- FMA
- The Fabricator
- FABTECH
- Canadian Metalworking
Roll Forming Adjusts to Customer Demands
Speed, efficiency, and quick changeovers challenge roll forming machine engineering
- By Jim Austin
- June 15, 2015
- Article
- Fabricating
Roll forming manufacturers face pressure from their customer base to provide equipment and answers that 10 years ago seemed unlikely.
“You would think an 80-year-old industrial technology that simply bends metal in motion would reach a saturation point in its advancement,” said Joe Repovs, founder of Samco Machinery, Toronto. “After all, the principles of metal forming are well-established and somewhat rudimentary. Yet, speak to any of the roll forming industry leaders today and you will soon learn of a different perspective.”
Time is money, and roll forming manufacturers appreciate that as much as anyone.
“The roll forming industry has definitely changed,” explained Jaswinder Bhatti, vice president of applications engineering at Samco. “Roll formers used to run at relatively slow speeds, running with the use of very few electronics. Today the speed has picked up to the point where it’s impossible for the operator to nest parts manually.”
So how do operators handle this new challenge?
Whether a product coming off the roll former is being nested for another process or is ready for packaging, operators now need to handle it at a much higher speed. One common method is to add staff to try and keep up with product.
However, some forward-thinkers in the roll forming industry have turned to material handling equipment as an evolution in the industry. This equipment is capable of packaging product or preparing it for the next process.
“High-speed roll formers have changed the way Samco and other roll forming manufacturers think,” said Bhatti. “Material handling never was a part of the roll forming process. Now it’s a big, big part of the overall process.”
Bhatti said this evolution has been a quick one—all within the last 10 years. In that same time span, customers also started asking about more complex shapes and for their lines to do more.
“With roll forming now, we try to make every process a part of the line,” said Bhatti. “Whether it be prepunching or postpunching or some other process, roll forming is not the only process customers are looking for. They’re looking for a full system, a finished product.”
Industry Expectations
Customers aren’t afraid to ask for anything. Many are looking for machinery that can bend and form thicker material and form more complex shapes. Material handling equipment must be developed to take quickmoving product from one process to the next.
“It’s technically challenging, but a line may include multiple roll forming stations to accommodate the more complex shapes,” said Bhatti.
Another trend is the demand for quick changeovers. Customers want a machine that can produce multiple variations of a product with minimal machine adjustments. Bhatti calls this a new, fast-moving trend.
Manufacturers today don’t necessarily want to mass-produce. They want to produce limited numbers and move on to something else.
Adding Electronic Systems
Roll former manufacturers are meeting these demands with machinery that can reset itself automatically. The operator may only have to change the coil.
“There has been an evolving interdependence of electromechanical systems to produce a wider array of profiles for increased capacity utilization,” explained Gerry Birmingham, vice president of engineering at Samco. “With the introduction of devices such as encoders, sensors, servomotors, and electronic data capturing devices in an overarching closed-loop communication structure, singlepiece production flexibility was born. We are now manufacturing lines that are capable of discrete product sequencing.”
The collateral benefit of a common communication structure is greater diagnostic levels as well.
“Advancements now enable manufacturers to provide remote dial-in access support down to the drive level. It’s possible to virtually troubleshoot at a sophisticated level from anywhere in the world. In the past, if something went wrong, we were not able to troubleshoot unless we traveled to meet the customer,” said Bhatti. “Now we can install remote access capabilities in every line. Roll form manufacturers can monitor the machine and access the problem with the help of electronic sensors. If something is covered with dirt, we can tell them to clean it off. If something needs adjusting, we can tell them that as well so they can get back to business.”
Higher production rates and profile flexibility have caught the attention of other industries, according to Repovs.
“These advancements can be used to convert products typically produced in traditional brake presses and progressive stamping. They have expanded into automotive, rail, bus, metal building products, office furniture, HVAC, white goods, wire management systems, shelving, racking, garage door components, grain bins, metal roofing and siding, and framing products,” said Repovs. “The list continues to grow.”
It was even less than a decade ago, said Repovs, that forming composite material in a roll forming process was considered a radical idea.
“Today, lightweight, high-strength, multilayered panels for the trucking industry are formed in production volumes,” said Repovs. “Electronic error checking and highly accurate measuring systems can be incorporated into the line for advanced statistical data capturing and quality monitoring.”
Other industries are seeing the benefits too. For example, in the garage door industry, manufacturers can produce infinitely flexible, low-volume front and back skins. Multiple flange heights, a wide array of profile widths, and ribbing and grooving can be systematically produced in the line sequence.
“The guided conveying, slitting, and roll forming can be repositioned for each sheet without stopping the line. This system permits immediate inline assembly without additional handling,” said Repovs.
The steel framing industry also has adopted this type of automation. The stud industry, as it is commonly called, offers approximately 80 products with different gauges, web widths, flange heights, and flange returns.
“The older machinery in this industry required manual tool changes and adjustments when any of the above parameters required a change,” said Repovs. “Thanks to the electronic and mechanical enablers, changes to the process can be achieved on the computer screen and in full automation.”
The technology is not done changing, either.
“On the far side of the inventive technology is the emerging use of adaptive motion control,” said Birmingham. “Years of significant investment into the development of complex computer software and mechanical systems can articulate independent inline roll forming tools. Product development trials are proving that 3-D shape forming technology may one day surface as a commercially viable option.”
subscribe now
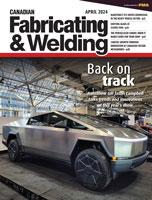
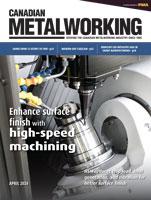
Keep up to date with the latest news, events, and technology for all things metal from our pair of monthly magazines written specifically for Canadian manufacturers!
Start Your Free Subscription- Trending Articles
- Industry Events
MME Winnipeg
- April 30, 2024
- Winnipeg, ON Canada
CTMA Economic Uncertainty: Helping You Navigate Windsor Seminar
- April 30, 2024
- Windsor, ON Canada
CTMA Economic Uncertainty: Helping You Navigate Kitchener Seminar
- May 2, 2024
- Kitchener, ON Canada
Automate 2024
- May 6 - 9, 2024
- Chicago, IL
ANCA Open House
- May 7 - 8, 2024
- Wixom, MI