- FMA
- The Fabricator
- FABTECH
- Canadian Metalworking
It’s Not How You Start, It’s How You Finish
How your grinding wheel selection affects cost, safety, finished product
- By Bob Costa
- June 4, 2015
- Article
- Fabricating
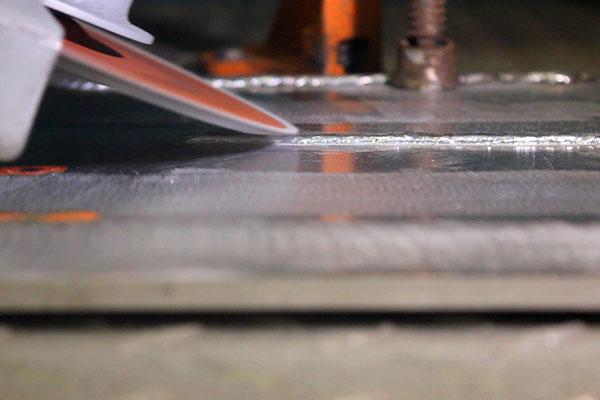
When evaluating a wheel, you must consider the durability of the abrasive, not just its performance in removing material.
Metal finishing is a complicated business, but abrasive selection doesn’t have to be. By knowing the differences between abrasives, you can produce more accurate bids, more accurate time estimates, and keep your organization running at peak efficiency.
Metal fabricators often struggle when bidding on jobs, trying to account for every factor. But what they don’t realize is that one of their variable costs actually is easier to estimate than they think.
Abrasive wheel selection can have a large impact on finishing operations, and on a fabricating business as a whole.
Bidding a Job
When you are putting together a bid, estimating items such as materials cost is relatively easy, but where a big X-factor comes into play is estimating labor. One reason that estimating labor is a challenge is the complexity involved with finishing.
Fabrication and welding labor costs are predictable, but estimating the time it takes for the gradual, multistep process of finishing can produce results that swing from one extreme to the other, and create the potential for cost overruns in the process. This is an area where proper abrasive wheel selection can play a critical role in keeping costs under control.
Typical expenses incurred when grinding a weld are:
- Welder/grinder operator wage: up to $40/hour
- Equipment depreciation: $4/hour
- Rent, 50 square feet: $2/hour
- Disposable grinding material: $1/hour
- Maintenance: $2/hour
- Electricity: $1/hour
During this process, multiple steps are involved to achieve the desired final finish, and each time a step is repeated, these costs are incurred. Often more steps are needed with low-quality wheels because you have to constantly change the abrasive grit as you grind and then polish to a final finish. But higher-quality wheels eliminate some of those extra steps because they are able to produce a broader range of finishes with more control. And minimizing steps reduces the overall cost of finishing.
Performance vs. Durability
When evaluating a wheel, you must consider the durability of the abrasive, not just its performance in removing material. While you do not want to add additional steps to the finishing process, you also do not want to drive up costs by unnecessarily changing wheels.
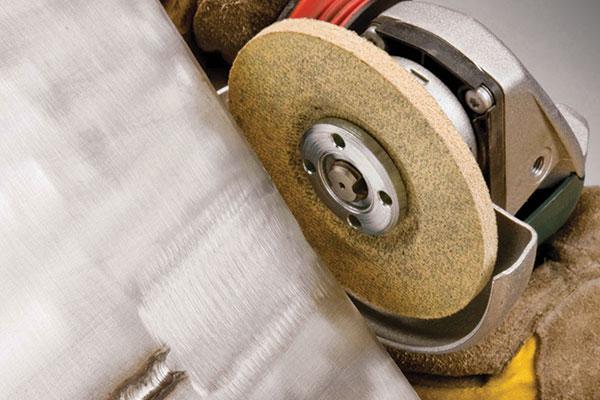
A finish can be as simple as removing a weld down to a smooth surface or as sophisticated as prepping the surface to receive paint, powder coating, or anodizing.
One way to preserve abrasive life is to run wheels at the optimal operating speed for the surface in question instead of the maximum rated speed for the wheel. In most cases, slowing the wheel down and not applying excessive downward pressure will actually deliver a better finish and enable you to go longer between wheel changes. In essence, let the wheel do the work.
Material Considerations
The material being finished also can greatly affect costs. Metal finishes serve a variety of purposes, from cosmetic to functional. A finish can be as simple as removing a weld down to a smooth surface or as sophisticated as prepping the surface to receive paint, powder coating, or anodizing.
As examples, aluminum is a very soft metal that can gum and clog the abrasives on a wheel, while stainless steel has a durable oxide surface. The material’s properties dictate wheel type. For aluminum, you want to select an abrasive surface that is coated or a surface that the aluminum will not stick to and clog the wheel. When you’re working with stainless steel, you want an abrasive that can cut efficiently without gouging the material. Some grains tend to react better on stainless steel than others, and it’s important to select the correct grain based on the surface it will come into contact with.
In some cases, you may be creating a food-grade or other contaminantfree surface. For these applications, the grain used must not leave any particles on the surface that may become permanently embedded in the material and promote the development of corrosion.
Safety Issues
Metal fabricators are always concerned about proper wheel safety and are always looking for information that helps them select wheels that minimize risk of injury. Examining the material safety data sheet (MSDS) for any material that will be cut, ground, or smoothed with the abrasive wheel you are considering is a must.
Inhalation of dangerous substances also can create long-term health problems, so you need to be protected when using an abrasive wheel on a particular material.
Another recommendation is to examine the type of tool that you will use in conjunction with a wheel.
Some units may create excessive vibration that can cause long-term repetitive stress injuries and joint problems. Any wheel selected should be perfectly balanced with low vibration to protect against health issues that develop slowly over time.
When measured against the lost productivity and financial implications of work-related injuries, any time and money spent on improving safety offers extremely high ROI.
Wheel Vendors
A good wheel vendor will balance variables such as rate-of-cut, finish, and longevity to provide a product that can meet your needs in the most efficient manner possible.
Following are some basic questions to ask a potential supplier:
- Will the supplier become familiar with your business and work with you to make sure you have the right abrasive for the application?
- Can they help to educate you on wheel selection?
The answer to these questions will go far in helping you determine the abrasive that will maximize productivity and safety and create the best finished product.
subscribe now
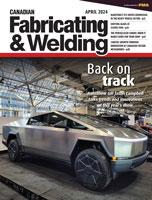
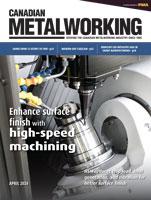
Keep up to date with the latest news, events, and technology for all things metal from our pair of monthly magazines written specifically for Canadian manufacturers!
Start Your Free Subscription- Trending Articles
- Industry Events
MME Winnipeg
- April 30, 2024
- Winnipeg, ON Canada
CTMA Economic Uncertainty: Helping You Navigate Windsor Seminar
- April 30, 2024
- Windsor, ON Canada
CTMA Economic Uncertainty: Helping You Navigate Kitchener Seminar
- May 2, 2024
- Kitchener, ON Canada
Automate 2024
- May 6 - 9, 2024
- Chicago, IL
ANCA Open House
- May 7 - 8, 2024
- Wixom, MI