- FMA
- The Fabricator
- FABTECH
- Canadian Metalworking
Playing It Safe With Machine Guarding
Separate workers from all moving equipment, including automation
- By Joe Thompson
- May 13, 2015
- Article
- Metalworking
Adoption of advanced industrial robots is on the rise around the world.
In fact, a recent study by the Boston Consulting Group (BCG) is forecasting an impending boom in the robotic sector. The study projects annual growth in the use of industrial robotics will rise to 10 percent from 3 percent, which could reduce the cost of labor by an average of 16 percent in the world’s largest exporting nations.
Of all manufacturing tasks that currently can be automated, robots perform only about 10 percent of the total number. This percentage is expected to rise to 25 by 2025.
Countries with large robotic installation bases, such as the U.S., China, Japan, and Germany, can expect the biggest returns. The BCG study reports that South Korea is expected to reduce its labor costs by as much as 33 percent, followed by Japan (25 percent); Canada (24 percent); the U.S., Taiwan, and the U.K. (22 percent); and Germany (21 percent).
As the manufacturing industry gets more automated, more focus will be placed on moving parts and material more safely and efficiently.
“There is a definite rise in the use of automation across many industries,” explained Eric Esson, national sales and marketing manager at Rite-Hite Machine Guarding. “In the manufacturing sector we see welding, machine loading and unloading, material handling, and part retrieval all becoming more automated.”
New products that enhance safety without impeding productivity are needed, added Esson.
“Safety products designed specifically for automated equipment are developed based on user needs, safety regulations, and modern shop environments,” said Esson. “New manufacturing methods mean new safety products are needed to make those processes operate safely and efficiently.”
Modern Safety for Modern Shops
“Most often we install a guarding system in a shop where one did not previously exist, for example, when a new machine is purchased. However, we also replace outdated safety devices with new technology,” said Esson.
Safety equipment, like any other form of technology, can become outdated and need replaced.
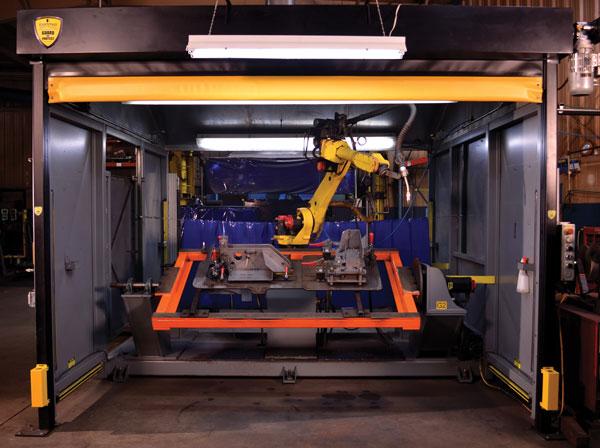
A robotic welding operator checks his work with the automated curtain in the up position. The robotic welding operation will not occur when the barrier is open.
“A manufacturing plant can be a dangerous place,” said Esson. “Safety devices are installed to help workers perform their tasks in a safe manner, while also aiding in productivity and enhancing lean manufacturing principles.”
The Canadian Standards Association (CSA) standards Z432-04, Safeguarding of Machinery, and CSA Z434- 14, Industrial Robots and Robot Systems, are designed to eliminate the common hazards associated with working with machinery and robotic systems.
To be compliant with the goals of the standards, safe- guarding devices must be constructed to prevent any part of the body from reaching a dangerous location. Simply put, protection needs to be more than a yellow line painted on the shop floor.
“One of the most common forms of workplace protection is a fixed guardrail system separating walkways in work areas,” said Esson. “Improperly protected or inadequately protected areas need to be dealt with, and there are several levels of safety devices that can be installed depending on the circumstances.”
To protect workers from the potential hazards that exist near machinery, some sort of barrier is needed. By creating a physical barrier, machine guarding can minimize physical dangers, as well as guard against weld flash and flying debris.
“In addition to physical protection, it also is important to reduce noise levels and remove fume from the air,” said Esson.
Access Granted
Quite often it’s not enough to just provide a full physical barrier. Machine and robot guarding requires access to the equipment, while still offering protection. In cases like these, industrial safety doors that restrict access to dangerous robot and machine movement should be considered.
Protection by separation helps separate and define work areas, walkways, and even areas such as loading docks. Creating a buffer zone around machines and robots can be accomplished in several ways. Some of the most common are:
- Safety fence. Safety fencing typically is easy to set up and move, and it can be used as machine perimeter guarding, perimeter guarding for welding areas, robot safety fencing, and conveyor system perimeter guarding, among others. Gates in the fencing allow access to the equipment where necessary.
- Light curtain. Safety light curtains detect when an object enters its sensing field. They are commonly used for machine guarding and are suitable for applications that require frequent and easy access to a point of operation.
- Retractable curtain. Retractable industrial curtains provide protection in areas where conventional industrial screens fall short. Retractable safety doors can be positioned closer to a hazard, reducing the total footprint of the manufacturing cell, including all safety zones. Curtains also guard against flying debris.
- Automated curtain. Automated curtains protect workers from machine and robot movement zones, but can be controlled electronically. These curtains also help to contain fumes, sparks, smoke, mist, flying debris, and noise from the manufacturing process, making them suitable for robotic welding cells, automated assembly, and palletizing/packing machinery
Automated barrier doors also typically feature a hold-down mechanism, which locks the door in the down position during operation. Rotary cam limit switches, encoder positioning, and variable-frequency drives control the curtain’s operating speed and position.
“It is important to adhere to all guidelines and keep employees safe during potentially dangerous operations,” said Esson. “Automated doors safely separate machine operators from the manufacturing process and can also be used to separate cells from the rest of the shop.”
During a welding operation, for example, the arc will not activate if the door is in the up position.
“If the door is down, it means the operator is currently working,” said Esson. “If it’s up, the operator could be performing setup or there could be a problem with the equipment. It’s an easy way for a supervisor to tell what’s going on by scanning the shop floor.”
Safety and Productivity
Identifying the need for hazard containment and the need to protect employees and equipment is important. When deciding on a machine guarding system, ask yourself the following questions:
- Does the guarding meet the minimum standard requirements?
- Does it prevent workers from making contact with moving machine parts and robots?
- Is all auxiliary equipment guarded adequately?
- Can safe, ergonomic operation of the machine be performed?
- Is the point-of-operation safely guarded?
Common applications and processes that require guarding include:
- Production lines
- Cutting systems
- Conveyor systems
- Packaging machinery
- Material handling
- Palletizing applications
- Stretch-wrap machines
- Machine tools
- Transfer lines
- Robots and factory automation
subscribe now
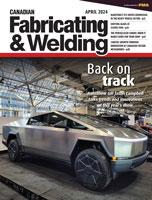
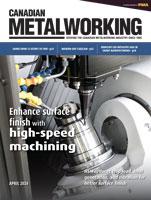
Keep up to date with the latest news, events, and technology for all things metal from our pair of monthly magazines written specifically for Canadian manufacturers!
Start Your Free Subscription- Trending Articles
- Industry Events
MME Winnipeg
- April 30, 2024
- Winnipeg, ON Canada
CTMA Economic Uncertainty: Helping You Navigate Windsor Seminar
- April 30, 2024
- Windsor, ON Canada
CTMA Economic Uncertainty: Helping You Navigate Kitchener Seminar
- May 2, 2024
- Kitchener, ON Canada
Automate 2024
- May 6 - 9, 2024
- Chicago, IL
ANCA Open House
- May 7 - 8, 2024
- Wixom, MI