Associate Editor
- FMA
- The Fabricator
- FABTECH
- Canadian Metalworking
From 2D to 3D waterjet cutting
Multiaxis waterjet can cut virtually any material regardless of its shape
- By Lindsay Luminoso
- June 24, 2021
- Article
- Fabricating
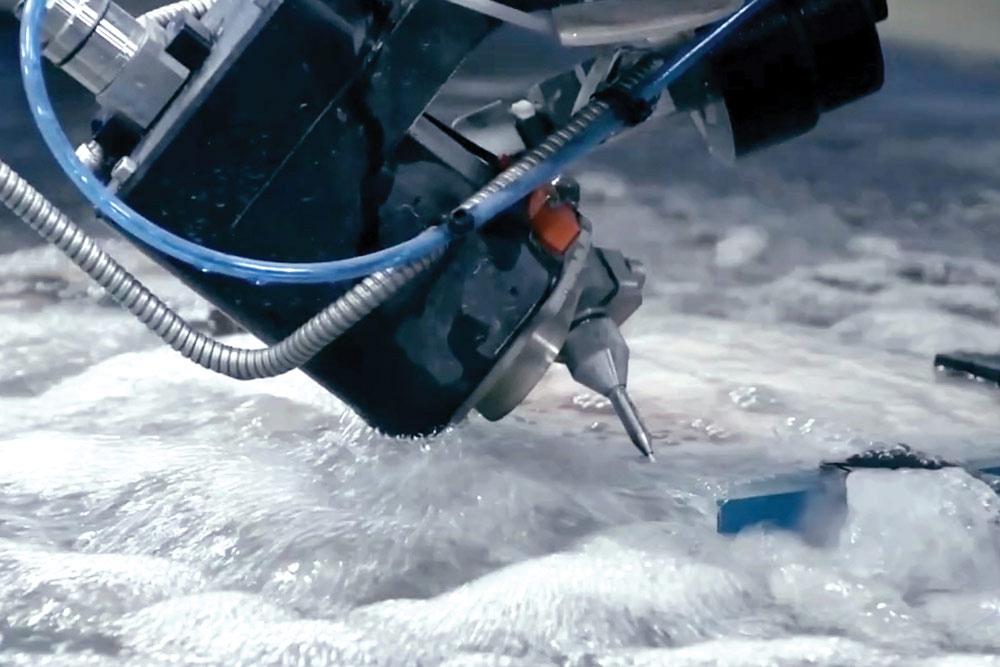
With 3D cutting, you need to anticipate how the machine is going to rotate to reach challenging angles so that you don't inadvertently rotate the mechanism into a grate, clamp, or something that could damage your machine. WARDJet
Waterjet systems have always been versatile, highly productive machines, but some manufacturers saw these systems as messy and a crude cutting technology. However, these systems have evolved over the years, making them fast, accurate, and relatively clean. Waterjet machines can cut virtually any material, making them a workhorse on the shop floor. As such, the adoption rate of waterjet technology has jumped significantly, and fabricators have found ways to expand their capabilities using this platform. Today’s systems can be found in many fab shops across the country and are being used in more unique and advanced ways, further evolved by the introduction of 3D or multiaxis cutting.
2D Versus 3D
With 3D waterjet systems, fabricators now can perform complex cutting operations not only on flat plate, but also asymmetrical materials and intricate workpieces. Bevels, chamfers, weld preps, and angled holes are just a few of the common applications made possible by 3D waterjet cutting. However, the transition from standard to 3D waterjet cutting can present some unique challenges that need to be considered before the first cut.
Fixturing and Setup. With 2D cutting, fixturing a flat plate to the cutting table is fairly simple. Slats and grates span the length of the tank, and clamps are used to fixture the material to the cutting bed.
With 5-axis cutting, fixturing parts can be more challenging. Many complex components require custom fixtures. The challenge comes with ensuring that the fixtures do not interfere with the path of the cutting head or the jet stream.
"The goal of 5-axis cutting is to reduce overall cycle time of a part by eliminating secondary processes," said Benjie Massara, waterjet product manager, WARDJet, Tallmadge, Ohio. "If it takes a long time to produce fixturing or you are constantly having to refixture, you lose the advantage. You want to make sure that the machine is able to perform and cut your features. If they cannot be done in a single setup, we would use 5-axis undercutting. Instead of actually seeing the exposed, angled face of the part, it’s cutting under the material. This allows for multiple features to be cut in one go."
Clearance. Many fabricators working with 3D waterjet tend to come from a milling background. With milling, once the cutting tool clears the material, it stops and moves to the next part geometry. 3D waterjet cutting requires the operator to think about how the cutting stream will behave.
"With waterjet, the water just wants to keep going," said Ivan Kondeykin, applications and demo lab supervisor, OMAX, Kent, Wash. "Once the cutting stream is through the material, it is still very destructive. This is one of the reasons that these systems include huge waterbeds that go pretty much all the way to the floor."
For safe clearance, it’s important to be aware of part placement on the bed. If a part requires cutting outward towards the front of the machine, you want to make sure the part is far enough away from the front of the tank to ensure that you aren’t damaging the system.
"With 2D waterjet cutting, you only really have to worry about the nozzle or tool tip clearing grates, clamps, and things of that nature," said Massara. "With 3D, you have to understand that the cutting mechanism will be rotating. With the complex applications you may have a workpiece that is asymmetrical or have a piece protruding off one side. You need to anticipate how the machine is going to rotate to reach those angles so that you don’t inadvertently rotate the mechanism into, say, a grate, clamp, or something that could damage your machine."
Cutting Heads and Accessories. Shops looking to get into 5-axis waterjet have the option to either retrofit an existing 2D machine with a dynamic cutting head or purchase a new system designed specifically for multiaxis cutting.
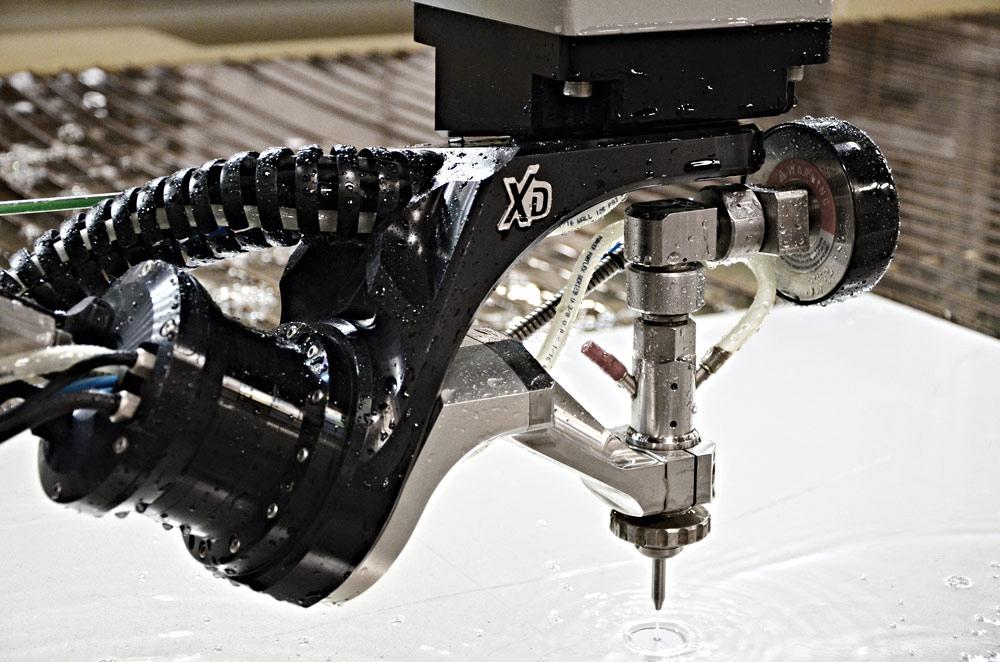
On a 3D dynamic waterjet, the cutting head has more technology than the standard waterjet head, but the possibilities are greater, especially with the evolution of easy-to-use software. Flow International Corp.
"It’s a significant capital expenditure to get into waterjet in the first place," said Ted Irwin, regional business manager, Flow International Corp., Kent, Wash. "With a 3D dynamic waterjet, the cutting head has more technology than the standard waterjet, but the possibilities are greater, especially with the evolution of easy-to-use software. Like any upgrade, there’s a cost, but we are seeing more clients consider 5-axis heads as a path to a faster return on their investment."
It’s not just about taking the cutting head and tilting it at an angle to perform angled cuts; the system needs to control the taper dynamically and perform cuts accurately. Software and modelling also can be used to account for any variables and look at the geometry to ensure that the cut is done right.
"Another difference between 2D and 3D waterjet cutting involves the standoff distance—basically how far the nozzle or jet is from the material surface," said Brian Sherick, vice-president of global systems sales, Flow International Corp. "The standoff distance needs to remain at roughly the same distance, and with 2D cutting that’s not difficult. When you start imparting angles into the cut, the standoff distance must remain exact otherwise your angle will be way out of line versus the finished part. We’ve spent years dialing in these variables, ultimately making it easier to use. For example, a compass device can be used to monitor the height of the cutting nozzle from the material surface. This tool is important when performing high-tolerance cuts in 5-axis."
As the technology continues to advance, multihead cutting is slowly gaining traction. Some fabricators may find that adding cutting heads dedicated to 2D cutting to their 3D system can make the machine even more versatile and expand production capabilities.
Part Orientation. There are some limitations when it comes to cutting angle and part orientation.
"Most people think in terms of 2D cutting a plate and they often overlook the fact that when 5-axis cutting, the cutting head is angling around the perimeter of the plate, so the part is actually going to be a lot wider towards the bottom," said Kondeykin. "When they nest parts next to each other, the angle from the other side will cut into the angle from the first cut. So, it’s important to understand the mechanics and how the cut will affect part placement."
When cutting, you can really see the part only from the top. When the material is removed and flipped over, it is then that operators realize that they cut over into another part, ruining two parts.
The experts also noted that, although not necessarily a part orientation issue, some shops want to use 3D waterjet to perform one pocket in a hole or a simple cut on the top surface without touching whatever is underneath.
"If you want to do this, then sacrificial material is a must," said Kondeykin. "This is needed to displace the water. The other option is to find another way to divert or stop that high-pressure waterjet cutting through. It’s definitely something to keep in mind."
Software. As new waterjet technology enables more complex cutting, especially with 5-axis, the jet stream must perform appropriately. This is where software with taper control and taper compensation comes into play.
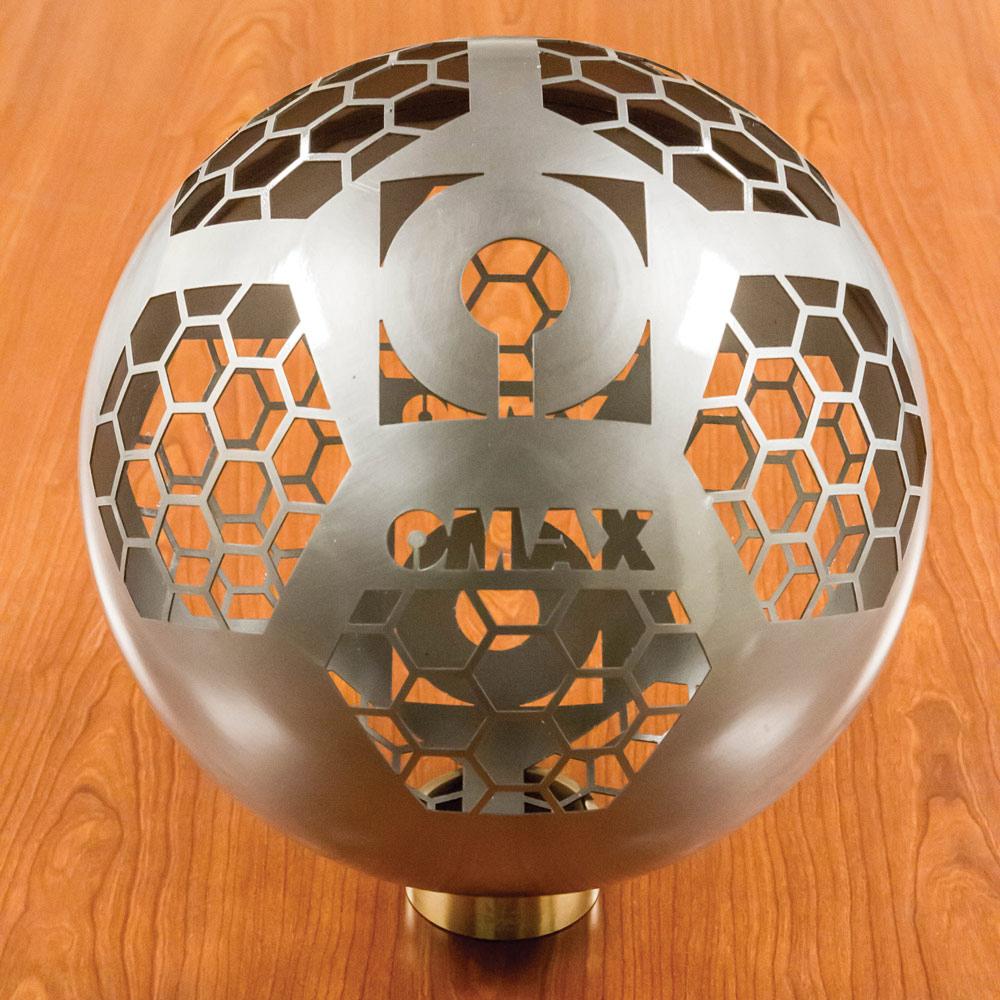
3D waterjet systems perform complex cutting operations not only on flat plate, but also asymmetrical materials and intricate workpieces. OMAX
"There’s a V-shape taper that occurs in the edge, so you can really lose that accuracy," said Sherick. "In 5-axis cutting, it becomes exponentially harder to control. Software, in conjunction with the cutting head, is needed to compensate for that taper. Good software will also have modelling options to be able to see how exactly the waterjet will perform and act."
Without the proper software and programming tools, the learning curve can be extremely steep. This is why it is so important to investigate what software tools are included in the machine and how user-friendly they are.
"Programming that includes a virtual model, cutting mechanism, and performance logistics can give you that view of how the machine will react," said Massara. "It will let you see how it will hit a certain angle, whether it will rotate right or left, and perform a simulation that will show clamps and fixturing mechanisms and how best to avoid any sort of collisions or cutting where you don’t want to."
Safety. In 2D waterjet the cutting stream is very predictable: It goes down vertically into the material. However, when the stream is angled, safety becomes an issue. Does the stream shoot toward a support in the tank? Or will it be angled upward in any way that could present a safety hazard?
"With 3D cutting, you really need to be mindful of the jet," said Kondeykin. "You have to make sure that there is enough stopping distance for that jet. Getting the right safety mechanisms in place is a good first start, but you certainly want to also make sure that the cutting stream will never go where you are not expecting it to."
Safety features include steel guards around the cutting table; sensors or equipment that can shut off the machine before the waterjet stream leaves the boundary; perimeter mats to ensure that the machine cannot run without an operator or shuts off if someone gets too close; and light curtains to detect intrusion that shuts the machine down.
Skill. Not all fabricators may require 5-axis cutting. It can be an intimidating technology, especially if the shop is not familiar with waterjet. The mechanisms tend to be more complicated, and routine tasks can be a bit more cumbersome and time-consuming. A good place to start is to talk to the experts to make sure the application really fits a shop’s needs.
"You certainly want to investigate what exactly you are getting in a system," said Sherick. "You want to evaluate the supplier, make sure the software is easy to use, and whether it comes with the intelligence needed to do the required work so that you don’t need to have an operator standing in front of the machine with all the knowledge in their head."
Sometimes fabricators are brought into the 5-axis world because they have a specific job or certain part that they need to cut. Massara said that it’s advisable to look at the skills of the workforce and operators. The technology can range from simple to complicated and training may be needed, so it’s really important to get a feel for how operators will function with this technology.
It’s also a matter of practice and spending time with the machine. The experts agree that fabricators should try anything and everything with their machines. Waterjet can basically cut any material, so exploring new applications can open doors. But it’s important not to be afraid of the technology. See where it can take you.
Associate Editor Lindsay Luminoso can be reached at lluminoso@canadianfabweld.com.
Flow International Corp., www.flowwaterjet.com
OMAX, www.omax.com
WARDJet, www.wardjet.com
About the Author
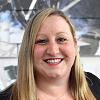
Lindsay Luminoso
1154 Warden Avenue
Toronto, M1R 0A1 Canada
Lindsay Luminoso, associate editor, contributes to both Canadian Metalworking and Canadian Fabricating & Welding. She worked as an associate editor/web editor, at Canadian Metalworking from 2014-2016 and was most recently an associate editor at Design Engineering.
Luminoso has a bachelor of arts from Carleton University, a bachelor of education from Ottawa University, and a graduate certificate in book, magazine, and digital publishing from Centennial College.
Related Companies
subscribe now
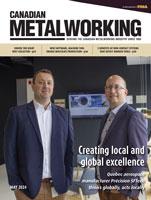
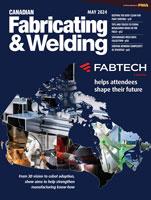
Keep up to date with the latest news, events, and technology for all things metal from our pair of monthly magazines written specifically for Canadian manufacturers!
Start Your Free Subscription- Trending Articles
FMA Annual Meeting: Ingenuity still key with tech innovations
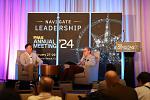
Torch made for welding thin, conductive sheet metal
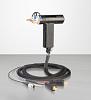
Compact swing chamber shot blast machine features robotic workpiece handling
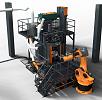
Welding jacket designed for protection, comfort
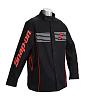
Gang punching press system accommodates different parts quickly
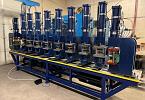
- Industry Events
Automate 2024
- May 6 - 9, 2024
- Chicago, IL
17th annual Joint Open House
- May 8 - 9, 2024
- Oakville and Mississauga, ON Canada
MME Saskatoon
- May 28, 2024
- Saskatoon, SK Canada
CME's Health & Safety Symposium for Manufacturers
- May 29, 2024
- Mississauga, ON Canada
DiPaolo Machine Tools Open House 2024
- June 4 - 5, 2024
- Mississauga, ON Canada