- FMA
- The Fabricator
- FABTECH
- Canadian Metalworking
An Overview of Precision-ground Tooling
This press brake tooling may be the best choice for precision fabricators
- By Gunter Glocker
- May 1, 2010
- Article
- Management
Planer-made press brake tooling has been in use for more than 100 years, continues to be widely used by many companies, and will likely be used for many years to come. However, with customers turning more and more to higher-precision, more flexible press brakes, precision-ground and segmented press brake tooling are gaining a greater market share to better complement these newer machines.
Where planer-made tooling has an important place in the market, and will likely keep this place long-term, is for special combination tools, such as corrugation dies, channel dies, curling dies, and special-radius form tools.
With these special combination tools, the part typically is formed by the shape of the tool combination in a bottoming process, and a precision-ground, hardened tool is not normally required. These combination tools also can be manufactured more cost-effectively and faster as a planer-made tool rather than as a hardened and precision-ground tool.
For standard and modified press brake tooling, precision-ground, segmented, and hardened tooling has many advantages over planer-made tooling. This is the case even for customers that are not forming tight-tolerance parts.
The Tools
When used in a press brake that is in good condition, precision-ground tooling will always produce higher-quality parts than planer-made tooling.
The accuracy of precision-ground tooling is within +/- 0.0008 in., and for some precision tooling lines, within +/- 0.0004 in. Planer-made tooling normally has an accuracy range from +/- 0.002 in. to +/- 0.008 in.
With precision-ground tooling you can be sure that all punches and dies will load into the press brake in exactly the same position every time. This is very important because, in an average setup requiring 30 to 35 minutes with planer-made tooling, approximately half of this time can be spent getting the flange lengths correct. This is due to the constant shift in the tooling center along the Tx axis (backgauge origin) that occurs when changing from one die to another.
It is extremely rare for two planer-made tools to share exactly the same centerline. Therefore, it is impossible to order a punch or die at a later date and be assured they will match.
More often than not, the only guarantee that you will get from the manufacturer is that they will not match, unless you are willing to send back a section of the original tooling so that the new tool can be machined to match the original tool.
Depending on the amount of wear on the original tool, even that may be impossible.
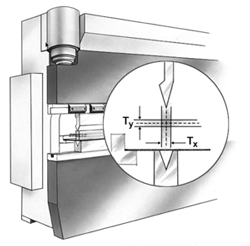
The critical center point (where the T x and T y axis intersect) is very important to maintain over the length of the press brake in order to consistently produce quality parts.
This always requires you to order tooling in lengths long enough to bend your longest part. Usually, that is going to be the full length of the press brake, which can get very expensive, especially when you consider the additional costs associated with cutting individual pieces out of various punches and dies, and having to paint or color-code them so that you will know which sections were cut from the same tool.
This may not work, either, as cutting a tool can relieve the residual stresses that are created during the manufacturing processes. When that happens, the individual sections may twist or bow enough so that they will no longer line up.
With precision-ground tooling, you can purchase just the length of punch and die sections that you need, and when additional tool lengths are needed, the new tools are guaranteed to match up to the original tools.
Precision-ground tools are also presegmented in a rational manner to facilitate making a tool combination quickly to form any length part.
This also makes it easier to store the precision tooling in a small tool cabinet by the press brake versus having to hunt for tools in long tool racks.
Most precision-ground tooling manufacturers mark their tooling with part number, tool length, radius, load capacity, and other critical information for easy identification and use. Obviously, handling short tool segments is also more ergonomic and safer for the press brake operator.
Parts that have holes for insertion of hardware, or holes that are used for assembly to other components, are going to take more time to assemble if they’re made with planer-made tools. Also, inconsistencies in tooling heights along the Ty axis will result in angular errors that must be compensated for via die shimming or a crowning system.
All of this represents lost time and productivity.
Tool Hardening
Tool hardening is critical. Tooling that is hardened at the wear areas, for example the punch tip radius and the shoulders of the V die, will retain its accuracy for the long-term.
Some hardening processes are: flame hardening, nitriding, laser hardening, and induction hardening.
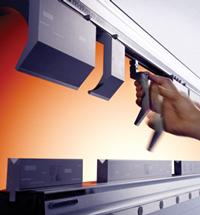
Vertically loading a punch segment for a quick setup using the hydraulic clamping system on the ram and press brake.
Some of today’s precision-ground tooling is also available with safety buttons that allow for fast vertical loading and unloading, rather than sliding tools in from the end of the press brake.
This saves time especially when you must add to or reduce tool lengths to form the inside of down flanges. Top and bottom hydraulic clamping systems are also available that will self-seat and automatically align precision-ground tooling in seconds.
Planer-made tooling has an important role as a cost-effective solution for many special-application forming needs, but for flexibility, accuracy, and speed in consistently producing quality parts, precision-ground tooling is almost always the better choice.
For more information, visit www.wilausa.com.
subscribe now
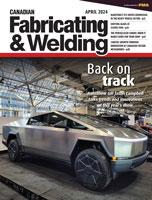
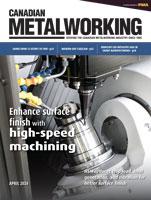
Keep up to date with the latest news, events, and technology for all things metal from our pair of monthly magazines written specifically for Canadian manufacturers!
Start Your Free Subscription- Trending Articles
- Industry Events
MME Winnipeg
- April 30, 2024
- Winnipeg, ON Canada
CTMA Economic Uncertainty: Helping You Navigate Windsor Seminar
- April 30, 2024
- Windsor, ON Canada
CTMA Economic Uncertainty: Helping You Navigate Kitchener Seminar
- May 2, 2024
- Kitchener, ON Canada
Automate 2024
- May 6 - 9, 2024
- Chicago, IL
ANCA Open House
- May 7 - 8, 2024
- Wixom, MI