- FMA
- The Fabricator
- FABTECH
- Canadian Metalworking
Tooling Organization Means Punching Optimization
These tips will keep turret punch presses running efficiently
- By Dennis Lowry
- December 1, 2009
- Article
- Fabricating
Turret punch press uptime will increase if you know your process capability, manufacture products within that capability, and optimize the layout of your tooling. It also will increase if you optimize programming, design, and tooling. It also is important to maintain proper die clearance and alignment of the press station.
Turret punch press uptime can be increased if you know your process capability, manufacture products within that capability, and optimize the layout of your tooling.
A process that can't produce the desired result reliably will cause waste as people struggle to make satisfactory parts; spend extensive time on setup; and lose productivity because of overly cautious operation, such as by running the press too slowly.
One of the best ways to ensure punching uptime is maximized is to concentrate on design for manufacturability (DFM). DFM is a cooperative effort between the product design engineering team and the manufacturing team, with both working together to develop the lowest-cost product design. The manufacturing group must communicate process capability, and the design group must communicate design intent while justifying the features of the product design. This iterative process becomes more efficient and effective with each product DFM as the team members better understand each other's responsibilities and capabilities.
Two ways to accomplish DFM are to design the product rationally and incorporate creative programming.
1. Design the Product Rationally. Press uptime also can be increased if you minimize the variation in similar sizes and shapes of holes. It is not uncommon to see round punches in increments of every 0.001 to 0.002 in. in diameters from 0.098 through 0.394 in. Decreasing the variety of standard-shape tools simplifies tool storage, maintenance, and press setup time.
2. Incorporate Creative Programming. Creative programming of parts can go a long way in increasing press uptime. For example, installing a special-shape tool, such as one used for some complex corner notches, can potentially eliminate nibbling with other tools. Excessive nibbling causes premature press wear, tool wear, punching debris, and lower-quality parts. Nibbling should be eliminated whenever possible because it will increase press uptime.
DFM is only one method of improving punching machine efficiency. Another means is improved punching tool organization, which can have an almost immediate impact on punching performance.
5 Ways to Optimize Tooling
1. Use a Standard Turret Layout.Develop a standard turret layout for commonly used tools, and provide programs that use those tools in the designated stations consistently. Do not program using a standard tool in a different station because this increases non-value-added time to change the tool or program at the press. It also increases the risk of error. When tools do need to be installed for the next job, locate them as close to each other as possible to help decrease setup time.
A standard turret layout is based on keeping general-purpose tools and commonly used tools resident in the press, each in a specific station location. Tools that need to be changed for the next job can be located close to each other in the turret, making it easier to install them.
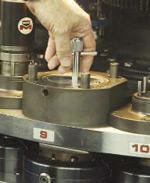
Tool alignment takes just minutes using the correct alignment tool and ensures quality parts while minimizing tool damage and wear.
The white board "map" of Turret 4 (Figure 1) shows how a shop can organize tooling. The tools that have labels are part of the standard turret layout, and the stations that are empty or labeled with red writing are the variable tools that are installed and removed based on the job requirements. The programmers must know where the resident tools are and program to use those tools in their correct locations in the press. The variable tools and their locations also are specified by the programmer to help operators locate those tools in the press quickly.
2. Control From the Toolroom. Look for ways to keep your tooling organized when preparing for a changeover to the next job. Having a toolroom to organize, maintain, and prepare tooling for each production order will change complex press setups into simple tool installations (Figure 2). This eliminates wasting time looking for tools and time spent maintaining tools that were not put away in a ready-to-use condition. It also ensures the correct tool and proper die clearance are being used for the job.
Toolrooms should be organized in such a way that the tools are well-labeled and easily located (Figure 3). All tools in storage must be ready for use, and tools that have reached the end of their life must be discarded. To get there and stay there requires discipline and guidelines.
3. Minimize Variation in Tool Styles. To increase press uptime, minimize the variation in the number of tool styles that you use. Many different tool designs and revisions have occurred over the years. Use a flexible system that can accept various manufacturers' tooling to simplify tooling assembly and decrease the level of knowledge needed to perform tool changes and press setups.
4. Install Quick-change Tooling. Use a tool style that enables quick, precise setup and easy adjustability. Quick-change tooling is intended to minimize the time required to prepare and install the tool into the press. It has unitized construction to simplify the assembly by decreasing the number of component parts.
An example is an original-style, thick-turret, 1 1/4-in. station punch assembly, which comprises a punch head, stripping spring, and spring retainer at the top of the assembly. The punch head is a clamp of sorts that provides a striking surface for the press, but it also sets the length of the tool. Quick-change tooling unitizes those three components into a single subassembly with added features such as toolless length adjustment. Make the tool easier to assemble and adjust to the proper length, and you will decrease tool changeover time.
5. Schedule Frequent and Proper Tool Maintenance. Maintain your tooling properly to keep it in working order and keep your press running. The worst time to maintain a tool is when the tool tells you to. It is much more efficient and effective to sharpen a tool when it's convenient for you. This may mean tools are sharpened more frequently, with smaller amounts removed per sharpening. But it prolongs tool life because properly maintained tools can run for long periods of time between sharpening.
Follow these guidelines to assist with maintenance of tooling:
- Sharpen frequently
- Use coolant
- Observe proper setup practices
- Establish written maintenance procedures
Die Clearance and Press Station Alignment
Die clearance is a function of the material type and thickness being punched. Incorrect die clearance results in slower press speeds, accelerated tool wear, punch point galling, and lower-quality finished parts, so be sure to use the proper die clearance for your material type and thickness.
If you incorporate the toolroom concept, the proper die clearance will be presented to the press operator for installation and use with the next job. A good lean work practice is to develop a standard die clearance chart and train all press operators to understand why it's important to use the correct clearance. This will help them understand problems that occur when die clearance is incorrect.
Press uptime will be increased if accurate station alignment is maintained. This will ensure the punch enters the center of the die, resulting in even die clearance around the cutting edge and the best possible tool life. Extremely accurate products are available to help maintain this important relationship.
Alignment tools should be used as soon as misalignment is evident. The alignment tools refresh the precision orientation of the upper and lower tools, allowing the punch to enter the center of the die. You can detect the need for alignment through tool wear, part burrs, and scrap inspection. If possible, align the station as a preventive maintenance measure to prevent poor-quality parts and damage to tools.
Add Value at the Punching Process
Ultimately, it is most important to maximize the value added to the product when it is being processed in the press. Increasing the value added to the product can produce dramatic improvements to downstream processes. For example, most fabricators have processes following punching, and they could improve downstream efficiencies if they incorporated fabrication directions directly on the part with the punch tooling. Complex bend angles, the order of the bending operation, directions, and locations for the installation of pressed-in or spot-welded hardware can benefit postpunching processes.
Find opportunities to use your punching process to improve the entire manufacturing process, and you can increase the overall quality of the product and the productivity of your workers and equipment.
For more information, visit www.mate.com.
Related Companies
subscribe now
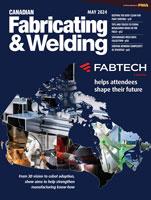
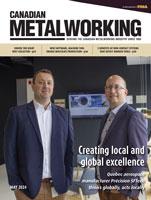
Keep up to date with the latest news, events, and technology for all things metal from our pair of monthly magazines written specifically for Canadian manufacturers!
Start Your Free Subscription- Trending Articles
- Industry Events
Automate 2024
- May 6 - 9, 2024
- Chicago, IL
ANCA Open House
- May 7 - 8, 2024
- Wixom, MI
17th annual Joint Open House
- May 8 - 9, 2024
- Oakville and Mississauga, ON Canada
MME Saskatoon
- May 28, 2024
- Saskatoon, SK Canada
CME's Health & Safety Symposium for Manufacturers
- May 29, 2024
- Mississauga, ON Canada