- FMA
- The Fabricator
- FABTECH
- Canadian Metalworking
Warming up Reshoring
SRP brings manufacturing of infrared heaters home
- By Sue Roberts
- October 7, 2015
- Article
- Fabricating
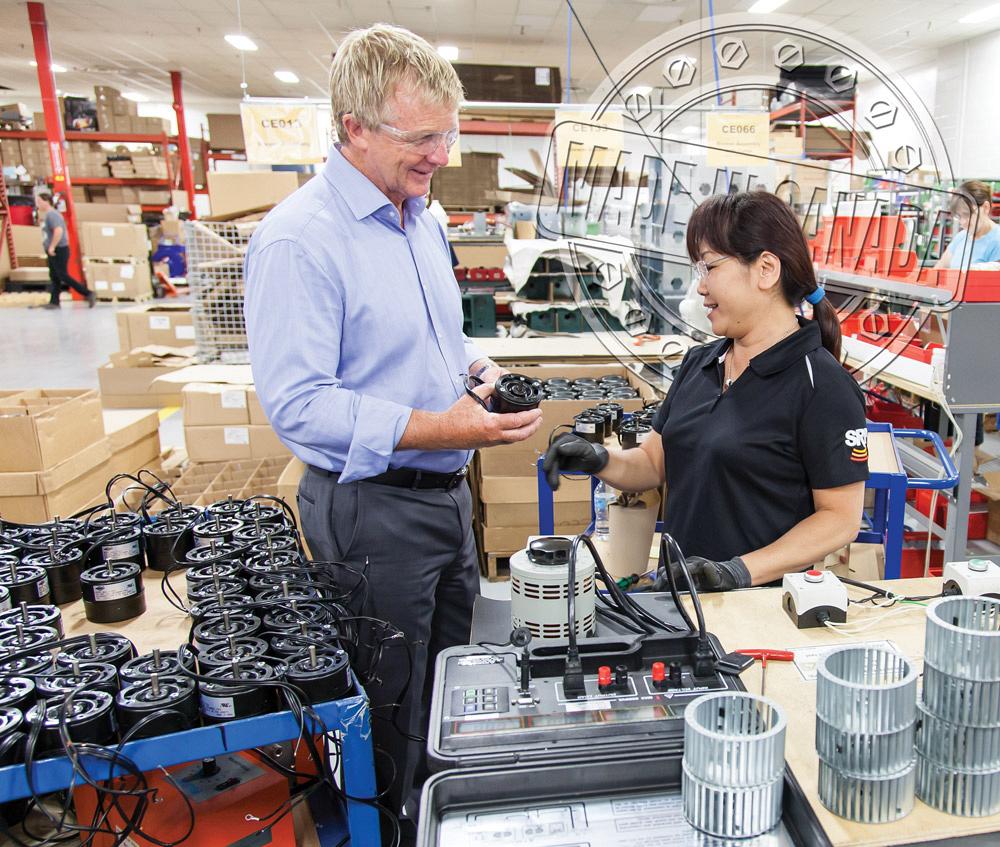
Kevin Merritt, president of Superior Radiant Products and IR Energy, discusses an order with Ann Du in the burner assembly workcell.
Infrared (IR) heating is a quiet, clean process. It doesn’t stir up dust with noisy fans. It can create comfortable, warm environments in stadiums, airplane hangars, and chicken houses and on patios and golf courses. It can eliminate moisture and thaw frozen earth at construction sites. And, similar to Superior Radiant Products (SRP®) in Stoney Creek, Ont., it is efficient and green.
A burner at one end of a 3- to 5-inch-diameter emitter tube generates a flame and forces hot gases through the tube. The heated tube emits infrared radiant energy that is redirected by parabolic reflectors positioned over the top of the tube. Floors and objects within the span of that redirected heat absorb the energy and warm the surrounding air. ASHRAE (American Society of Heating, Refrigerating and Air-Conditioning Engineers) estimates that IR systems save users 35 to 50 percent or more over conventional heating methods.
An idea about improving infrared heating technology sparked the beginning of Superior Radiant Products (SRP) 20 years ago. Kevin Merritt, president, said, “We knew there was room for improvement in the technology when we started the company. We developed our product from scratch, put it through CSA testing, and secured a number of customers willing to give us a try.
“Our goal was--and is--to provide high-quality, well-performing products at a price that is competitive with the lower-quality or lower-performing units in the market. Essentially, we want to offer more for the same price. We began with the Canadian market because that’s what we knew best and we just started growing.”
A “lucky break” quickly propelled the company forward. At the same time that SRP products were being introduced, backhoes were moving earth for the construction of Toyota Motor Manufacturing Canada in Cambridge, Ont. Cold weather and frozen ground, however, threatened to delay progress. “They couldn’t get the foundations in,” Merritt said. “So they found us on our website and asked if we could help. We developed an infrared heater to thaw the ground and keep them on schedule. It was lucrative for us and gave us a boost in our early days.”
More Products, More Exports, and Reshoring
Success has continued. SRP introduced multiple IR products, captured significant Canadian market share, expanded marketing into the U.S., and incorporated sister companies to support their markets and export activity. “Divisions of the company evolved. SRP takes care of the industrial and commercial building market. IR Energy was established to serve the outdoor heating market in 1999.
We incorporated Qingdao Thermpro Ltd. in Qingdao, China, in 2009, where we have a sales office and warehouse for infrared space heating and process drying technologies. Superior Radiant Products Inc. was established in Kennesaw, Ga., in 2012 to create a physical presence in the United States, where we now do all product finishing, distribution, and service for that market. We send semifinished product from here to the U.S., combine it with locally supplied components, and stock it for incoming orders. China and Europe orders ship from Stoney Creek.” More than 50 percent of production is exported.
Some components for the industrial and commercial heaters for the Chinese market are still produced in China because of too high import tariff fees. But, Merritt said, all of the R&D and core components for those products come from the Canadian operation. Low labor costs, a consideration at one time, is only one of the many factors to consider when manufacturing abroad, he added, and the gap between Canadian and Chinese wages has been shrinking. Quality control, another key consideration, is much easier to ensure when manufacturing in Canada. “QC needs to be rigid. We find that components coming from suppliers who source elsewhere—Mexico, China, Vietnam—require more incoming inspection and testing. In the past we could assume a component was good, but we can’t do that anymore. We’ve incorporated multiple levels of inspection on components we have not brought in-house.”
SRP’s manufacturing relationship with Chinese suppliers has recently changed. For several years the majority of SRP’s patio heaters were made in China. This past year the manufacturing of those high-end patio heaters has been reshored. The now made-in-Canada product line, using internal resources and local sub supply of items that require spinning processes, launched in October 2014. Components such as valves are all of high-end North American or European origin.
This year the company added CE approval to its existing CSA and ISO 9001:2008 certifications, so products completely manufactured in the Canadian plant can be shipped into Europe. SRP products are finding their way to Germany, Ireland, Spain, and Turkey and sales into other European markets are now possible. The CE certification will also result in more reshoring as the company pulls production in Germany back to Canada.
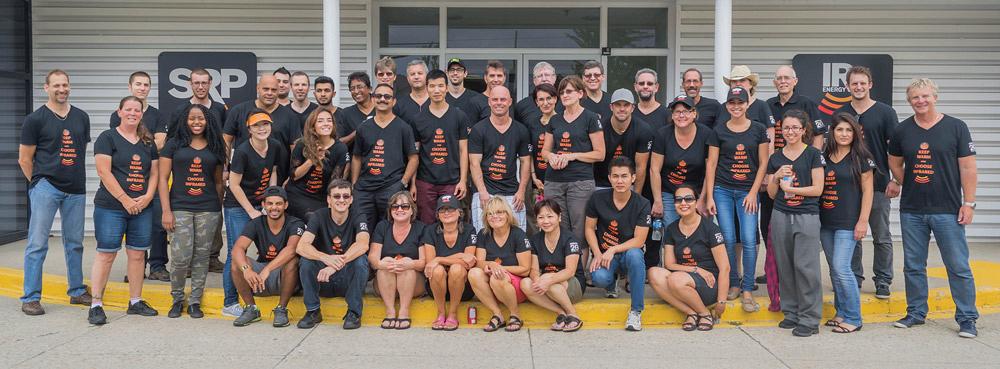
SRP employees celebrated the company’s 20th anniversary at a barbecue held at the new facility in Stoney Creek, Ont. Photo courtesy of SRP.
A Larger, Leaner Shop
2014 marked another milestone for the company. It moved to a new 43,000-sq.-ft. facility a short distance from where it started in the back of a strip mall. “In our previous location we would knock out neighbors as we expanded. As the years progressed we grew in a long, skinny line. We vertically integrated different pieces of equipment and put machines wherever there was space to bring manufacturing in-house,” Merritt said.
More than manufacturing elbow room was changed with the move. Additional hires hiked the number of employees to 60 across all locations, and the company adopted a lean philosophy and new enterprise resource planning and material requirements planning systems.
“When we moved we wanted the right shape to the factory. A lean consultant helped us design an efficient work flow so when materials come in the door, they never have to move more than a minimal distance while going from one process to the next. But getting the machines in the right positions was just the beginning,” Merritt said.
“We were working from spreadsheets before we had lean in place. We spent about a year helping our people learn about lean, 5S, and all those things as we planned the expansion and made the move. We restructured the organization internally and added employees to implement the ERP/MRP system. We also implemented Microsoft Dynamics® to help us find new ways of doing things. We instilled a culture of continuous improvement.
“It was a real challenge but today we are miles ahead of where we were even a year ago because of the lean concept. And we’re still advancing. “We just switched to electronic work orders--eliminated routing paper through the shop. This has created a real improvement in efficiency, especially when customers change their minds midstream. We have to be able to revise orders quickly and not worry about communicating the change. With the paperless system we can change-on-the-fly and not worry about a mix-up.” Each product moving through the system is made-to-order.The next change underway is implementing bar coding throughout the facility to improve the timeliness of information.
Producing Made-to-Order Heaters
Truckloads of stainless steel, sheet, and tube and aluminized and galvanized steel arrive JIT to be transformed into components to fit multiple SRP and IR Energy products. Primary infrared components are the burner/control box, emitter tubes, reflector, couplings, and hangers.
Emitter tubes from 10 to 70 ft. long are produced for heaters from hot-rolled, aluminized, or stainless steel, or aluminized tube that has been heat-treated to create a gray/black color that increases the tube’s ability to emit heat outward. Tube sections for the suspended industrial and commercial heaters are connected with 12-in.-long band couplings that can be removed and reinstalled to relocate the heaters. Heavy-duty, chrome-plated hangers are placed 10 ft. apart to support the tube heaters.
Reflectors, constructed of 24-gauge aluminum because of its good reflective properties, are bent in a shape unique to SRP. The company is the only infrared supplier offering a 10-sided reflector with 100 percent efficiency. “Our concept is to preassemble some generic parts and then final the unit to the customer’s order,” Merritt said.
Components move from the shop’s CNC turret punch press, at the heart of production, to the CNC brakes, and on to spot welding. Painting is the only process that is not done in-house. Then comes assembly.
Customization is available and has led to new products more than once. “We listen to customers and as a result we have developed some products for niche markets,” Merritt said. “A customer will want to tweak a product for an application and suddenly there is a new product and a new market.
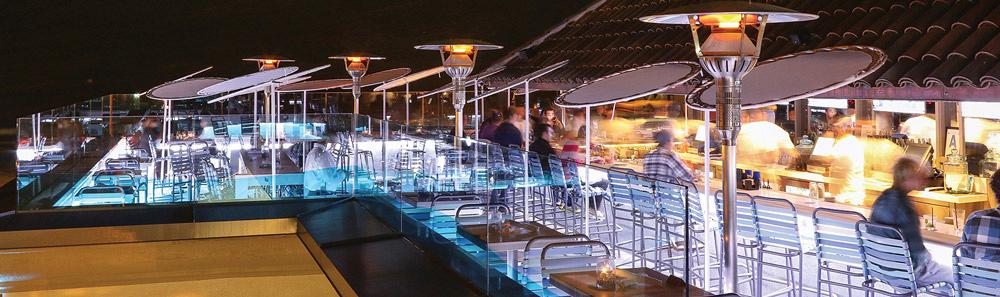
EvenGLO® gas patio heaters from IR Energy Inc., SRP’s sister company, warm the evenings at Belmont Park, a beachfront amusement park in San Diego, Calif. Photo courtesy of SRP.
“For example, the standard tube heater needed some changes for an ag market customer. The high amount of moisture in the environments and wash-downs required the burner box to be watertight. We put silicone around the welded joints as an added protection, used a weatherproof ignition control, and made a few other minor changes. It’s the same heater with a few tweaks. We then adopted these same changes to our even heat L-Series and ended up with a winner.
“In the last few years the chicken farms have been learning about and purchasing this product. The farms, and there are a lot of them, are being upgraded to the latest technologies.”
Measurement of Success
“So here are two challenges for us,” Merritt said. “One is to continually improve the efficiency of the products, and that is something we know we can do. The other is to create market acceptance of the improved efficiency and provide a way to measure the improvements to allow customers to compare old to new and brand to brand.”
SRP is one of several companies that joined together to create an infrared efficiency standard. “A fair number of competitors collaborated over many years to develop a North American standard based on European standards,” Merritt said. “Industry standards work to everyone’s benefit. And I don’t mind if the government steps in and sets minimum standards because I believe in working to develop products that are as efficient as possible.
“It may eventually cost more to produce to the standards, but it will result in better, more efficient products. We are quite excited because we know we will be in good shape. The standards will enable us to show that one infrared heater is actually more efficient than another, and that allows us to put more value into the product.” The new standards should be introduced to the North American market in the next year or so.
Expanded product lines and markets are also in the near future. Merritt said that several infrared products are in the lab, ready for introduction in North America—all developed to increase and improve heating efficiencies. Taking full advantage of the National Research Council’s Industrial Research Assistance Program has enhanced the company’s R&D efforts.
Broadening sales into the Southern Hemisphere is in the works to help smooth out the seasonality of the product. “We are quiet during the summer and start to get busy at the end of August. We get really busy November through January then begin to trail off. We want to find a market that is countercyclical—either a product that is sold in the summer or expand sales into the Southern Hemisphere. South America is a good potential market for us. We’re already selling in Mexico and Colombia, and we’re dabbling in Peru and Chile.”
Photos by Adamski Tomasz Photography unless otherwise noted.
- More than 1,600 heaters in one building in China.
- More than 1,700 aircraft deicing units for a project at John F. Kennedy International Airport in New York.
- 430 burners and over 5 miles of tube and reflector for the U.S. Army Garrison Fort Gillem in Georgia.
- 2,160 linear ft. of custom-engineered, in-series burner systems for perimeter heating on the concourse the level at BC Place Stadium in Vancouver.
subscribe now
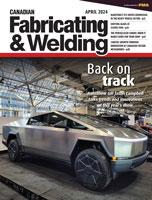
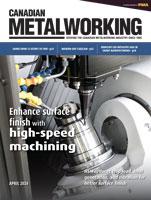
Keep up to date with the latest news, events, and technology for all things metal from our pair of monthly magazines written specifically for Canadian manufacturers!
Start Your Free Subscription- Trending Articles
- Industry Events
MME Winnipeg
- April 30, 2024
- Winnipeg, ON Canada
CTMA Economic Uncertainty: Helping You Navigate Windsor Seminar
- April 30, 2024
- Windsor, ON Canada
CTMA Economic Uncertainty: Helping You Navigate Kitchener Seminar
- May 2, 2024
- Kitchener, ON Canada
Automate 2024
- May 6 - 9, 2024
- Chicago, IL
ANCA Open House
- May 7 - 8, 2024
- Wixom, MI