- FMA
- The Fabricator
- FABTECH
- Canadian Metalworking
Form-Fitting Bending Cells
Small parts flow from downsized press brakes with integrated automation
- By Sue Roberts
- February 25, 2015
- Article
- Fabricating
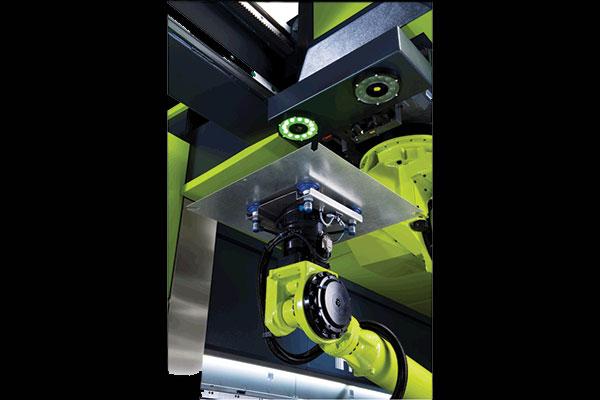
A vision system and a positioning table are standard on R-Brakes to square a blank before bending. Photo courtesy of Westway Machinery Ltd., Canada’s exclusive distributor of SafanDarley equipment.
Origami, the Japanese art of folding paper into a form, can be awkward. Try making a series of crisp creases, in the proper places, in the correct sequence, in a small piece of paper. Fingers or hands that are too big or clumsy can get in the way.
Change the medium from paper to a 12- by 12-inch or smaller piece of metal and fold it on a press brake. Using big equipment can make the process downright problematic. When you add robotics to the mix, the size of the arms and end-of armtooling can impede getting close enough to the brake to get the job done. If automation to change brake tooling is part of the process, it may need to slim down to reach behind and in-between what can be a smaller access area.
Downsized Cells
Manufacturers are taking the clumsiness out of bending petite parts. Small pieces of metal are being tucked into brakes with as little as 35 tons of bending power and bending lengths no longer than 4 feet. They are being paired with robots that have thinner arms to fit into compact spaces and customized end-of-arm tooling to daintily grip and maneuver parts and, in some cases, to change their own end-of-arm tooling. Automated brake tool changers are losing bulk to sneak into tight spaces. Added together, these features create small-part bending cells that smooth the process.
Like the small parts, the cells are compact. The jobs that are appropriate for the cells don’t require press brakes with the lengths or widths of their larger counterparts or beefedup structures to support heavy tonnage capacity. Likewise, the size of the robots and their tooling, while still robust, can be smaller because they handle less weight. The size of other automation components, like those involved in some load and unload systems, follows suit.
Moving Into Job Shops
On the other hand, functionality has increased, making the cells logical, profitable additions to a company’s capabilities. Fully integrated systems that used to be limited to bending batches in the thousands are upping small-part bending productivity in more job shops.
“In the past automated bending systems didn’t have tool changers or gripper changers, so there was quite a bit of manned setup between jobs,” said Scott Ottens, bending product manager, Amada America Inc., Buena Park, Calif. “For that reason you would see these systems only in OEMs or shops that had long runs. But with the full automation, we are seeing these cells going in anywhere.”
A small-parts bending cell will let jobs run operator-free or lights-out, which Ottens said can double output and save 90 percent of labor. “There’s some labor at the beginning of the day getting the jobs set up and the tables loaded, but then the operator is done. Our system has four tables that can be loaded so the system can automatically go from job to job.”
Small-scale Automation
Mauricio Gutierrez Matta, area export manager for SafanDarley B.V., Lochem, Netherlands, said, “The main reasons to robotize any bending process, including those for small parts, are to increase throughput and save on operator costs. The bending speed remains the same whether automated or not, but with automation the material handling time is consistent so productivity increases.”

End-of-arm tooling for the robots integrated with R-Brakes is customized to meet specific application needs for automated bending of small parts. Photo courtesy of Westway Machinery Ltd., Canada’s exclusive distributor of SafanDarley equipment.
The robot on SafanDarley’s 100-ton, 10-ft. R-Brake 100T-3100 is mounted on a traverse across the top of the press brake, although the brakes can be run in a manual mode as needed. The floor in front of the brake is available for sheet-feed and -discharge tables. The smallest robotic arm carries up to 110 pounds.
“We also offer a small robot cell for small parts with the robot mounted at the front of an E-Brake,” Matta said. “In general, all parts that can be made on the R-Brake can be made on the EBrake.” The servo-electronic E-Brakes have pressure forces beginning at 35 tons up to 130 tons. Lengths are available 4 ft. to 13 ft.
Amada offers a family of EG AR small bending cells. The smallest brake has 60 tons of power and a 4-ft. rail. The largest in the series has a 14-ft. rail with 240 tons of bending force. “These systems have automatic tool changers that are mounted to the brake. The robots grab and bend the blanks,” said Ottens.
Customization Is Standard
Robot end-of-arm tooling is customized to allow a firm grip on small sections of metal. Two types of tooling work with the Amada small-cell robots, both designed with clearance to reach over a part and grip a small bend. “One hand is a normal tool with a little, wide jaw. The other one is the microhand for very small parts. We change hand configurations to whatever the customer’s part requires,” Ottens said.
Software advantages in place for programming large-part cells, such as offline programming, are repeated for small-part cells. One difference, however, is that fine-tuning programs at the machine for small parts is easier because the blanks are more stable.
“The software looks at a blank as a rigid piece of material, and that’s not the case with larger blanks. They can have some sag to them so you have a little more teaching to do before starting a job,” said Ottens. “With a smallsized machine working with small blanks, there is very little material sag so little programming adjustment is required.”
Matta said that safety is an added advantage to using automated cells because the operator doesn’t physically support the small blank during the bending process.
Ottens agreed. “Imagine trying to bend a 11⁄2- by 3-in. part. The operator’s hands are real close to the tool zone, and it can be hard to hold the part during the bend. Fingers can get pinched between the part and the tool.”
Match Cell to Part Size
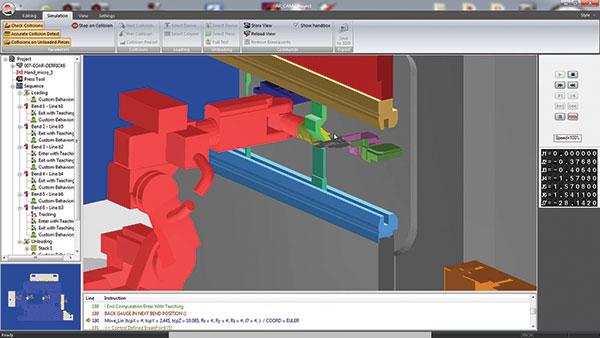
AR (Automated Robot) CAM allows 3-D programming for Amada’s EG AR and verifies a part’s feasibility before beginning production. Illustration courtesy of Amada America.
Small grippers can be mounted on robots designed for larger systems, but they may not work efficiently or even be able to make the bends. “Sizing has to be involved based on the family of parts to get the best results from an automated system mainly because of clearance reasons,” Ottens said. “A bigger, thicker robot designed to handle heavy parts may not be able to get close enough to the brake to allow small, precise bending.”
Before investing in a small-part manufacturing cell, Matta recommends that a company consider three things to determine ROI: space available, the usual batch size, and the number of tooling changes during an average shift.
Ottens said to also look at the complexity of the parts. “There are actually quite a few bends that the robot can do that an operator can’t accomplish without special fixturing or jigging. I’m talking 15 or 16 bends on a very small part. There are cases where the robotic cell can produce more complex parts than a human.”
subscribe now
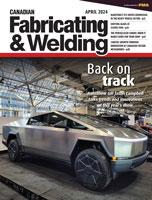
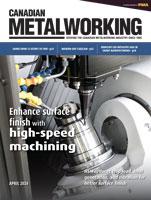
Keep up to date with the latest news, events, and technology for all things metal from our pair of monthly magazines written specifically for Canadian manufacturers!
Start Your Free Subscription- Trending Articles
- Industry Events
MME Winnipeg
- April 30, 2024
- Winnipeg, ON Canada
CTMA Economic Uncertainty: Helping You Navigate Windsor Seminar
- April 30, 2024
- Windsor, ON Canada
CTMA Economic Uncertainty: Helping You Navigate Kitchener Seminar
- May 2, 2024
- Kitchener, ON Canada
Automate 2024
- May 6 - 9, 2024
- Chicago, IL
ANCA Open House
- May 7 - 8, 2024
- Wixom, MI