Editor
- FMA
- The Fabricator
- FABTECH
- Canadian Metalworking
AI and robotics in assembly and finishing
While AI supports greater accuracy, industrial applications still demand expert hands
- By Rob Colman
- May 18, 2023
- Article
- Automation and Software
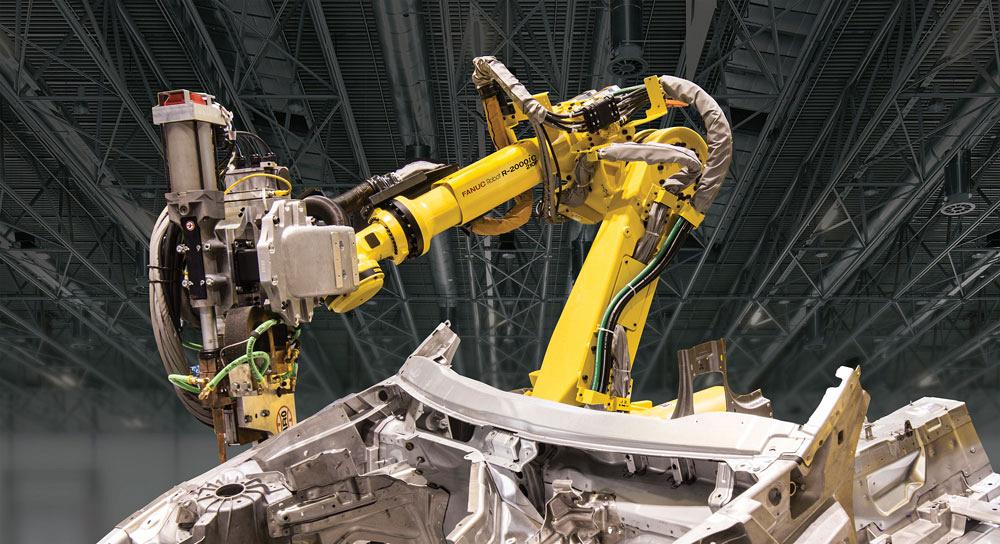
Force sensing is one example where the AI involved can go from the simplest of designs to something much more complex. For automotive applications involving high-strength materials that are generally thinner, stronger, and more challenging to weld, force becomes a critical component in making sure your weld is precise. FANUC Canada
Discussions about artificial intelligence (AI) right now imply that it will have the ability to manage tasks autonomously. AI chatbots like ChatGPT and other apps that can create art suggest that, for many functions, people can be removed from the equation. But that really isn’t the case for industrial applications. For instance, assembly and finishing, where the technology is more sophisticated and valuable every year, still benefit from being managed by skilled operators.
“There are several different levels of AI, and most industrial applications fall into what is described as ‘narrow intelligence,’” said Dale Arndt, director, engineering and integration, FANUC Canada, Mississauga, Ont. “What you are trying to do in that case is learn how to do one task and improve it. It’s based on algorithms, and a lot of machine learning falls into that narrow AI category.”
One definition of machine learning is the ability of a computer system to learn and adapt without following explicit instruction by using algorithms and models and infer patterns in data. Simplified welding paths using cobots are a good example of basic applications. With robots, Arndt noted, we are able to take MIG welding or spot welding and, using vision inputs, welding machine data, and force sensing, ensure each process is done properly. Force sensing also can be used for securing rivets and other fasteners.
“We’re doing these processes again and again and making incremental improvements to the algorithms to create a better process,” he said.
Force Sensing Spread
Force sensing is one example where the AI involved can go from the simplest of designs to something much more complex.
“On the relatively simple end, you can consider force sensing of nuts or rivets in auto manufacturing,” said Arndt. “You can set the amount of torque required to install that fastener correctly. If that trip point isn’t met, you know that the part isn’t in spec. That can save a tremendous amount of rework, but it’s still relatively simple.”
In this case, the robot can carry an automatic nut driver with a built-in force sensor, so no external connections are necessary in this scenario.
Algorithms get more complicated, however, when you start to consider material removal, like polishing material or deflashing injection molded parts.
“With deflashing, you want to move the flashing tool along the part and remove the excess material from seam lines and edges,” said Arndt. “That gets quite complicated because it can depend on the composition of the material, how long it has been out of the mold, the temperature of the plant, and the sharpness of your tool. Suddenly your data set is much larger.
“You have the same issue in material finishing. How worn is the polishing tool? How much excess material is there on the part that you’re polishing? This can involve a number of factors, like monitoring tool use, force sensing, and vision systems.”
A FANUC robot force sensor or an ATI force sensor directly connected to the robot can be used as part of the motion planning in these applications to create immediate changes to the robot path based on the real-time force vector.
Spot Welding Guidance
Spot welding can be equally challenging.
“Most of the high-strength materials that go into modern vehicles are generally thinner and stronger and can be more challenging to weld,” he said. “Force becomes a really critical component in making sure your weld is precise: If you squeeze too hard, you are going to make a hole; if you don’t squeeze hard enough, the weld’s not going to heat up properly and will be too weak.
“But of course, that is not your only variable. Between the current and the force and the timing of your weld, you can determine if there are other concerns to address. There can be a force sensor in the jaw of the gun. And the current is monitored through the weld controller. And the position is managed and monitored by the robot. The communication between the weld controller and the robot is incredibly critical, and a lot of work goes into making sure that we are reacting with the servo system as fast as we can to make changes on that weld as quickly as possible. Getting good welds may be a simple goal, but it involves a variety of interrelated data.”
The feedback mechanisms for this type of system connect directly to the weld controller to rapidly adjust the current flow as the weld metallurgy changes.
Audio Data Input
Weld monitoring also is advancing incrementally, helped along the way by companies like Burlington, Ont.-based Xiris Automation. The company has been developing machine vision products for process and quality control for more than 30 years. Xiris’ weld cameras are known for the clear views they offer of weld arcs, capable of clearly showing the weld pool and seam.
They now are expanding the data set welders can gather with the introduction of its Audio AI tool.
“We have done a lot of experiments on weld audio signals,” said Cameron Serles, CEO of Xiris. “In discussions with experienced welders, we knew that they could tell when something was wrong with a weld process that was taking place on the other side of the shop, if it was bad enough. Sometimes the issue is more subtle than that, but audio can pick up on issues such as missing shielding gas, burn-through, and wire feed skips in real time.”
The system uses an approximately 10-second recording of a good weld to use as the baseline (Xiris recommends a span well under 30 seconds). With that recording, the system can then warn operator if the process is out of spec.
“This is roughly 80 per cent effective in determining when there is an issue,” said Serles. “We did a number of experiments on creating an inference engine that would detect multiple types of defects, but at this stage the data required is too complex. Ultimately, though, the goal is to develop this to a state where the system can actually learn to improve itself based on the audio input.”
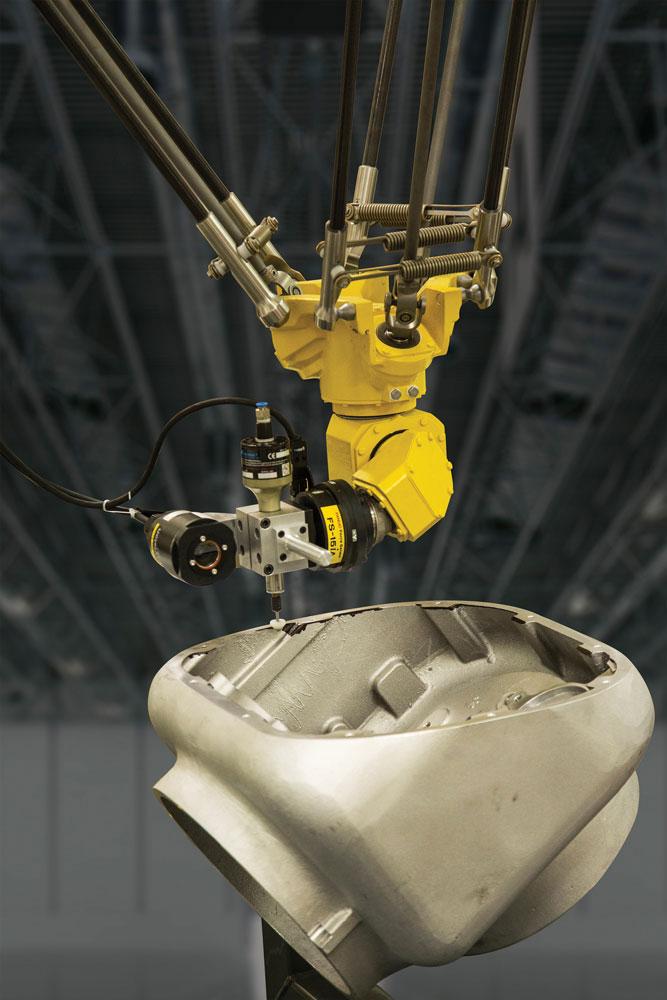
AI algorithms get more complicated when you start to consider material removal, like polishing, deburring, or deflashing injection molded parts. FANUC Canada
Combined with the video data that Xiris systems can already produce, however, this adds a degree of sophistication to how welders can diagnose issues.
“By partnering with the camera system, you can see if the torch is off-centre, or there is a shielding gas issue, or any other concern,” said Serles. “And in some ways, it is easier for integrators to use this in conjunction with a robot because the microphone can be free floating, it doesn’t have to aim exactly at the arc the way a camera does.”
The important thing is that users are adding more information to their data sets.
The Strength of Knowledge
But Arndt hesitates to call any AI-designed system of this sort a “magic bullet.” A good integrator that knows how to manage these tasks will provide a shop with the initial master part parameters to determine what a good part should be, but Arndt sees this as just the beginning of the process.
“Once the system is in production and running for a while, we would hope that the end user would have the capability to say, ‘Hey, I’ve got a lot more data now, and I want to take a look at it and make sure I’m doing everything as optimally as possible.’ This is how the process improves over time. A shop might want better tool life, fewer rejects, or a better finish. Working with the data can help them push the process forward.”
As Arndt noted, there are many variables that affect how an industrial process will run.
“Unlike a translation app, for instance, which is simply dealing with language, industrial processes aren’t linear,” he said. “You are interacting with the physical world, which is always changing. Somebody has to maintain the robot, the polishing head, whatever is being used. All of that takes good industrial discipline.”
Industry 4.0 Complexity
What’s next for this subset of AI? Arndt believes that Industry 4.0 will drive further innovation.
“It’s all about networking industrial devices and how we manage all of this data,” he said. “Just like we all get faster and more capable laptops every year, we will get faster and more capable industrial robots. But with the industry 4.0 architecture, as data is stored from whole facilities, eventually it may be possible for information to be transferred from one robot to another without duplicating programming.
“For instance, if one robot learns a better way to run a weld or polish a part, that information could be uploaded to the plant-level system and then shared with other robots. We are not there yet—that is a lot of data and requires a lot of new connections—but that is a plausible beneficial outcome of where research is going.”
Editor Robert Colman can be reached at rcolman@canadianfabweld.com.
FANUC Canada, fanucamerica.com
Xiris Automation, xiris.com
About the Author
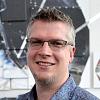
Rob Colman
1154 Warden Avenue
Toronto, M1R 0A1 Canada
905-235-0471
Robert Colman has worked as a writer and editor for more than 25 years, covering the needs of a variety of trades. He has been dedicated to the metalworking industry for the past 13 years, serving as editor for Metalworking Production & Purchasing (MP&P) and, since January 2016, the editor of Canadian Fabricating & Welding. He graduated with a B.A. degree from McGill University and a Master’s degree from UBC.
subscribe now
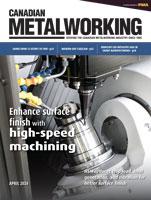
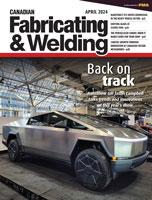
Keep up to date with the latest news, events, and technology for all things metal from our pair of monthly magazines written specifically for Canadian manufacturers!
Start Your Free Subscription- Trending Articles
Aluminum MIG welding wire upgraded with a proprietary and patented surface treatment technology
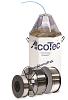
Hypertherm Associates partners with Rapyuta Robotics
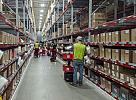
Gema welcomes controller

Brushless copper tubing cutter adjusts to ODs up to 2-1/8 in.
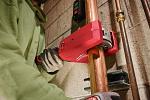
HGG Profiling Equipment BV names Western Canada area sales manager
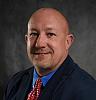
- Industry Events
CTMA Economic Uncertainty: Helping You Navigate Kitchener Seminar
- May 2, 2024
- Kitchener, ON Canada
Automate 2024
- May 6 - 9, 2024
- Chicago, IL
ANCA Open House
- May 7 - 8, 2024
- Wixom, MI
17th annual Joint Open House
- May 8 - 9, 2024
- Oakville and Mississauga, ON Canada
MME Saskatoon
- May 28, 2024
- Saskatoon, SK Canada