Associate Editor
- FMA
- The Fabricator
- FABTECH
- Canadian Metalworking
Ace Machining shows off fabrication expansion
Fab division helps Dartmouth machine shop reach new customers
- By Lindsay Luminoso
- June 22, 2022
- Article
- Fabricating
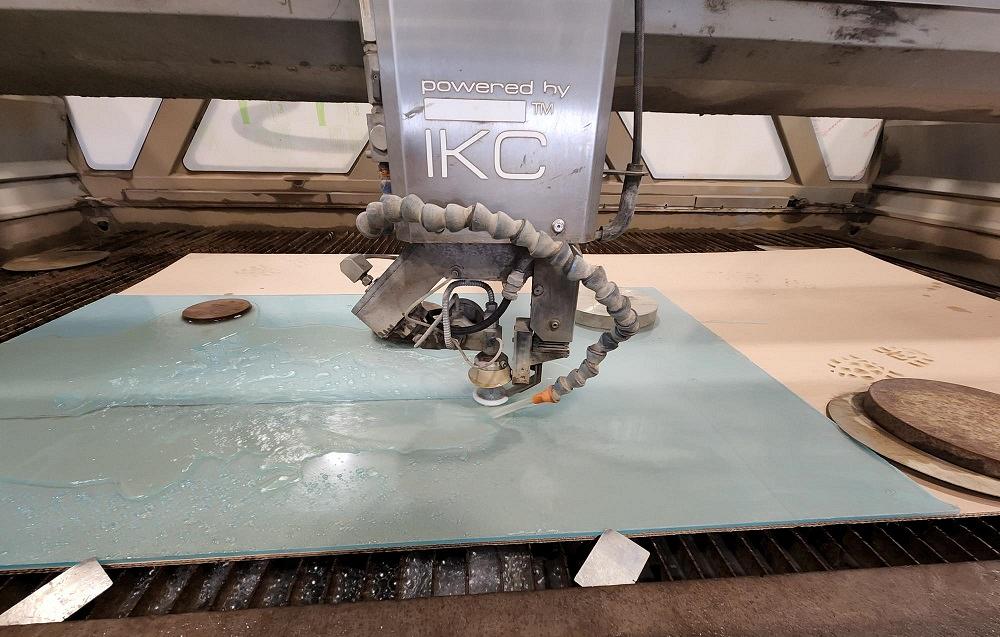
The CMS waterjet’s cutting versatility has allowed the shop to continue cutting metal but also begin working with plastics and plexiglass.
Ace Machining Ltd., a job shop focused traditionally on machining, has thrived in Dartmouth, N.S., since 2008. However, it wasn’t until recently that co-owners Ron Wallace and Andy Race decided that investing in new capabilities and expanding the shop floor would give them an even greater edge and invite in new customers from a diverse range of industries. Little did they know a global pandemic would have other plans for them. Before the pandemic exploded in February 2020, Ace Machining wanted to expand its shop floor and create a new fabrication division.
Don't miss our first profile of Ace Machining back in 2015
"We invested in a waterjet machine about six years ago," said Wallace. "However, we quickly realized that we wanted to add a second waterjet. It was set to arrive the first week of March 2020. The technician came to our facility for the first couple weeks of March; by mid-March the machine was in full swing. The technician left on a Friday, and on that Saturday our province went into full shutdown. I couldn’t help but shake my head thinking of how we just spent all this time and money investing in this new waterjet and how the uncertainty of the pandemic would affect business going forward. Could we be out of business in a few months? We really didn’t know."
Pandemic Influence
However, as luck would have it, that Sunday the shop picked up a contract to produce all plexiglass dividers for Sobeys throughout Eastern Canada. While plastic wasn’t the shop’s niche, they dove headfirst into this new project and it kept them going through the early times of the pandemic. Like so many others, Wallace had expected the shutdowns and pandemic to be short-lived, but that proved not to be the case.
"The longer the pandemic dragged on, many of our customers started to pivot to making pandemic-related products," said Wallace. "So we did the same. We built the molds for a customer that was making N95 masks and worked on other projects like mask and hand sanitizer dispensers."
It was on his drive to work one morning that Wallace was struck with an idea. While grabbing a coffee from the local Tim Hortons he accidentally touched hands with the cashier as she handed him his coffee through the drive-through window. This got Wallace thinking, and when he arrived at the shop he came up with an idea to make drive-through service paddles for passing the debit machine and items through the drive through window to limit that interaction. That idea was then integrated into some Tim Hortons and McDonalds, as well as Dairy Queen locations across North America.
"We were able to custom design them for the various stores," said Wallace. "But eventually we came up with a uniform product that we can sell to anyone. It really took off and became our flagship product. We have always been a job shop, but now with our own product, it gave us a little bit more control."
Expanding Into Fabricating
At first, the pandemic had put a pause on the shop’s building expansion project. However, by September 2020 the shop was busier than ever before. Wallace decided that it was important to start building the new space.
It took just about one year, but in September 2021 Ace Machining had a new 12,000-sq.-ft. shop dedicated to fabricating. All in all, the company now has around 26,000 sq. ft. of floor space.
"The new building is where we focus all of our fabrication," said Wallace. "The old building is now focused on manual and CNC machining. We also invested in a third waterjet that arrived in January 2022. We are still waiting on a DMC m950 plate profiling/deburring machine that has been delayed because of supply chain issues, but we are hopeful it will arrive soon."
Originally the shop chose to invest in its own waterjet machine after it realized it was spending over $100,000 per year subcontracting out waterjet work.
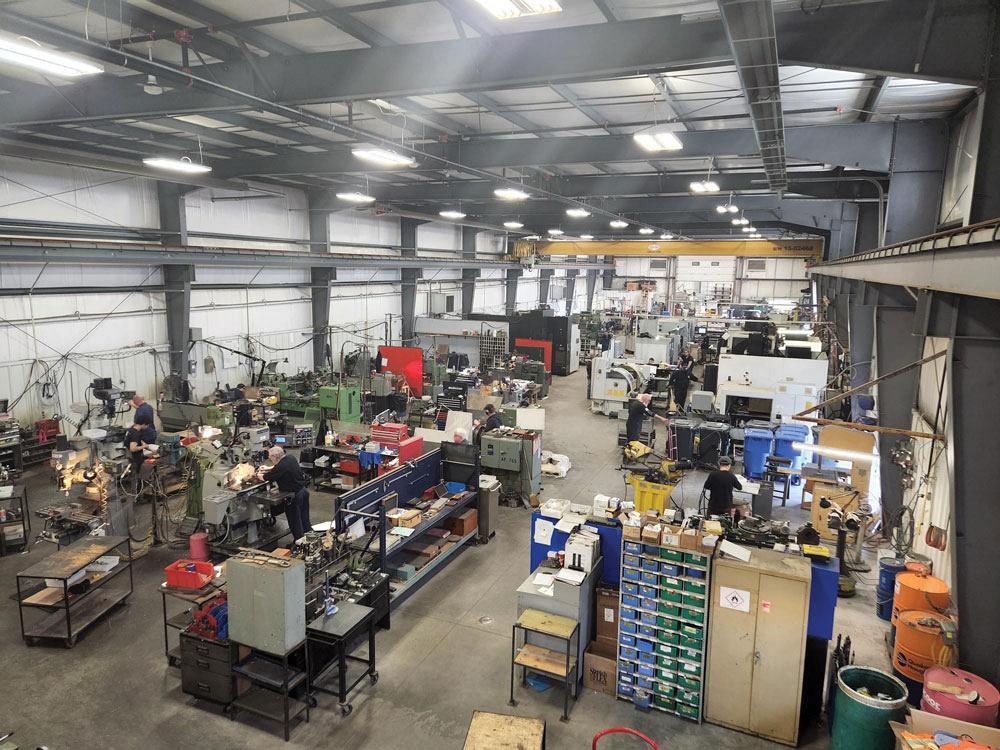
Ace Machining’s original 14,000-sq.-ft. shop is now a dedicated machine shop. Its new 12,000-sq.-ft. facility is devoted to fabricating.
"Waterjet behaves like it’s trying to destroy itself all day long, and there’s a lot of maintenance that goes with it," said Wallace. "A lot of our subcontractors’ waterjets would often be down for maintenance, delaying our parts, which then pushed projects back and made our customers unhappy. For that reason, we steered clear from waterjet work, but a lot of our customers had projects that required it. We didn’t like being a victim of our subcontractors’ issues so we decided to invest."
For all the waterjet work that the shop was taking on, it just made sense to bring this capability in house. The first CMS 5-axis waterjet was purchased six years ago. Wallace did quite a bit of research into waterjets before he decided on CMS.
"CMS is huge in Europe," said Wallace. "And, in my opinion, there is nobody making waterjets like them in North America. I would consider CMS to be the Ferrari of waterjets." After extensive research, the Ace Machining team settled on CMS for several reasons. One of the main reasons why the shop decided to invest in a waterjet in the first place was it didn’t want to deal with its subcontractors’ downtime, and it certainly didn’t want to deal with its own equipment’s downtime either. For Ace Machining, abrasive removal was a feature that a new waterjet machine needed to have.
"Our CMS waterjet has an abrasive removal system that constantly pulls out the abrasive, so there’s no downtime for abrasive removal," said Wallace.
Cleaning a waterjet costs shops both money and time because of the significant downtime required for that task, which equates to revenue loss. To clean it, a vacuum truck is needed, which can be expensive, and several workers have to shovel out the abrasive. However, the machine’s abrasive removal feature constantly removes the abrasive by itself; there is no need to shutdown to clean it.
Another benefit of the waterjet is that it runs a 3-cyclinder EVO pump system. If a pump blows, the operator can turn off that particular cylinder and operate the other two without having to stop the project to fix the machine. The job can be completed on schedule without the customer knowing a problem occurred. Wallace noted that some other waterjet manufacturers offered only a single-acting cylinder, and from what he’d encountered with subcontractors he wanted to limit as much downtime as possible.
It also had automated cutting with an anti-collision device. This allowed operators to load parts on the machine overnight for it to work unattended. Some other waterjet manufacturers were hesitant to recommend unattended operation, but this was something Ace Machining felt strongly about.
"With most waterjets you get about 1,000 hours of work per year because you’ve got load/unload and programming stoppages," said Wallace. "But we’re hitting well over 2,000 hours per year on the waterjets working eight hours a day because we’ll load them up and they’ll cut unattended for four or five hours every night. They’re work horses."
Ace Machining is a machine shop first and foremost, so it’s always worked in that 3D space, which is why it was important for the shop to invest in a 5-axis waterjet machine. The benefit of 5-axis is there is no post-op machining.
"I can counter sink holes, back-bevel plate, or perform a curve compensation," said Wallace. "I don’t have to set it back up in a mill machine, locate a hole, and finish the part, which would be a huge waste of time."
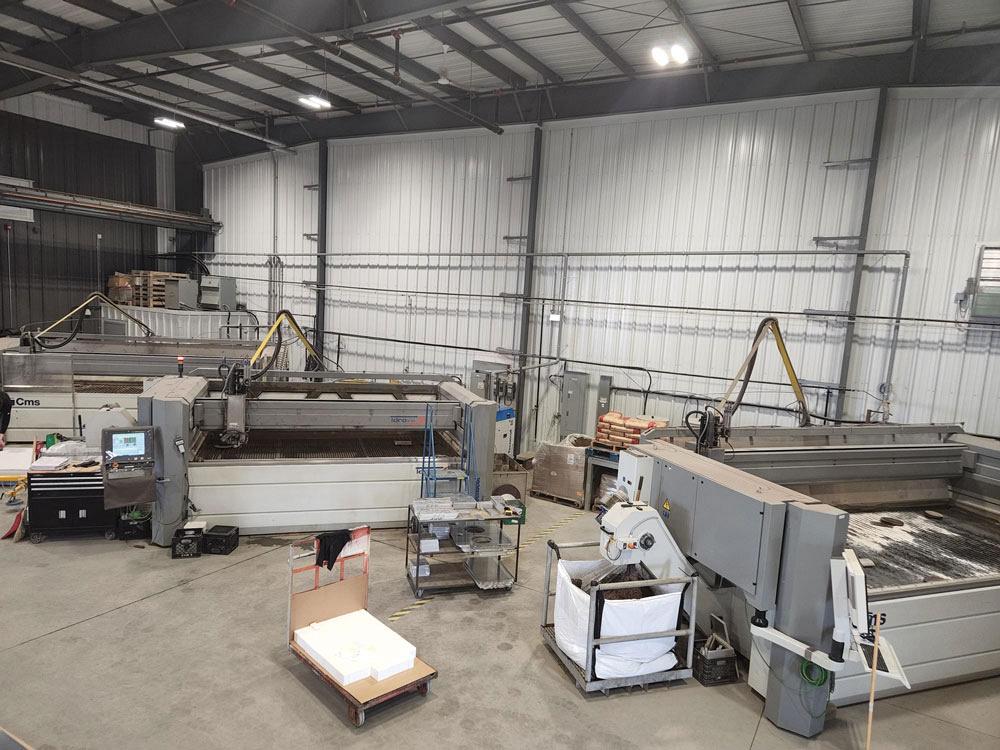
After purchasing its first CMS 5-axis waterjet, the company decided to invest in a second 5-axis machine and more recently purchased a 3-axis waterjet.
It’s first waterjet made sense as the shop expanded into fabricating, but as business picked up so did the need for a second machine. And as business grew, including it’s move into a dedicated product line, so did the need for a third.
Ace Machining worked with CMS directly for its first purchase; however, Elliott Matsuura has since become the distributor for CMS machines in Canada.
While the first two waterjets are 5-axis, the third one is strictly 3-axis and includes the abrasive removal and other features the shop wanted in all of its machines. The 5-axis machines are used primarily for precision cutting while the 3-axis machine is used for non-precision cutting.
"The initial waterjet was like a game changer," said Wallace. "It put us into a new level of fabrication because we were a machine shop first. Now we’ve got this new building and we employ around 43 people, but I’m hoping to get close to 50 this year."
The Next Project
With the expanded floor space and dedicated fabrication division, integrating an enterprise resource planning (ERP) system was the next logical step for Ace Machining.
"An EPR system now has become essential with 26,000 sq. ft. of workspace," said Wallace. "Having to look for a job or components could take quite some time, so we wanted to eliminate that. I’ll be able to track the job from the office. We’ll have a better handle on costing, especially with the cost of material right now. We really need to get a better handle on how to best quote a job. Every machine in the shop will have its own computer in an attempt to go paperless."
The installation of the company’s ERP system has hit some bumps with supply chain issues, but Wallace is confident that the hardware portion of the install will be completed in the next couple of months. The shop already has started its onboarding with ProShop.
"With ProShop, our operators will be able to pull up any information they need, take pictures of setups, and upload them to the job files," said Wallace. "The next time the job comes back you can just look at how it was done the last time. We went with ProShop because it was designed by a machinist for machine shops."
And while nobody likes change, Ace Machining has invested in a product that will fit the needs of both the shop and the employees who will champion this new technology. Having a worker dedicated to the ERP system’s rollout will help the shop capitalize on all of its features and help other workers get up to speed quickly, giving the shop a quick return on investment.
"The big thing right now for us is the ERP system," said Wallace. "I’ve been toying with the idea of getting into Swiss machining. We have some parts that we are currently sending out to be Swiss machined, so again we are at the mercy of a subcontractor. I’ve been doing my research into them to learn a little bit more about it. My gut tells me it’s in my future and we’ll own a Swiss lathe. And while we are a job shop first, it’s nice to have a couple products of our own. The only thing I can’t produce more of is time. I really wish I could, but we are doing our best to invest in equipment and processes that will help us make the most of our time."
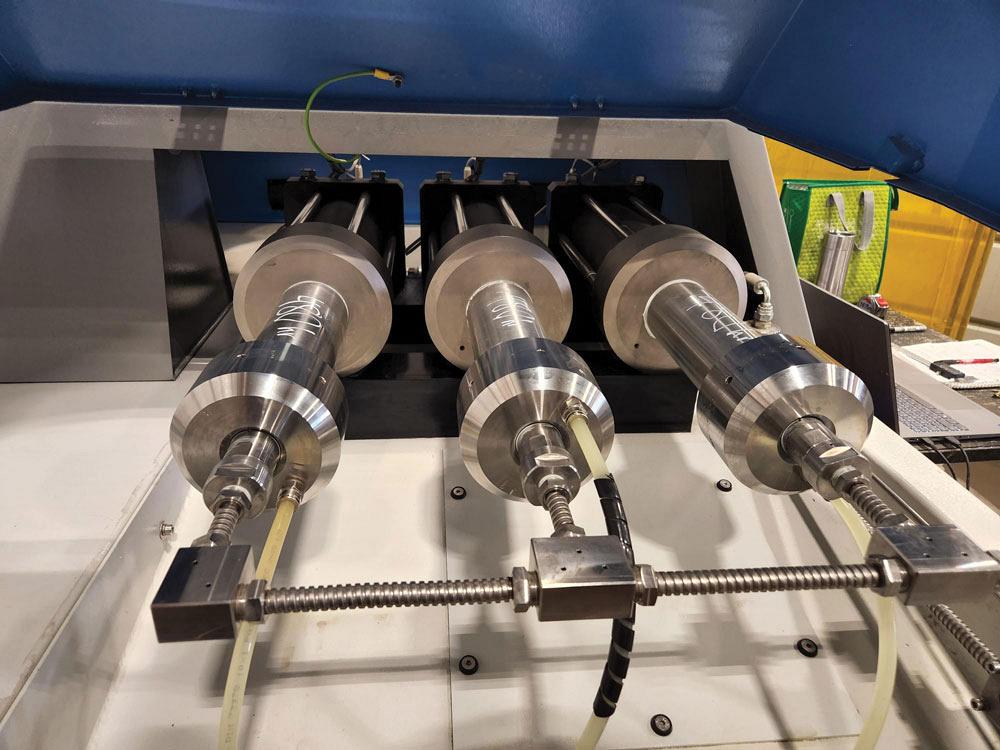
The CMS waterjet comes with a 3-cyclinder EVO pump system. If there is a problem with one of the pumps, the operator can turn off that particular cylinder and operate the other two, allowing the machine to complete the job on schedule.
Associate Editor Lindsay Luminoso can be reached at lluminoso@canadianfabweld.com.
Ace Machining Ltd., www.acemachining.ca
Elliott Matsuura Canada, www.elliottmachinery.com
ProShop ERP, proshoperp.com
About the Author
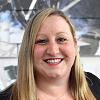
Lindsay Luminoso
1154 Warden Avenue
Toronto, M1R 0A1 Canada
Lindsay Luminoso, associate editor, contributes to both Canadian Metalworking and Canadian Fabricating & Welding. She worked as an associate editor/web editor, at Canadian Metalworking from 2014-2016 and was most recently an associate editor at Design Engineering.
Luminoso has a bachelor of arts from Carleton University, a bachelor of education from Ottawa University, and a graduate certificate in book, magazine, and digital publishing from Centennial College.
subscribe now
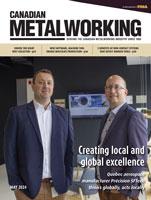
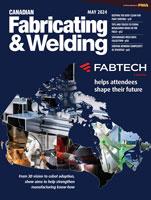
Keep up to date with the latest news, events, and technology for all things metal from our pair of monthly magazines written specifically for Canadian manufacturers!
Start Your Free Subscription- Industry Events
Automate 2024
- May 6 - 9, 2024
- Chicago, IL
ANCA Open House
- May 7 - 8, 2024
- Wixom, MI
17th annual Joint Open House
- May 8 - 9, 2024
- Oakville and Mississauga, ON Canada
MME Saskatoon
- May 28, 2024
- Saskatoon, SK Canada
CME's Health & Safety Symposium for Manufacturers
- May 29, 2024
- Mississauga, ON Canada