- FMA
- The Fabricator
- FABTECH
- Canadian Metalworking
Lean Refreshed
Top 6 ways modern ERP systems and lean concepts combine to benefit manufacturers
- By Larry Korak
- July 9, 2015
- Article
- Management
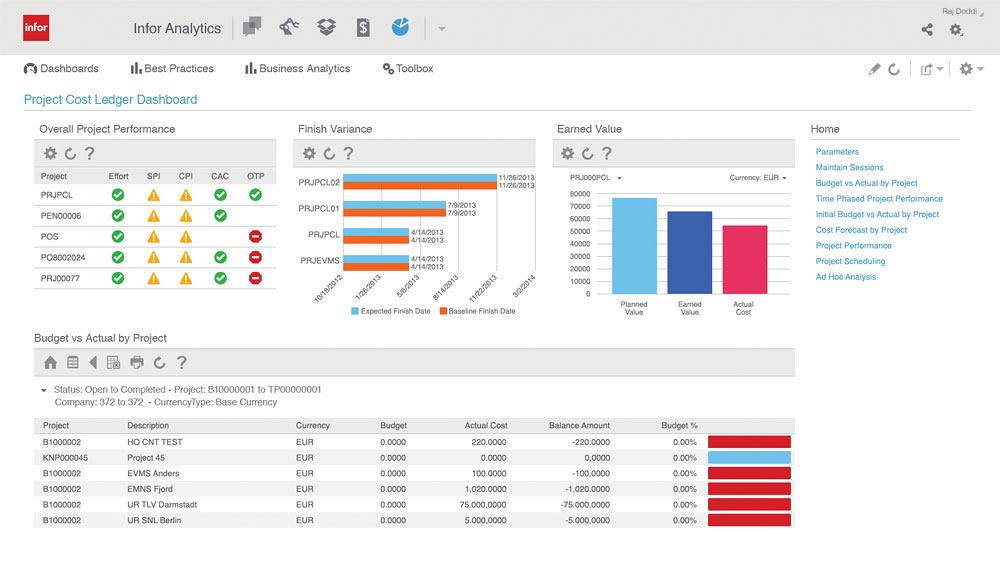
Modern ERP software has new tools to capture real-time data accurately, enabling production managers to forecast and plan accordingly, eliminating wasted time and effort. Photo courtesy of Infor.
Lean manufacturing, which originated as the Toyota Production System (TPS), is one of the most well-known process strategies in modern manufacturing. It migrated to the U.S. in the 1950s and began to draw serious attention in the 1980s. Since then it has become the industry’s default best-practice approach and has been widely adopted in manufacturing facilities worldwide.
But where does lean stand today? How do modern IT systems interact with lean strategies?
Lean manufacturing has two main building blocks: reducing waste and creating customer value.
Continuous improvement is the ultimate goal. To achieve this, manufacturers strive to eliminate information silos and optimize the flow of products and services through the entire value stream—across departments, processes, and equipment to customers.
Modern ERP systems are designed to help manufacturers achieve the same goal. When lean strategies and modern ERP capabilities are coupled, the result is exponential growth. Many lean strategists once considered the two strategies to be opposing principles. Today, however, the top techsavvy manufacturers have discovered there is actually a symbiotic relationship between the two camps. Working together, lean strategies and ERP systems create powerful synergies.
Is Lean Still Relevant?
Lean processes are still at the heart of most manufacturing operations worldwide. As the manufacturing industry recovers from the recession and moves into a growth phase, analysts are starting to once again pick up the lean dialogue and add layers to address the use of technology.
The manufacturing industry has changed dramatically since lean principles were first adopted, especially in the areas of manufacturing technology and information management. When many companies first rolled out their lean initiatives, the Internet was in its infancy, and few could imagine a workplace that included mobile devices, online portals for customers and suppliers, and realtime collaboration with suppliers on other continents.
However, it’s a quickly evolving global marketplace today with highly demanding customers. How do lean principles fit into this new manufacturing environment?
In the early days of lean adoption, IT managers and production managers often clashed, as they struggled to find the balance between big, powerful ERP systems and streamlined, minimalist processes with as few steps as possible. The monolithic ERP systems that tried to impose a one-size-fits-all structure were not always lean-compatible.
Early pioneers of lean systems pursued strategies to remove IT from production processes, viewing it as an additional step that could be “leaned out” of processes to remove waste. This philosophy may have had some merit in the 1970s when ERP technology was in its early stages, but, the speed of market changes and manufacturing complexity today make the technology mandatory, not an option.
6 Ways ERP and Lean Combine Forces
- Smart devices create smart production lines. Customer satisfaction is a key component of lean thinking. This is more important than ever now as manufacturers are expected to provide enhanced customer experiences, such as on-demand product customizations. Multiple process tactics and IT tools are required to make on-demand manufacturing feasible—and profitable—from product configuration to component subassembly, comanufacturing partnerships, and latestage assembly. Modern ERP software brings these concepts together into one streamlined process flow. Today’s highly flexible ERP system acts as the central nervous system, connecting process flows and making lean production attainable.
Modern data management makes lean predictive as well as reactive. Business intelligence is one of the key areas where ERP software and lean strategies coexist and align for improved performance. Since many of the early books on lean concepts were written, big data technology has dramatically transformed reporting and analytics. Now modern IT goes further to support lean initiatives by helping companies take proactive measures to minimize waste in the purchasing of raw materials and warehousing of products just in case unexpected orders come in.
Modern business intelligence (BI) software helps companies accurately predict market demands, rather than just report on historical transaction trends. Reporting tools are also easier to use, bringing key performance indicator (KPI) tracking to employees throughout the organization. This means purchasing agents and production managers can more accurately forecast order trends and plan accordingly.
Just-in-time inventory concepts evolve to “on-demand” manufacturing. Expectations for speed of delivery have drastically changed since lean strategies were first developed. At one time a six-month delivery wait may have been tolerated by customers; today, in some industries, six days or six hours may be too slow.
Just as expectations have drastically changed, supply chain tracking and planning have changed to be more insightful with clear visibility throughout the supply chain. Even an extended, global supply chain can respond with great agility. Purchasing and warehouse managers can use modern IT to manage complexity, minimize steps, and optimize resources.
Advanced shop floor operations support lean planning. The shop floor is where lean strategies are most prevalent. This, too, is where modern IT advances have drastically changed operational standards.
The two initiatives can be used in tandem to provide exponentially better production results. Best practices now include new production norms and higher standards of operational excellence for speed and value-add services. Early lean consultants didn’t address technologies such as 3-D printing, smart sensors, and the Internet of Things (IoT) for one important reason: These concepts were little more than visions and prototypes in early lean rollouts. In lean 2.0 these disruptive technologies can be leveraged to provide greater value, with less waste.
Embrace innovation without sacrificing efficiency and cost control. Can manufacturers reconcile disruptive innovations and lean efficiency? How can a manufacturer balance innovation, which brings some natural waste as ideas are tried and discarded, with the lean mandate to minimize waste? On the surface, the two precepts seem incompatible.
Manufacturers must strive to overcome this fallacy that branching into uncharted territories to develop new products is wasteful and against lean philosophies. Innovation can’t be curtailed, as it brings the next-generation breakthroughs that will continue to inspire growth and investment.
Disruptive technology brings some degree of waste as new systems and workflows continue to be refined until best practices are reached. Manufacturers are still on the upward slope of the learning curve, as they work to establish new best practices for on-demand scheduling and “printing” needed components, rather than manufacturing them. Lean concepts can be used to guide the workflows and keep waste in check, without totally restricting some tolerance for the trial and error and experimentation that come with any new approach.
- Reducing waste is an ultimate goal. ERP and lean share many goals, including waste reduction. From reducing excessive inventory to eliminating gaps in processes, both strategies strive to streamline operations and cut extra steps. This can include a range of tactics, from unnecessary structures to over-reporting and duplication of tasks. Removing unnecessary motions, from ergonomics to disparate IT systems, saves time, increases productivity, and, therefore, saves money.
Bringing Lean to a New Generation
A look back at lean’s history and forward to its future comes at an opportune time, as many of the early adopters of lean transformation projects are reaching retirement age. The graying of baby boomers is leaving gaps in the workforce that are hard to fill. These retirees likely include the managers and their production crews who sat through the eye-opening training sessions in the 1980s in which words like kaizen and kanban still sounded so strange.
Now a new generation of manufacturing personnel is being introduced to the lean vocabulary and striving to put the lean concepts in context for their jobs, their roles, and their priorities. This isn’t always easy, but it’s certainly necessary.
The lean manufacturing philosophy is so important, so entrenched in manufacturing today that it isn’t going away completely. It’s time to polish up some of the lean concepts and recognize that they are still relevant and still valuable to manufacturing.
When this lean 2.0 is paired with the power of modern ERP software, the potential is truly limitless.
subscribe now
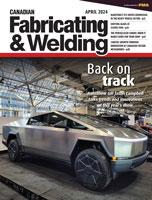
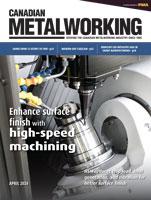
Keep up to date with the latest news, events, and technology for all things metal from our pair of monthly magazines written specifically for Canadian manufacturers!
Start Your Free Subscription- Trending Articles
- Industry Events
MME Winnipeg
- April 30, 2024
- Winnipeg, ON Canada
CTMA Economic Uncertainty: Helping You Navigate Windsor Seminar
- April 30, 2024
- Windsor, ON Canada
CTMA Economic Uncertainty: Helping You Navigate Kitchener Seminar
- May 2, 2024
- Kitchener, ON Canada
Automate 2024
- May 6 - 9, 2024
- Chicago, IL
ANCA Open House
- May 7 - 8, 2024
- Wixom, MI