Associate Editor
- FMA
- The Fabricator
- FABTECH
- Canadian Metalworking
Fab Rite keeps on rolling
New plate rolling machine with CNC ups B.C. fab shop's productivity
- By Lindsay Luminoso
- December 29, 2020
- Article
- Fabricating
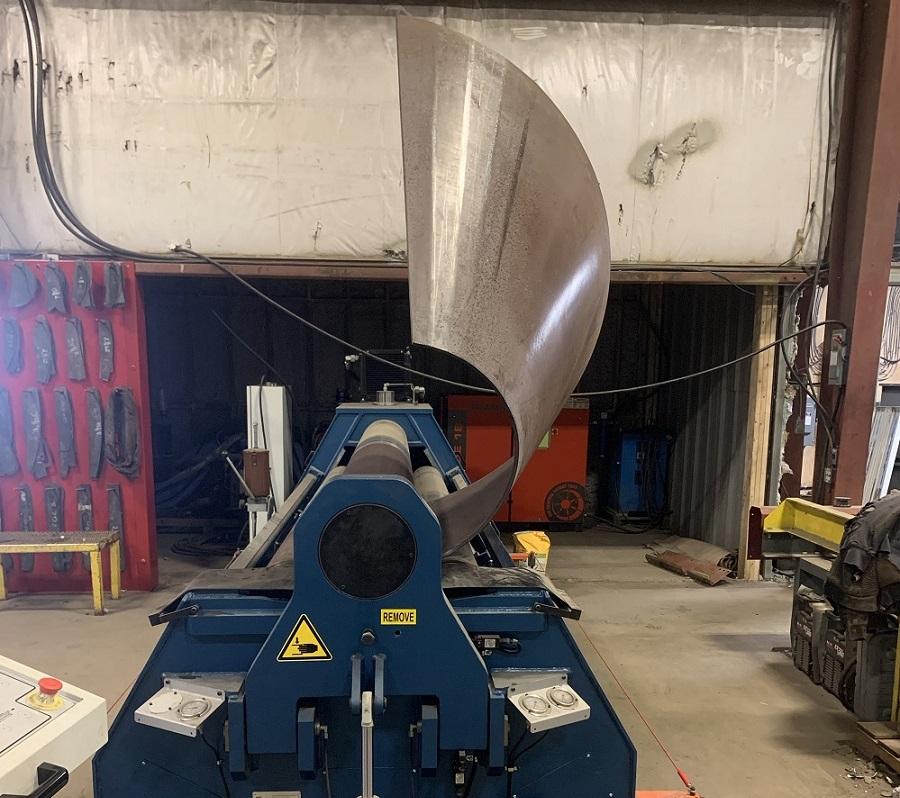
The shop says the Faccin plate roller has been a game-changer by taken a lot of the preprocessing work out of the equation and allowing it to compete more broadly by driving down the cost per.
Fab Rite Services has spent the greater part of the last decade trying to keep up with the latest technology. Each year the Cranbrook, B.C.-based shop has invested more and more in new equipment to help it stay competitive while expanding its reach across the West Coast.
In 1982 Mike Kozinuk, along with four others, founded the company, specializing in fabricating contracts for the mining industry. Today Kozinuk owns the shop. As it grew in size, the shop also adapted to changing market conditions, expanding into forestry equipment, structural steel, and miscellaneous steel fabrication. The bulk of its work today is still heavily in the mining and structural steel markets.
The company has around 67,000 sq. ft. of floor space and employs about 100 people across two B.C. locations; the Cranbrook shop is dedicated to fabrication activities and is approximately 57,000 sq. ft., while the Sparwood shop is 10,000 sq. ft. and focused on repairs, particularly of mining and truck boxes.
Fab Shop
To meet the needs of its customers, Fab Rite is focused on getting the right equipment and currently runs plasma tables, press brakes, saws, and sandblasting and paint booths. It also has a hydraulic machine shop.
"We’ve spent a lot of time investing in new CNC equipment," said President Mike Kozinuk. "We have also added more automation. It’s our quality, speed, and ability to adapt to different products that give us an edge. We are a job shop, so we just don’t do one product. We’ve had to reinvent ourselves over the years and cater to a number of different industries, from mining to forestry to construction and back to mining. We’ve also reinvested in our machines a lot over the years, which has allowed us to expand into markets further away. Today we are able to ship all over Western Canada and into the United States. And it’s really the new machinery that is helping make us more competitive. It was getting tougher and tougher without automation."
This is why Kozinuk decided to upgrade the shop’s existing plate rolling equipment. About a year ago he started his search and decided on a Faccin 4HEL 4-roll plate roller with CNC.
"We had an old set of rolls, but we really wanted to get CNC-operated rolls," said Kozinuk. "We still have the old rolls, but the new roll technology makes it so much easier to operate."
Plate Roller
Fab Rite shopped around with different manufacturers to see what the best option was. Kozinuk explained that they weren’t necessarily looking for the cheapest model but something that would give the shop the best bang for its buck. In the past the shop had decided to go with the cheapest equipment available and that didn’t always serve it well.
In late 2019 Kozinuk purchased its new 4-roll plate rolling machine through All Fabrication Machinery, Calgary.
"Faccin really specializes in rolls and we really noticed the quality," said Greg Brass, Cranbrook shop manager. "There were other manufacturers that we looked at, but we weren’t sure they would last on our shop floor. With the Faccin plate roller, we have confidence that in 20 years from now it will still be in the same condition if we look after it."
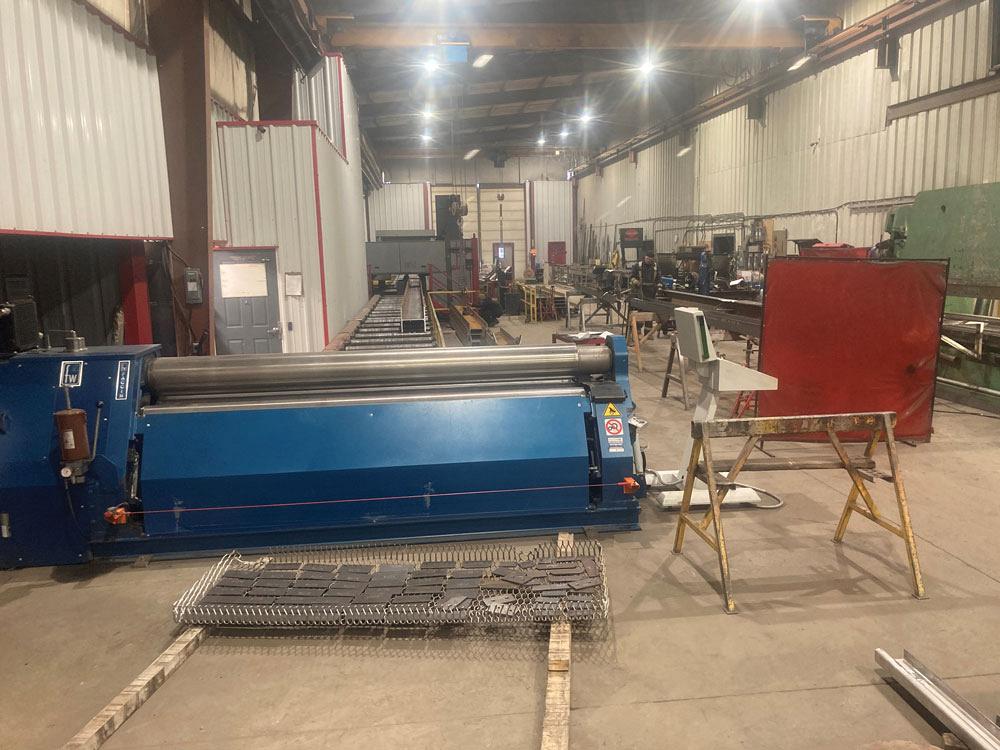
In late 2019 Kozinuk purchased its new Faccin 4HEL 4-roll plate roller with CNC through All Fabrication Machinery, Calgary.
The Fab Rite team spent time looking at the layout of the shop to find the most efficient spot to put the new machine. The 4-roll machine was smaller than some other machines the shop bought recently, so compared to the larger equipment, the installation was a breeze.
When All Fabrication Machinery delivered the machine in March 2020, the shop was fortunate enough to have technicians from Faccin travel to Cranbrook to train the team before COVID-19 travel restrictions were put in place. They were shown how to adjust the machine and process the plates to get the results they were looking for.
"There was a bit of a learning curve, but we do have some employees who are experienced with plate rolling technology," said John Stacewicz, CNC equipment manager. "These guys knew what to look for and really got on board with the new technology, learning how to program it and seeing all the different values of the machine and what they mean for the plate rolling process."
The team anticipated having to do a test first and then adjust the rolls, but with the steel characteristics changing throughout the sheet, they have found that it often takes three tests to get the exact result they need. Stacewicz and Brass agreed that this machine is ideal for three or more parts per run.
"It really shines on jobs where we have multiple rolls of the same material thickness, and we can just keep rolling and rolling," said Brass. "We can see how the steel is bending with a particular grade of steel we are using or how a particular roll or plate from a mill differs from others. But once you get the first one right, the rest takes no time. It’s competitive at that point."
Productivity Gains
The new plate roller has additional power that allows the team to splice longer cans and have rings that are stitched together rather than rolled one ring at a time. The machine can produce three to five rings per roll, making it five times faster than the shop’s previous operation. It also allows the shop to work with thickergauge material. One of the main advantages of this machine is that there is no need to prebump the roll, saving steps and reducing handling of the material.
"The existing machine just didn’t have the capability and we were constantly needing to bump the parts," said Brass. "That meant going to the brake all the time. Now we are able to do larger items and can run it as a smooth roll."
The new plate roller has taken a lot of the preprocessing work out of the equation. Instead of having to take the plate over to the fabrication side for prebumping or the like, it can go straight on the roller and all the information can be put right into the CNC machine, producing a higher-quality item with less human error.
With strategic placement of the 4-roll machine on the shop floor and faster rolling times, the shop is able to capitalize its efficiencies. If the team is working with large plate, it can be cut directly on the plasma table and moved straight to the forming area with the press brakes and rollers. That way, if the project requires prebumping, it can still be done without significant material handling. But for the most part, if it’s within the right parameters, the plate roller can perform the prebend and finish the roll. This means that the team can basically use one crane to move the plate through all necessary processing, limiting the amount of handling and safety concerns.
"When we get away from the one-off jobs, you really can’t compete with the speed of this machine," said Stacewicz. "With the Faccin machine we are able to roll 10 things at a time; that’s a big advantage."
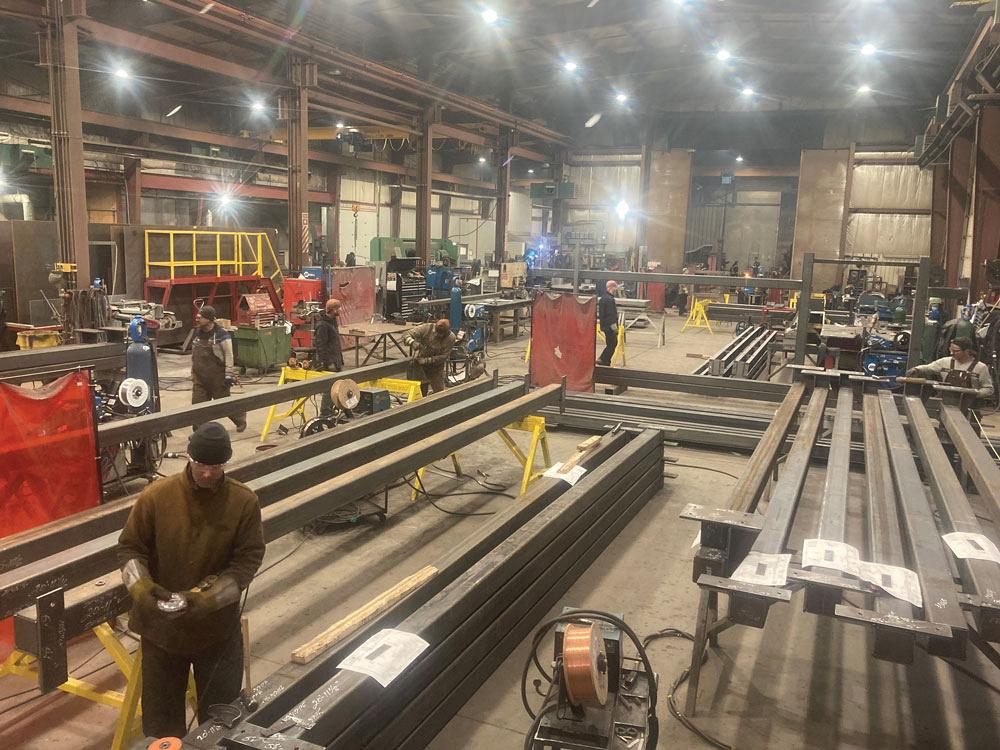
Kozinuk has spent a lot of time and money investing in new CNC equipment and believes that it’s the shop’s quality, speed, and ability to adapt to different products that give it an edge.
The CNC capabilities have really helped Fab Rite increase its productivity. And the team hopes to continue to invest in the latest CNC equipment as it sees significant payoffs with its current upgrades. As the company expands, the team is continually thinking about the flow of the shop and ensuring that each new piece of equipment maximizes the space and work flow efficiencies by reducing handling time and making the processes as seamless as possible. The shop says the Faccin plate roller has been a game-changer, allowing it to compete more broadly by driving down the cost per part and quoting more competitively.
The 4-roll, CNC model was a good midrange choice for the shop. Because Fab Rite takes on a range of unique projects, there are times when it requires heavier or lighter rolling, which is why the shop kept its existing plate rolling machine. But for the most part, the Faccin roller fits the majority of the shop’s current needs. This has allowed it to outsource far less and bring almost everything in-house.
"To be honest, we don’t put that many hours on it right now because when we do, it produces the part so quickly, we just don’t have the work to keep up with the speed," said Brass.
Associate Editor Lindsay Luminoso can be reached at lluminoso@canadianfabweld.com.
Photos courtesy of Fab Rite Services Ltd., www.fabriteservices.com.
About the Author
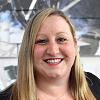
Lindsay Luminoso
1154 Warden Avenue
Toronto, M1R 0A1 Canada
Lindsay Luminoso, associate editor, contributes to both Canadian Metalworking and Canadian Fabricating & Welding. She worked as an associate editor/web editor, at Canadian Metalworking from 2014-2016 and was most recently an associate editor at Design Engineering.
Luminoso has a bachelor of arts from Carleton University, a bachelor of education from Ottawa University, and a graduate certificate in book, magazine, and digital publishing from Centennial College.
Related Companies
subscribe now
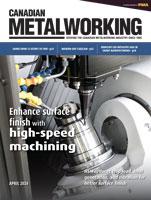
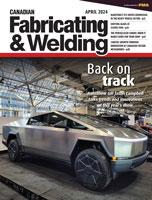
Keep up to date with the latest news, events, and technology for all things metal from our pair of monthly magazines written specifically for Canadian manufacturers!
Start Your Free Subscription- Trending Articles
Aluminum MIG welding wire upgraded with a proprietary and patented surface treatment technology
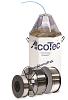
Achieving success with mechanized plasma cutting
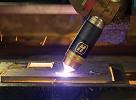
Hypertherm Associates partners with Rapyuta Robotics
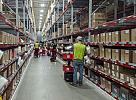
Gema welcomes controller

Brushless copper tubing cutter adjusts to ODs up to 2-1/8 in.
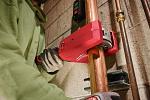
- Industry Events
MME Winnipeg
- April 30, 2024
- Winnipeg, ON Canada
CTMA Economic Uncertainty: Helping You Navigate Windsor Seminar
- April 30, 2024
- Windsor, ON Canada
CTMA Economic Uncertainty: Helping You Navigate Kitchener Seminar
- May 2, 2024
- Kitchener, ON Canada
Automate 2024
- May 6 - 9, 2024
- Chicago, IL
ANCA Open House
- May 7 - 8, 2024
- Wixom, MI