Editor
- FMA
- The Fabricator
- FABTECH
- Canadian Metalworking
Adapting to new needs at Bourque Industrial
Saint John shop sees impact of new ERP system and fabricating machinery
- By Rob Colman
- September 1, 2022
- Article
- Fabricating
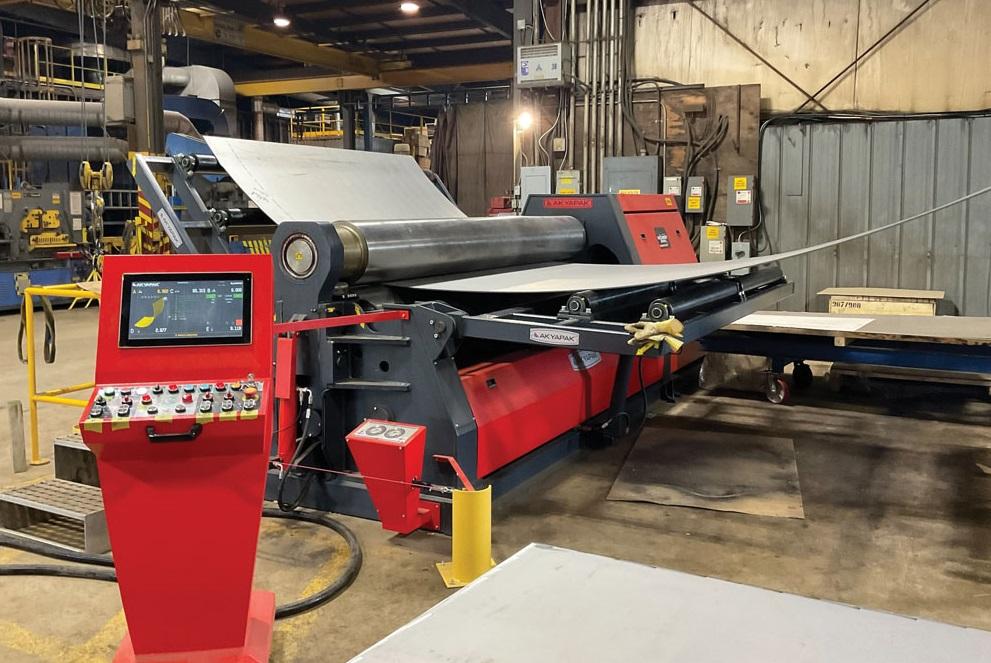
Bourque recently replaced its old plate rolls with an Akyapak AKBend four-roll CNC set supplied by Machinery Experts that allows them to program jobs right at the machine.
The economics of change are rarely simple, particularly when you’re running a business that deals in very heavy machinery and parts. But often, when that one new investment is made, it creates something of a domino effect in a shop.
Saint John, N.B.-based Bourque Industrial Ltd. could be said to have experienced this recently. Between a change in enterprise resource planning (ERP) systems and machine investments necessitated by customer needs, the 76-year-old company is seeing its floor adapt quickly to new expectations, both internal and external.
John Bourque is the third generation of his family to run the company, and both his son and daughter are also involved in the business. Asked what the secret is to the business’s longevity, Bourque said it’s all about relationships.
“Everything we do is based on relationships,” he said. “You want the customer to think of you first when they have a job. It doesn’t mean you get every job out there, but there are some companies we’ve been working with longer than I’ve been with the company.”
The company’s quality management system (QMS) is, in part, driven by the need to meet the regulatory requirements in the many industries the company supplies, such as the oil refining industry, marine, pulp and paper, renewables, and the mining sector. But that QMS also strengthens relationships with local customers.
“It makes it easy for customers to come in and do an audit of the work we are doing for them, and they’re welcome anytime,” said Bourque. “As we develop the use of our ERP system, we will be able provide information on the cloud for customers as well.”
ERP Update
Bourque’s new ERP system was adopted this past year. The company had been considering a new system for some time, but the pandemic brought it to the fore.
“One of our supervisors said, ‘I’d really like to be able to do certain duties from home on a Saturday and not have to come in to set up a job and post people’s time and that sort of thing. Why can’t I make those phone calls I need to make and get people doing what they need to be doing?’ That sent us down a road and drew us to the system we have today. It used to be that everything we did was server-based. This year we went to Office 365. Everyone has total access to their work. We have more collaboration through Teams, and we’re just moving more information to the cloud.”
It has changed the way the front office works, certainly.
“We encourage people to stay home if they have to because at least the office work can be done from anywhere,” he said. “I’m not sure that we’ll ever use tablets on the shop floor to look at prints—there are many quality checks and alterations done on the shop floor, so I’m not sure how well that would work—but when it comes to shipping and receiving, we see real advantages to moving everything into the cloud. The key in making these changes is ensuring that everyone is comfortable with the information they are getting and how the process works. We’re taking baby steps with the system all the time, making sure everyone is comfortable with the way it works rather than doing a radical switchover over the course of a weekend.”
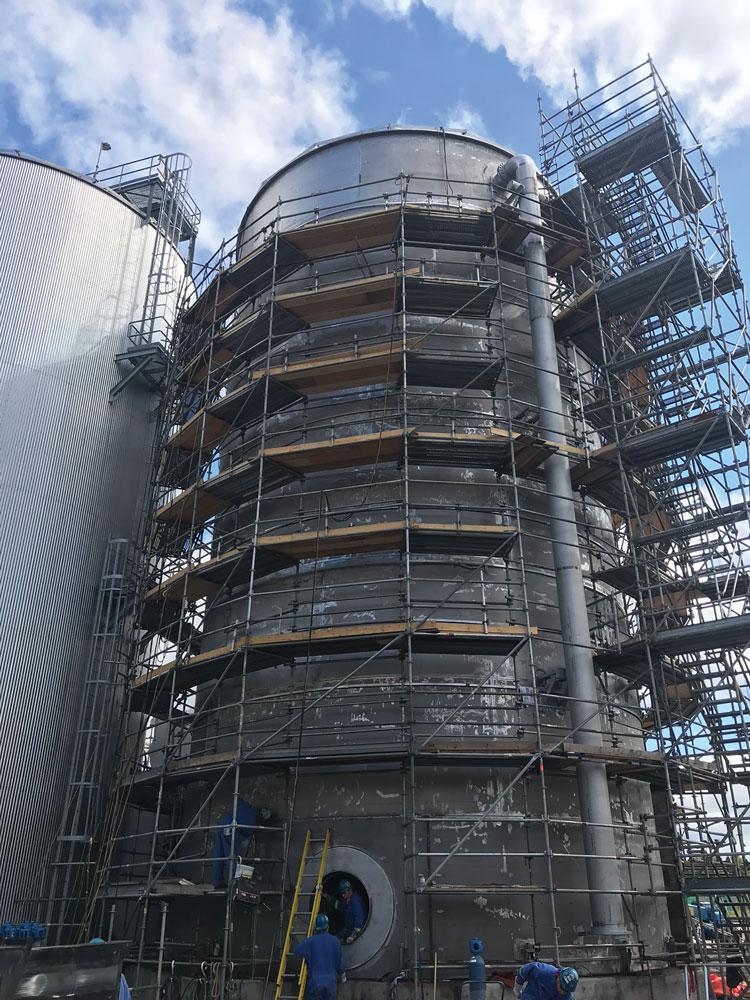
Bourque’s ability to fabricate and deliver large storage tanks has become very popular with its customers. Materials used vary from mild steel to stainless and duplex steels.
Plate Roll Improvements
When we spoke of the challenge of transferring legacy information to new systems, Bourque joked that the only way to save that information is “don’t let people leave. A lot of information in a company our age is trapped in life experiences.”
Like any other company that has been around as long as Bourque Industrial has, there is legacy equipment in the shop that needed to be replaced, and the replacement had to account for an aging workforce and the need for greater efficiencies.
“Our plate rolling machine was 50 years old, and we found that we were quoting a job that it couldn’t handle,” said Bourque. “We don’t erect tanks, but we do roll steel for large storage tanks. Our replacement had to be a machine that could be run by fewer people and be more efficient. We had to make sure the investment we made would make us more competitive.”
Bourque replaced the old plate rolls with an Akyapak AKBend four-roll CNC set supplied by Machinery Experts that allows them to program jobs right at the machine. He invested in a bar roller from the same company for angles, pipes, and flat bar as well because he had been able to do this type of work on his old plate roller.
“Working with a CNC roller is much faster,” he said. “The need to check and recheck patterns as you process material becomes less once the initial part is confirmed. The four-roll setup also means our pre-brake process is more efficient. We are doing things better, more accurately, and quicker.”
In concert with this purchase, the shop upgraded some of its cranes.
“While most of our cranes were powered in every direction, we do have some that were powered up and down but manual push/pull,” said Bourque. “Now three more of our cranes are powered in every direction. Between trying to retain employees and manage the needs of an aging workforce, this is the sort of investment that is necessary.”
Seeing the CNC roller’s ease of use helped Bourque understand how the shop’s bending department could benefit from similar upgrades.
“We purchased a used CNC press brake when we started working for a customer that required a lot of repetitive bends on a certain job,” he said. “We just had to get better part quality and faster production. The dependability and safety of the equipment is making the job easier for our employees, and they appreciate the investment in the work they do.”
Looking Forward
The efficiencies that Bourque has seen with this newer equipment has him looking carefully at all other processes on the shop floor.
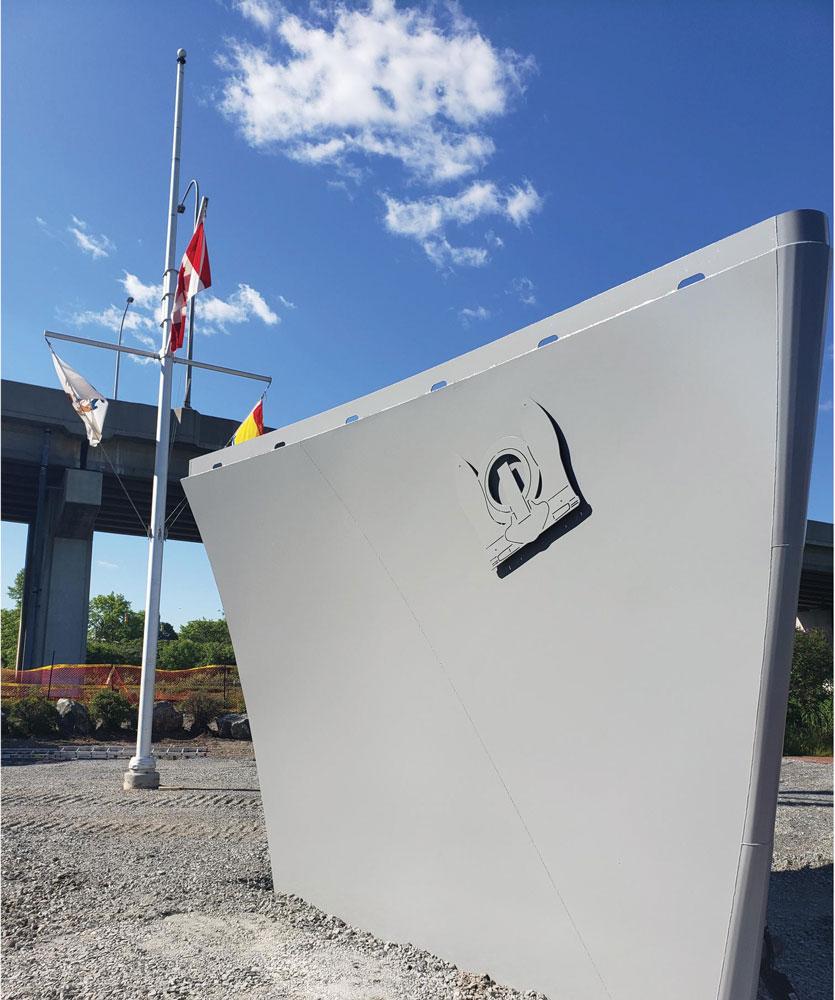
The company’s work varies greatly. For instance, it recently constructed the replica of the bow of HMCS Saint John for the New Brunswick Naval Memorial, which was unveiled to the public at Harbour Passage in Saint John in June.
“For instance, how we cut material has room for advancement,” he said. “The vast majority of what we do is cut on high-definition plasma, but is there other tech out there that might improve our production times? The same can be said for our saw; it’s extremely dependable but we’re bidding on work now that might require an upgrade. It’s a matter of seeing what’s out there and how it might fit our future growth.”
One thing is for sure, Bourque remains busy. “Over the last three or four years, our local work has grown a lot and, in general, has been more consistent over a 12-month period, whereas we used to have seasonal dips. That just isn’t happening now.
“Everything has been positive in our shift to a new ERP system and introducing new equipment,” he continued. “And if we can keep employees and customers happy, then that is ideal.”
Editor Robert Colman can be reached at rcolman@canadianfabweld.com.
Bourque Industrial Ltd., bourqueindustrial.com
Machinery Experts, machinery-experts.solutions
About the Author
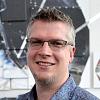
Rob Colman
1154 Warden Avenue
Toronto, M1R 0A1 Canada
905-235-0471
Robert Colman has worked as a writer and editor for more than 25 years, covering the needs of a variety of trades. He has been dedicated to the metalworking industry for the past 13 years, serving as editor for Metalworking Production & Purchasing (MP&P) and, since January 2016, the editor of Canadian Fabricating & Welding. He graduated with a B.A. degree from McGill University and a Master’s degree from UBC.
subscribe now
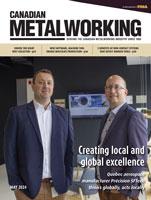
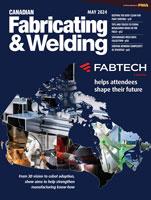
Keep up to date with the latest news, events, and technology for all things metal from our pair of monthly magazines written specifically for Canadian manufacturers!
Start Your Free Subscription- Industry Events
Automate 2024
- May 6 - 9, 2024
- Chicago, IL
ANCA Open House
- May 7 - 8, 2024
- Wixom, MI
17th annual Joint Open House
- May 8 - 9, 2024
- Oakville and Mississauga, ON Canada
MME Saskatoon
- May 28, 2024
- Saskatoon, SK Canada
CME's Health & Safety Symposium for Manufacturers
- May 29, 2024
- Mississauga, ON Canada