Press Brake International Sales and Design Supervisor
- FMA
- The Fabricator
- FABTECH
- Canadian Metalworking
Material marking management
Proper maintenance, attention to detail can help ensure your parts reach the pain line mark-free
- By Steve Brown
- March 22, 2023
- Article
- Fabricating
Part marking is an issue that affects almost every press brake department. It’s easy to notice marking on a part and ignore it, thinking that the die is damaged and knowing that with the cost of new tooling, you will have to work around the damaged die. Quite often, however, it is not a problem with the die at all. Understanding the following processing techniques will help you troubleshoot potential issues on the brake and develop techniques to ensure very sensitive material is properly protected.
Check Your Alignment
Today’s precision tooling needs to be properly installed and maintained to perform as it is meant to. This means ensuring that the upper and lower beam on your machine align correctly, the upper and lower beam on your holder line up, and your punches and dies line up properly.
Maintenance is critical to ensure this alignment remains precise. I was recently in a shop that had relatively new dies and a crowning system that had been installed a few weeks prior, and yet its dies weren’t lining up. I suggested they remove their dies and wipe the length of the beam, air blow the channel that the tools were sitting in, and give the tools one wipe with a rag before putting them back in. Everything matched perfectly. The alignment was off by so little that 20 years ago it would not have been an issue. But today, the precision required by clients means you must maintain your tooling precisely too.
The other problem, of course, is that improperly aligned tools will lead to the edge of your tools rounding off and failing prematurely.
Use the Correct Tools
Tooling choices change when marking concerns come into play. A shop may be used to running a number of parts on the same punch and die to help speed processing without doing changeouts. This is fine if marking isn’t a concern, but once it is an issue, it’s important to think carefully about the tonnage being produced relative to the die’s shoulder radius and V opening size. An undersized V will create tonnage. The smaller the shoulder radius, the more the material will grab on the shoulder of the die. An oversized V die will help reduce the tonnage.
V-Series black dies from Wilson Tool, which are essentially moving paddles, are another option to avoid marking. The paddles move, meaning that the material being bent is sliding on a flat into the bend rather than grabbing on a shoulder radius. This can be particularly effective when bending galvanized or coated materials, both of which can catch on any shoulder, regardless of the depth of bend. It’s important to keep the paddles and saddle clean and lubricated to maintain their effectiveness.
When lubricating the paddles, take care in choosing the correct product. Using lithium lubricant spray, for example, is not effective for paddles. It is a very effective lubricant for many home uses, such as garage doors, but keep in mind no compression is involved in these applications. It’s important to find a product that still works given the compression involved in the action of the press brake.
Another method to decrease the chance of materials grabbing on a shoulder is applying a surface treatment like Nitrex for your tools. This is a treatment that penetrates the material to a depth of approximately 0.5 mm, has a hardness of 68 to 70 RCS, and increases tool lubricity. It can help prevent buildup of material on the shoulder of the die and reduce marking.
Check Tool Conditions
It’s important to inspect dies prior to each operation. Any deformities, burrs, or chips will transfer to the material you are forming. Poorly maintained tools will result in premature tool replacement, material marking, and inconsistent bend angles.
Some die marking occurs due to residue buildup. Particularly with aluminums and galvanized material, subtle buildup of material can look like scratches on your die shoulder to the untrained eye. The galling can be removed easily. Regular cleaning can help alleviate this concern.
Tooling should be checked each shift for damage and as often as needed if galling is known to happen quickly. A wipe down of the tools at the end of a shift and when tools are put away is a simple habit that all operators should be encouraged to maintain. The reason you bought precision tooling and paid that kind of price is so you can be precise. Any buildup on your tools will affect that precision and tool life.
Remove Buildup Carefully
When you do experience buildup on your dies, be sure to remove it with the correct abrasive type, such as a very fine abrasive that won’t scratch the surface itself. Some companies offer colour-coded abrasives that can help guide operators, but it’s important to double check the grit size of any product you use to ensure it won’t damage your tools. Even with a fine abrasive pad, make sure you don’t lean into the work because too much pressure can still damage your tools. If you wait too long and get heavy buildup on your tools, it can be difficult to clean them without marring their surfaces.
Try using a lightweight oil to clean your tooling as well. A good example of this is LPS Platinum Grade 3. It will clean your dies without creating a film that will grab and hold onto particles it comes into contact with.
Be Proactive With Material Protection
There are a variety of options for protecting materials against scratching. Stainless steel is commonly going to have a PVC white or clear protective coating. But many other materials, such as galvanized, require other approaches applied to your dies.
With aluminum, you might use a urethane or cloth drape across the die. The choice of protection will depend on the thickness of the material you are working with.
With stainless steel, even with the PVC coating, it’s still important to consider your shoulder radius because the coating can stretch, rip, and leave the material at risk of marking. Increase your V opening size and shoulder radius to prevent tonnage buildup and grabbing from the shoulder radius.
If you are bending a material that is 12 ga. or heavier, a cloth drape is an effective material to use. Once you get under 12 ga., the cloth is thick enough that it can start to add to your V opening size such that you would have to increase your V opening to accommodate it. A 0.015-in. (0.38-mm) urethane drape can work for 12 ga. material and less. A 0.030-in. (0.76-mm) urethane can be effectively used 14 ga. to 10 ga. Once you get around 10 ga. and above, cloth tends to be more durable.
There is the option of using blue sky urethane, which has less elasticity than a regular urethane drape but lasts longer.
Other Considerations
There are other concerns you should consider when it comes to tool management to avoid marking parts. The first is storage. Make sure you have a system that will keep your tools free of dust and dirt.
Second, consider how other processes in your shop are affecting your parts before they get to the brake. For instance, when laser-cutting thicker material, if too much heat is transferred into an alloy that accepts the heat, this “heat-treated” part will change the qualities of the bend on the part. This can cause premature die wear and transfer into the part.
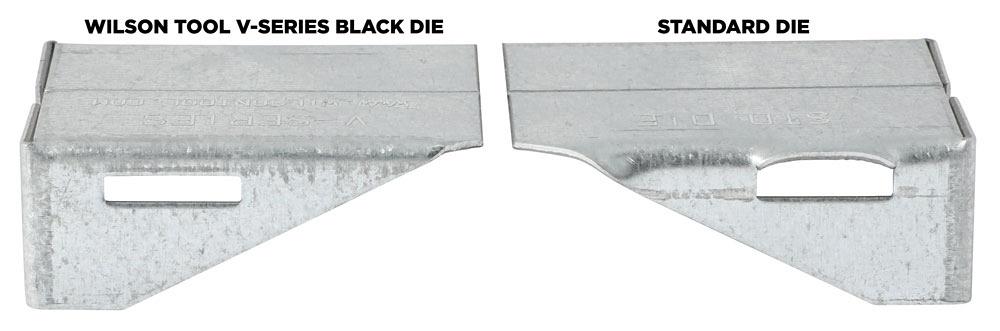
Here we see the difference between taking precautions and not taking precautions against part marking. The part on the left was bent using V-series black dies from Wilson Tool, which are essentially moving paddles, meaning that the material being bent is sliding on a flat into the bend rather than grabbing on a shoulder radius.
It is not complicated to ensure materials aren’t marked during the bending process, but it does require a consistent approach to maintenance and bending procedures for various materials. Include your brake operators in creating standardized procedures that can help reduce the number of issues that occur on the shop floor.
Steve Brown is bending product manager, Wilson Tool International, 12912 Farnham Ave., White Bear Lake, Minn. 55110, 651-286-5806, steve.brown@wilsontool.com, www.wilsontool.com.
About the Author
subscribe now
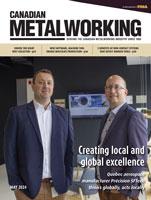
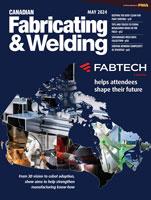
Keep up to date with the latest news, events, and technology for all things metal from our pair of monthly magazines written specifically for Canadian manufacturers!
Start Your Free Subscription- Trending Articles
Aluminum MIG welding wire upgraded with a proprietary and patented surface treatment technology
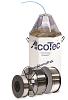
HGG Profiling Equipment BV names Western Canada area sales manager
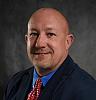
Protected and productive: welding helmet tech
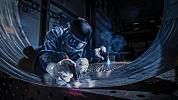
Automotive industry gets back on track
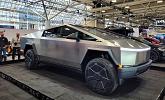
Power source added to cobot welding system for simplified automation
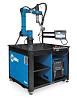
- Industry Events
Automate 2024
- May 6 - 9, 2024
- Chicago, IL
ANCA Open House
- May 7 - 8, 2024
- Wixom, MI
17th annual Joint Open House
- May 8 - 9, 2024
- Oakville and Mississauga, ON Canada
MME Saskatoon
- May 28, 2024
- Saskatoon, SK Canada
CME's Health & Safety Symposium for Manufacturers
- May 29, 2024
- Mississauga, ON Canada