Editor
- FMA
- The Fabricator
- FABTECH
- Canadian Metalworking
The Adventures of Manufacturing Across the Third Dimension
- By Joe Thompson
- November 10, 2014
In science fiction—both the well-written and the drivel —bad guys quite often appear from another dimension. Doctor Who, the Avengers, and physicist/pilot/rock star Buckaroo Banzai have all had their share of interdimensional enemies.
Designers, programmers, and machine operators in manufacturing shops today are no strangers to multidimensional headaches either.
Programming tool paths in 3-D is more complicated, time-consuming, and requires a special software package. Workholding and toolholding must be correctly chosen and implemented to eliminate the potential for head crashes during operation.
It’s rather simple: 3-D work is hard.
That fact is not stopping Canadian shops from moving into the third dimension, however. Even though the work is more complex, the value of finished parts is higher, and this creates the opportunity for shops to be more profitable.
Removing material in order to create a finished piece is an artistic idea that dates back thousands of years. In 2009 an ivory figurine was found in southwestern Germany that has since been dated to roughly 34,000 B.C. Fast-forward 36,000 years and we are still doing it that way.
Milling, turning, grinding, and EDM, as well as traditional fabrication cutting processes such as plasma, laser, and waterjet, all are subtractive machining operations. They are comfortable. They are like my old, almost-wornout Chuck Taylor All Stars.
Additive manufacturing, the industrial version of the much-heralded 3-D printing, uses digital design data to build a part layer by layer by depositing material in three dimensions.
It’s an interesting process, and one that’s definitely en vogue.
At the recent International Manufacturing Technology Show (IMTS) in Chicago, it was talked about … a lot. AMT—The Association For Manufacturing Technology partnered with Local Motors, Oak Ridge National Laboratory, and machine builder Cincinnati Incorporated to “print” and assemble an electric car during the show.
The 3-D printing process took 44 hours to create a car from carbon fiber-reinforced polymer (CFRP). The wheels and hubcaps also were 3-D-printed, but using the direct metal process.
Gimmick? Sure. Interesting, also yes. Social media literally was all atwitter.
The industrialization of the 3-D printing process is intriguing to Canadian manufacturers. It’s hot, it’s now, and it has potential for large-scale growth.
It also has the theoretical community interested.
CRIQ, the Centre de recherche industrielle du Québec, got so interested it already has invested in the technology —a piece of equipment for the production of metal parts.
“The new 3-D printer will allow us to continue making strides in applied industrial research and support businesses hoping to modernize equipment and increase productivity. Our new business service will enable these businesses to bring this emerging technology to the world stage,” said Denis Hardy, president and CEO of CRIQ.
It is just one of many institutions preparing for the future of manufacturing in this country, one that likely involves additive manufacturing on an industrial scale.
It’s happening now … in a dimension near you.
subscribe now
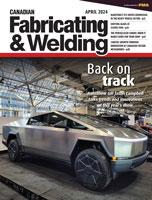
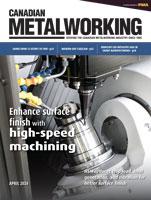
Keep up to date with the latest news, events, and technology for all things metal from our pair of monthly magazines written specifically for Canadian manufacturers!
Start Your Free SubscriptionAbout the Author
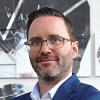
Joe Thompson
416-1154 Warden Avenue
Toronto, M1R 0A1 Canada
905-315-8226
Joe Thompson has been covering the Canadian manufacturing sector for more than two decades. He is responsible for the day-to-day editorial direction of the magazine, providing a uniquely Canadian look at the world of metal manufacturing.
An award-winning writer and graduate of the Sheridan College journalism program, he has published articles worldwide in a variety of industries, including manufacturing, pharmaceutical, medical, infrastructure, and entertainment.
- Trending Articles
Automating additive manufacturing
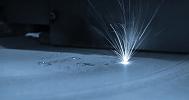
CTMA launches another round of Career-Ready program
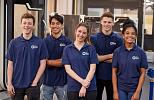
Collet chuck provides accuracy in small diameter cutting
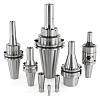
Sandvik Coromant hosts workforce development event empowering young women in manufacturing
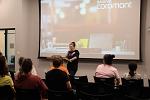
GF Machining Solutions names managing director and head of market region North and Central Americas
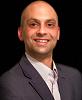
- Industry Events
MME Winnipeg
- April 30, 2024
- Winnipeg, ON Canada
CTMA Economic Uncertainty: Helping You Navigate Windsor Seminar
- April 30, 2024
- Windsor, ON Canada
CTMA Economic Uncertainty: Helping You Navigate Kitchener Seminar
- May 2, 2024
- Kitchener, ON Canada
Automate 2024
- May 6 - 9, 2024
- Chicago, IL
ANCA Open House
- May 7 - 8, 2024
- Wixom, MI