- FMA
- The Fabricator
- FABTECH
- Canadian Metalworking
Technology Spotlight: Rolling With New Technology
Ontario machine tool builder creates modular plasma cutting machinery using roller pinions
- By Tim Dillon
- February 10, 2014
- Article
- Fabricating
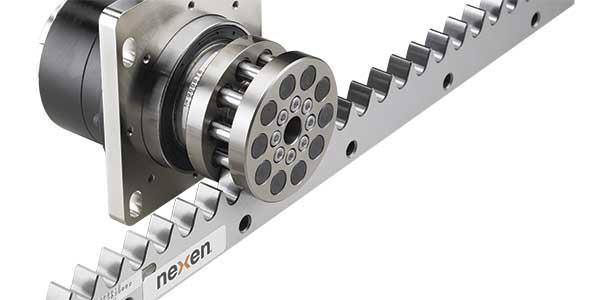
The roller pinion system uses bearing-supported rollers that minimize backlash and reduce downtime. They also do not require any clearance within the rack’s profile like the teeth of a rack-and-pinion system do.
Floor space varies from shop to shop, and building an addition can be expensive. This leads some fabricators to make purchasing decisions based on a machine’s size.
Pinnacle Industrial Automation, Guelph, Ont., builds modular plasma cutting machines for the profile cutting industry, with each machine tailored to suit the specific requirements and budget of its customers.
When the company started developing the new Whistler HP plasma cutting table, its engineers knew they needed to create a reliable, multipurpose cutter. One of the components the company knew would be critical to the success of the system was the drive system, which serves as the track for the plasma torch.
“A top-of-the-line plasma cutter needs to meet high standards, so this worked out really well for us,” said Pinnacle co-owner Dave Jones.
The goal was to create a productive, fully zoned downdraft table that could cut shops’ components. Because the table needed to be suitable for numerous industries and needs, the company also wanted to make the table modular, allowing shops to adjust table sections to customize their length.
To achieve accurate and reliable operation, Pinnacle’s design team incorporated with the plasma cutting torch linear-drive systems, AC brushless digital servo drives, high-precision gearboxes, and dual-drive technology powered by the newest CNCs.
However, the manufacturer did not opt for a traditional rack-andpinion system to move the plasma torch along the cutting table. To develop the machine, Pinnacle used a roller pinion system from Nexen, a rack-and-pinion alternative designed to eliminate backlash and increase accuracy for linear-motion applications.
Instead of utilizing pinion teeth to control the rack’s movement and positioning, the roller pinion system uses bearing-supported rollers that minimize backlash and reduce downtime. The rollers do not require any clearance within the rack’s profile like the teeth of a rack-and-pinion system do.
The roller pinion system creates only small amounts of friction during operation, and it does not lead to the jams that might occur in traditional rack-and-pinion systems.
These jams are the result of a single pinion tooth pushing off one side of a rack tooth and then immediately moving to the next side of the tooth. This problem does not exist when rolling movement is created because the pinions simultaneously engage several tooth flanks in opposing directions. It also allows clearance between the other teeth. This design helps to ensure continuous, smooth motion and minimizes production loss that results from equipment jams and the time and resources it would take to compensate for traditional linear-motion control errors.
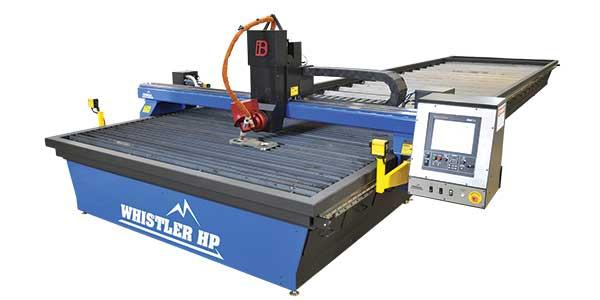
Pinnacle Industrial Automation, Guelph, Ont., builds modular plasma cutting machines for the profile cutting industry, with each machine tailored to suit the specific requirements and budget of its customers.
Lack of friction also means high heat is not generated, eliminating a situation that usually leads to component wear. This provides long equipment life and low maintenance needs. In certain applications, it can even operate without lubrication.
“It’s incredible just how fast and accurate the roller moves along the rack. You would think it would eventually get out of position after some time—or require a lot of lubrication— but it doesn’t,” said Pinnacle co-owner Paul Silva.
subscribe now
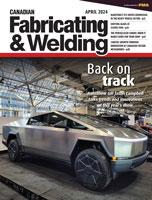
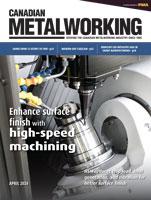
Keep up to date with the latest news, events, and technology for all things metal from our pair of monthly magazines written specifically for Canadian manufacturers!
Start Your Free Subscription- Trending Articles
- Industry Events
MME Winnipeg
- April 30, 2024
- Winnipeg, ON Canada
CTMA Economic Uncertainty: Helping You Navigate Windsor Seminar
- April 30, 2024
- Windsor, ON Canada
CTMA Economic Uncertainty: Helping You Navigate Kitchener Seminar
- May 2, 2024
- Kitchener, ON Canada
Automate 2024
- May 6 - 9, 2024
- Chicago, IL
ANCA Open House
- May 7 - 8, 2024
- Wixom, MI