Editor
- FMA
- The Fabricator
- FABTECH
- Canadian Metalworking
Nature comes to life in artist Angello Glaros’ hands
Nanaimo, B.C., artist demonstrates how metal can be shaped to look lifelike
- By Rob Colman
- February 9, 2024
- Article
- Fabricating
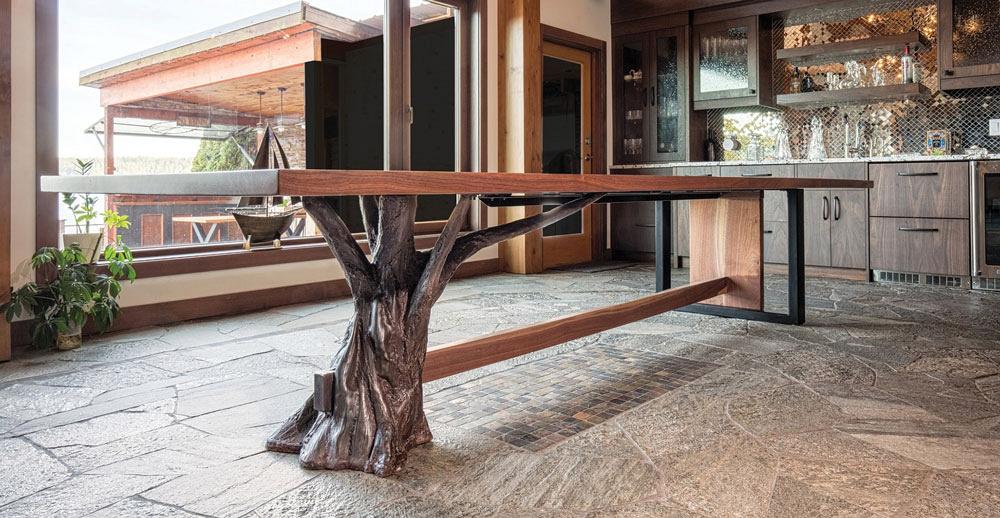
The base of this table is an example of the organic forms Glaros is able to add to furniture with his metalwork and metal finishing skills.
In November 2023, the winners of Metal Supermarkets’ annual Metal My Way contest were announced. The contest aims to showcase versatility and craftsmanship in metalworking, fabricating, and design. From among 870 international submissions, Angellos Glaros’ sculpture, “Blue Heron,” was chosen as the grand prize winner. Glaros lives and works in Nanaimo, B.C., running Glaros Studios/WestCoast Arts. Shortly after the win was announced, Canadian Fabricating & Welding spoke to him about the award-winning piece and his career.
Metal Inspiration
Glaros grew up in southern Ontario but pursued his interest in the arts at Nova Scotia College of Art and Design, where he learned to work in marble and clay.
“I think I took my first life-drawing class at about age 11, so I always knew I’d pursue the arts,” he said. After college, Glaros learned woodworking, further expanding his artistic and commercial skills.
In the late ‘90s, Glaros was building houses when an injury led him to switch to finishing work. From there he developed his woodworking business, eventually opening up his own studio in 2000. He built wooden furniture and carved representations of nature themes, such as animals, trees, and people.
It wasn’t until visiting a metal artist’s studio in about 2008 that Glaros was inspired to pursue work using mild steel.
“The artist was working on an oak tree motif, including leaves and acorns—a lot of detail,” said Glaros. “I was blown away and ran right out and got myself a welder to start learning.” He now has two welding power sources (one for the shop and one for on-site work), two plasma cutters, an anvil, power hammer, and a 6-tonne fly press to do most of his work.
Glaros still does woodwork and some marble work, but his metal artworks and the way he has incorporated metal into some of his furniture have added to his artistic range. Not only does he do private commissions, but he has done several public art installations, and several commercial jobs for pubs, schools, and the Nanaimo visitors’ centre.
“When I do my woodworking now, I usually combine it with metal somehow,” he said.
Capturing the Natural World
What stands out in several of Glaros’ works is his ability to bring a lifelike look to metalwork that is designed to appear organic. For instance, he has made railings that look like tree branches and a large shaker-style dining table base that looks like a tree stump.
“I shape the metal with a power hammer first,” explained Glaros. “With the railings, I would heat the pipe to cherry red and use the power hammer to taper the ends, which creates folds and a natural look. Once it was shaped, I basically laid down weld beads along the length of it and fill some of the folds to create the desired shape. Once that is done, I grind it, sand it, and then use a sanding flap wheel to get the textured look and the smoothness just right.”
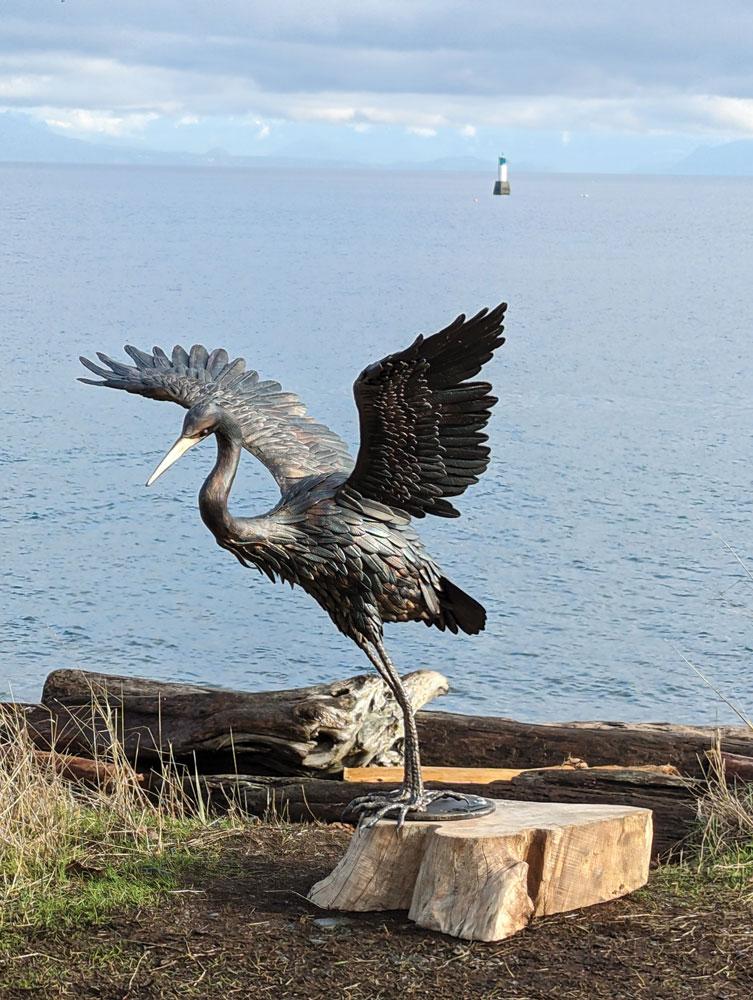
Angellos Glaros’ “Blue Heron” won the Metal My Way contest in late November. Images: Angellos Glaros
Although the texture is achieved primarily in the grinding process, the finishing process is just as important for Glaros to make sure that the pieces have the correct look and can last in the elements as long as possible.
“At that point, I do a chemical bath, spraying it until I get the colour precisely how I want it,” he explained. “I then wash it and apply an automotive finish for outdoor pieces. That helps preserve it better, and it’s the only finish I’ve found that really works effectively for the outdoors.”
Blue Heron
Glaros’ “Blue Heron” required an arduous process to create the look the artist was aiming for.
The details on the neck of the bird were achieved using a die grinder.
“It was a smooth-shaped 12-ga. mild steel pipe when I started, and I just worked it with the die grinder,” he said.
“Similarly with the feathers, I cut them out and used the die grinder to create the lines in the feathers and used a flap-wheel sander to blend it all when I’m done. At that point, I put each one on a fly press to give it a bit of a curve in whatever direction is necessary to dome it.”
Normally, Glaros would use 12-ga. plate as a base for the neck and the body. With this design, he used an armature for the body, which allowed the finish to flow around the back side of all of the feathers. For the wings, he used a basic armature at the leading edge to achieve the appearance of lightness necessary.
The feathers were the big challenge for Glaros because he had to get the finish on the backside of the layered feathers. To achieve this, he pre-treated them individually before welding to ensure they would not be affected by the elements.
“I had to hang them all up in the spray booth for six hours and watch to ensure no drips formed on the tips of the feathers,” he said. “When that was dry, I put five coats of automotive finish on it. I use a finish with which you can control the sheen on it, so that I could make it fairly flat. It would look bad if it were too shiny.” There are over 1,200 feathers on the finished sculpture, all welded on by Glaros.
The wings can be removed from the sculpture for shipping purposes. The artist created a mortise and tenon joint to insert them and a bolt mechanism to further hold them in place.
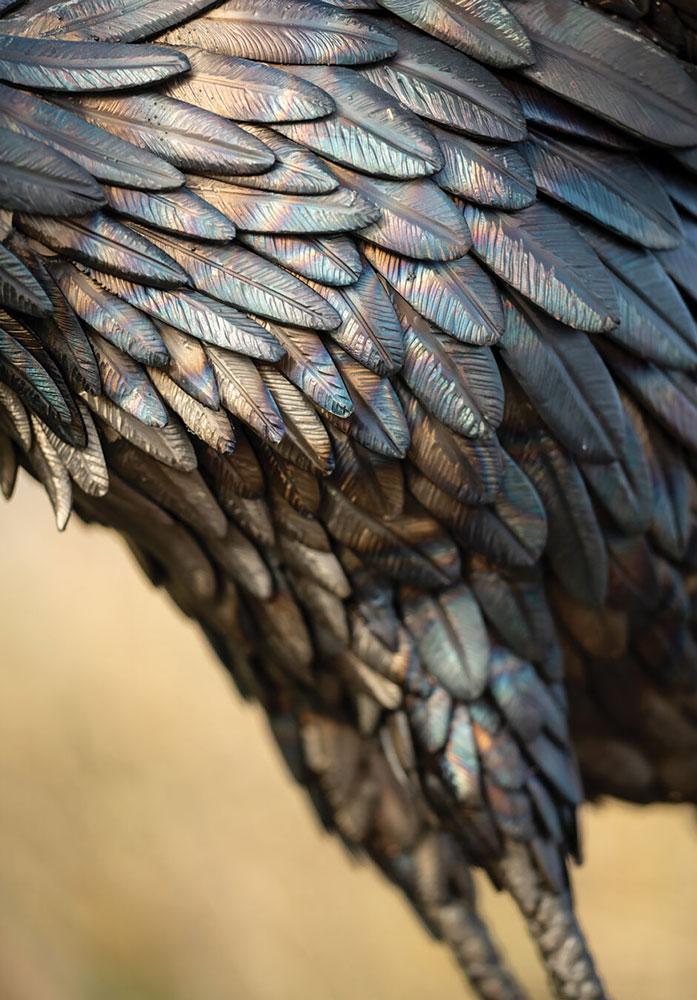
Glaros cut out each feather individually and used a die grinder to create the lines in the feathers. He then used a flap-wheel sander to blend it all together.
The texture on the legs of the bird were achieved in a similar manner as Glaros’ tree work—applying the beads along their length, in conjunction with using a hammer and chisel (and fly press) to cut in all of the ridges and fine detail. Correctly grinding and sanding also helped to achieve his desired look.
The whole bird was torched to some degree to add colour.
“For example, the beak was heated to a light red to get the final dark grey colour,” said Glaros. “The feathers used much less heat but heat was used to create the variation in colour.”
The sculpture took approximately 450 hours to complete.
Ever Growing
“Blue Heron” is, to Glaros’ estimation, the best and most complicated piece he has achieved thus far, but he feels like there is still much for him to learn.
“I have only done one metal sculpture depicting a person, so I think the human face is where I want to explore more now,” he said. “I use models for that work and do clay molds to better understand the form before I even attempt working in metal. I have a lot to learn in that area.”
What’s key is that Glaros remains undaunted in the face of new opportunities to explore.
“I’d say to anyone interested in this sort of artistic pursuit, no matter what your medium, take some life-drawing classes. Start sketching. It’s all about training your eyes to see what is there as opposed to seeing what your brain thinks is there. I often turn a face upside down, or look at it in a mirror, to see what is actually there as your brain can trick your eyes. It’s the same for furniture and any woodworking. I do my own design, and it’s all about getting the balance right. That’s the hard part of any discipline.”
Editor Robert Colman can be reached at rcolman@fmamfg.org.
Glaros Studios/WestCoast Arts, www.westcoastarts.com
Metal My Way contest winners
Both professional and amateur metalworkers alike were invited to submit a photo or video of their innovative metal-made projects for the opportunity to win prizes, including the Grand Prize (Milwaukee Tool 13-amp 1-5/8-in. Electromagnetic Drill Kit) or five secondary prizes (Husky Standard-Duty 26-in. W 6-Drawer Tool Storage Chest and Rolling Cabinet Combo). Winning submissions were chosen based on criteria such as complexity, detail, intricacy, uniqueness, creativity, craftsmanship, quantity of metal used, and ingenuity.
The full list of 2023 Metal My Way contest winners are:
- Grand Prize: Angellos Glaros, Nanaimo, B.C. – “Blue Heron”
- Best Furniture and Home Project: Noah Khoury, Altamont, N.Y. – “Forged and Fabricated Steel Doors”
- Best Knives Project: Justin Lamoureux, Winnipeg, Man. – “Wheel of Time Dagger”
- Best Industrial or Shop Project: Matthew Mitman, Bowman, S.C. – “Pneumatic Power Hammer”
- Best Vehicle Project: Tim Strochine, Cincinnati– “Airsoft Combat Vehicle”
- Best Artistic and Design Project: Steve Nielsen, Oroville, Calif. – “Polished Stainless Steel Eagle”
Alongside title sponsor Metal Supermarkets, the contest was sponsored by Airgas Inc., Cosen Saws, Ferric Machinery, Haco-Atlantic Inc., and Space Aid Mfg.
Metal Supermarkets, www.metalsupermarkets.com
About the Author
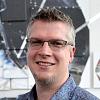
Rob Colman
1154 Warden Avenue
Toronto, M1R 0A1 Canada
905-235-0471
Robert Colman has worked as a writer and editor for more than 25 years, covering the needs of a variety of trades. He has been dedicated to the metalworking industry for the past 13 years, serving as editor for Metalworking Production & Purchasing (MP&P) and, since January 2016, the editor of Canadian Fabricating & Welding. He graduated with a B.A. degree from McGill University and a Master’s degree from UBC.
subscribe now
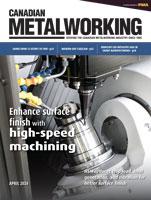
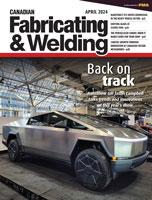
Keep up to date with the latest news, events, and technology for all things metal from our pair of monthly magazines written specifically for Canadian manufacturers!
Start Your Free Subscription- Trending Articles
Aluminum MIG welding wire upgraded with a proprietary and patented surface treatment technology
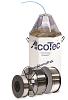
Achieving success with mechanized plasma cutting
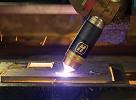
Hypertherm Associates partners with Rapyuta Robotics
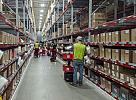
Gema welcomes controller

Brushless copper tubing cutter adjusts to ODs up to 2-1/8 in.
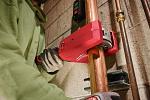
- Industry Events
MME Winnipeg
- April 30, 2024
- Winnipeg, ON Canada
CTMA Economic Uncertainty: Helping You Navigate Windsor Seminar
- April 30, 2024
- Windsor, ON Canada
CTMA Economic Uncertainty: Helping You Navigate Kitchener Seminar
- May 2, 2024
- Kitchener, ON Canada
Automate 2024
- May 6 - 9, 2024
- Chicago, IL
ANCA Open House
- May 7 - 8, 2024
- Wixom, MI