Editor
- FMA
- The Fabricator
- FABTECH
- Canadian Metalworking
Streamlining manual parts sorting
Having a parts-sorting strategy is key to managing this potential bottleneck
- By Rob Colman
- February 22, 2021
- Article
- Automation and Software
The high speed at which fibre lasers cut sheet metal has allowed shops to become much more efficient. However, anytime one process becomes more efficient, it inevitably leads to bottlenecks elsewhere in an operation. For those shops that haven’t been able to invest in automated parts sorting, that is where a bottleneck in processing is likely to happen.
Bottlenecks are particularly likely to occur if different assemblies or orders have been nested on the same sheet. No matter how careful an employee is, it is easy to confuse very similar parts with each other, and it’s easy to miss a part if it has fallen out of the nest somehow in processing. The problem, of course, is that these errors probably won’t be captured until the parts have been shifted to their next destination, whether that be welding, paint, or shipping.
One solution to this potential issue is to nest discrete assemblies in separate areas of the sheet. The benefit is that each assembly can be clearly marked. One of the challenges with this approach is that it won’t necessarily lead to the most efficient use of the sheet. Also, if a shop has many short-run assemblies to sort, it could lead to longer programming time.
As an alternative to such an approach, TRUMPF has introduced a sorting guide system. Basically, the system comprises a camera on an arm at the back of the machine connected to a monitor that shows the operator the parts on the sheet. The system colour-codes the parts on the monitor to indicate which parts need to be kitted together.
“Using this, you can reliably remove parts and kit them as the system tells you to do so,” said Brett Thompson, sales engineer for TruLaser at TRUMPF Inc. “Even if you remove multiple parts at a time, it will indicate that they have been removed. And because all parts are highlighted based on what kit they are meant to be grouped with, it is easy to see on-screen if a part is missing because it has fallen out of the nest or is tilted in such a way that it might not otherwise be noticed.”
In our article about Oakville, Ont.-based Mancor in this issue is a photo of a robotic welding cell that also uses a work instruction screen to help the employee determine which part goes where in a fixture before it is placed in the weld cell. In that case, the screen displays a diagram rather than showing parts in real time on the workbench, but the idea behind it is the same: to simplify these processes so that lower-skilled employees can manage jobs more promptly and to allow higher-skilled employees to be deployed elsewhere, where they can add more value.
Thompson, however, sees the real value of the data that the sorting guide provides and collects in how it can be integrated with other tools across a shop floor.
“For shops using our TruTops Fab software, when the parts are sorted out into their assemblies, the system tracks when that assembly is ready to go to its next destination,” he explained. “It books inventories for you at that point. The software will indicate if anything is missing before you take that assembly to its next process. Basically, you are getting a more granular understanding of your process flow. If this is used in concert with our Track&Trace monitoring system, for instance, you could then monitor how that assembly is transported to its next destination and determine if that is handled in the most efficient way possible.”
It’s important for a shop to get as much value as possible from each sheet of metal it processes. Finding ways to streamline part picking is one piece to that value-optimizing puzzle.
Editor Robert Colman can be reached at rcolman@canadianfabweld.com.
TRUMPF Inc., www.trumpf.com
About the Author
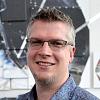
Rob Colman
1154 Warden Avenue
Toronto, M1R 0A1 Canada
905-235-0471
Robert Colman has worked as a writer and editor for more than 25 years, covering the needs of a variety of trades. He has been dedicated to the metalworking industry for the past 13 years, serving as editor for Metalworking Production & Purchasing (MP&P) and, since January 2016, the editor of Canadian Fabricating & Welding. He graduated with a B.A. degree from McGill University and a Master’s degree from UBC.
subscribe now
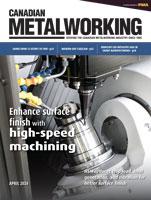
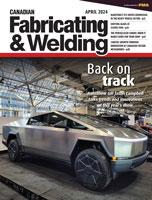
Keep up to date with the latest news, events, and technology for all things metal from our pair of monthly magazines written specifically for Canadian manufacturers!
Start Your Free Subscription- Trending Articles
Aluminum MIG welding wire upgraded with a proprietary and patented surface treatment technology
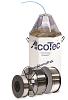
Achieving success with mechanized plasma cutting
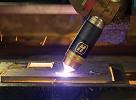
Hypertherm Associates partners with Rapyuta Robotics
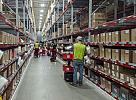
Gema welcomes controller

Brushless copper tubing cutter adjusts to ODs up to 2-1/8 in.
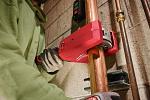
- Industry Events
MME Winnipeg
- April 30, 2024
- Winnipeg, ON Canada
CTMA Economic Uncertainty: Helping You Navigate Windsor Seminar
- April 30, 2024
- Windsor, ON Canada
CTMA Economic Uncertainty: Helping You Navigate Kitchener Seminar
- May 2, 2024
- Kitchener, ON Canada
Automate 2024
- May 6 - 9, 2024
- Chicago, IL
ANCA Open House
- May 7 - 8, 2024
- Wixom, MI