Associate Editor
- FMA
- The Fabricator
- FABTECH
- Canadian Metalworking
Make cutting difficult material easy
The right saw blade can cut even hard materials
- By Lindsay Luminoso
- February 8, 2021
- Article
- Fabricating
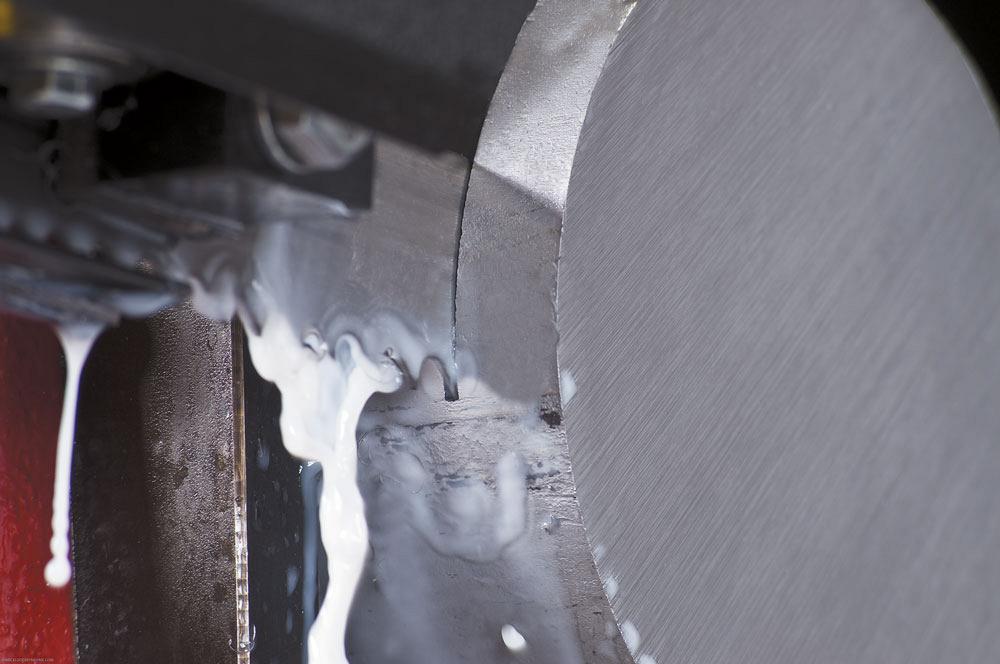
A bimetal blade that can take a little bit more force and has more durability and longevity, like the Starrett Primalloy bimetal band saw blade, is a good option because heat and wear resistance of the M-51 high-speed steel is greatly increased through alloying with cobalt and vanadium. Photo courtesy of Starrett.
In the past working with difficult-to-cut materials was not for the faint of heart. But as fabricators look to expand capabilities and take on new work, they are more likely to come across these materials that they have never worked with before, particularly nickel-based superalloys and other exotics.
"There has been an onslaught of hard-to-cut, high-nickel-content, proprietary, and different types of alloys—all which are gaining popularity in the market," said Jay Gordon, North American sales manager, saws and hand tools, The L.S. Starrett Co., Athol, Mass. "We are now seeing them across the board. At one point it was really only the big aerospace companies cutting these types of materials. Now you will see them in these big aerospace companies as well as local job shops. And I assume it’s going to continue that way."
Whether it’s a large production run or a small, one-off project, fabricators are increasingly encountering these difficult-to-cut materials in a variety of sectors.
"We are really seeing companies in different industries, like aerospace, automotive, military, marine, oil and gas, and power generation, that are cutting these materials," said Greg Winiarz, territory sales manager, saws and blades, Kasto Inc., Export, Pa. "And because the traditional way of cutting these hard materials isn’t working well, they are looking to find better ways to cut."
Gordon noted that there tends to be a general misconception that a shop can cut these difficult materials in the same way it’s been cutting all its material for however long it’s been in business. It doesn’t really work that way. Some shops think that they are already cutting hard materials when in fact they aren’t. These shops are often surprised at how difficult these high-nickel alloys, such as Waspaloy, are to cut compared to the more traditional materials and need to make adjustments in order to cut correctly.
These alloys tend to be very expensive, which means any cutting mistake could be costly, which is why some shops hesitate to expand into the difficult-to-cut materials. But with the right saw, blade, and cutting parameters, fabricators can cut with ease.
"With so many new materials available, it is impossible to provide a chart covering every size and conceivable alloy," said Lee Larson, general manager, Kalamazoo Machine Tool, Portage, Mich. "However, an operator can rely on experience working with similar materials. Leaning on good sawing principles and understanding the factors that affect a cut can help fabricators develop general guidelines as a starting point for anyone cutting hard materials."
But what about mystery materials like proprietary metals? These can present some significant challenges for operators, especially if the material composition is unknown. In many instances, cutting a proprietary metal can involve some guesswork and trial and error.
"There is nowhere in the world that has all the proprietary steels’ cutting parameters available," said Gordon.
The experts agree that with proprietary steels, guessing can be a problem, and these materials can present challenges that can be difficult to overcome. If a shop is unfamiliar with the material, a simple internet search can be a good starting point. If that yields few results, reaching out to the metal’s manufacturer is another option. For operators who are well-versed in sawing a variety of materials, the material’s makeup can give hints as to how it needs to be cut. An operator can rely on his previous experience working with a similar material and use it as a general starting point for trial and error.
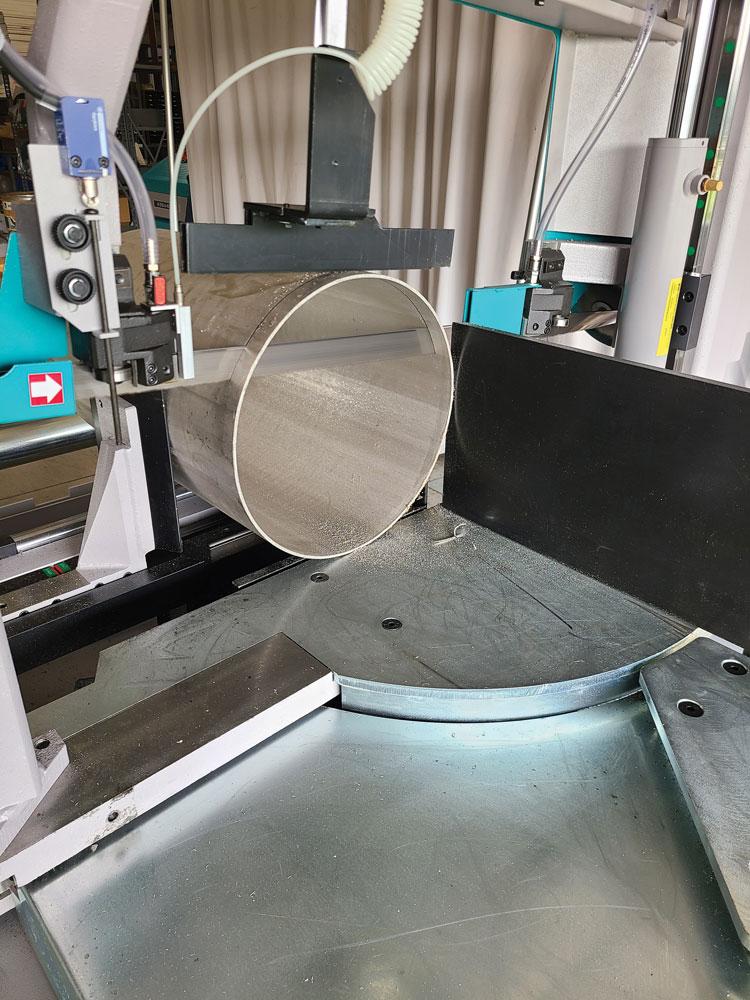
Leaning on good sawing principles and understanding the factors that affect a cut can help fabricators develop general guidelines as a starting point for cutting hard materials, said Larson. Photo courtesy of Kalamazoo Machine Tool.
The Saw
Most shops have saws that they’ve been using for years, and they can continue to use these saws when they move into hard materials, especially for on-off jobs rather than production runs. However, for shops that want to expand capabilities and move primarily into cutting hard materials, investing in a new saw might make sense.
Many different types of saw are available, including scissor-type, dual-column, vertical, and cold saws, and there is an argument to be made for each. Whichever saw a shop is working with, it’s important to ensure it offers the allowances for high-nickel alloys and hard proprietary steels.
"Some band saw blades now feature wave or ramp back technology," said Winiarz. "This allows the blade to cut through a longer cross-section of material using a wave or rocking motion with greater ease in tough material while effectively breaking up the chips. With this technology, the blade is not overforced through the material, limiting blade damage."
The condition of the saw will play a big role in cut quality. Winiarz added that shops need to make sure that on their existing saws the blade tracks properly so that it is not running on the wheels or ruining the blade set. They also should ensure that the blade guides are in good condition.
Another important thing to think about is a chip brush that cleans the chips out of the gullet so the blade can perform quality cuts. Most saws today come equipped with one; however, the brush needs to be moved out of the way when the blade is being replaced, and some shops forget or choose not to put it back in its proper position. Without a chip brush or with one that hasn’t been properly adjusted, the chips can get packed in the gullet and bond to the cutting edge of the blade. Then the chips get brought back through the cut channel, causing blade breakage as well as the potential to damage the workpiece, which in this case can be expensive.
The Blade
One big factor in getting a quality cut with hard materials such as INCONEL alloys and Waspaloy is the blade type. The experts agree that a carbide-tipped blade is the best option. Carbide-tipped band saw blades tend to be much more costly and require higher speeds. But they are not the only option.
"If a shop only needs to cut one or two pieces, then a bimetal blade could work, but a carbide-tipped blade should be used for any sort of production work," said Gordon. "When you get into the carbide tip, there’s a lot of different requirements with regards to the saws being used."
For shops that want to stick with a bimetal blade, Winiarz said that they should choose a higher-quality bimetal blade that has a harder cutting edge than the standard options.
"A standard bimetal would be an M42 saw blade," he added. "Then you have an M51 or M71 cutting edge of the bimetal blade that can take a little bit more force and has a little bit more durability and longevity. That’s an option. But a carbide-tip saw blade or a coated carbide blade is a better option. It all depends on the type of material you’re cutting."
The experts also noted that shops need to consider the size and shape of the material, hardness of the material, variety of materials being cut, quantity of cuts, and if it needs to be a mitre cut or a straight cut. Regardless of what blade a shop is working with, there are a few things that will make cutting more effective.
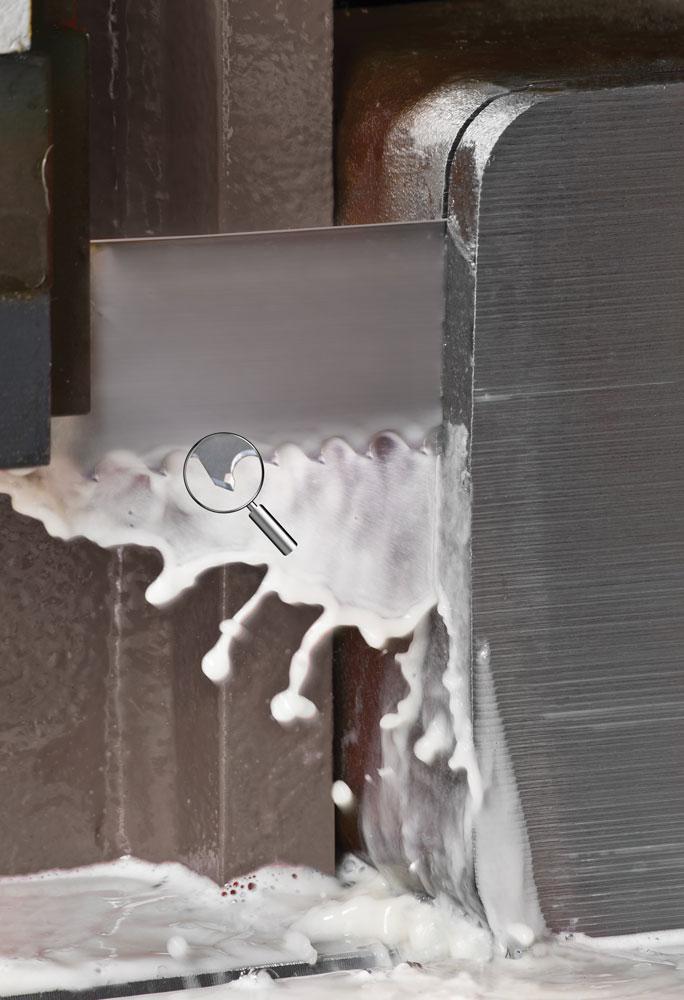
The experts agree that a carbide tipped blade generally is the best option for cutting hard materials. Starrett Advanz MC7 carbide-tipped band saw blades offer high productivity and longer life when cutting these metals. Photo courtesy of Starrett.
"You can put a carbide blade on almost any saw," said Gordon. "But if you really want it to work properly, the saw should be set up for a carbide blade in order to minimize vibrations. This will allow the operator to cut these hard materials at a decent rate throughout."
Gordon added that the wider the blade, the better the beam strength. The bigger the blade, typically the better control and availability of more feed pressure and feed rate. Shops really need a good amount of control to cut these expensive and hard materials.
The Right Cut
Many factors and features go into making a good cut in difficult materials. Ensuring the saw is in good working order and having the correct blade are two important ones, but a shop should also focus on getting the correct speeds and feeds, proper chip extraction, and coolant to obtain a quality cut.
"With the hard-to-cut materials, it’s so important to know your blade speed, feed rate, and feed pressure," said Gordon. "Those are your main factors. Then you throw in the tooth pattern and the tooth design, and whether it’s a bimetal or carbide-tipped blade. Then the last thing that you really have to throw in is coolant, which is very important."
Speeds and Feeds. For cutting a standard material, plenty of feed and speed charts are available. However, that’s not always the case for hard-to-cut materials, and it’s especially difficult for those proprietary metals. The experts said that comparing the challenging material to one that a shop already has worked with is a good starting point.
"I would just really start with a baseline of speeds when cutting these materials," said Winiarz. "For example, start with 100 surface feet per minute and 1-sq.-in.-per-minute removal rate, and from there see how the cut looks and sounds and the condition of the chips. If everything looks good, then you can continue on or make the appropriate speed and feed adjustments to get the right condition. If not, then maybe look at the blade and see if it can be upgraded, especially from a bimetal to a carbide."
When it comes to trial and error, it’s important to note that many shops think they have worked with hard materials before and use previous projects as a starting point. Often they are surprised at how much harder these difficult-to-cut materials are than what they are used to. Shops need to keep this in mind when determining a starting point.
"When the blade cuts through difficult-to-cut materials, the teeth generate heat as they remove the material," said Larson. "Slowing the blade speed reduces the heat, but the cutting rate is too slow to be economical in a production application. If the blade speed is too fast, the heat generated leads to premature dulling of the tool. While coolant and the correct tooth pitch are important factors, finding the correct blade speed is essential for difficult materials."
The blade speed, feed rate, and feed pressure are so important to get right because scrapping an expensive part is the last thing any shop wants to do.
Chips. During trial and error, the chips will tell an operator how effective the cutting parameters are. And there are some signs that all operators should look for.
"As far as the chip quality, it should have a nice curl coming out," said Winiarz. "You definitely don’t want a tight curl but rather something thin, curly, and springy. If the chips come out with a light grey or silver colour, then you’re in the right ballpark. But if they come out blue, it means that you’re creating too much heat or you’re cutting too fast. If the chip is just coming off kind of straight, you’re not putting enough pressure. If it’s coming off grainy, then you need to be increasing your feed rates and slow down the speed. But on the other end of the spectrum, if they’re coming out black or a dark blue and like a really tight curl, that means you’re probably overfeeding."
Chips also can be detrimental to the cutting process if they are not extracted correctly.
"The chips produced during the cutting process must be extracted at the correct rate or they might stick in the gullets of the teeth," said Larson. "This results in a loss of cutting efficiency, which in turn increases heat buildup, causing galling as well as shortened blade life."
Coolant. Because of the extensive amount of heat generated when sawing difficult-to-cut materials, using the proper concentration and amount of coolant is necessary for a quality cut. Coolant is used for both lubrication and cooling.
"Some shops run dry, they don’t use the right coolant, or they just run water," said Winiarz. "This is a big mistake. Not having the right lubricant on the saw blade when cutting these materials can lead to the tool heating up and burning at a much faster rate."
Coolant is important to cool the blade and workpiece, but it also works with the chip brush to provide the necessary chip evacuation. As Larson noted, having the chips removed at the correct rate will help ensure the blade remains in good working order and the cut quality remains high. The key to coolant success is applying a high-quality cutting fluid with the correct mixture, opting for flood coolant if possible, to provide the necessary lubricity for the chips and to cool the cut.
Associate Editor Lindsay Luminoso can be reached at lluminoso@canadianfabweld.com.
Kalamazoo Machine Tool, kmtsaw.com
Kasto Inc., www.kasto.com
The L.S. Starrett Company, www.starrett.com
About the Author
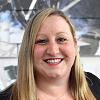
Lindsay Luminoso
1154 Warden Avenue
Toronto, M1R 0A1 Canada
Lindsay Luminoso, associate editor, contributes to both Canadian Metalworking and Canadian Fabricating & Welding. She worked as an associate editor/web editor, at Canadian Metalworking from 2014-2016 and was most recently an associate editor at Design Engineering.
Luminoso has a bachelor of arts from Carleton University, a bachelor of education from Ottawa University, and a graduate certificate in book, magazine, and digital publishing from Centennial College.
Related Companies
subscribe now
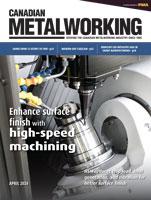
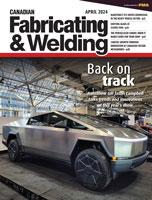
Keep up to date with the latest news, events, and technology for all things metal from our pair of monthly magazines written specifically for Canadian manufacturers!
Start Your Free Subscription- Trending Articles
Aluminum MIG welding wire upgraded with a proprietary and patented surface treatment technology
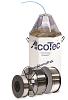
Achieving success with mechanized plasma cutting
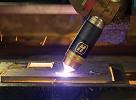
Hypertherm Associates partners with Rapyuta Robotics
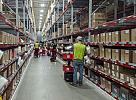
Gema welcomes controller

Brushless copper tubing cutter adjusts to ODs up to 2-1/8 in.
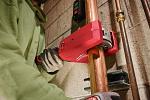
- Industry Events
MME Winnipeg
- April 30, 2024
- Winnipeg, ON Canada
CTMA Economic Uncertainty: Helping You Navigate Windsor Seminar
- April 30, 2024
- Windsor, ON Canada
CTMA Economic Uncertainty: Helping You Navigate Kitchener Seminar
- May 2, 2024
- Kitchener, ON Canada
Automate 2024
- May 6 - 9, 2024
- Chicago, IL
ANCA Open House
- May 7 - 8, 2024
- Wixom, MI