Editor
- FMA
- The Fabricator
- FABTECH
- Canadian Metalworking
You Say You Want a Revolution?
- By Joe Thompson
- October 6, 2014
The Industrial Revolution is coming.
No, not the sooty, steam-powered revolution so hated by English author Charles Dickens, but Industry 4.0—the fourth industrial revolution.
Industry 4.0, which also is being called advanced/digital manufacturing and even smart manufacturing, is the merging of traditional manufacturing methodologies with advanced digital systems. It is, at its heart, the computerization of manufacturing.
These so-called cyber-physical systems are being touted as the future of manufacturing, especially in the Western world. Smart factories that are productive, adaptable, and ergonomic will be at the center of the fourth industrial revolution and are currently being studied in Kaiserslautern, Germany, by the German Research Center for Artificial Intelligence.
However, this journey into the future of manufacturing will not be an overnight trip. Expect a decade or more of incremental steps and growing pains.
MTConnect, the openstandard system that creates greater interoperability among shop devices and software applications, is one step along the path. The Internet of Things (IoT) is another. IoT is a collection of systems, products, and objects—the Things—that can be assigned an IP address, enabling wireless machine-to-machine communication without human interaction. Things with this ability often are referred to as “smart.”
These smart objects are made possible thanks to both advances in computing power and the miniaturization of computer components.
The end game is very complex, and the journey to get there will be as well. After the fourth industrial revolution, a part will communicate with every operation and process along its path. In other words, the production facilities of the not-too-distant future will control—and optimize—the manufacturing processes by themselves.
The first Industrial Revolution was propelled by the mechanization of manual work. Sound familiar? The second Industrial Revolution revolved around mass production techniques. Also familiar. The third Industrial Revolution happened just a few decades ago when computer systems were first added to manufacturing machines.
The fourth industrial revolution adds the Internet to the equation.
Next-generation manufacturing definitely has its challenges. Openness and standardization among all suppliers are necessary to properly exchange and use data. It must also be cost-effective.
However, such openness already is being seen in the carbide cutting tool market, so it can happen.
ISO 13399 is a new international standard for describing cutting tool product data. Tools made by manufacturers that use this new standard share the same parameters and definitions, making it easier to communicate tool information between different software systems.
It is now possible to import this standardized cutting tool information directly into a CAD, CAM, simulation, or tool management system quickly, and without fear of entering the wrong parameter. Job planning, simulation, and proveouts can now be done faster and with higher accuracy.
These are just the beginning steps; more will follow. Let’s hope they happen without anybody getting their toes stepped on.
subscribe now
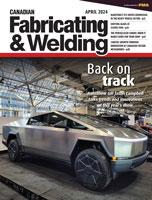
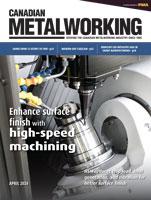
Keep up to date with the latest news, events, and technology for all things metal from our pair of monthly magazines written specifically for Canadian manufacturers!
Start Your Free SubscriptionAbout the Author
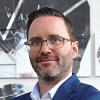
Joe Thompson
416-1154 Warden Avenue
Toronto, M1R 0A1 Canada
905-315-8226
Joe Thompson has been covering the Canadian manufacturing sector for more than two decades. He is responsible for the day-to-day editorial direction of the magazine, providing a uniquely Canadian look at the world of metal manufacturing.
An award-winning writer and graduate of the Sheridan College journalism program, he has published articles worldwide in a variety of industries, including manufacturing, pharmaceutical, medical, infrastructure, and entertainment.
- Trending Articles
Automating additive manufacturing
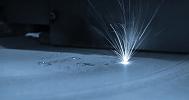
CTMA launches another round of Career-Ready program
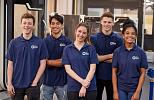
Collet chuck provides accuracy in small diameter cutting
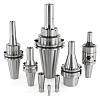
Sandvik Coromant hosts workforce development event empowering young women in manufacturing
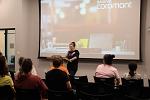
GF Machining Solutions names managing director and head of market region North and Central Americas
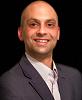
- Industry Events
MME Winnipeg
- April 30, 2024
- Winnipeg, ON Canada
CTMA Economic Uncertainty: Helping You Navigate Windsor Seminar
- April 30, 2024
- Windsor, ON Canada
CTMA Economic Uncertainty: Helping You Navigate Kitchener Seminar
- May 2, 2024
- Kitchener, ON Canada
Automate 2024
- May 6 - 9, 2024
- Chicago, IL
ANCA Open House
- May 7 - 8, 2024
- Wixom, MI