Associate Editor
- FMA
- The Fabricator
- FABTECH
- Canadian Metalworking
Fractal Fabrication gets back to basics
Alberta shop focuses on traditional fabrication skills to boost its architectural fab business
- By Lindsay Luminoso
- April 3, 2024
- Article
- Fabricating
Randy Mullin is a third-generation fabricator. He got his start in sheet metal fabricating at his father’s shop, just as his father had done. Mullin recognizes that his passion and dedication to manufacturing is written in his DNA.
After several years working in his father’s shop, Mullin moved on to work at other fabricating companies in central Alberta. Seeing the successes and struggles of local shops in the area paired with his 20 years of experience helped propel Mullin to start his own custom fabricating shop in 2017.
“I started out wanting to do things differently,” said Mullin, owner, Fractal Fabrication, Red Deer, Alta. “I was tired of doing everything the same way all the time. I didn't want a company where it was so specialized that workers only ever worked on one thing and could never do anything else. I wanted to develop well-rounded tradesmen, which we really aren’t seeing a lot of anymore. I wanted to build a shop where everybody could learn how to manufacture all different kinds of stuff in creative ways. That was really the motivation in starting the company.”
Today, the 2,000-sq.-ft. shop employs seven people and is focused on taking on odd-ball jobs—the kind of work that no other shop in the area wants to do. It’s a lot of trial based on experience, but Mullin said it makes for good business that way. While the shop is open to taking on projects in a range of industries, its strengths rest in commercial kitchens, HVAC, agriculture, signage, automotive and fleet, and architectural manufacturing.
Shop Capabilities
Mullin’s vision was to develop a shop that mixed classic heritage equipment and skills with the ability to perform repeatable tasks faster through CNC and CAD applications. His unique approach is an attempt to not only create a better, more creative workforce, but also to produce products in the best way possible.
While the shop has a variety of modern machines, including a CNC router and CNC press brake, what really excites Mullin is working with the manual leaf brakes, hand rotary machines and antiques like Brown & Boggs equipment.
“All of our work is on the lighter materials and projects,” said Mullin. “We don’t get into the heavy stuff, which is why light-gauge equipment works for us, but we do still need that high accuracy at lighter gauges. We work with a lot of aluminum, which is why a router made more sense than a plasma or laser machine. It gives us the unique capability to not cut all the way through materials, so we could do a little more creative stuff that way.”
The traditional manual equipment also has allowed the shop to build its own plasma table. Mullin decided to do this because the company’s inability to CNC cut steel was a huge limitation that kept coming up.
Taking On Unique Projects
“We do weird,” said Mullin. “And it’s great. If a customer has a weird or random project that a lot of other shops won't take or even look at, that's where we come into play.”
For example, the shop recently built three grappling hooks for a customer looking to do hoist work. It also built ostrich wrangling hooks for a customer with an ostrich farm. These cool, albeit strange, projects have allowed the shop’s craftsmen to showcase their creativity and problem-solving skills.
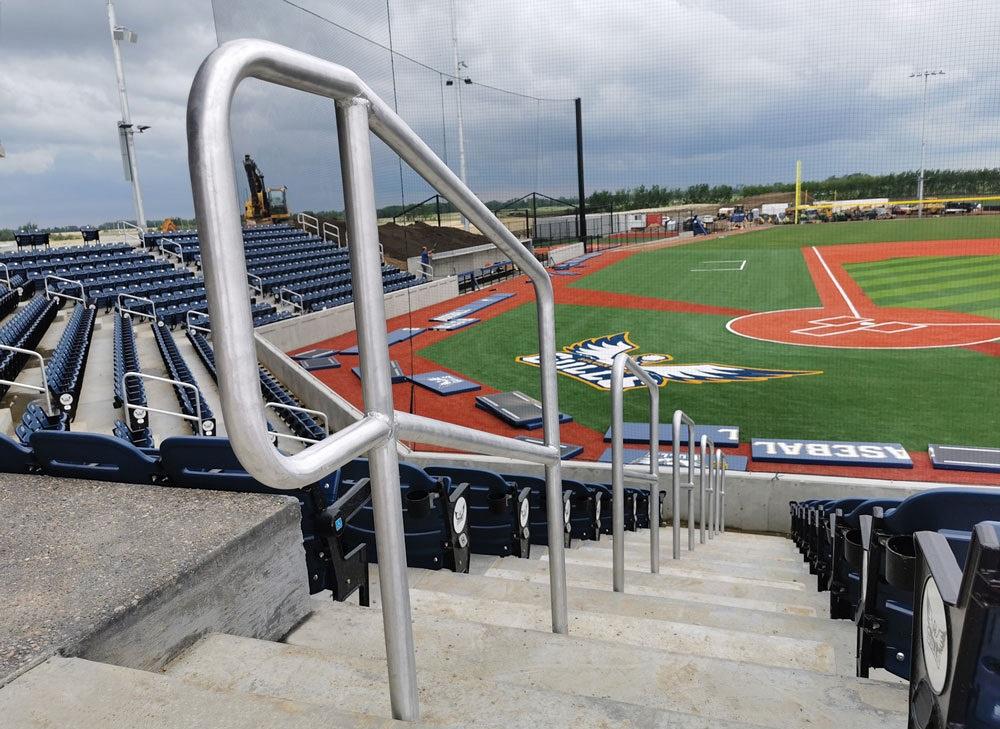
One of the cool projects the company worked on was creating polished aluminum handrails for the Sylvan Lake baseball stadium.
Currently, the shop is working on a custom wheelchair project. The customer, who had tried many different wheelchair manufacturers, came to Fractal looking for a wheelchair back that suited her daughter’s needs.
“She came to us looking for something to be comfortable for her daughter's wheelchair when nobody else could do it,” said Mullin. “These are the type of projects we love. We do anything and everything metal, that has kind always been our slogan. And we are willing to take on anything. We are transparent with the customer and tell them that we can try, and most often they are willing. There are some losses there for sure. But that’s what makes it fun.”
Since branching out with the CNC router, the company has been able to expand capabilities to include mixed media, like aluminum composite material (ACM), wood, and plastics.
“Moving into this space has been particularly helpful for us and our customers because there was just one company that was cutting these types of materials,” said Mullin. “It puts some competitive advantage back into the market that was controlled for so long by just one company around here.”
When Mullin first started the company, his focus was on producing signs for companies. With this, he has always been interested in working with many different materials.
“The coolest-looking signs are the ones with many mixed elements,” he said. “We deal with a few sign companies in town and are able to offer them the whole sign for their projects with using different materials. Instead of them having to go to six different companies, now they can come here and get everything in one stop.”
Architectural Work
While the shop does a lot of custom fabrication work, Mullin quickly noticed that there was little to no competition in the architectural space.
“For the most part, the heavy welding shops didn't want to do the light, detailed architectural work like brackets for the outside of a strip mall,” said Mullin. “They don't want to go outside the big heavy steel because they bill by poundage, so it makes more sense to do all the big stuff, and to heck with the rest. Sheet metal shops didn’t typically get into anything other than duct work. There's this gap in between that nobody was really filling.”
That’s where Fractal came in. The company was able to blend that light-gauge welding and decorative wrought iron brackets production with custom work like chimney chase covers made out of light-gauge sheet metal.
“There are challenges in it for sure,” said Mullin. “Like many apprentices or journeymen, you never really learn the skills needed for that more artistic work in school or in an apprenticeship. For us, it’s all about taking a project piece by piece and figuring out how to solve whatever we're trying to overcome with relying on similar issues that have come up previously to make good process decisions. It takes a lot more on-your-feet thinking when approaching these projects.”
A recent project involved fabricating architectural brackets for a strip mall. The building had just two bars that came up from the face of the building to meet the overhang of the eavestrough. However, the building walls were sloped from the center outward, and the roof was sloped in the opposite direction. The two bars with plates welded on either side had matching odd compound angles in two directions. Each one needed to maintain a certain angle on the bars, which needed to be level.
“Measuring for something like that is a whole day project on its own, which was really interesting,” said Mullin. “It took a little bit of brain power to get it figured out for sure. We learned triangulation for layout, which is what we use to measure it. It's all about taking skills that you learn and figuring out a new way to apply them.”
Many customers request stainless for anything outdoors, but the shop tends to favor aluminum over steel.
“People don't really think of aluminum for a lot of these outdoor projects,” said Mullin. “They want steel because it’s less expensive. But, if it’s for outdoors, we have to take the steel and put a galvanizing coating on it before colouring, and that brings it up to the same price as using aluminum anyway.”
Architectural projects don’t usually deal with structural loads, so that makes aluminum a good option. And the advantage with aluminum is that it tends to be much easier to install due to its lighter weight, meaning that the installers don’t need a hoist or other equipment to lift it.
Challenges and Opportunities Ahead
Fractal Fabrication has weeded out some soft spots, including discontinuing a mudflap that it had been producing for trucks across Canada. With the increased cost of materials during the pandemic, it made it almost impossible to compete with offshore purchases and resold products.
“We now are looking for different streams to supplement the labour for workers in what we lost with that one discontinuation,” said Mullin. “A locally, Canadian-made option is no longer fiscally viable for our wholesalers. So now we're looking to branch out again and find different things, particularly in the automotive aftermarket sector, fancy-built custom work, and pursuing more on the architectural side.”
However, Mullin noted that construction in the region is limited, making it more difficult to find work in that architectural space as fewer strip malls are being developed.
“We are always looking to fill a gap right now in servicing other shops with the CNC equipment,” he said. “There is a massive gap right now between new shops starting out and established shops that already have full CNC capabilities. It's really hard for a small guy to compete. We're looking to develop a low-cost, medium-accuracy CNC cutting option, either plasma or router. We just finished developing our CNC plasma table, and once we get a few more kinks worked out and get it a little more retail ready, we'll be looking to try and push those out there. When I was starting out, I really saw how difficult it was. With this product development, I wanted to find a way to make it easier for people like me to get started in this industry.”
Associate Editor Lindsay Luminoso can be reached at lluminoso@fmamfg.org.
Fractal Fabrication, fractalfabrication.com
About the Author
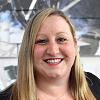
Lindsay Luminoso
1154 Warden Avenue
Toronto, M1R 0A1 Canada
Lindsay Luminoso, associate editor, contributes to both Canadian Metalworking and Canadian Fabricating & Welding. She worked as an associate editor/web editor, at Canadian Metalworking from 2014-2016 and was most recently an associate editor at Design Engineering.
Luminoso has a bachelor of arts from Carleton University, a bachelor of education from Ottawa University, and a graduate certificate in book, magazine, and digital publishing from Centennial College.
subscribe now
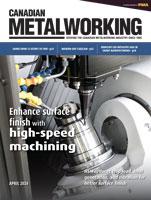
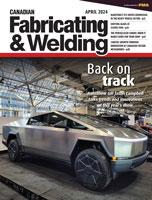
Keep up to date with the latest news, events, and technology for all things metal from our pair of monthly magazines written specifically for Canadian manufacturers!
Start Your Free Subscription- Trending Articles
Aluminum MIG welding wire upgraded with a proprietary and patented surface treatment technology
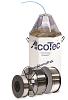
Achieving success with mechanized plasma cutting
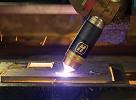
Hypertherm Associates partners with Rapyuta Robotics
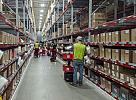
Gema welcomes controller

Brushless copper tubing cutter adjusts to ODs up to 2-1/8 in.
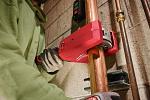
- Industry Events
MME Winnipeg
- April 30, 2024
- Winnipeg, ON Canada
CTMA Economic Uncertainty: Helping You Navigate Windsor Seminar
- April 30, 2024
- Windsor, ON Canada
CTMA Economic Uncertainty: Helping You Navigate Kitchener Seminar
- May 2, 2024
- Kitchener, ON Canada
Automate 2024
- May 6 - 9, 2024
- Chicago, IL
ANCA Open House
- May 7 - 8, 2024
- Wixom, MI