President
- FMA
- The Fabricator
- FABTECH
- Canadian Metalworking
Shrink-fit Toolholding for the Medical Industry
- By Brendt Holden
- March 1, 2010
- Article
- Management
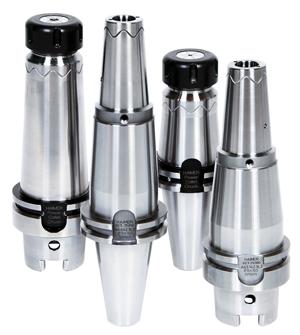
Haimer USA's Power series, which includes shrink chucks and collet chucks, is suitable for medical equipment machining.
Tolerance requirements in the medical industry typically are much more precise than in general machining. This means that more attention must be paid to selecting the toolholder with the appropriate features and benefits.
Generally speaking, many manufacturing facilities throughout North America have overlooked toolholding for milling machines. Those that produce parts for the medical supply chain, however, often have been early adopters of more precise toolholder options. Over the last decade, the North American-based medical industry has accepted and integrated shrink-fit toolholders to a larger degree than other segments of the manufacturing sector.
Addressing a Challenge
The medical industry faces many challenges in which shrink-fit toolholders have provided benefits. Fine finishes, cutting tools with small diameters, deep reaches for clearances on five-axis machining centers, and difficult-to-machine materials are among the obstacles for many medical manufacturers.
To address these challenges, medical equipment shops have been forced to look at their entire process.
For example, choosing the correct machine tool for the job is no longer the only consideration. It is important to choose an appropriate machine control, CAD/CAM software package, toolholders, and cutting tools to complete the job in the most efficient manner.
Finding a Toolholder
When looking for toolholding systems for any type of machining process, manufacturers first must focus on three main features that a toolholder must provide:
- Rigidity. Only sufficient taper contact and proper clamping of the toolholder in the machine tool spindle will provide the rigidity necessary for complex medical manufacturing.
- Accuracy. Minimal run-out at the cutting edge of the cutting tool will ensure accuracy of any job.
- Balance. A balanced assembly of the toolholder (including accessories such as pull-studs) and cutting tool combination will create the proper balance.
Beyond the three main toolholder functions, a medical manufacturer often must think of the following:
- Toolholder geometry. Often deep reaches are required in the process, which can present clearance challenges. Also, with the five-axis machining applications common in medical manufacturing, extreme clearances must be taken into account.
- Toolholder cleanliness. Clean toolholders will prevent excessive run-out, especially with small-diameter cutters.
- Cutting tool clamping. Many small-diameter cutters are used in medical machining. Also, because exotic materials often are machined, a strong gripping torque is required.
- Cutting tool life. Cutting tools often have exotic coatings for optimal performance, which lead to a high price tag.
- Finish. Higher speeds and feeds are used with lower depths of cut, which translates into better surface finishes. This makes balance even more important to minimize vibration at the cutting edge of the cutting tool. Also, proper chip evacuation provides better finishes.
Based on these requirements, most medical manufacturers have found utilizing shrink-fit toolholders during production will give them the best opportunity to accomplish the job in a timely, productive, and cost-effective manner. Also, with the evolution of inductive shrink-fit machines, the process of shrink-fitting has become easier, faster, safer, and less costly.
Ten Characteristics of Shrink-fit Toolholders
- Accuracy
The shrink-fit chuck should be able to guarantee 0.00012-in. (3-micron) maximum run-out at three times the cutting tool diameter, an accuracy that should also be repeatable from operator to operator. - Slim profile
Shrink-fit chucks are available with 3-degree draft angles and slim profiles. They can be modified to be straight-walled if needed to prevent toolholder collision with the workpiece. - High gripping torque
The 360-degree grip of a shrink-fit chuck provides very high gripping torque that helps prevent the cutting tool from moving during roughing or finishing operations. - Extended reach
Extensions to the standard reach can provide many options for standard products. For deep-cavity machining, the shrink-fit extensions are placed into standard shrink-fit chucks, which results in longer toolholder lengths with very little run-out. This is beneficial for five-axis machining as well. - Balance repeatability
Because a shrink-fit toolholding system has no moving parts, high balance repeatability is possible. Shop that use a properly balanced shrink-fit chuck with the correct accessories (such as pull-studs) and use quality cutting tools without inherent unbalance (such as flats), often can achieve good balance characteristics for running at high speeds with no additional fine-tune balancing required. - Fast toolchanging, less inventory
Tool changes can be made in five to 10 seconds. Also, a shop needs fewer toolholder accessories such as collets, nuts, and seal disks. - Cleanliness
A shrink-fit chuck typically is a sealed system, which minimizes the introduction of contaminants to the bore. - Coolant options
Often shrink-fit chucks have a means of delivering the coolant or air/oil mist to the cutting edge of the cutting tool. This helps with chip removal and can also aid in providing better finishes. In addition, if a medical manufacturer does high-precision drilling, a shrink-fit chuck makes an excellent holder for coolant through drills since no accessories or special collets are needed—the sealed design of the toolholder simply allows the coolant to flow through the cutting tool. - Setup consistency
All toolholder setup operators set the toolholders the same way with shrink-fit holders. Variables such as overtightening or undertightening a collet nut or not cleaning out a chuck sufficiently are eliminated. - Availability of shrink chucks
Most of the major toolholder builders in the world now offer shrink-fit chucks as a standard.
This means that shrink-fit holders provide high repeatability from toolholder setup to toolholder setup, which is beneficial for shops running lights-out.
Selecting the Proper Shrink-fit Chuck
Typically, a new toolholder will last the life of a machine tool. Studies have found that the overall expense of toolholders is less than 0.5 percent of the overall cost of the machining process over the machine tool’s life.
Also, it is important that the chuck subscribes to DIN standards for the nose dimensions so that all cooling options from the shrink-fit machine side can be utilized.
For more information, visit www.haimer-usa.com.
About the Author
Related Companies
subscribe now
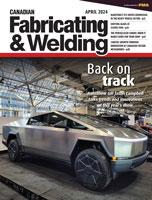
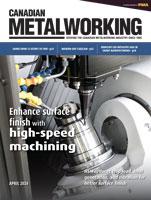
Keep up to date with the latest news, events, and technology for all things metal from our pair of monthly magazines written specifically for Canadian manufacturers!
Start Your Free Subscription- Trending Articles
Automating additive manufacturing
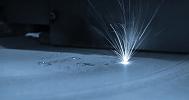
Identifying the hallmarks of a modern CNC
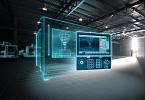
CTMA launches another round of Career-Ready program
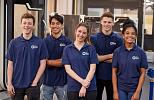
Collet chuck provides accuracy in small diameter cutting
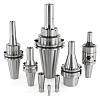
Sandvik Coromant hosts workforce development event empowering young women in manufacturing
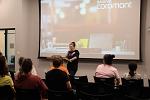
- Industry Events
MME Winnipeg
- April 30, 2024
- Winnipeg, ON Canada
CTMA Economic Uncertainty: Helping You Navigate Windsor Seminar
- April 30, 2024
- Windsor, ON Canada
CTMA Economic Uncertainty: Helping You Navigate Kitchener Seminar
- May 2, 2024
- Kitchener, ON Canada
Automate 2024
- May 6 - 9, 2024
- Chicago, IL
ANCA Open House
- May 7 - 8, 2024
- Wixom, MI