- FMA
- The Fabricator
- FABTECH
- Canadian Metalworking
Powders Are Building Production Parts
Additive manufacturing offers design flexibility and material variety
- By Sue Roberts
- September 26, 2015
- Article
- Metalworking
Laser sintering, an industrial 3-D printing or additive manufacturing (AM) process, entered the manufacturing world as a technology primarily used for prototyping or proof of concept. Now it is building its own reputation as a production technology for quantities of functional parts. Equipment builders and material suppliers are keeping a laser focus on advancing the machine tools and powders used to build components a layer at a time and educating manufacturers and engineers about the high level of design flexibility that accompanies producing a part with AM.
Andrew Snow, senior vice president, EOS of North America Inc., talked with CIM about the growing AM market and the powders that form the parts.
CIM: How long has EOS been providing AM equipment and powders?
Andrew Snow: For 26 years EOS has been developing and providing the market with laser sintering technology. We continue to innovate. About one-third of our more than 700 employees and 15 to 18 percent of annual sales are dedicated to R&D. We have almost 2,000 systems installed worldwide.
CIM: Since AM has been an accepted industrial process for 26 years, why has it gained so much attention recently?
Snow: A lot of the movement and hype you see now are related to the consumer side of the business and the advent of affordable polymer printers for the home or office.
CIM: What types of metals can be used in the laser sintering process?
Snow: Laser sintering is virtually a microwelding process, so you can only process alloys that are weldable.
The powders that have been commercialized— maraging steel, stainless steels, nickel alloys, cobalt chrome, titanium, and aluminum—fit into a large variety of applications for various industries.
CIM: Are new powders being developed?
Snow: Applications drive the development of materials, and new materials drive the development of new applications. Indeed, there are materials out there that haven’t been officially processed for use in laser sintering, and these additional materials may become commercially available. But before a powder is commercialized, there has to be extensive research on its performance, and data needs to be collected to support its mechanical properties when used in an additive manufacturing build. And ultimately there needs to be enough market demand for the material.
New alloys are always being investigated by OEMs, manufacturers, and universities, but not all powders go to market. A material with a specific build parameter can be developed for a customer, but it might be proprietary or might not have a wide enough appeal to become part of the standard materials offerings.
CIM: What physical characteristics are important for an AM powder?
Snow: The shape of the granules is very important. They should be 100 percent spherical. And particle size and distribution comes into play. We work with particle size distribution of about 20 microns.
CIM: Should a manufacturer purchase powder from the OEM?
Snow: Powder can be purchased from the equipment manufacturer or an outside source. Some OEMs provide an assurance that their powders will perform with their machines. For example, our powder is offered into the marketplace as a prequalified lot of material. We add value to our powders by performing quality checks based on our specifications for material, consistent performance, and processing parameters. We design our systems around our materials and our materials around our systems so they work in sync.
CIM: What specifications make a component a good prospect to move from subtractive to AM?
Snow: In many cases we find that engineers, for example, are redesigning existing products and adapting them to additive manufacturing by lightweighting the original product. Front-end software allows for lattice structures to be implemented in the design to maintain the mechanical strength and properties and to take a significant amount of weight out of the product itself.
Also, we see part consolidation. Many customers are reducing the assembly and secondary manufacturing costs by taking an assembly of 10 or 15 parts that are brazed or welded together and consolidating them into one part. It streamlines the manufacturing process. Overall, laser sintering lifts the constraints of conventional manufacturing. Complex parts that are not achievable with traditional methods are now attainable via additive manufacturing. We look at this as being design-driven manufacturing as opposed to manufacturing-driven design.
CIM: Is there a difference between machining parts produced by AM compared to subtractive technologies?
Snow: There is really no difference in machinability. Parts produced with AM can be machined just like any other alloy. Treat additive-manufactured parts just like any conventional piece of barstock or material.
CIM: How does the material in an AM part compare to the material in a component produced by traditional technologies?
Snow: The material in an additivemanufactured part has less porosity, especially when compared to castings. There might be some surface porosity and an occlusion within the product, but the finished material will have a very high integrity and mechanical properties that are closer to the raw material than when working with other processes.
CIM: What can be done to avoid material occlusions?
Snow: If it is a really critical application, like for an aerospace component, many manufacturers will perform a secondary sintering of the component just to be sure that microporosity no longer exists.
CIM: How environmentally friendly is AM?
Snow: With laser sintering, nearly 100 percent of the powder that is not used, or in other words fused in the part, can be recycled. Unused material in the build chamber can be repossessed, reprocessed, and blended into the machine for another lot.
CIM: What else should manufacturers know about AM?
Snow: Unlike the subtractive manufacturing practices that have established design parameters taught in universities, AM has virtually no design restrictions. Very few rules have to be considered, so it offers new creative opportunities and provides design freedom.
We are beginning to see organizations, institutions, and universities developing additive manufacturing guidelines that will help engineers gain an appreciation for how things can be designed differently to gain the full advantages of metal fusion technology.
Additive Powders Mirror Standard Materials
Metal powders available for additive manufacturing and their typical applications include:
Maraging steel—18 Mar 300, a martensite-hardenable, tough tool steel, was developed primarily for the injection mold industry but is used to build a variety of mechanical parts. It is easily machinable, can be hardened to more than 50 HRC, has good thermal conductivity, and can be polished to a mirrorlike finish.
Stainless steels—The stainless series, including hardenable 15-5, is designed for general-purpose manufacturing. Powders like 17-4 and 15-5 are used to build medical instruments, functional prototypes, and small series products. Medical implants, watches and jewelry, the marine industry, and other applications where corrosion resistance is important are built from 1.4404.
Nickel-based alloys—INCONEL® alloy materials are used by the aerospace and jet engine industries because of their light weight, strength, and ability to withstand heat. UNS N06002 is used for components that have to withstand severe thermal conditions such as high-temperature turbines, combustion chambers, roller hearths, and supports in industrial furnaces.
Cobalt chrome—The strength and durability of the superalloys developed primarily for dental implants are finding applications in the aerospace industry.
Titanium—Lightweight and strength are desired for many parts for the aerospace and motorsports industries. Low-oxygen-content titanium like ELI is used for biomedical and demanding industrial applications.
Aluminum—Very weldable, lightweight die casting aluminum is frequently used for prototypes and to produce production parts for industries like motorsports.
subscribe now
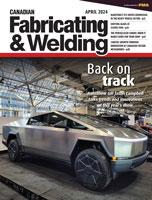
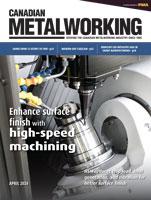
Keep up to date with the latest news, events, and technology for all things metal from our pair of monthly magazines written specifically for Canadian manufacturers!
Start Your Free Subscription- Trending Articles
- Industry Events
MME Winnipeg
- April 30, 2024
- Winnipeg, ON Canada
CTMA Economic Uncertainty: Helping You Navigate Windsor Seminar
- April 30, 2024
- Windsor, ON Canada
CTMA Economic Uncertainty: Helping You Navigate Kitchener Seminar
- May 2, 2024
- Kitchener, ON Canada
Automate 2024
- May 6 - 9, 2024
- Chicago, IL
ANCA Open House
- May 7 - 8, 2024
- Wixom, MI