.
Today, it’s possible to get an oxyfuel table equipped with height sensing and ignition as standard. The height sensor keeps the torch at the correct height and location at all times. The flame is a combination of fuel gas and oxygen, and the preheat flame is a balance of those two gases. You then adjust the torch to achieve a cone that is not distorted to the point that it loses its efficiency. When you have your torch at the proper height, the tip of the cone will be at the top of the plate, which will provide the maximum amount of heat transfer to the material. That is important for two reasons: It reduces your high preheat cycle, and it achieves the best cut quality by having a sharp top edge. If the flame is adjusted too aggressively, it will round the top edge by melting it.
These tools can be added to existing torches, but there is a risk of molten material hitting them and affecting their function. Some height sensing and ignition systems are built internally, so they are not affected by slag or water splashed up on a water table.
Gas Flow
Another challenge that has been addressed by newer technology is the transition from the high preheat cycle to the cutting operation. With thick materials, it is easy to shoot hot slag up inside a torch when transitioning from an initial pierce to the cutting process. Some operators on old tables would pierce the plate with one set of tips, scrape the slag off the plate, put in new tips, and start cutting from the edge of those pierced holes to manage this problem.
Messer has addressed this concern with the development of its Omniflow technology. This automatically controls the fuel gas and oxygen pressures and their timing to transition from the high preheat cycle to the cutting operation. It provides a “moving pierce,” ramping up the proper oxygen pressure while running the machine at a reduced speed to ease into the cut. The purpose of this is to extend the tip life and avoid the need to have separate tips for piercing. The slag still goes up in the air, but the design ensures it goes up away from the motion of the torch.
At a time when it is challenging to attract new, young people to manufacturing, it helps to have tools in the shop that new hires will feel comfortable using. Newer oxyfuel tables can be equipped to operate in a manner that adds safety benefits that everyone in your shop will appreciate, while making it possible to save time and money on consumables and setup.
David Binger is applications manager, Messer Cutting Systems Inc., W141 N9427 Fountain Blvd., Menomonee Falls, WI 53051, 262-255-5520, sales.us@messer-cutting.com, www.messer-cutting.com.
About the Author
subscribe now
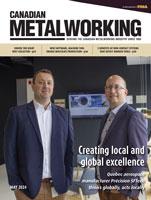
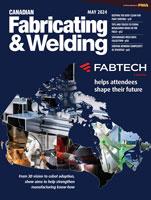
Keep up to date with the latest news, events, and technology for all things metal from our pair of monthly magazines written specifically for Canadian manufacturers!
Start Your Free Subscription- Industry Events
Automate 2024
- May 6 - 9, 2024
- Chicago, IL
ANCA Open House
- May 7 - 8, 2024
- Wixom, MI
17th annual Joint Open House
- May 8 - 9, 2024
- Oakville and Mississauga, ON Canada
MME Saskatoon
- May 28, 2024
- Saskatoon, SK Canada
CME's Health & Safety Symposium for Manufacturers
- May 29, 2024
- Mississauga, ON Canada