Associate Editor
- FMA
- The Fabricator
- FABTECH
- Canadian Metalworking
The ever-changing automotive stamping industry in Canada
Two stamping facilities discuss successes, challenges of producing complex automotive components
- By Lindsay Luminoso
- Updated May 18, 2023
- April 20, 2020
- Article
- Fabricating
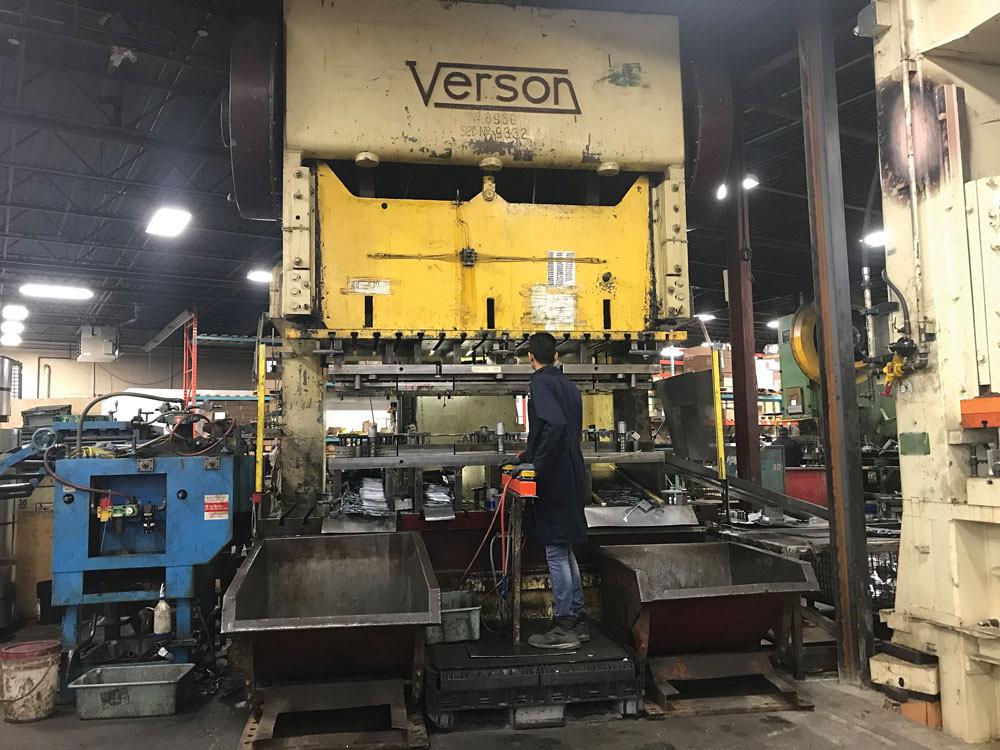
LA Metal Stamping works with aluminum, galvanized steel, Corten steel, cold-rolled steel, and stainless steel, with volumes from 200,000 to 1.5 million parts per year. Photo courtesy of LA Metal Stamping.
According to Statistics Canada, in 2019 Canada’s motor vehicle metal stamping sector had over 100 stamping establishments, with a primary concentration in Ontario and a few businesses in British Columbia, Alberta, and Quebec. These businesses range in size from very small stamping facilities with one to four employees up to large enterprises with more than 500 employees. The majority of Canada’s stamping businesses fall into the small (five to 99 employees) to medium-sized (100 to 499 employees) category.
Over the past few years, the automotive manufacturing sector in Canada has changed dramatically with shifts in production and closures of major plant operations. But what does that mean for the motor vehicle metal stamping sector in Canada?
"As a Canadian stamper we are committed to being very competitive with China and overseas markets; we have to," said Mo-D, director of new business development, LA Metal Stamping, North York, Ont. "In the last 24 months, we have been able to pull a significant amount of business from China and Mexico. We have been focusing on changing our process to a better way of producing parts, particularly in automotive stamping, which tends to be a very turnkey approach. We try to find a compromise between production and engineering and address cost savings from the onset."
LA Metal Stamping focuses only roughly 7 to 10 per cent of its business on automotive stamping. The bulk of its stamping projects are in the housing, appliance, restaurant and food, and payment system segments. This is partially due to a need for diversification to manage market volatility in any one given sector, but also because automotive stamping has significantly more technical requirements and certification than many other traditional industry segments.
As new certification becomes available, automotive stampers need to upgrade to meet the standards. And with that come quite a bit more paperwork and administrative duties that go along with automotive part production in general.
"Because of all the technical requirements, we thought it would be better to stay in the Tier 2 segment of the automotive world rather than be a Tier 1 supplier," said Mo-D. "This has allowed us to be more flexible and cash-happy. We are able to dictate the projects we accept from Tier 1 and have more negotiation room for pricing. As a family-operated business, being able to say no to jobs because of an unnecessarily high expectation of requirements is so important."
While LA Metal Stamping has diversified its project portfolio, many Ontario-based stamping shops have jumped into the automotive stamping world completely.
"Ultramet had previously been working with some larger presses and heavier parts but it shifted to some lighter components with a large production mix," said Justin Garisto, general manager, Ultramet Industries, Breslau, Ont. "However, in the last 10 years, we’ve moved to 99 per cent automotive part production."
Garisto explained that the company is well-suited to take on the advanced technical challenges of the automotive industry and has adapted its shop floor to meet quality and traceability requirements such as the IATF guidelines and certification.
"Production releases and scheduling are different in automotive than some other industries," said Garisto. "For example, if the construction industry and door stamping requested 25,000 parts, once they are completed, we would deliver all the parts, where the construction company would then keep them in a warehouse to consume over time. When it gets down to a reorder point, it would order another 25,000 parts. In automotive stamping, it’s not like that. Usually they want 2,000 parts on Tuesday and then 3,000 parts on Thursday. The release sequence is more spaced out."
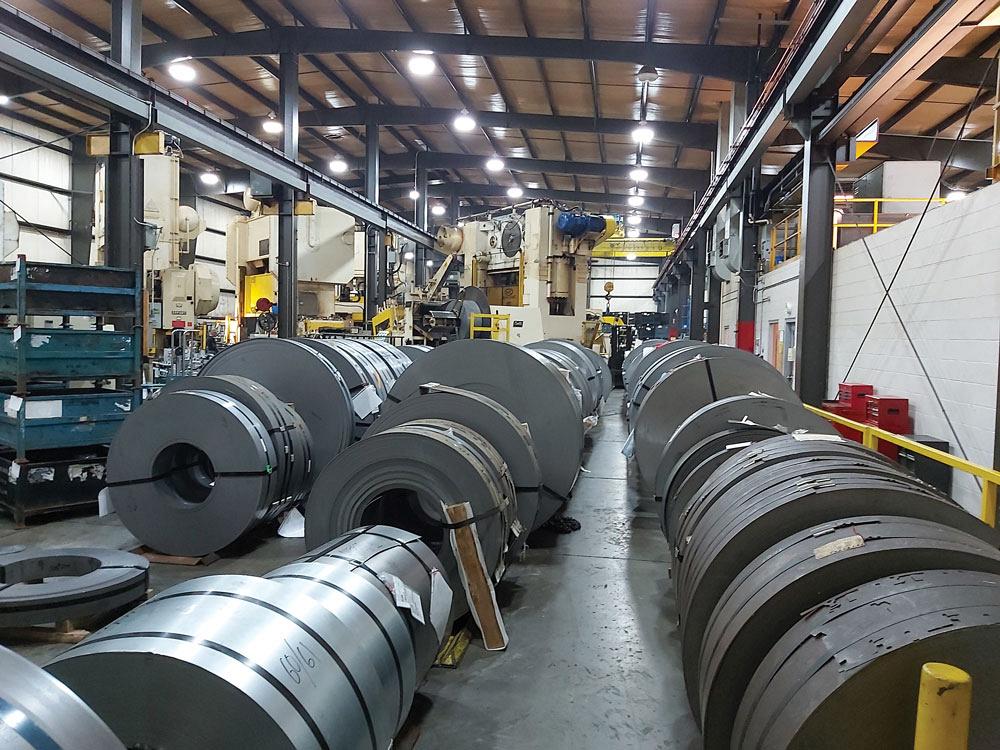
Ultramet has focused on taking on some unique and very technically challenging jobs and recently purchased a new weld cell and is expanding its stamping capabilities. Photo courtesy of Ultramet Industries.
The one advantage Garisto sees with the automotive industry is that it tends to be leaner and cleaner than stamping projects for other industries. He also noted that in automotive, the dies are generally owned by the Big Three automotive manufacturers or whomever the shop is stamping for.
Automotive Stamping Trends
Both LA Metal Stamping and Ultramet Industries provide quality automotive components to their customers. While LA Metal Stamping focuses primarily on presentation parts, Ultramet stamps brackets and structures, primarily suspension, seat, frame, and engine components. The shop does little in the way of presentation or cosmetic parts.
"Presentation parts can present some additional challenges for stampers," said Mo-D. "We’ve had to have some conversations with one of the automotive clients about quality control. When parts leave our facility, they are clean, but when they get to the assembly line, they may not be. When you have presentation parts, which tend to be very expensive parts, traceability is important to see where a part may have gotten damaged along the way and ensure customers are getting good, quality parts."
This is why with automotive stamping it’s really important to ensure that the material coming in meets specifications. Stamping shops need to ensure that their material is close to 100 per cent clean and good to use before the material goes into the press. This is important for all stamped parts, but is critical for cosmetic components.
LA Metal Stamping works with aluminum, galvanized steel, Corten steel, cold-rolled steel, and stainless steel, with volumes from 200,000 to 1.5 million parts per year. The shop is stamping parts under a number of brands including Hino, General Motors, and Chrysler.
Ultramet has focused on taking on some unique and very technically challenging jobs and can stamp parts up to 7 mm thick. The shop recently purchased a new weld cell and is expanding its stamping capabilities.
"We recently reissued one of our 500-ton presses that is made for heavy blanking and forming," said Garisto. "Our largest stamping press is a 600-ton press with a linear transfer system. We have a nice range of stamping equipment to meet the needs of the jobs we are taking on. And currently we can run 42-in.-wide coils, which is quite large."
Both shops are concentrating on expanding their shop floors and capabilities to adapt to ever-changing industry trends.
"One of our investments is in expanding our building and bringing in some larger presses that are over 1,000 tons to accommodate the projects that are in the market, not just automotive, but in many industries," said Mo-D. "Right now we are looking to expand by 25,000 sq. ft."
Automotive Projects
As both shops concentrate on expanding, they see different trends within the automotive stamping world and are adapting to stay ahead of the curve.
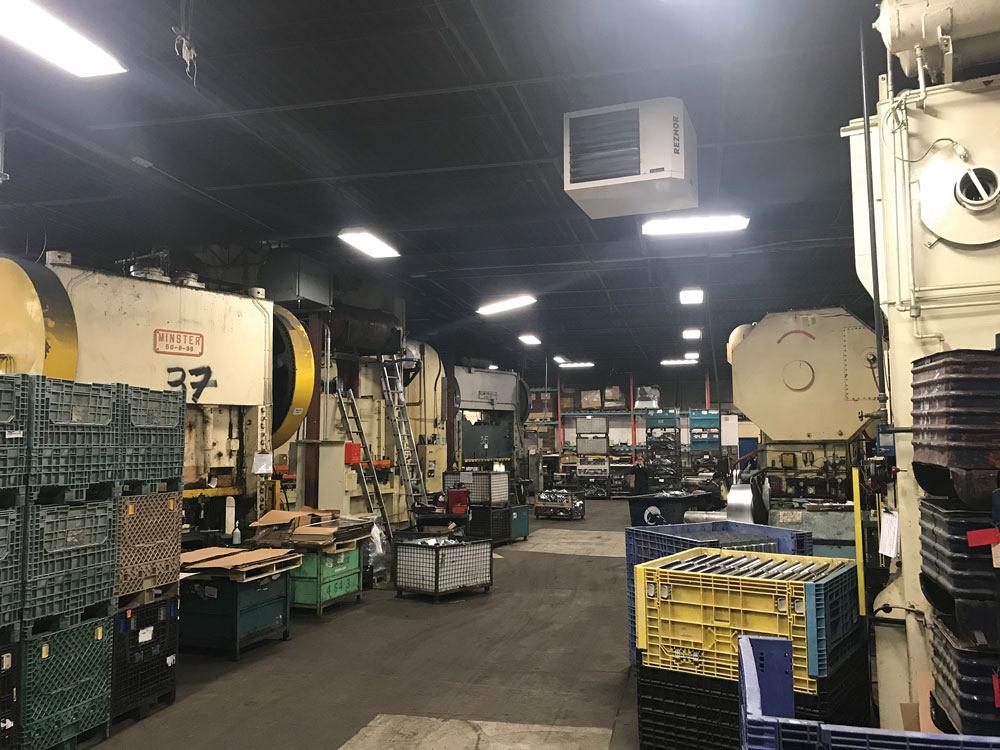
LA Metal Stamping focuses only roughly 7 to 10 per cent of its business on automotive stamping. The bulk of its stamping projects are in the housing, appliance, restaurant and food, and payment system segments. Photo courtesy of LA Metal Stamping.
"We’ve been seeing a lot of low-production work, so specialized vehicle work," said Garisto. "One of our latest projects required 7-mm material. The 6-mm material wasn’t enough for what they were doing. This is very uncommon. This thicker-gauge material is harder to purchase and is a challenge to work with. We are also seeing changes in materials, particularly in the hardness of the steel we have to work with."
Garisto noted that the complexity of the parts that they are currently working with has changed drastically over the last few years. Accuracy requirements are also getting much stricter.
"We are stamping parts that are 0.1-mm tolerance," said Garisto. "That’s pretty accurate. Currently 0.004 in. is the limit of what stamping is capable of for surfaces. So we are in the right range. We also are seeing components that were being cast 10 years ago using aluminum that are now being produced using steel, which is great for our industry."
Garisto gave an example of one of the projects the shop is currently working on, a heavy-duty axle that is produced using its gas metal arc welding cell as well as stamping.
"The stamping of this component is very thick and cumbersome," he said. "Some of the parts are up to 12 lbs. and all are hand-held on the shop floor. So workers literally have to hold these parts repeatedly throughout the day. We are certainly concerned about the ergonomics of these projects and are constantly trying to figure out ways to ease this for the operator. These parts, because they’re so thick, require welding in very tight and confined spots on the component. We are spending a lot of time with the developments, trying to get the proper penetration."
As automotive parts become more complex, shops need to find new solutions to avoid safety hazards and quality control issues.
"One of the trends we’re finding in the industry is that most automotive stamping is moving away from smaller presses in the 100- to 300-ton range," said Mo-D. "Many are now looking for presses in the 1,000- to 2,000-ton or higher range. There also is a tendency to look for a larger bed size to focus on making larger, singular parts rather than four or five different parts. As an industry, we are being tasked with trying to figure out how to make these four or five parts into one larger component."
Customer Relations in Automotive Stamping
Both Mo-D and Garisto expressed concern over changes in the bidding process for automotive projects. While both shops tend to focus on different areas of the industry, they both see similar challenges with what automotive OEMs expect from companies in the supply chain.
"We recently got an RFQ from a Tier 1 automotive company that had technical expectations that were way beyond the pale," said Mo-D. "What was more, the company wanted a price reduction over the five years of the project, paid upfront before it even accepted the business. It wanted stamping shops like us to go into the RFQ auction process like this. That’s not the way it should be done. We’re not interested in taking on these types of jobs because the company is not looking at quality, reliability, or building a relationship, which is what we are good at. The company just wanted to dirt-bottom the price."
Garisto echoed this same sentiment.
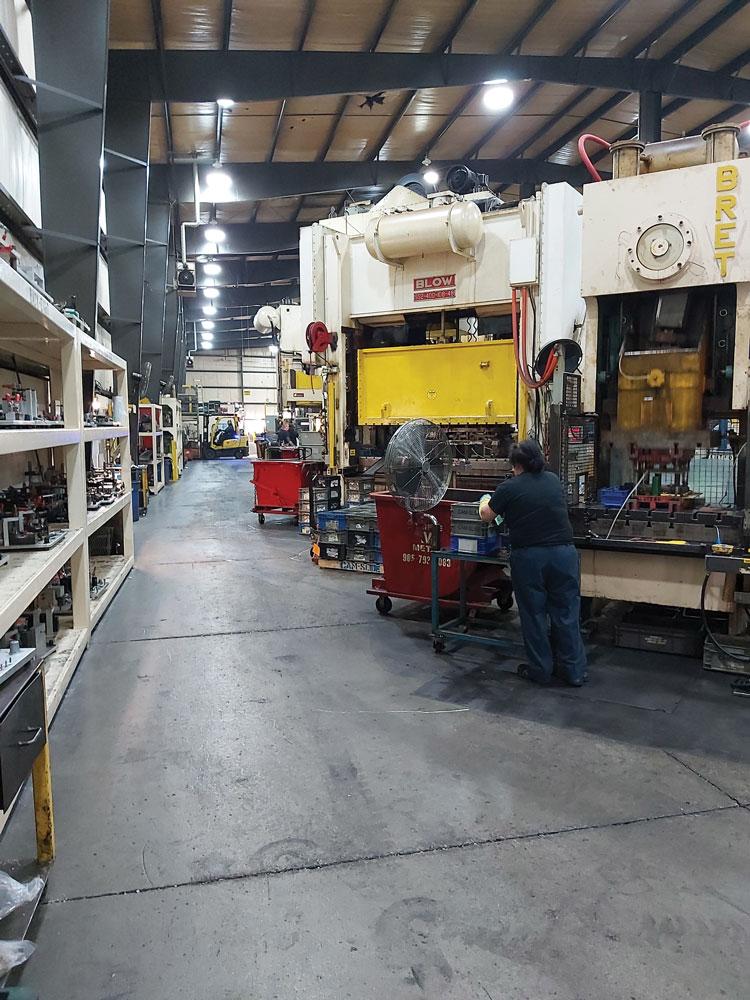
Ultramet is well-suited to take on the advanced technical challenges of the automotive industry and has adapted its shop floor to meet quality and traceability requirements such as the IATF guidelines and certification. Photo courtesy of Ultramet Industries.
"We’re really big on relationships and having open communication with our suppliers and customers," he said. "We try to give them what they need regularly. And that usually keeps them coming back for more. But I think the automotive industry for the most part has lost that sense of relationship. It’s basically about hard numbers and really accounting-driven rather than relationship-driven."
Garisto added that he too has seen that many automotive companies are changing the way they quote.
"Automotive companies are putting out open tenders and letting everybody race to the bottom," he said. "That’s going to be a harder thing to maintain because people will adjust their practices knowing they are going to lose money. There’s no value in that. However, a shop that takes on a loser job from a client it has a relationship with can offset the loss with future jobs that the client will bring it. It’s a give and take that you don’t get with this destructive bidding practice. Stamping shops will therefore need to reduce its quality or risk major fiscal losses just to keep up."
The Future of Automotive Stamping
The automotive parts manufacturing supply chain has constantly needed to adapt to changes in the Canadian automotive manufacturing landscape, particularly as they relate to closures and shifts in production that the industry has recently undergone. However, from a more technical standpoint, the automotive industry is also moving toward more advanced, intelligent vehicles, which will also impact how and what will need to be stamped.
"I think that because everyone’s moving to more self-driving cars, fewer standard cars are being produced," said Mo-D. "With the industry needing fewer cars, volumes are now going down. Instead of having smaller cars made, we’re now seeing only large vehicles being made. Sedans are now a thing of the past.
"We are no longer making cars, we’re making people movers. The industry is now moving more toward this whole pickup, dropoff car rental idea. And I think with Tesla coming out with this new AI technology, it will make it easier for people to rent a car rather than own one. It’s a more car-sharing way of using vehicles. You can order whatever class of car you want and it will show up and you can go about your driving. This will certainly impact the way we produce cars going forward."
Associate Editor Lindsay Luminoso can be reached at lluminoso@canadianfabweld.com.
LA Metal Stamping Co., www.lametalstamping.com
Ultramet Industries Inc., www.ultramet.on.ca
About the Author
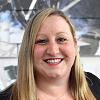
Lindsay Luminoso
1154 Warden Avenue
Toronto, M1R 0A1 Canada
Lindsay Luminoso, associate editor, contributes to both Canadian Metalworking and Canadian Fabricating & Welding. She worked as an associate editor/web editor, at Canadian Metalworking from 2014-2016 and was most recently an associate editor at Design Engineering.
Luminoso has a bachelor of arts from Carleton University, a bachelor of education from Ottawa University, and a graduate certificate in book, magazine, and digital publishing from Centennial College.
subscribe now
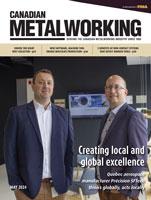
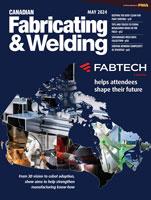
Keep up to date with the latest news, events, and technology for all things metal from our pair of monthly magazines written specifically for Canadian manufacturers!
Start Your Free Subscription- Industry Events
Automate 2024
- May 6 - 9, 2024
- Chicago, IL
ANCA Open House
- May 7 - 8, 2024
- Wixom, MI
17th annual Joint Open House
- May 8 - 9, 2024
- Oakville and Mississauga, ON Canada
MME Saskatoon
- May 28, 2024
- Saskatoon, SK Canada
CME's Health & Safety Symposium for Manufacturers
- May 29, 2024
- Mississauga, ON Canada